The process sure sounds cool, but you might have caught yourself wondering: What is a laser cutter? Dig into this lengthy guide where break down laser cutting.
Introducing the Laser Cutter
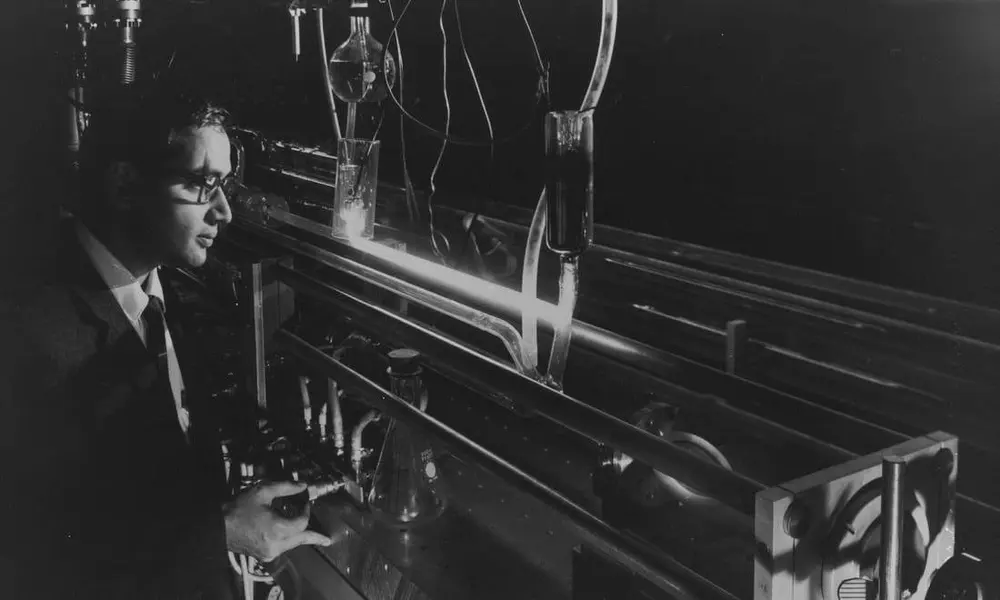
As the name suggests, laser cutters create patterns and designs by cutting into materials. A powerful laser beam is the source that melts, burns, or vaporizes the material.
Essentially, laser cutting is a fabrication process that uses a thin, focused, laser beam to cut and etch materials into custom designs, patterns, and shapes as specified by a designer. This non-contact, thermal-based fabrication process is ideal for several materials, including wood, glass, paper, metal, plastic, and gemstone. It’s also capable of producing intricate parts without needing a custom-designed tool.
A Bit of Background
The invention of the laser cutter is attributed to Kumar Patel, who began his research in laser action when he joined Bell Labs in 1961. In 1963, he developed the first C02 laser, which is the variant with more modern applications than any other type of laser. C02 lasers are for engraving materials ranging from acrylic and plywood to cardboard and MDF.
Applications
Today, laser cutting has found a home in industries such as electronics, medicine, aerospace, automotive, and semiconductors. One of the most common applications is for cutting metal – whether its tungsten, steel, aluminum, brass, or nickel – because lasers deliver clean cuts and smooth finishes. Lasers are also used for cutting ceramics, silicon, and other non-metals.
Perhaps one of the most intriguing uses of laser cutting technology is in the surgical field, where laser beams are now replacing the scalpel and are being used to vaporize human tissue. This is especially useful in high-precision surgical procedures like eye surgery.
We’ll talk about more applications in a later section, but for now, let’s see how the laser-cutting process works.
