More than 85,000 commercial options for plastic materials are listed in materials databases, and, within those, 45 polymer families can be broadly classified into two categories: thermosets and thermoplastics. At FacFox, we primarily focus on the latter category, offering hundreds of stocked engineering-grade thermoplastic resins through our rapid injection molding service. In addition to our stocked supply of resins, we have the capabilities to support many more customer-supplied resins as well.
Narrowing down that extensive list of materials can sometimes seem like a formidable task, so we’ve prepared this list that outlines the benefits and applications of some of our most commonly molded materials. By choosing the right material, you can improve the form, fit, and function of your parts.
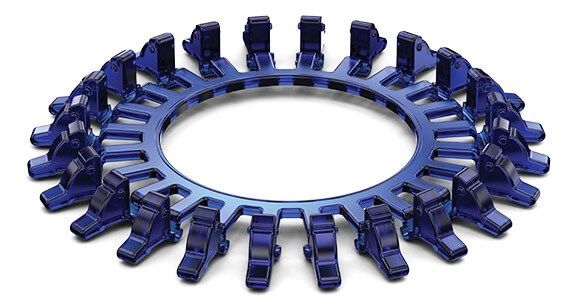
ABS (Acrylonitrile Butadiene Styrene)
Benefits: ABS is a tough, impact-resistant plastic that is widely used across many different industries. It has low shrink and high dimensional stability, and it has good resistance to acids and bases. ABS is a good choice for handheld consumer devices. It’s also relatively inexpensive.
Applications: cosmetic parts, handheld devices, housings, and moldings for electrical tools, remote controls, computers, telephone components.
Considerations: ABS-molded parts will show knit lines and can have sink and voids in thick areas. Reduction of sink can possibly be had by switching to an ABS/PC-blended material. ABS also mates well to PC parts.
ABS/PC
Benefits: ABS/PC combines the strength and heat resistance of polycarbonate with the flexibility of ABS. ABS/PC also provides improved processing during injection molding, increased toughness and dimensional stability, higher heat resistance than ABS, and improved low temperature impact resistance than PC.
Applications: These blends are typically used in the automotive, electronic, and telecommunications industries among others applications.
Considerations: ABS/PC materials oftentimes can minimize thick molding concerns found in ABS or PC materials when molded alone. It is frequently used when increased mechanical properties are required when using ABS or when a lower cost PC is required.
PC (Polycarbonate)
Benefits: PC is strong and extremely impact resistant with low shrink and good dimensional stability. It’s a transparent plastic that is available in optically clear grades. PC has good heat resistance and accepts high cosmetic finishes well.
Applications: Lenses, indoor and outdoor lighting, cell phone housings, electrical components, medical devices, bulletproof glass.
Considerations: There can be sensitivities in thick sections of parts that may cause voids, bubbles and sink, and PC parts possess poor chemical resistance. An ABS/PC blend is a good alternative for opaque parts with these issues, and Acrylic (outlined below) is another option for parts with thick geometries.
PA or PPA (Aliphatic Polyamides)
Benefits: There are many types of PAs, or nylons (4, 6/6, 6, 6/10, 6/12, 12, etc.), each with its own advantages. Generally, nylon parts provide high strength and high-temperature strength, especially when reinforced, and are chemically resistant, except to strong acids and bases. Some, like nylon 6/6, offer great hardness and stiffness, and are abrasion resistant. Nylon 6 is extremely hard and tough at low temperatures, but nylon 6/12 has the better impact strength.
Applications: thin-walled features, combs, spools, gears and bearings, screws, structural parts (with glass), pump parts, under-hood components, cameras.
Considerations: Nylon can be more susceptible to warp due to non-linear shrink, so keep that in mind when choosing a specific type of nylon. If your part will be exposed to moisture, you should consider avoiding nylon as it is a hygroscopic material that will absorb moisture, causing dimensional and potentially structural issues.
POM (Polyoxymethylene)
Benefits: Commonly called acetal, it is characterized by high toughness, stiffness, hardness and strength. Acetal has good lubricity and resistance to hydrocarbons and organic solvents. It also has good elasticity and is slippery, so it works well for bearing surfaces and gears.
Applications: gears, pumps and pump impellers, conveyor links, soap dispensers, fan and blower blades, automotive switches, electrical switch components, buttons and knobs.
