Wondering what is Fusion 360? Learn more about the popular 3D CAD software tool for hobbyists in this guide!
Fusion 360 is a 3D CAD program by Autodesk. Its name comes from the software’s ability to allow users to go through much of the design pipeline without ever needing to switch programs. It was first launched in 2013 and became an almost instant hit. Fusion 360 has only grown in popularity since.
Its popularity derives from the accessible price, flexible options, and versatile applications. The program can be used for 3D modeling, generative design, failure mode simulation, electrical circuits, manufacturing, and motion animation.
With so many capabilities, Fusion 360 can be a bit daunting and overwhelming to a beginner. So, we’ll give you the rundown of the software’s essentials in this article. Let’s dive in!
Prices & Licensing
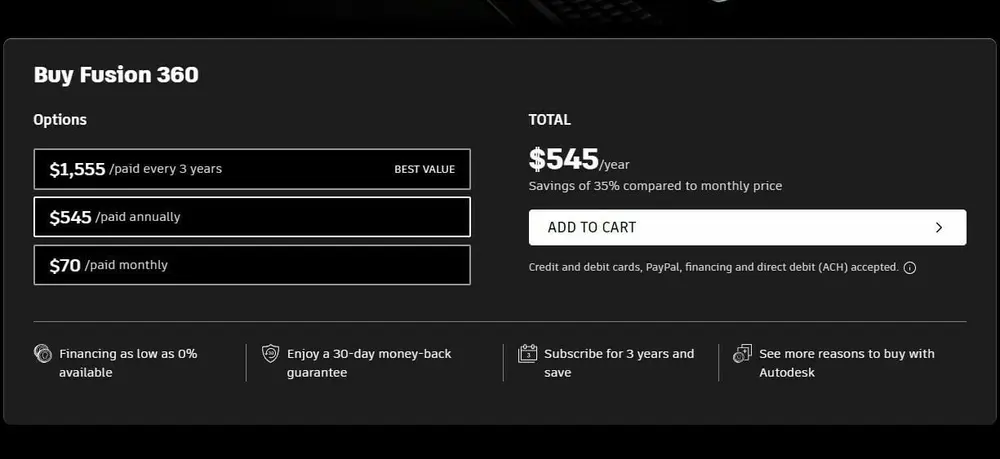
Fusion 360’s license is subscription based, and there are different plans you can choose from:
- Monthly: $70
- Annual: $545 (~$45 monthly)
- Triennial: $1,555 (~$43 monthly)
- Free trial: 30-day free trial
- Student version: Students can access the full program, and it doesn’t matter if their academic institution has a version or not. Simply log in to Autodesk and provide proof of enrollment. Educational licenses are available for one year, after which you have to either renew the proof of enrollment or get a different license.
- Free version: Hobbyists and personal users can get a free, limited version that only has the CAD, CAM, and PCB workspaces.
- Start-up option: If you have a company start-up under three years old with fewer than 10 employees, you can qualify for a free version of the full software.
System Requirements
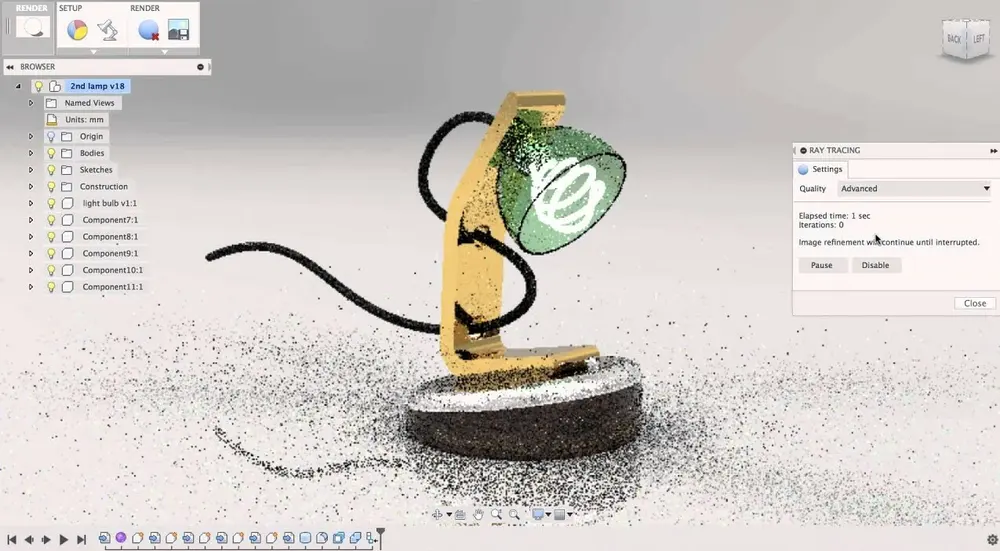
Fusion 360, like most Autodesk programs, is available for Windows and MacOS. Below are the recommended specifications to run Fusion 360:
- OS: Windows 8.1 (until March 2023), 10, or 11; MacOS 10.15.7 Catalina (until March 2023), 12 Monterey, 11 Big Sur
- CPU: 64-bit processor, six or more cores, 1.7 GHz Intel Core i3, AMD Ryzen 3 or greater
- RAM: Minimum 8 GB
- Graphics card: At least 1 GB of VRAM
- Disk space: 3 GB of disk space for installation – keep in mind that your computer needs even more than that free to run properly
In addition to the requirements listed above, a three-button mouse is highly recommended.
