Our metal 3D printer buyer’s guide provides the insights you need to make the best metal 3D printer decision. Plus, a look at all the specs and prices!
Metal 3D printing provides a proven menu of benefits to a growing number of industries. Not only can you create parts with shapes and internal structures that could not be cast or otherwise machined, but metal 3D printing can create parts within parts so engineers can design a complex assembly in one piece. This saves the time and labor of assembling parts or performing processes, such as welding, and increases efficiency of the final part.
Metal additive manufacturing makes it possible to quickly create functional prototypes made out of the same material as production components. The technology also makes creating specialized metal components for high-tech areas, such as aerospace, far less expensive and time-consuming. To top it off, there’s also far less waste in metal 3D printing, reducing the cost of printing in titanium and specialized alloys.
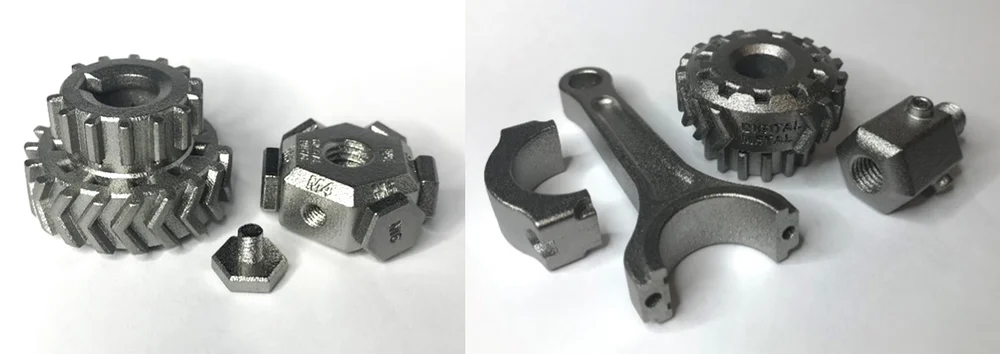
In fact, nearly every industry that uses metal parts or fixtures has benefited from the time, money, labor, and material savings offered by metal 3D printing.
In recent years, metal 3D printing has become more accessible and affordable with an increasing number of office-ready printers that bring fast ROI and production agility. Third-party 3D printing services also have matured in their offerings, eliminating the overhead of maintaining your own system. Through platforms like Craftcloud, you can upload your CAD file, select your metal material, and receive quotes from reputable metal additive manufacturers near you.
In short, there’s never been a better time to transition to 3D printed metal parts. Here we cover the most trusted names and most innovate machines in metal additive manufacturing, and explain the technology behind them. 2021 welcomed the launch of several new metal 3D printers, such as Raise3D’s MetalFuse, Wayland Additive’s Calibur3, and the FormUp 350 from AddUp. We’ll be watching to see how these perform. There are also a couple of really exciting and outlier metal technologies attracting a lot of attention, namely Spee3D’s take on cold fusion and Meltio’s laser metal deposition.
If you’re looking for your first metal 3D printer, ask yourself these questions to narrow down your options:
- What metal(s) or composites do I want to print with?
- What mechanical properties do my final prints need?
- How important is speed and volume to my business?
- Are my final metal parts for a regulated industry?
- Can existing staff operate the machine or do I need new expertise?
- Does my manufacturer or distributer offer consulting and support?
Now, let’s dive in to the best companies making the metal 3D printers today.
Metal 3D Printer | Technology | Build Volume in mm | Feedstock | Price |
---|---|---|---|---|
Markforged Metal X | fused deposition modeling (FDM) | 300 x 220 x 180 | bound powder filament | $99,500 |
Desktop Metal Studio System 2 | fused deposition modeling (FDM) | 300 x 200 x 200 | bound powder filament | $110,000 |
Rapidia Metal Designlab | fused deposition modeling (FDM) | 200 x 280 x 150 | bound powder filament | $100,000 |
Desktop Metal Shop System | binder jetting | 350 x 220 x 200 | metal powder | $150,000 |
3D Systems DMP Flex 100 | laser powder bed fusion (LPBF) | 100 x 100 x 90 | metal powder | $150,000 |
Trumpf TruPrint 1000 | laser powder bed fusion (LPBF) | 100 x 100 x 100 | metal powder | $170,000 |
Desktop Metal (ExOne) InnoventX | binder jetting | 160 x 65 x 65 | metal powder | $250,000 |
GE Additive | laser powder bed fusion (LPBF) | 800 x 400 x 500 | metal powder | $250,000 |
Renishaw RenAM 500Q | laser powder bed fusion (LPBF) | 250 x 250 x 350 | metal powder | $250,000 |
Digital Metal DM P2500 | binder jetting | 203 x 180 x 69 | metal powder | $250,000 |
Optomec CS250 | direct energy deposition (DED) | 250 x 250 x 250 | metal powder | $225,000 |
EOS M 100 | laser powder bed fusion (LPBF) | 100 x 100 x 95 | metal powder | $350,000 |
HP Metal Jet | binder jetting | 430 x 320 x 200 | metal powder | $399,000 |
SLM Solutions SLM 125 | laser powder bed fusion (LPBF) | 125 x 125 x 125 | metal powder | $400,000 |
Velo3D Sapphire | laser powder bed fusion (LPBF) | 315 x 315 x 1000 | metal powder | >$500,000 |
Farsoon FS121M | laser powder bed fusion (LPBF) | 120 × 120 × 100 | metal powder | >$500,000 |
BLT S210 | laser powder bed fusion (LPBF) | 105 x 105 x 200 | metal powder | – |
DMG Mori Lasertec 12 SLM | laser powder bed fusion (LPBF) | 125 x 125 x 200 | metal powder | >$500,000 |
KNOW YOUR METAL 3D PRINTING TECH
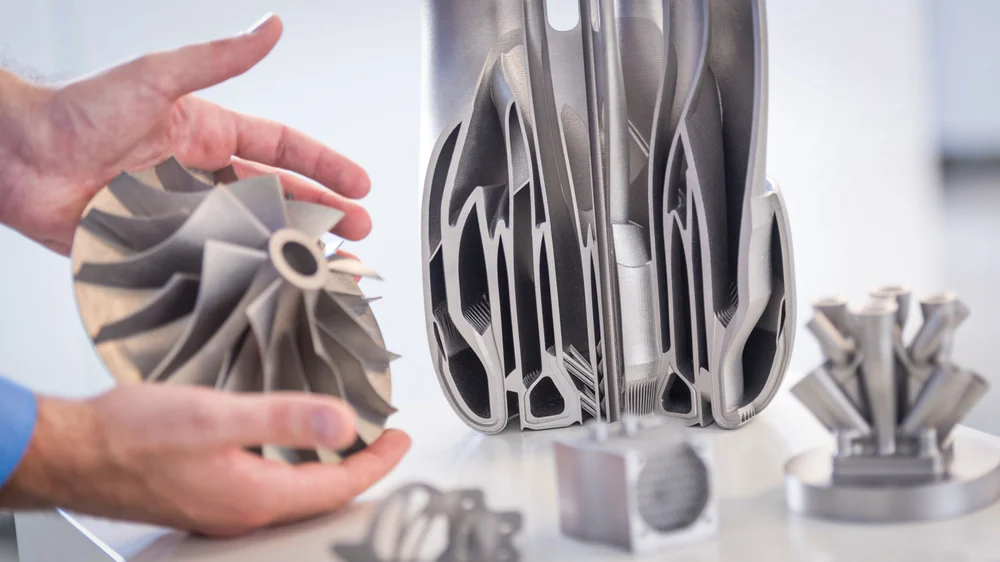