How Laser Cutting Works
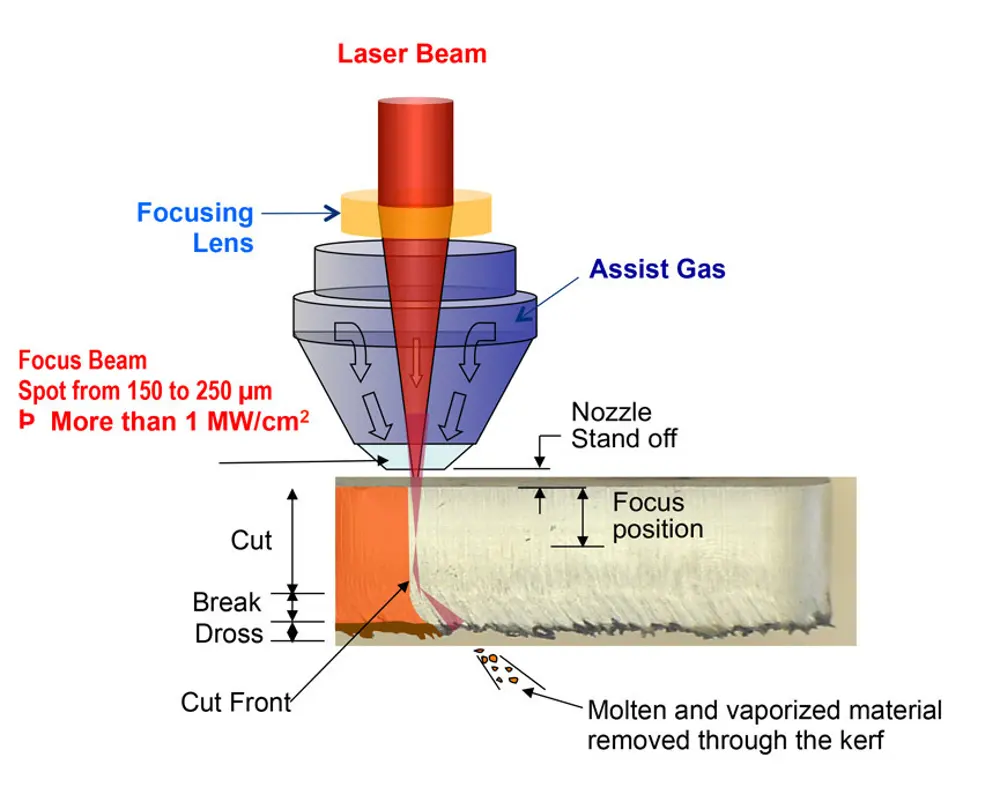
A laser cutter’s beam usually has a diameter between 0.1 and 0.3 mm and a power of between 1 to 3 kW. This power needs to be adjusted depending on the material being cut and the thickness. To cut reflective materials like aluminum, for instance, you may need laser powers of up to 6 kW.
Laser cutting is not ideal for metals like aluminum and copper alloys because they have excellent heat-conductive and light-reflective properties, meaning they need powerful lasers.
Below are some core components of a laser cutter:
- The Laser Resonator: The laser beam emanates from a laser resonator, an airtight glass tube with two mirrors that face each other. The tube is filled with C02 and other gases like hydrogen, nitrogen, and helium. The mix of these gases is activated by diodes or an electric discharge that emits energy in the form of light.
- The Cutting Head: The light bounces in various directions with the assistance of several mirrors that are strategically positioned to ensure it reaches the laser cutting head. Once the beam has reached the cutting head, it passes through a curved lens and is magnified and focused onto a single point. It is within this cutting head that the laser is turned into a thin, concentrated beam, which can cut or raster. The focused laser beam passes through a nozzle before hitting the plate, with compressed gas like nitrogen or oxygen also flowing through this nozzle. If you are cutting aluminum or stainless steel, for example, the laser beam will melt the material before the highly-pressurized nitrogen blows the molten metal out of the kerf. Normally, the cutting head is attached to a mechanical system that is driven by a chain or belt, which allows it to make precise movements within a limited area. The focal point of the lens needs to be on the surface of the material being cut for the laser to make an actual cut.