UI & Layout
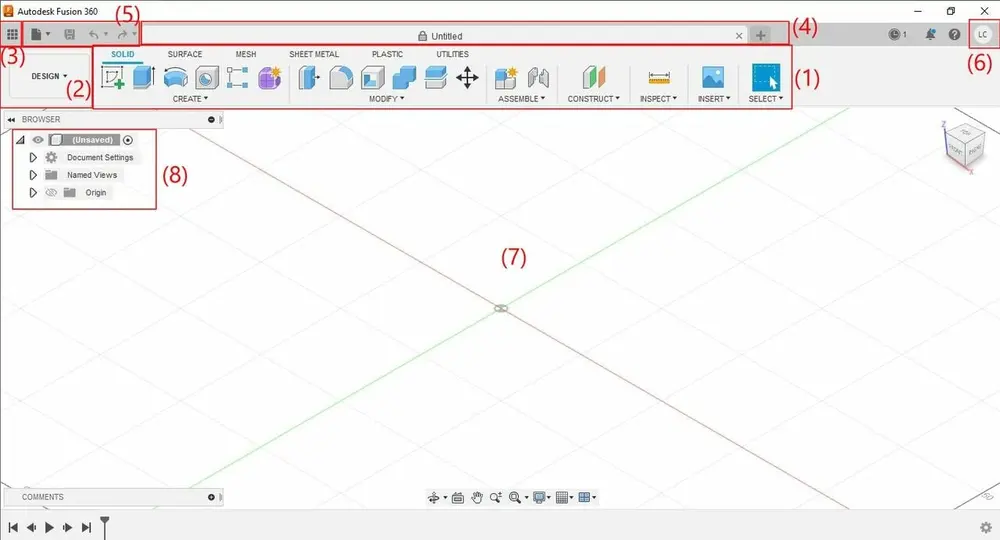
As mentioned previously, Fusion 360 has many features, and to organize them, it uses workspaces.
Main Toolbar
The Main Toolbar (1) is where you find the essential tools. You can see the current workspace (2) on the left. When you switch workspaces, the available tools will change as well, and they’re organized in tabs to help better locate everything.
In this example, we’re in the Design workspace, and you can see the various tools in the Main Toolbar organized in tabs, including Solid, Surface, and Sheet Metal, among others.
Application Bar
Above the Main Toolbar are the Application Bar (3) and the tabs for any open files (4). From the Application Bar, you can open the application menu or use the Quick Menu (5) for things such as Save, New Project, Undo, and Redo.
To the right of the Main Toolbar, you can see your Profile (6), where you can manage your license and projects saved in the cloud.
Canvas
The main working area where you see the model is called the Canvas (7). To the right of the canvas, you find a floating menu called the Browser (8) that lists every available feature on the Canvas, including solids, meshes, and even measurement systems.
The Making Menu is a floating right-click menu with commonly used tools. When you use a feature – for example, a milling operation in the Manufacturing workspace – a setup window opens up where you finish setting up the feature. While this isn’t something you can immediately see when opening the application, some additional tools may be located in that window.
