Have you adopted additive manufacturing for production or looking to do so soon? We share 5 tips to help you succeed.
Additive manufacturing has become a key manufacturing method for production. According to a recent survey by Jabil, over 55% of companies are using 3D printing technologies to produce at least 25% of their functional or end-use parts.
But how can you make the most of the technology and ensure that your additive production can scale?
Before we dive into what companies adopting AM should consider on their additive production journey, let’s first explore what makes AM attractive for production in the first place.
Why adopt industrial 3D printing?
The growth of 3D printing technologies across industries shows that companies, both small and large, can benefit from 3D printing in multiple ways.
On-demand manufacturing
For companies looking to embrace more agile manufacturing, additive manufacturing provides a cost-effective solution for on-demand production. The technology can be used to make tooling and spare parts at the point of need, reducing the need to maintain an excess stock of inventory.
Design innovation
Additionally, for companies exploring new design approaches, 3D printing expands design possibilities. Complex geometries, such as lattice structures, can be 3D printed to create components impossible to produce with other technologies.
Mass customization
Furthermore, 3D printing makes mass customisation attainable. With traditional manufacturing where high-volume, mass production is standard, the costs to produce customised products in small batches is prohibitive.3D printing enables manufacturers to bypass high tooling costs, thereby producing customised parts faster and more cost-effectively.
These and other low-volume, complex parts would ordinarily be injection moulded or cast, resulting in high costs. Additionally, designers were able to include design features not possible with other manufacturing methods.
As this case study demonstrates, examining your product portfolio is a key step when determining your company’s potential applications for the technology.
Other ways to leverage AM include manufacturing parts that are typically produced in low volumes, or components that require a high level of customisation not economically viable with traditional manufacturing.
Of course, not all parts will benefit from additive manufacturing – which is why identifying potential applications is key. If your design is prohibitively expensive, or otherwise too complex to manufacture, AM could be the right choice. In contrast, where high volumes are needed, it’s likely best to consider injection moulding.
But how can you best combine the process of identifying products that will be good for AM with the process of developing other essential AM skills?
This is where a centre of excellence comes into the picture.
#3 Set up your own centre of excellence
Setting up a centre of excellence (CoE) is a great way to manage your company’s adoption and integration of additive manufacturing.
A CoE can be defined as a team or facility set up to support business objectives and drive your company’s expertise in a certain area – in this case, additive. Your CoE will be key to finding the best use cases and practices – and disseminating this throughout your organisation.
Putting such a team in place will require input from key stakeholders, including production staff and engineers. Of course, this isn’t without its challenges, not least because AM differs considerably from conventional manufacturing techniques. It means rethinking conventional approaches to design, production and supply chain management.
This means that your CoE should also focus on fostering a new organisational mindset that will help to embrace the new manufacturing and business models offered by AM.
Swagelok is one company that has identified the importance of a cultural shift in addition to process changes in successfully integrating AM. The US company manufactures high-volume gas and fluid systems components, with extensive capabilities in subtractive manufacturing methods.
However, the company has identified areas in which additive manufacturing can be used to overcome the limitations of these traditional methods, for example in the production of its steam-traced ball valve. In a conference held by SME, Swagelok’s presentation focused on the importance of changing company culture and its commitment to creating a ‘multi-faceted additive manufacturing strategy’.
Developing your workforce will be another strand of your centre of excellence. With the vast majority of manufacturers citing a lack of knowledge as a key barrier to their adoption of AM, developing a talent pool in-house is becoming increasingly significant.
#3 Set up your own centre of excellence
Setting up a centre of excellence (CoE) is a great way to manage your company’s adoption and integration of additive manufacturing.
A CoE can be defined as a team or facility set up to support business objectives and drive your company’s expertise in a certain area – in this case, additive. Your CoE will be key to finding the best use cases and practices – and disseminating this throughout your organisation.
Putting such a team in place will require input from key stakeholders, including production staff and engineers. Of course, this isn’t without its challenges, not least because AM differs considerably from conventional manufacturing techniques. It means rethinking conventional approaches to design, production and supply chain management.
This means that your CoE should also focus on fostering a new organisational mindset that will help to embrace the new manufacturing and business models offered by AM.
Swagelok is one company that has identified the importance of a cultural shift in addition to process changes in successfully integrating AM. The US company manufactures high-volume gas and fluid systems components, with extensive capabilities in subtractive manufacturing methods.
However, the company has identified areas in which additive manufacturing can be used to overcome the limitations of these traditional methods, for example in the production of its steam-traced ball valve. In a conference held by SME, Swagelok’s presentation focused on the importance of changing company culture and its commitment to creating a ‘multi-faceted additive manufacturing strategy’.
Developing your workforce will be another strand of your centre of excellence. With the vast majority of manufacturers citing a lack of knowledge as a key barrier to their adoption of AM, developing a talent pool in-house is becoming increasingly significant.
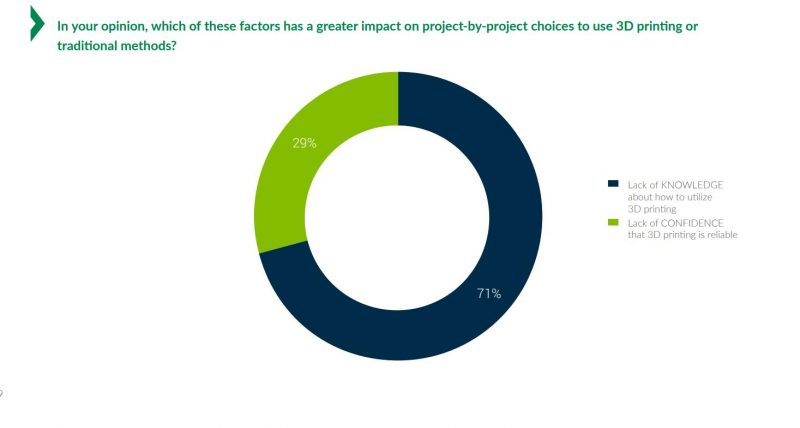
#4 Partner with universities and research institutions
Establishing collaborative relationships with universities and research institutions is another way to foster AM adoption within your organisation.
