With the benefits of reduced material waste and the ability to create lightweight designs, titanium 3D printing is finding its niche in many industries. Titanium has excellent material properties, but its high cost has historically limited its use to high-value applications in aerospace. Now that metal 3D printing is becoming increasingly recognized as a viable manufacturing method, the technology is making titanium more available to industries like medical, automotive, and motorsports. This article aims at explaining what makes titanium a good choice for 3D printing, the technologies that support the material, as well as key industrial applications.
Why 3D Printing is Suitable for Titanium
Titanium can be a difficult metal to work with, particularly when it comes to machining. For one thing, titanium has low thermal conductivity. This means that when it is machined, for example with a CNC machine, the heat generated is stored in the CNC tool – which could cause the tool to wear out quickly. Additionally, since machining involves the cutting and removal of material, the process can lead to a lot of material waste being produced. Many companies are, as a result, looking for better alternatives to produce titanium parts. Metal 3D printing is proving to be a viable alternative. With metal 3D printing, the most commonly used grade of titanium is the alloy, Ti6Al4V (Ti64). In addition to Ti64, it’s also possible to 3D print with pure titanium.
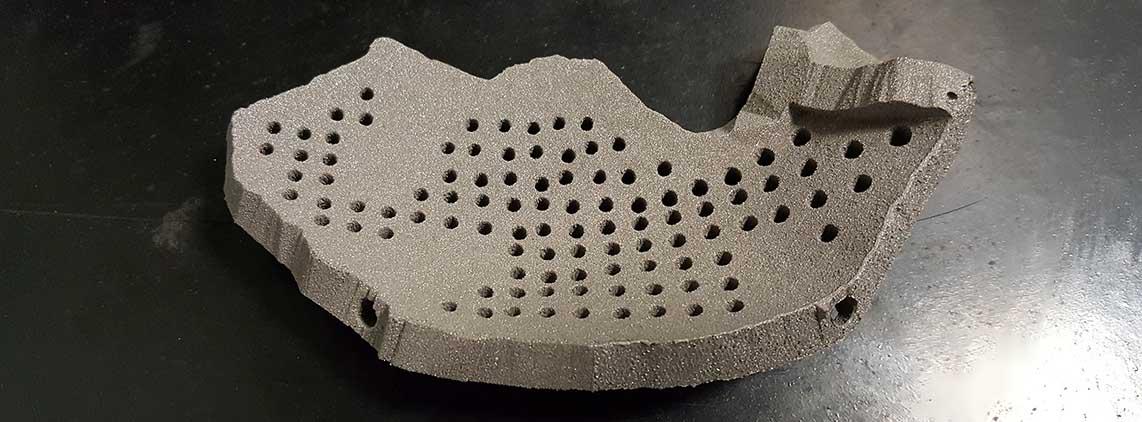
Technologies that Support Titanium
Direct Energy Deposition(DED)
In DED, a high-intensity energy source such as a laser or a beam is used to melt the titanium powder (or wire) as it is deposited through a nozzle onto the substrate. The key benefit here is the ability to create large parts at a relatively high material deposition rate (up to 320 cc/h). Today, there are many variations of DED technology, including Sciaky’s Electron Beam Additive Manufacturing (EBAM) and Wire Arc Additive Manufacturing (WAAM).
Electron Beam Melting(EBM)
EBM is considered to be more accurate than DED, and suitable for smaller, complex parts. Notably, the EBM process takes place in a vacuum and at a high temperature. This results in minimal residual stresses in 3D-printed parts, which also means the parts don’t require subsequent heat treatment.
Selective Laser Melting(SLM)
Like EBM, SLM is a powder bed fusion process, although it uses a laser beam instead of an electron beam to melt and fuse the layers of metal powder. The thickness of one layer in the SLM process can be as thin as 20 microns, making this technology much more accurate when compared to DED and EBM.