Features & Functions
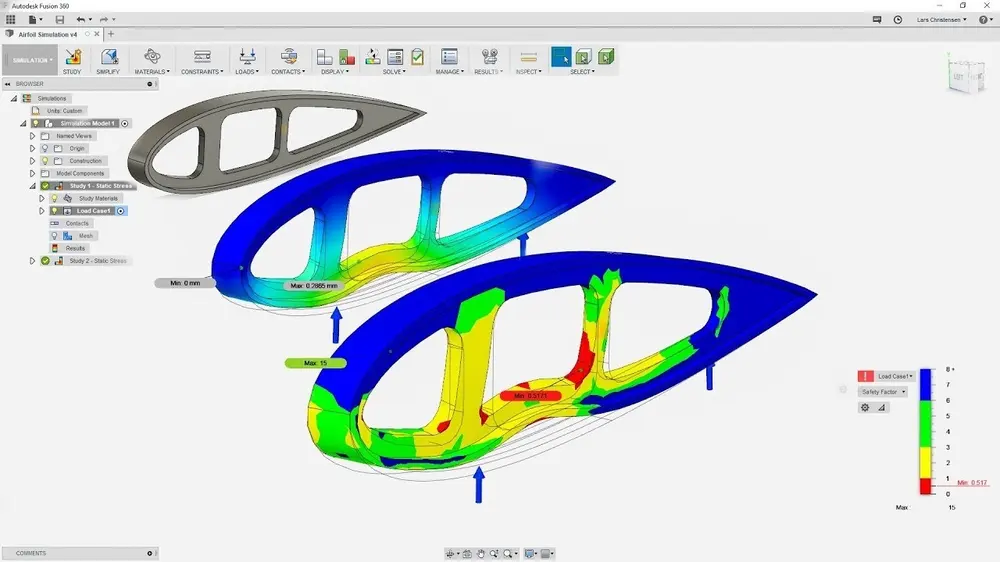
Since Fusion 360 has such a wide range of features and functionalities, we’ll give you a rundown of the workspaces and what they’re able to do.
Design
In this workspace, you can model parts from scratch or imported files. You can draw sketches and use operations such as Extrude and Revolve to make them into 3D volumes. Additionally, it has Surface, Mesh, and Sheet Metal modeling tools, as well as Plastic, which is for injection mold design. The Utility tab includes options to check interference or measurements.
Generative Design
Generative Design is one of the most unique capabilities of Fusion 360. It takes a structure in an existing model and optimizes it, reducing material spent while attempting to improve shear and normal resistance. It provides an analysis of these factors as well.
Render
Fusion 360 has very good and surprisingly fast rendering capabilities, especially compared to software like SolidWorks, which is quite slow in rendering. You can create realistic renders with different materials and backgrounds. Rendering is a useful tool when presenting a design proposal, as it allows you to see a representation of your design in the real world.
Animation
The animation suite is made to create motion animations of a system. The principle is very simple: You choose a fixed part (a part that acts like an anchor to the system) and an input part (a part that enforces rotation or translational motion), then check out how the complete assembly moves. It’s also possible to record and export videos of the animation.
Simulation
Fusion 360 uses finite element analysis to evaluate the mechanical properties of your model. It does so graphically, meaning you don’t need to concern yourself with the theory and programming behind it. It’s enough for some industries but not for academia and specialized industries like aerospace requiring greater precision.
Manufacture
This workspace is one of the most powerful and popular parts of Fusion 360. It has tools for milling, turning, and 3D printing, located under the Additive tab. It can do operations like contouring, face milling, and engraving for 2D and 2.5D CNC. You can simulate the path of the operations and have multiple operations inside one G-code file.
User Experience
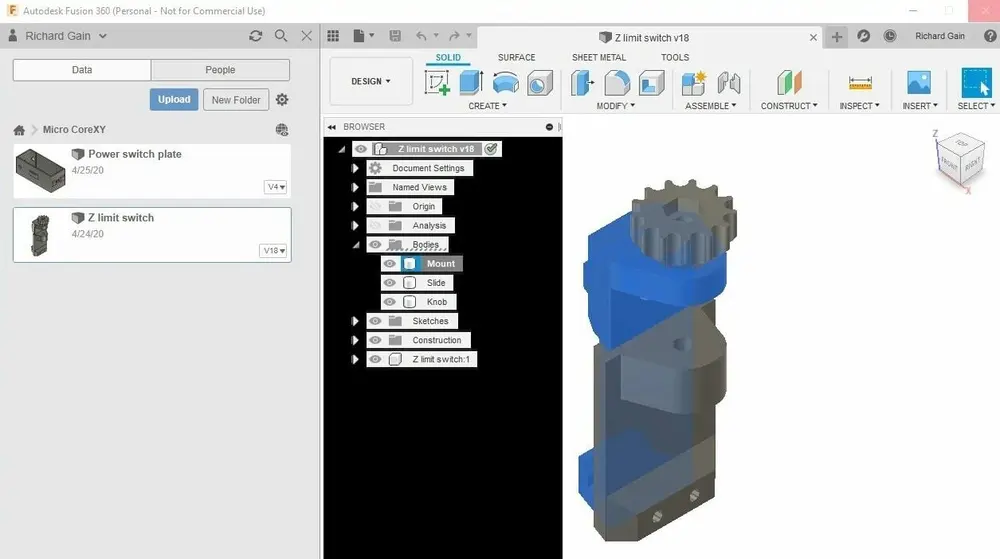
Fusion 360 is a very stable software once running, but launching the software and loading an existing file can take several minutes. If you’ve never done any 3D modeling, this program offers advantages and disadvantages. On one hand, it’s extremely accessible. You can start learning it on your own to prepare for future endeavors, start your own startup, or just start designing your ideas. This is in contrast to software like SolidWorks, which is extremely expensive. Individuals usually have to get a license through their company or educational institution.