- Nozzle Distance: At all times, an accurate distance is maintained between the plate and the nozzle. This space is crucial since it determines the focal point. Usually, the quality of the cut will be affected by changing the focal point. Several other variables can affect the cut quality, and they include the beam intensity and speed.
Three Major Varieties of Laser Cutting
- Flame/Reactive Rutting: The assist gas is oxygen, which is blown into the kerf at high pressure (up to six bar). The heated material (metal, in this case) reacts with the oxygen and begins to burn and to oxidize. This reaction expels more energy and assists the laser beam.
- Fusion Cutting/Melt and Blow: An inert gas (typically nitrogen) blows molten material out of the kerf, significantly reducing the power that is required. The material is first heated up until it reaches its melting point then the gas blows it out
- Remote Cutting: A high-intensity laser beam partially evaporates (ablates) the material, enabling thin sheets to be cut without the need for an assist gas.
Cutting vs Engraving vs Marking
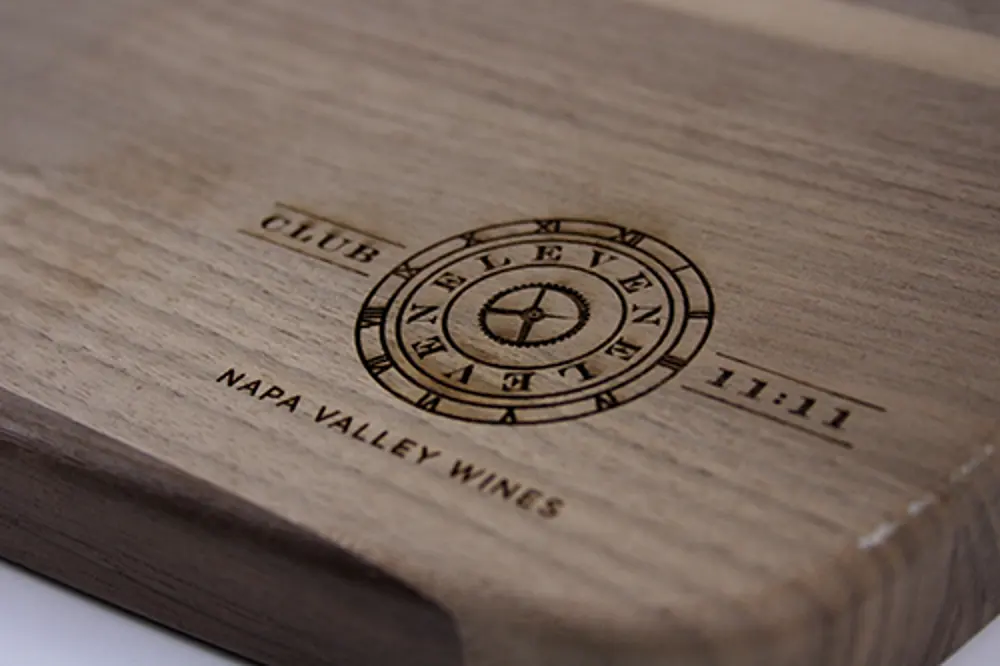
Generally, a laser cutting machine should also be able to engrave and mark. In fact, the only difference between cutting, engraving, and marking is how deep the laser goes and how it changes the overall appearance of the material. In laser cutting, the heat from the laser will cut all the way through the material. But that is not the case with laser marking and laser engraving.
Laser marking discolors the surface of the material being lasered, while laser engraving and etching remove a portion of the material. The main difference between engraving and etching is the depth to which the laser penetrates.
Here’s the difference between marking and engraving:
- Laser Marking: In laser marking, the laser does not go all the way through the material but instead only alters the properties or the appearance of the material. The laser creates high-contrast marks because the heat of the laser redistributes the carbon in the material in question.
- Laser Engraving: In laser engraving, the beam physically removes the surface of the material to leave a cavity that reveals your design. The laser heats the material to very high temperatures, causing it to vaporize and to create a cavity.
