Metal powder is one of the key ingredients for metal 3D printing, especially for powder bed fusion processes such as selective laser melting (SLM) and electron beam melting (EBM). However, metal powder is also one of the most expensive and scarce resources in the industry, as it requires high-quality and high-purity raw materials and sophisticated production methods. Therefore, many 3D printing users and service providers are interested in reusing the leftover powder from previous builds to reduce costs and waste.
But how does powder reuse affect the quality of 3D-printed metal parts? Is it possible to achieve consistent and reliable results with recycled powder? What are the best practices and challenges for powder management and recycling? In this post, we will explore these questions and share some insights from the latest research and industry experience.
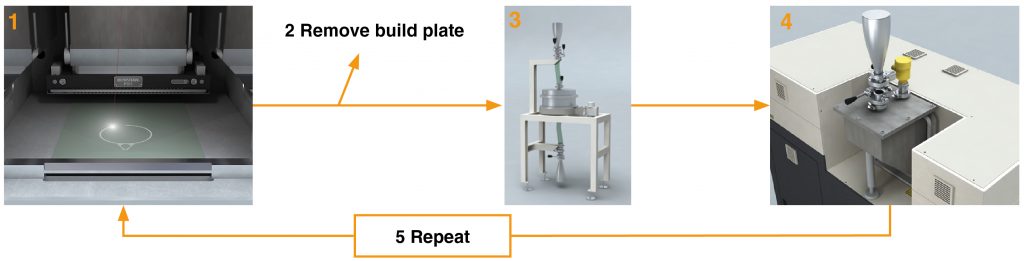
The Effects of Powder Reuse on 3D Printed Metal Part Quality
One of the main factors that influence the quality of 3D-printed metal parts is the morphology and composition of the powder particles. Ideally, the powder should have spherical and smooth particles with uniform size distribution and minimal contamination. This ensures good flowability, packing density, and melting behavior of the powder during the 3D printing process.
However, when the powder is reused multiple times, it can undergo physical and chemical changes that degrade its quality. For example, some of the powder particles can be partially melted, sintered, or oxidized during exposure to high temperatures and reactive gases in the build chamber. This can result in irregular shapes, rough surfaces, increased porosity, and altered composition of the powder particles. These changes can affect the flowability, packing density, and melting behavior of the powder, leading to defects such as pores, cracks, or inclusions in the 3D-printed parts.
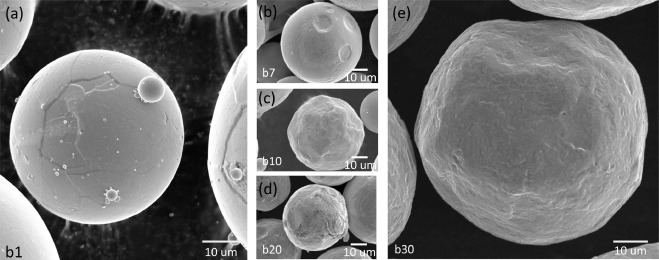
According to a recent study by researchers from the University of Washington, the reuse of Ti6Al4V powder for EBM 3D printing over 30 build cycles resulted in significant morphological and surface degradation of the powder particles. The researchers observed that the smaller particles tended to fuse together and adhere to the larger ones, creating agglomerates and satellites. They also found that the larger particles suffered considerable damage and deformation, losing their spherical shape and smooth surface. The study concluded that these changes could affect the flowability and packing density of the powder, as well as the microstructure and mechanical properties of the 3D-printed parts.