Considerations: Due to shrink, customers must specifically design for acetal with uniform wall thickness. Painting and coating acetal parts is difficult because of their lubricity. It’s also difficult to achieve a high-cosmetic finish using acetal. If a limited number of prototype parts are needed, it can easily be machined through FacFox.
PMMA (Polymethyl Methacrylate)
Benefits: PMMA, aka acrylic, has good optical properties, high gloss and is scratch resistant. Acrylic also has low shrink and has less sink in geometries with thin and think sections.
Applications: light pipes, lenses, light shades, optical fibers, signs.
Considerations: Acrylic can be brittle and thus more susceptible to stress cracking. PC is a good alternative, if needed. Draft is always required in acrylic parts due to its brittleness, often times twice the draft of other materials. Acrylic also has poor chemical resistance.
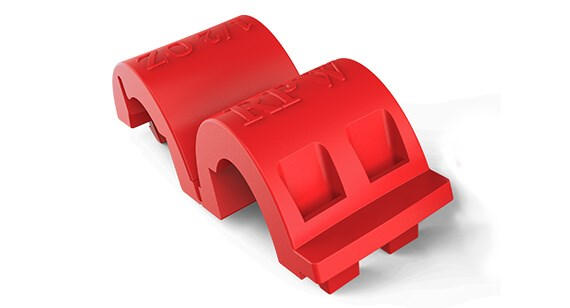
PP (Polypropylene)
Benefits: PP is an inexpensive resin option with higher impact resistance in some grades; propylene homopolymer can be brittle in cold temperatures, with copolymers more resistant to impact. PP is wear-resistant, flexible and can have very high elongation. It’s also resistant to acids and bases.
Applications: integral hinges or living hinges, fans, snap-over lids (e.g., shampoo bottle tops), medical pipette tubing.
Considerations: Thick sections in part geometry can void and show bubbles. Shrink and warp may also occur in PP parts. If the part has living hinges that require higher stiffness, K-Resin is a good alternative.
PBT (Polybutylene Terephthalate)
Benefits: PBT provides good electrical properties for power components and works well for automotive applications. It has moderate to high strength depending on glass fill; unfilled grades are tough and flexible. PBT also has good resistance to fuels, oils, fats and many solvents, and doesn’t absorb flavors.
Applications: Slide bearings, gears and cams; coffee makers and toasters; hair dryer nozzles; vacuum cleaners; handles and knobs for electrical cookers.
Considerations: Glass-filled PBT resins are prone to warp, and have poor resistance to acids, bases and hydrocarbons. Thin parts can also be hard to fill with PBT. Nylons should be considered as alternatives.
PPSU (Polyphenylsulfone)
Benefits: PPSU is a high-temperature, dimensionally stable material with high toughness and heat resistance. It also has resistance to radiation sterilization as well as alkalis and weak acids.
Applications: Medical instrument components, sterilization trays, automotive fuses, interior aircraft parts, hot water fittings, sockets and connectors.
Considerations: PPSU is sensitive to thick sections in part geometries, which could result in voids, bubbles or sink. Organic solvents and hydrocarbons can also attack PPSU material. Colorant cannot be added to FacFox-supplied PPSU resins.
PEEK (Polyether Ether Ketone)
Benefits: PEEK is one of the most recent materials added to the FacFox menu. It’s a high-temperature, high-performance resin used in medical, aerospace and automotive industries for a variety of reasons including heat resistance and flame retardancy; excellent strength and dimensional stability; and good chemical resistance.
Applications: Bearings, piston parts and pumps; cable insulation; compatible with ultra-high vacuum applications.
Considerations: PEEK is a high-performance material, and, as a result, is very expensive. Ultem (outlined below) is a slightly less-costly option, and PPSU is worth considering if price is a concern.
PEI (Polyetherimide)
Benefits: PEI, or Ultem, is the second of two high-temperature, high-performance resins recently added to the growing list of materials available through FacFox. Like PEEK, it’s used in medical, aerospace and automotive industries for its heat resistance and flame retardancy; excellent strength and dimensional stability; and good chemical resistance.
Applications: Medical and chemical instrumentation; tableware and catering; HVAC and fluid handling; electrical and lighting.
Considerations: Ultem is also very expensive, though not as costly as PEEK. Look at PPSU as a possible alternative.
More material options and information
FacFox has many additional stocked resin options including PPS, TPE, TPU, LCP, HDPE, LDPE and PSU, and most resin properties can be improved by additives such as glass and carbon fiber.
To order material samples, contact your sales rep or email us at info@facfox.com.