There are mutual benefits to such a partnership. On one hand, companies can gain greater access to cutting-edge research and scientific talent. On the other hand, universities are able to access financial support and partners in research.
One example is Proto Precision Manufacturing Solutions, a US company that specialises in metal fabrication. Seeing the advancements in metal 3D printing technology, the company decided to tap into its potential.
However, for a relatively small company like Proto Precision, buying a metal 3D printing wasn’t a viable option.
For this reason, in 2018 the company signed a partnership with the Ohio State University’s Center for Design and Manufacturing Excellence (CDME). The aim behind the partnership is to help Proto Precision develop its metal 3D printing capabilities.
CDME hosts a range of metal 3D printing technologies within one university lab, from binder jetting to powder-bed fusion. With this access to high-end 3D printers and CDME’s expertise in AM, Proto Precision was able to quickly integrate metal 3D printing technology into their operations to meet the needs of its growing customer base.
This is just one example of how the combined power of industry and academia can accelerate innovation.
Beyond that, companies looking to incorporate AM into production, but lacking the necessary skill sets, can turn to universities for workforce development.
In light of the existing AM skills gap, building stronger relationships with universities – especially those that run AM educational programmes or training courses – is a beneficial model that can yield great results.
#5 Focus on repeatability and minimisation of process complexity
Finally, as you begin developing AM production capabilities in-house, another crucial thing to consider is how you achieve repeatability.
Repeatable quality isn’t easily achieved in AM.
Most AM technologies require a comprehensive build setup to ensure the part completes the printing process and can undergo post-processing. As most AM users know, this is sometimes easier said than done, as it’s not uncommon to face part-to-part and machine-to-machine variations and inconsistencies.
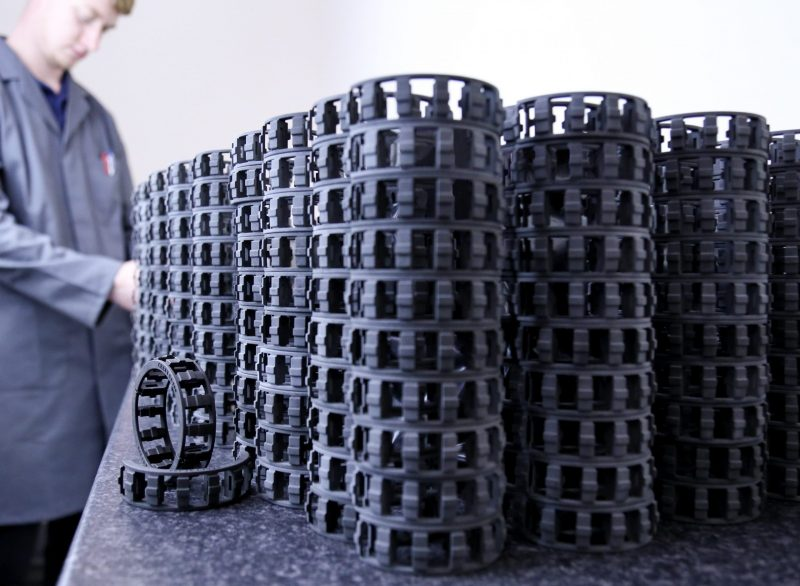
Establishing a closed-loop control system is considered the most efficient way to increase repeatability in AM.
A closed-loop control system involves three steps: the first is the planning of the build through simulation; the second is the machine and process monitoring; and finally, the use of the gathered data to analyse the printing process and adjust the system to prevent build failures and ensure reproducibility.
Establishing such a system will require a high level of connectivity between machines and the ability to coordinate these processes.
This is where you’ll need to start thinking about the digital side of things. Installing a digital system that underpins efficient gathering and handling of data and fosters transparency and accountability, is what’s necessary for 3D printing of parts with reliable, consistent results.
For example, Bowman Additive Production specialises in the production of bearings using AM. Since the AM specialist handles several projects on a daily basis, maintaining a clear overview of the parts and production requirements in the request, production and post-processing stages would be challenging with tools like Excel.
The use of specialised AM software has enabled the company to collect 3D printing order data, track parts through the production and post-processing and coordinate all steps digitally. As a result, Bowman AP centralised the data and established a streamlined process that underpins repeatability.
So the takeaway here is that you should start thinking about how you will be managing your AM production early on. Without specialised solutions developed for AM like additive MES and machine integration, you’re at risk of increasing process complexity. This will make achieving a high level of repeatability challenging and will impact the overall ability to scale.
Think big, start small, scale fast
Adopting any new technology can be daunting and isn’t without risk. However, the long-term benefits of additive manufacturing far outweigh the initial time and investment needed.
As Brian Alexander from Solvay, the leading provider of high-performance AM-ready materials, has summarised, “if you are realistic about using AM as a viable production process you need to combine material, printer/process and design to be successful, otherwise your part performance, quality and consistency will be well below that of traditional manufacturing.”
So find the areas where AM adds value. Explore the technologies available, prioritising those that will work best for your needs. Take advantage of the training and educational opportunities provided by research institutions and advisory companies.
Finally, start to develop a strategy for implementation – using your centre of excellence as the focal point.
These steps will help you gradually make your way towards building your own expertise of using advanced additive manufacturing.
Source: https://amfg.ai/2021/04/08/5-tips-to-help-your-company-succeed-with-additive-manufacturing/