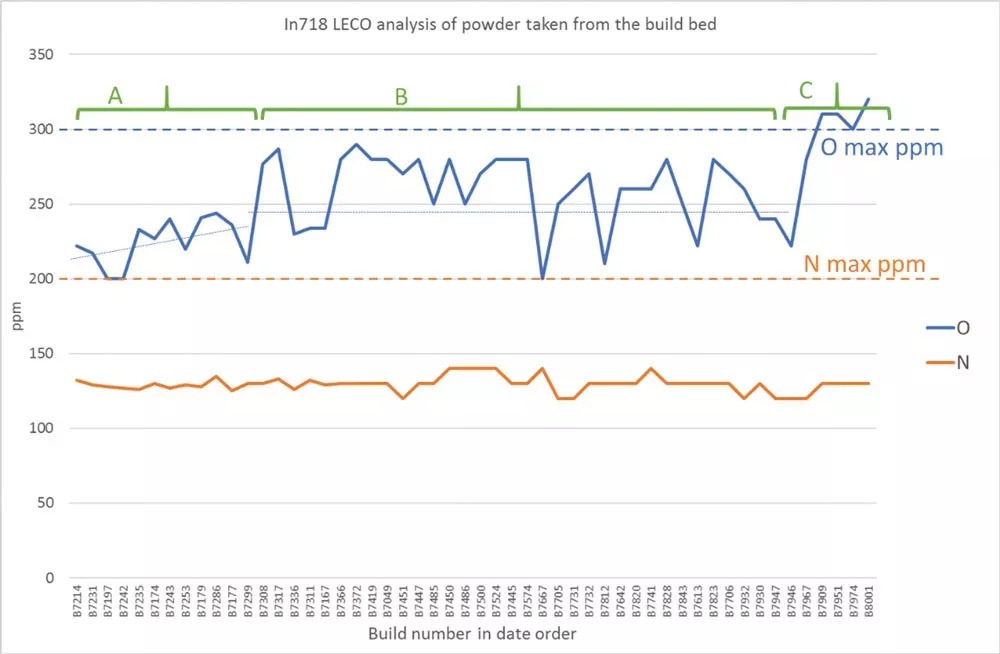
Another study by researchers from Carnegie Mellon University investigated the effects of powder reuse on SLM 3D printing of stainless steel 316L. The researchers found that the reused powder had higher oxygen content, lower carbon content, and more oxide inclusions than the fresh powder. They also observed that the reused powder had lower flowability and higher bulk density than the fresh powder. The study reported that these changes did not have a significant impact on the density, microstructure, or mechanical properties of the 3D-printed parts within 10 build cycles. However, they suggested that further research is needed to evaluate the long-term effects of powder reuse on part quality.
Best Practices and Challenges for Powder Management and Recycling
As we have seen, powder reuse can have various effects on 3D-printed metal part quality depending on the type of material, process, and number of cycles. Therefore, it is important to have a proper powder management and recycling system to ensure consistent and reliable results. Some of the best practices and challenges for powder management and recycling are:
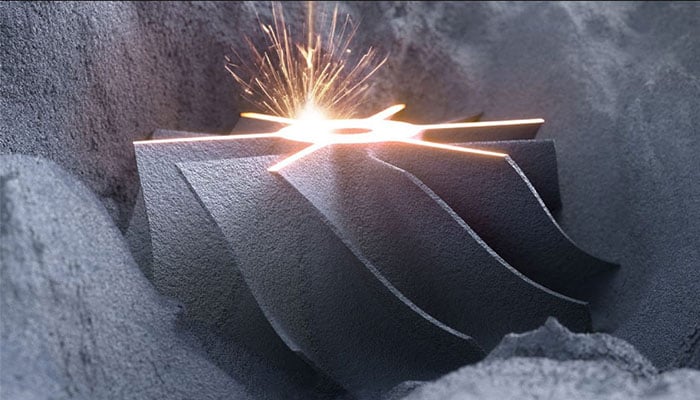
- Sieving: Sieving is a process that removes oversized or undersized particles from the powder using a mesh screen. Sieving can improve the flowability and packing density of the powder by eliminating agglomerates, satellites, or fine particles. Sieving can also reduce contamination by removing foreign materials or debris from the powder.
- Blending: Blending is a process that mixes fresh and reused powder in a certain ratio to maintain a consistent composition and quality. Blending can help to reduce variations in particle size distribution, morphology, surface chemistry, or oxygen content among different batches of powder.
- Testing: Testing is a process that measures various properties of the powder such as particle size distribution, morphology, surface chemistry, flowability, bulk density, or oxygen content. Testing can help to monitor the quality of the powder and determine its suitability for 3D printing. Testing can also help to identify any anomalies or defects in the powder that could affect part quality.
- Storing: Storing is a process that preserves the quality of the powder by keeping it in a sealed container under controlled temperature and humidity conditions. Storing can prevent moisture absorption or oxidation of the powder which could degrade its quality.
- Tracking: Tracking is a process that records various information about the history and usage of the powder such as batch number, source, material type, process parameters, number of cycles, or test results. Tracking can help to trace the origin and performance of the powder and ensure its traceability and accountability.
One of the main challenges for powder management and recycling is the lack of standardized methods and guidelines for the industry. Different 3D printing systems and service providers may have different requirements and specifications for the powder quality and reuse. Moreover, different applications and industries may have different standards and regulations for part quality and certification. Therefore, it is essential to establish clear and consistent criteria and protocols for powder management and recycling that can ensure the quality, safety, and reliability of 3D-printed metal parts.
