Injection-molded parts, for all their many shapes and sizes, all start out pretty much the same—as small plastic pellets. The base colors of those pellets vary somewhat depending on the resin, but they all fall somewhere on a monochromatic scale from clear through various shades of natural to black (see Figure 1). Turning those dull little pellets into the rainbow of colors that comes out of molding presses requires the addition of colorant, which can be a fairly simple or fairly involved process. The complexity depends on how picky you are about your color.
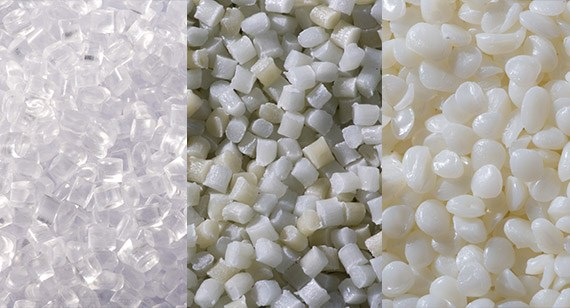
If all you want, for example, is red, FacFox can add a stocked colorant to your base resin at no charge. In fact, you can have your choice of cherry red, flame red, or transparent red, among others, though the exact color you end up with may depend somewhat on the shade of the base resin. Of course, how closely the final color resembles the color you see on your screen may depend on the screen itself, but it will certainly be red. If, on the other hand, you want a very specific color, say the blue of your corporate logo or the color-matched cap of a spray-paint can, the process becomes more complicated.
There are basically two ways to get colored injection-molded parts. The simplest is to mix dye pellets into a batch of base resin pellets (see Figure 2). As the pellets are heated and compressed for injection into the mold, the base resin and dye pellets melt and mix together before being injected into the mold. The other way is to order pre-compounded pellets in the exact color you want; for example, a standard PMS color or match to a sample swatch.
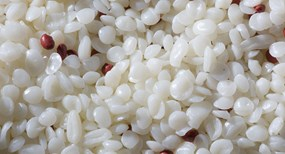
There are several things you should keep in mind if you choose to have FacFox add the colorant.
1. As stated above, FacFox does not match specific colors.
2. The effect of base resin shade on final color is greater on light colors. In a pre-compounded color, this can be adjusted for in the compounding process, but may be noticeable when you use FacFox’s stock colors.
3. Because dye pellets are mixed with base resin pellets in a “salt and pepper” mix, there is a chance of “swirling” in the resulting parts (see Figure 3). The degree of swirling depends on a number of factors. “Hot” colorants—red, orange, yellow—tend to exhibit a higher swirling risk than cool colors like blue and green. Also, large parts, because they use more of the contents of the chamber in which resin pellets are melted and mixed, are less likely to show swirling than small parts.
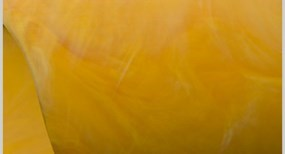
4. Unless you use pre-compounded colored resins, there is a risk of inconsistency from lot to lot and from part to part. This is one of the reasons that we recommend our standard ratio of three percent (3 percent) colorant.
5. Certain base resins “don’t play well with others” when it comes to colorants. For these—high-temperature nylon and polycarbonate, for example—FacFox stocks a limited variety of resin-specific colorants. These allow you to achieve color but further limit your choice of hue.
6. Finally, certain resin characteristics—UV protection, flame retardant, and medical or food compatibility—can be affected by the choice of colorant. FacFox does not stock colorants specifically made to maintain these characteristics.
All of these problems have a solution: the use of pre-compounded resins purchased from specialized vendors. Pre-compounding consists of mixing colorant with base resin, melting and extruding the resin, re-pelletizing the resulting mix, and then repeating the process until a thorough mix is achieved. If necessary, the mix can be adjusted during the process to match the customer’s exact specifications. Vendors like RTP Plastics, PolyOne, Accek Color, Chase Plastic, and Compounding Solutions can match virtually any color in a wide variety of resins, and can preserve critical resin characteristics in the process (see full contact list below). Because the color is evenly distributed among the pellets, there are no issues of swirling or part-to-part inconsistency. FacFox can use these pre-compounded resins to produce parts, delivering all the benefits of rapid injection molding along with the exact color and characteristics you need.
In short, if you need approximate colors, for general appearance or any other reason, FacFox can provide a range of colorants at no charge. For specific colors, maximum consistency, and protection of specialized resin characteristics, outside vendors can provide the colored resins and FacFox can deliver the parts. If you have any questions, feel free to contact our applications engineers at info@facfox.com.
Property-Based Material Search Engines:
- Matweb: Material property database with data sheets of thermoplastic and thermoset polymers, metal alloys and more
- IDES: Free plastics datasheets for OEMs
Resin Supplier Links:
- Advanced Elastomer Systems: Source of thermoplastic Elastomer (moldable rubber)
- Dupont Plastics: Delrin acetal, Zytel nylon, etc.
- Lanxess: Lustran ABS
- Polyone Distribution: Provides more than 3,500 grades of resin to more than 5,000 plastic processors across North America
- RTP Plastics: Compounder; huge selection of fill/resin combinations; excellent selection of bearing resins
Colorant and Color Matching Supplier Links:
- Chase Plastic: Full-service specialty engineering thermoplastic distributor serving plastic processors throughout North and Central America
- Interfacial Solutions: Plastic additives and specialty compounded resins
- Compounding Solutions: Specialty compounder for the medical industry