Surface energy plays a pivotal role in the bonding process. For an adhesive to bond effectively, it must wet the surface of the material, spreading over it and penetrating any surface pores. This action replaces any gases adsorbed on the material’s surface, transitioning from point contact to surface contact. Additionally, a strong interaction between the adhesive and the material is necessary to form secondary or primary valence bonds.
Factors Affecting Bonding Strength
- Wettability: Determined by the surface energy of both the adhesive and the material.
- Adhesion Force: Includes mechanical fitting force, intermolecular force, and chemical bond force.
- Surface Treatment: Often crucial for achieving a strong bond, especially for plastics with low surface energy.
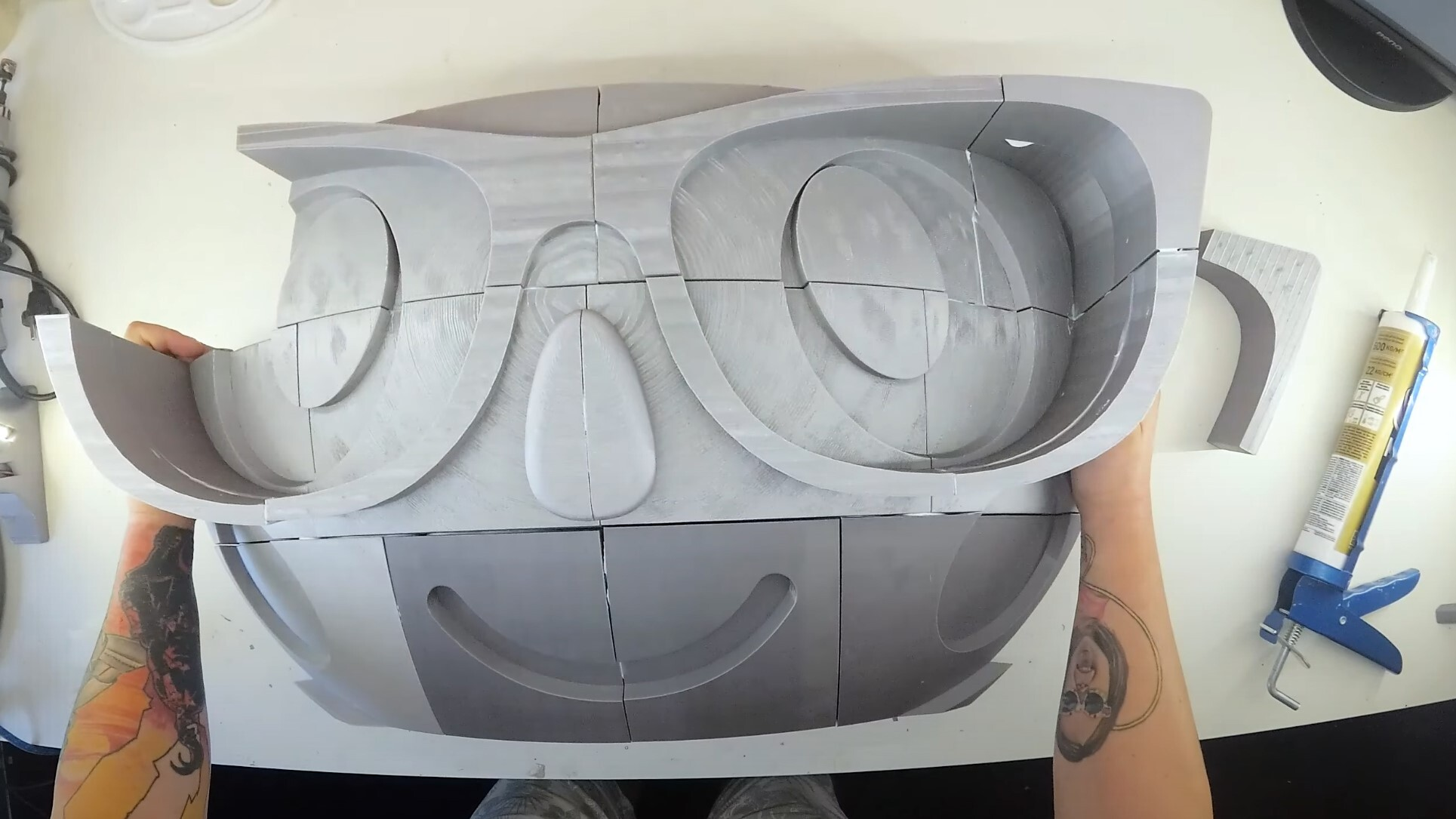
Daily Applications of Surface Energy
- Metal Surfaces: Typically have high surface energy, allowing adhesives to wet them effectively. However, contaminants can reduce this energy, impacting the adhesive’s performance.