FacFox: Your Trusted Partner for Metal 3D Printing Services
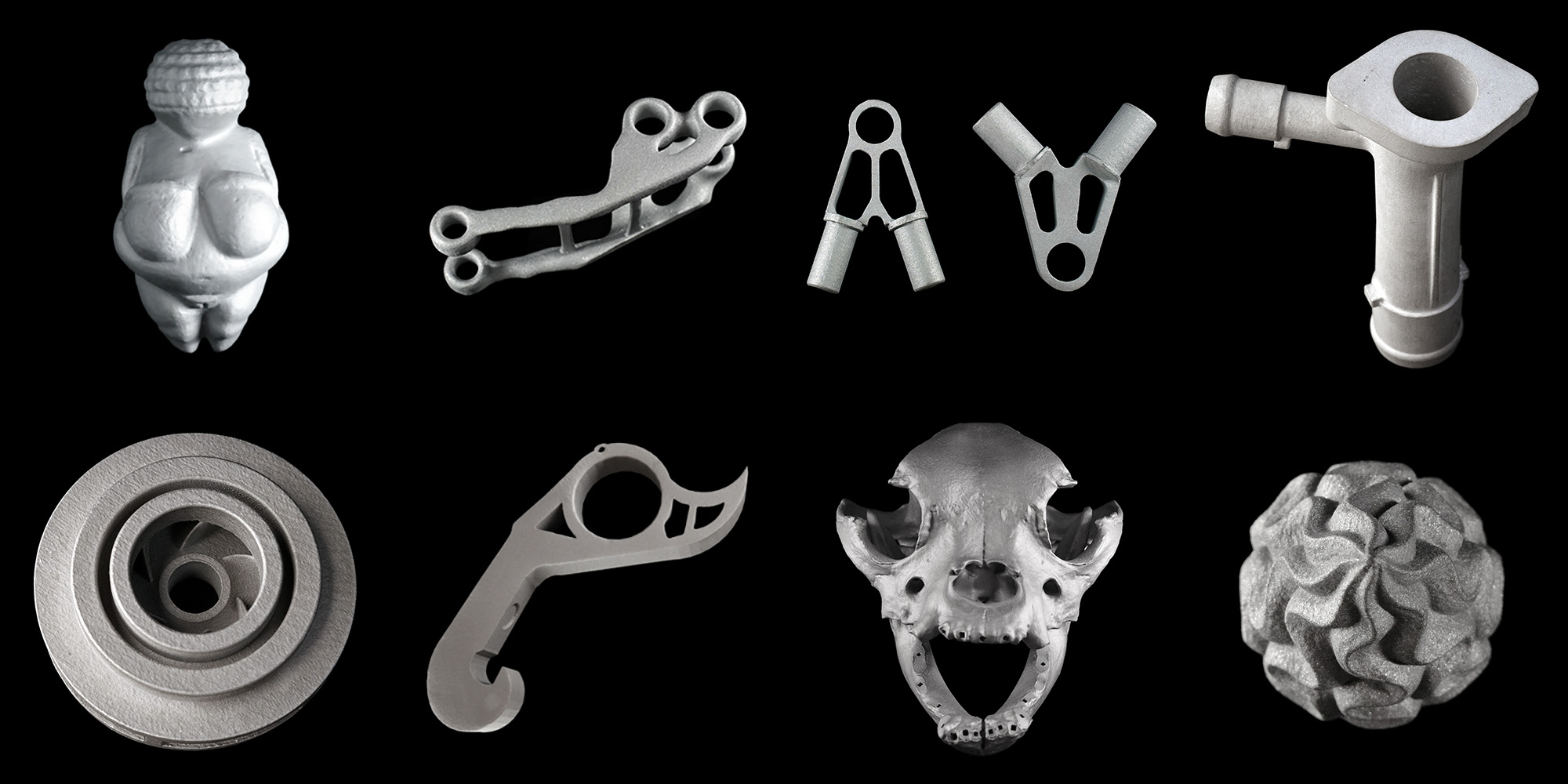
If you are looking for high-quality and cost-effective metal 3D printing services, look no further than FacFox. FacFox is a leading online platform that connects you with a network of professional 3D printing service providers across the world. FacFox offers a wide range of metal 3D printing materials and processes, such as SLM, EBM, DMLS, or Binder Jetting. FacFox also provides comprehensive powder management and recycling solutions that can optimize the quality and efficiency of your metal 3D printing projects.
At FacFox, we care about environmental protection and sustainability. We strive to reduce waste and emissions by reusing the metal powder in a responsible and effective way. We also monitor and test the quality of the powder and the parts to ensure they meet your expectations and standards. Whether you need metal 3D printing for prototyping, production, or customization, FacFox is your responsible and honest partner. Visit facfox.com today and get a quote with your 3D models!