The Main Types of Laser Cutters
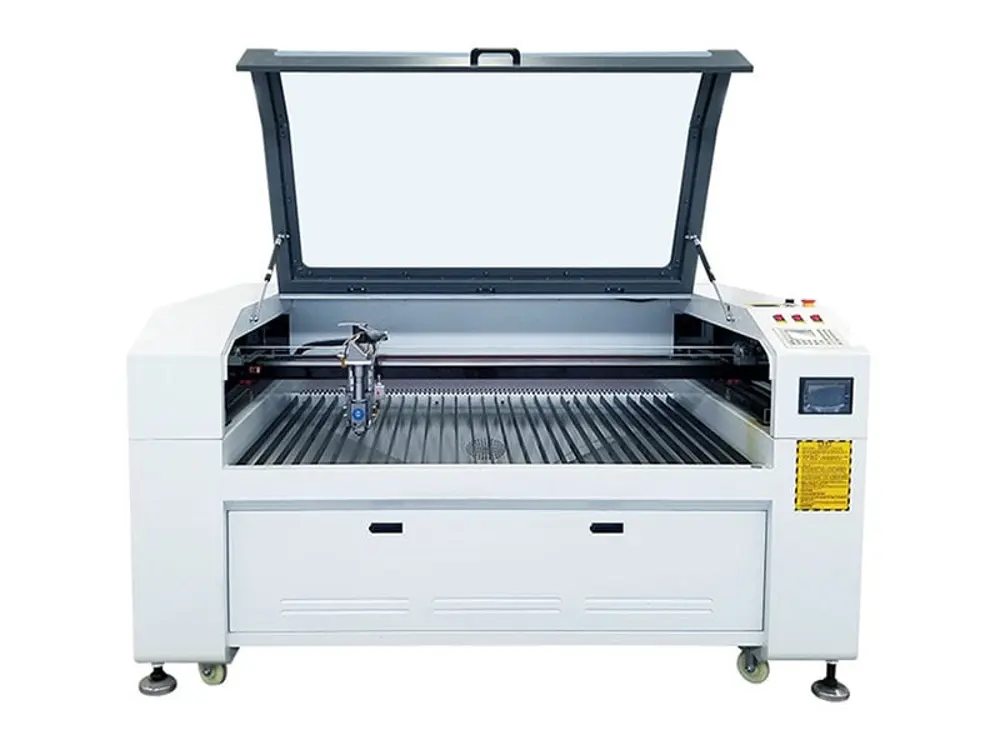
Differences in laser cutters come from the types of lasers in the machines, and the kind of laser determines the type of material thickness the laser may be able to cut. Generally, a high-powered laser will be ideal for professional applications where large sections of plastic or metal need to be cut. On the other hand, a low-power laser is effective for thinner materials like plastics, card stock, paper, and wood.
The three main types of lasers are:
1. Gas Lasers/C02 Laser Cutters
The cutting is done using electrically-stimulated CO₂. The CO₂ laser is produced in a mixture that consists of other gases like nitrogen and helium.
CO₂ lasers emit a 10.6-mm wavelength, and a CO₂ laser has enough energy to pierce through a thicker material compared to a fiber laser with the same power. These lasers also give a smoother finish when used to cut thicker materials. CO₂ lasers are the most common types of laser cutters because they are efficient, inexpensive, and can cut and raster several materials.
Materials: Glass, some plastics, some foams, leather, paper-based products, wood, acrylic
2. Crystal Laser Cutters
Crystal laser cutters generate beams from nd:YVO (neodymium-doped yttrium ortho-vanadate) and nd:YAG (neodymium-doped yttrium aluminum garnet). They can cut through thicker and stronger materials because they have smaller wavelengths compared to CO₂ lasers, which means they have a higher intensity. But since they are high power, their parts wear out quickly.