- Polytetrafluoroethylene (PTFE): Known for its low surface energy, making it challenging for adhesives to bond to it.
- Low Surface Energy Materials: Offer hydrophobic and oleophobic properties, useful in creating anti-fouling coatings and serving.
Surface Treatment for Effective Bonding
Why Surface Treatment Matters
Surface treatment significantly impacts the success of adhesive bonding. Consider the following factors:
- Contaminants: Plastic surfaces often harbor oil, mold-release agents, dust, fingerprints, and other pollutants. These impurities hinder adhesive wetting, affecting bonding strength.
- Surface Roughness: Creating a rough surface increases the actual bonding area of plastic components. Rough surfaces also allow cured adhesives to form more mechanical interlocks, enhancing bonding strength.
Methods of Surface Treatment
Surface treatment methods vary based on the material and its properties. Here are some common techniques:
- Cleaning: Removing contaminants is essential. Properly cleaned surfaces ensure better adhesive wetting.
- Surface Etching: Roughening the surface to enhance mechanical interlocking. Techniques include sanding, grit blasting, or chemical etching.
- Plasma Treatment: Using low-pressure plasma to activate the surface and improve wettability.
- Flame Treatment: Brief exposure to an open flame modifies the surface energy, aiding wetting.
- Corona Treatment: Applying high-frequency electrical discharge to increase surface energy.
Design Considerations for Adhesive Bonding
When designing adhesive joints, keep the following principles in mind:
- Joint Types: Consider whether the joint will experience tension, shear, peel, or cleavage forces.
- Matching Stiffness: Use adhesives with stiffness similar to or compatible with the adherent material to minimize stress concentration.
- Overlap Joints: For high-stress situations, consider lap joints or other reinforcing techniques.
- Ease of Assembly: Design joints that facilitate the adhesive process.
- Thermal Expansion: Choose materials with similar coefficients of thermal expansion to minimize stress during temperature changes.
- Continuity and Uniformity: Ensure continuous and uniform adhesive layers.
- Integration with Other Components: Consider ease of assembly and maintenance.
- Manufacturability: Opt for designs that are easy to produce and aesthetically pleasing.
Selecting the Right Adhesive
Choosing the correct adhesive is both critical and challenging. No adhesive is truly universal. Each type has specific performance characteristics, process requirements, and usage limitations. Some guidelines:
- Know the Types: Familiarize yourself with various adhesive types and their properties.
- Material Understanding: Understand the characteristics of plastic materials you’re bonding.
- Purpose Clarity: Clearly define the purpose of the bond (e.g., load-bearing, sealing, repairing).
- Environmental Considerations: Account for temperature, humidity, and chemical exposure.
- Process Feasibility: Consider the practical implementation of the chosen adhesive.
Balancing Requirements and Cost
While no adhesive is truly “one-size-fits-all,” balancing requirements and cost is essential. Compare different adhesives, analyze their strengths, and choose the most suitable option. Remember that thorough selection pays off in performance and durability.
The world of adhesives is as complex as it is fascinating. By understanding the intricate dance of surface energy, wettability, and adhesive forces, we can create bonds that are not only strong but also durable and reliable. Whether it’s for industrial applications or everyday fixes, the right adhesive can make all the difference. As we continue to innovate and improve adhesive technologies, we open up new possibilities for construction, repair, and design. The future of adhesion is sticky, in the best possible way.