On the other hand, even though the software uses a lot of symbols to indicate the purpose of tools, the actual design process in Fusion 360 isn’t as intuitive as it could be. You have to know your way around and understand that many setups require right-clicking to open menus.
Use Cases & Applications
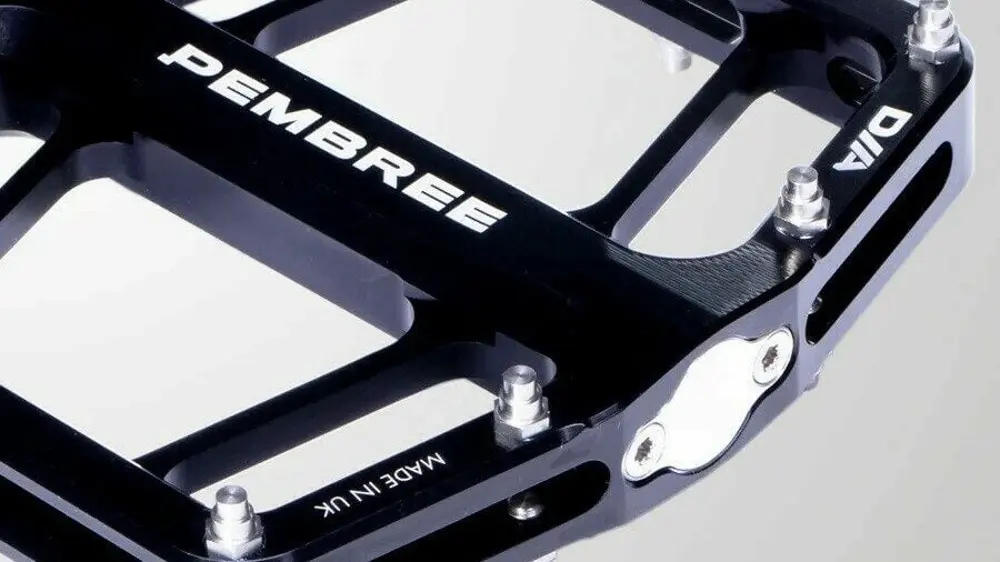
Fusion 360 is used for design by independent users, hobbyists, and start-ups thanks to its accessibility. On top of that, it’s one of the most popular programs for CAM because it’s complete and has a very user-friendly UI and good quality simulation. It allows for a lot of customization of operations needed on a project – all at a very affordable price. Fusion 360 also prioritizes cloud storage over hard disk storage, which makes it better suited for collaborative work.
One example of a company that uses Fusion 360 is Pembree. They use the software to design bicycle components such as bike pedals. Thanks to Fusion’s 5D CAM operations, they also use it to plan their manufacturing. Another example is Iterate, which uses Fusion 360 for feasibility studies that aim to determine the functionality, manufacturability, and marketability of a product.