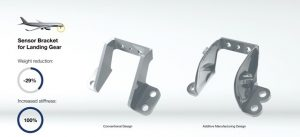
Benefits
Lower the buy-to-fly ratio.
The term, which comes from the aerospace industry, refers to the correlation between the weight of the amount of material originally purchased and the weight of the finished part. In conventional manufacturing, for example, titanium aircraft components may have a buy-to-fly ratio between 12:1 and 25:1. This means that 12-25kg of raw material is required to produce 1kg of parts. In this scenario, up to 90% of the material is machined away. Metal 3D printing can reduce this ratio for titanium components to between 3:1 and 12:1. This is because metal 3D printers typically use only the necessary amount of material needed to create a part, generating only a little waste from support structures. For an expensive material like titanium, the cost-savings from this reduced buy-to-fly ratio can be quite significant.
Enhance the lightweight properties of titanium with topology optimization.
Using topology optimization software, engineers set certain requirements, such as load and stiffness constraints and then let the software tool to optimize the initial design to meet those requirements. Through this optimization, any unnecessary material is removed from the design, creating a lighter yet strong component. Topologically optimized designs can often only be manufactured with the help of additive m manufacturing technologies. This benefit is particularly valued by the aerospace industry, where lightweight 3D-printed titanium parts can lead to weight savings and better aircraft performance.
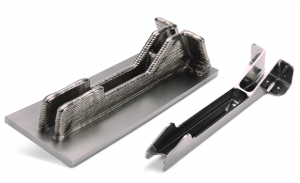
Limitations
Expensive
Unfortunately, just because it is common doesn’t mean it’s cheap. As the titanium needs to be optimized for the 3D printing process, added onto cost of extraction and purification, titanium powder will cost around $450 per kilogram. This is a key barrier to wider titanium 3D printing adoption, though costs have fallen over recent years.
Less Reliable
On a similar note, the difficulty involved in 3D printing titanium requires high skilled operators to produce a reliable product. And without proper attention, you could seriously undermine your own work.
More than other materials, titanium is extremely susceptible to striation, where cracks and separation can affect the product. These will make the part completely unusable in industries like medicine, where nothing less than perfection is acceptable.
Lack of Scale
The main aspect working against titanium 3D printing in its common form is the potential for scalable printing. The technology simply cannot function beyond printing small parts.
DMLS printers currently are limited to small build volumes, making them unsuitable for printing beyond small individual components. While new techniques are in development to change this, the reality is a handicap on the progression of titanium 3D printing.
Challenges
Not everything can be 3D printed in titanium, however — at least not yet. Because it cannot be joined together the way that steel can there are size limitations to what titanium objects are suitable to be 3D printed. Something like the individual parts for a bicycle frame, a knee replacement, a cell phone case or a valve for an engine are all easily fabricated — although large components that need to be made as a single part wouldn’t be a good idea.
Nor would any objects that have multiple angular shapes or edges due to the powder bed process being unable to prevent some striation to remain after the sintering process.
Besides, there are some challenges faced by general metal printing: porosity, density, residual stress, cracking and warping, surface roughness, etc.
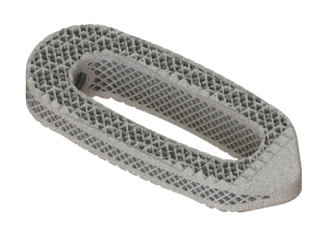
Titaniums and Titanium Alloys for 3D Printing
- Titanium 6Al-4V, grade 5
It’s the most commonly used in titanium alloy in additive manufacturing and is ideal for prototypes and functional parts in the aerospace and automotive fields and for military applications. It is also an excellent material for the manufacture of parts with complex geometry, precisions or production tooling. - Titanium 6Al-4V, grade 23
It’s a biocompatible alloy is commonly used for medical implants and prostheses. - Titanium Beta 21S
It exhibits a higher strength than conventional titanium alloys such as Ti-6Al-4V and has superior oxidation resistance and creep resistance compared to conventional titanium alloys such as Ti-15V-3Cr. Grade 21 Titanium has one of the lowest hydrogen uptake efficiency levels of any titanium alloy. It an ideal candidate for orthopedic implants and aerospace engine applications. Beta titanium is widely use in the orthodontics. - Cp-Ti (Pure Titanium), grade 1, 2
They are extensively used in the medical field for a wide range of applications, due to the biocompatibility of titanium with the human body. - TA15
It is a near-alpha titanium-alloy with additives of aluminum and zirconium. The high specific strength of components made of TA15 combined with their high load-bearing capacity and temperature resistance enable them to be used for heavy-duty components in aircraft and engine construction.