Materials: Plastics, metals, and some types of ceramics
3. Fiber Laser Cutters
Here, cutting is done using fiberglass. The lasers originate from a “seed laser” before being amplified via special fibers. Fiber lasers are in the same category with disk lasers and nd:YAG, and belong to a family called “solid-state lasers”. Compared to a gas laser, fiber lasers do not have moving parts, are two to three times more energy-efficient, and are capable of cutting reflective materials without fear of back reflections. These lasers can work with both metal and non-metal materials.
Though somewhat similar to neodymium lasers, fiber lasers require less maintenance. Thus, they offer a cheaper and longer-lasting alternative to crystal lasers
Materials: Plastics and metals
Out the three, CO₂ lasers are used most commonly, by both makers and professionals. They are used primarily for cutting non-metal materials, and even though they have evolved to cut through metals, they are still better suited for non-metals and organic materials (wood, leather, rubber), and engraving hard materials.
Pros and Cons
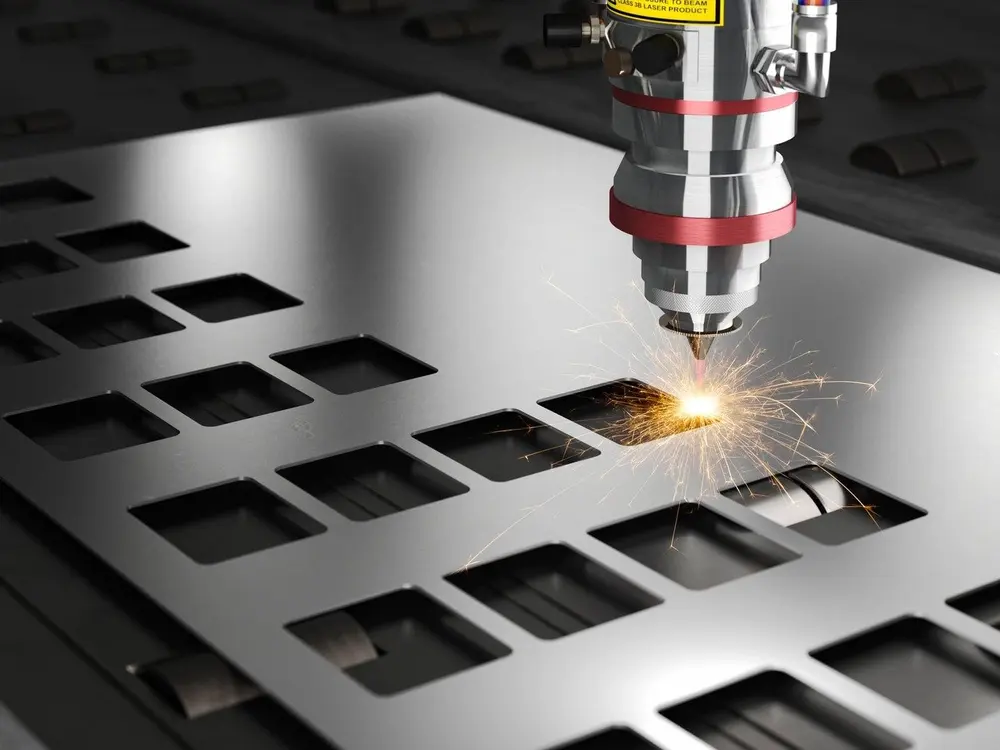
Pros
Here are the reasons why laser cutting is preferred compared to other cutting technologies, such as CNC milling:
- High precision and accuracy
- High production speed
- More affordable than CNC machines of the same caliber
- Wide material compatibility
- No risk of contamination (since it’s a contactless process)
- Narrower kerf widths
Cons
- High energy consumption
- Risk of toxic emissions release (from plastics)