Company & Community Support
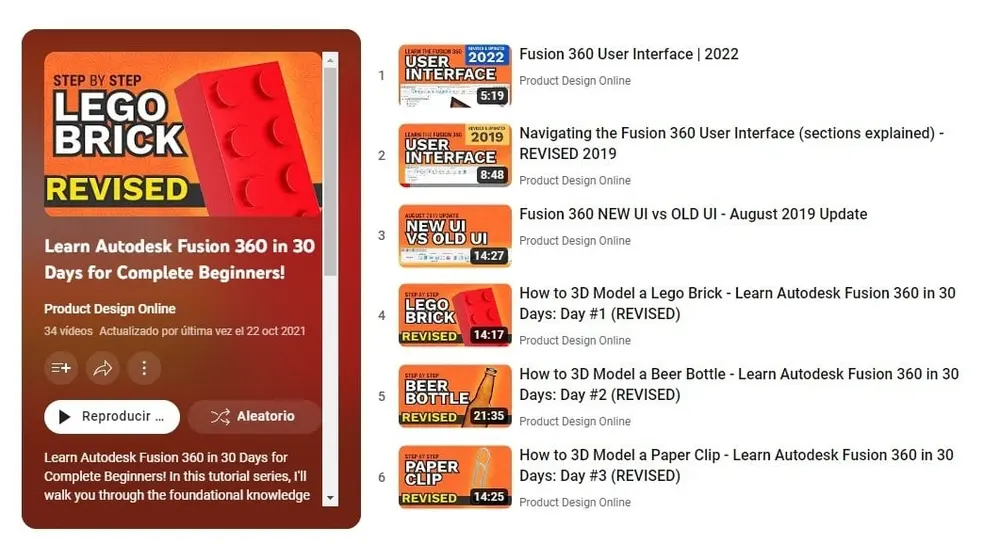
Fusion 360 has a dedicated site filled with resources, self-paced learning, and webinars. They also have the Community Forum for posting questions and troubleshooting. A good unofficial resource is the Fusion 360 subreddit, which is relatively responsive to questions. Finally, YouTube is filled with tutorials and resources for all things Fusion 360. You can try keywords such as simulation, CAM, or beginner to help you find more specific information.
If you want some resources to get started, Product Design Online’s Learn Fusion 360 in 30 days is one of the most recommended Fusion 360 courses. This course is completely free on YouTube, including the necessary demo files, but you can support the creator on other platforms.
Alternatives
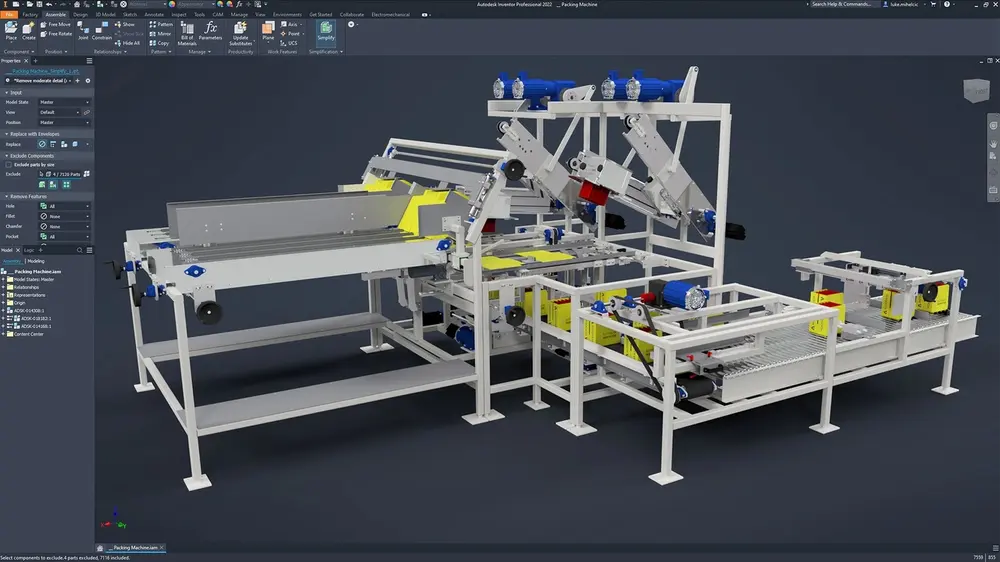
Now that you know all the basics about Fusion 360, perhaps you have decided that it is not for you after all, or maybe you want to see what else is out there before making a commitment. In that case, you can also check these alternatives and see if something else is a better fit.
The following are Fusion 360’s direct competitors. They share many aspects, but in the end, the devil’s in the details.
- Inventor is like a more optimized and powerful version of Fusion 360. It’s a more industrial and bigger-scale option. However, the main disadvantage is the price, at about $2,300 annually.
- SolidWorks is Fusion 360’s and Inventor’s most direct competitor. It’s by a completely different company, Dassault Systèmes. Since it’s an industry staple, learning it can open many doors. However, it’s also very expensive. Purchasing it yourself can be complicated because you can’t buy it online; you have to contact an authorized reseller (called “VAR”) and get a personalized quotation.
- FreeCAD is a free and open-source 3D CAD program. Since it also has many workbenches, you wouldn’t be sacrificing functionality too much. The main disadvantage, however, is that it’s way less stable. Also, the design workflow in FreeCAD isn’t the most optimized, as it’s still a work in progress and open source.