Industries and Applications that Embrace Titanium
Sector | Properties | Applications |
---|---|---|
Aerospace | Corrosion resistance High strength-to-weight ratio High-temperature resistance | Airframe and wing structures Smaller parts like compressor blades, rotors and other turbine engine components |
Medical | Excellent strength Biocompatibility (non-toxic, non-allergenic) | Orthopedic devices like spine, hip and knee implants. |
Automotive & Motorsports | Corrosion resistance High strength-to-weight ratio High-temperature resistance | Brake calipers, brackets, wheel rims, uprights. |
Think strong, light and corrosion-proof, and you have the essence of what makes titanium such a sought-after material. Titanium is known for its excellent material properties — as strong as steel but with only 60% of its density. Titanium’s high strength-to-density ratio, good corrosion resistance and chemical resistance make it particularly desirable for high-performance industries like aerospace and defence. Here, titanium alloys are used in applications that require lightweight parts able to retain their mechanical properties at high temperatures. Titanium is also known for its biocompatibility, which makes it an ideal choice for medical applications, such as implants. However, while titanium offers a range of benefits, it remains a relatively expensive material. This is because the metal is mined in relatively small quantities, and processing raw titanium remains a complex task, making the material considerably more expensive than alternative metals like steel.
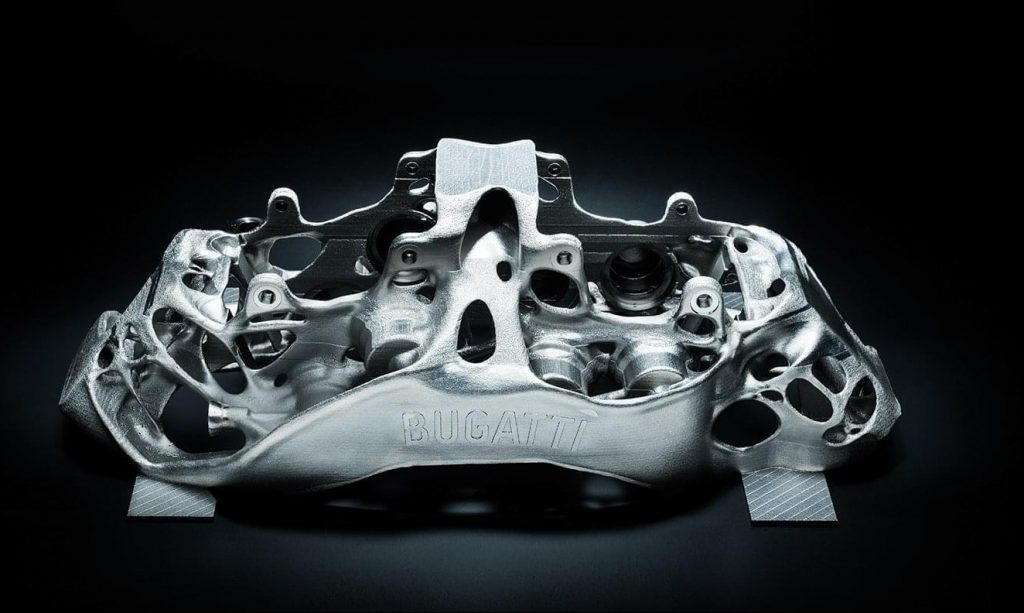