- Thicker materials can be difficult to cut
- Risk of burnt edges at cuts
Buying
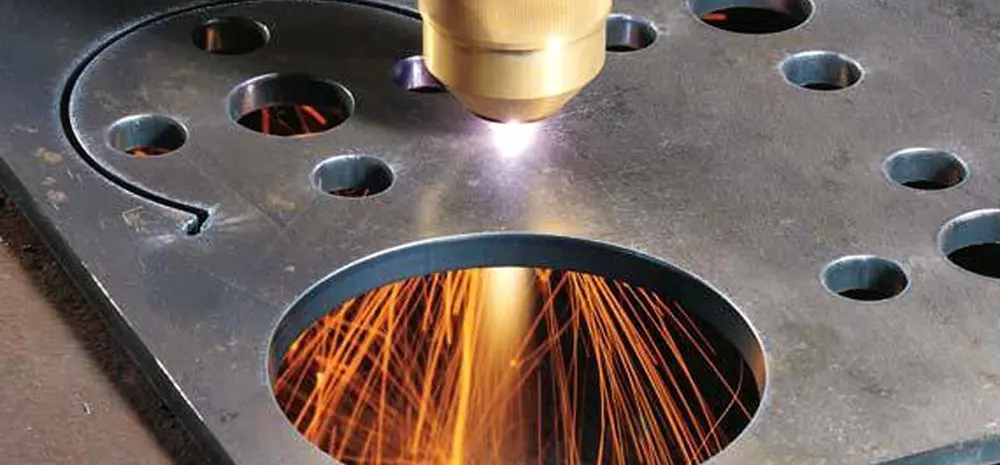
Key considerations when shopping for a laser cutter:
- Support: Several vendors stock cheap laser cutters, but are they reliable enough to provide you with the necessary support when your machine breaks down? How easy is it to find replacement parts?
- Size: The bed size puts a limit on the size of the material you can work with. A bigger bed will let you cut multiple pieces at once while a smaller bed will only allow you to work on one material at a time
- Power: The more the wattage, the more powerful your machine is. And remember, more power means you will cut faster and more reliably. A less powerful laser will slow you down.
- Compatible Materials: You can’t just pick any material and start blasting it with a laser. The composition of the material should guide you when selecting the right laser cutter. Also, note that some materials catch fire while others produce toxic fumes.
There are other concerns like the mechanics of the laser machine and the component parts, both of which can significantly determine how smooth and clean your cut will be.
Here are two of our favorite machines:
For even more, go through our comprehensive list of the best laser cutters.
Designing for Laser Cutting
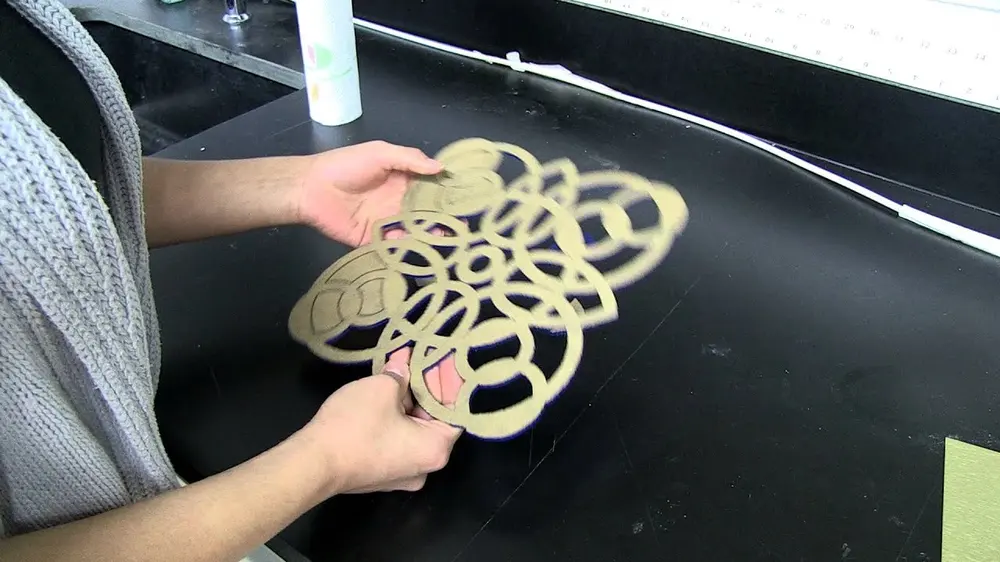
Laser cutters work just like your regular inkjet printers. The machines have certain drivers that enable them to pick designs from the computer and to convert those designs into a readable format.
Several software packages can support the drivers of a laser cutter:
2D Design
3D Design
While the designer’s imagination is theoretically the only limitation to what can be created, here are some general guidelines when designing for laser cutting:
- The design must meet the specifications of your cutter. The finished file must meet the technical requirements of your machine. Otherwise, trying to convert a file may lead to loss of detail or imperfections.
- Know the maximum and minimum laser cutting size and set them right. The size of your design is limited by the dimensions of the cutting table. If the table is 1100 x 1100 mm, you cannot design anything beyond that. Likewise, you should also respect the minimum dimensions.
- Details cannot be smaller than the material thickness. Avoid details that are smaller than the material’s thickness. If you want to make a hole, for instance, its diameter should be bigger than the thickness of the material.
- Maintain a minimum distance between lines. For a given material thickness, a minimum distance must be maintained between lines. As a general rule, let the distance between parts be 2x the material thickness
- The law of physics always applies. When you cut out a piece of metal, it is going to fall off unless there is a connecting piece in the design.
- Show restraint.Your design will fall apart or become fragile when you have many lines intersecting at the same point.
- Closely examine the details. Zoom into the detail and ensure intersections meet where needed.
- Watch out for bend reliefs. Improper bend reliefs will not give you a good cut straight off the laser.
Once the design is ready and has been loaded on the machine, the laser cutting head will move over the metal plate following the directions of the design to cut the part as desired. The laser beam follows the vector file that holds the design to cut away at the material until the shape/pattern is completed.
Laser Cutter Applications
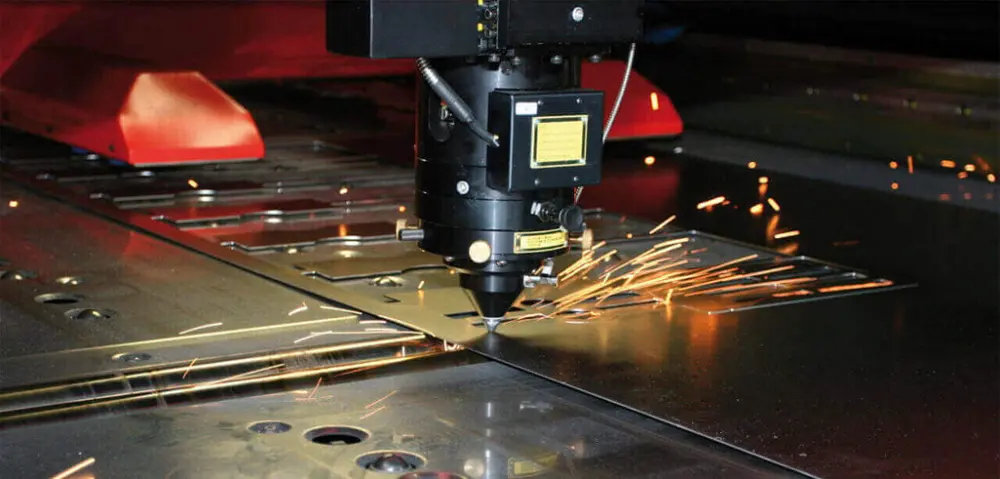
Laser cutters have become handy tools for prototyping and manufacturing. They are being used:
- in rapid prototyping, because they allow designers to quickly and cheaply iterate on their designs before producing in large scale.
- in machine shops as well as in industrial manufacturing to cut large pieces of materials.
- in hardware companies to create prototypes.
- in education for prototyping/small projects.
- by artists and makers who want to bring to life their digital designs.
Feature image source: soulcraftcle.org