There are nearly as many different ways to 3D print metal as there are metals to print with. The different technologies produce slightly different parts and affect your overall cost, speed, and efficiency, so it’s good to get a grounding on your options. We’ll breeze over the options here, but we link to fuller coverage and explanations elsewhere at FacFox.
Laser Powder Bed Fusion (LPBF)
The most common metal 3D printing technology is laser powder bed fusion, more popularly know as selective laser melting (SLM), which makes up about 80% of the metal 3D printer market.
LPBF can be used with a wide spectrum of materials – aluminum, titanium, iron, nickel, cobalt, copper-based alloys, and their composites – and involves a laser (or several) that slowly and steadily melts layer by layer of metal powder, fusing the tiny particles inside the metal.
Parts emerge from the LPBF processes ready to use without further steps required, except for possibly having to remove the support structures. The surface finish of the sintered parts is rough, however, and, depending on your requirements, may need some post-processing.
Selective Laser Melting / SLM 3D Printing – The Ultimate Guide
Fused Deposition Modeling (FDM) with Metal Filament
FDM, which uses filament extruded through a nozzle, is the workhorse of plastic 3D printing but turns into a metal printing technology when you use plastic filament infused with metal powder or nearly full-metal filaments. The plastic part of the filament (or binder) is removed in the post-processing to reveal a part that is up to 98% metal, although they can have relatively high porosity. Metal filaments are also abrasive to FDM machine extruders, so reinforced or hardened steel extruders are a necessity.
Metal FDM is by far the least expensive way to produce metal parts because metal filament can be used on a wide range of desktop 3D printers originally designed for plastics, such as Ultimaker S5, MakerBot Method, and Raise3D. In fact, there’s been a lot of buzz about using stainless steel filament on desktop 3D printers designed mainly for plastics. So what’s the difference between this method and the dedicated metal printers we feature below?
In short, it’s all about the structural and mechanical properties your parts require. That’s not to say that metal parts from these desktop printers are just decorative. They are real metal parts suited for a broad range of applications, including tooling, jigs and fixtures, small series production, functional parts, prototypes, and even jewelry. The FDM print method, however, is less accurate than other metal 3D printing technologies and this method requires supports, which can limit part geometry. Parts from metal filament also require debinding and sintering (often at a third party), slowing down your production.
Printed parts can lose up to a third of their volume in post-processing so that has to be accounted for before printing, but fortunately your software should manage the calculations.
Metal Filament for Real Metal Parts: The Ultimate Guide
Electron Beam Powder Bed Fusion (EBM)
EBM is another powder bed fusion technology that uses an electron beam instead of lasers to fully melt and fuse the metal materials. It’s less accurate than SLM but can produce larger parts faster. The EBM process takes place in a vacuum and at high temperatures, resulting in stress-relieved components with material properties better than cast and comparable to wrought material.
3D Printing Titanium: Methods, Printers, Applications
Metal Binder Jetting
Binder jetting has really taken off in the last few years and is poised to overtake SLM as the industry standard because it’s flexible and inexpensive. A binder jet printer distributes a layer of metal powder and then uses a jetting head to deposit a binding polymer to create the geometry. Although the part is produced faster and in larger batches than any of the other powder bed processes, printing is only the first step. Just like FDM, post-processing, such as de-powdering, debinding, sintering, infiltration, annealing, and finishing the part will often take more time than printing the initial part.
Betting on Binder Jetting for Production Additive Manufacturing
Cold Spray
Cold spray is a manufacturing technology that sprays metal powders at supersonic speeds to bond them without melting them, which produces almost no thermal stress. Since the early 2000s it’s been used as a coating process, but more recently, several companies have adapted cold spray for additive manufacturing because it can layer metal in exact geometries up to several centimeters at about 50 to 100 times higher speed than typical metal 3D printers.
For additive manufacturing, cold spray is being used to quickly manufacture metal replacement parts and for on-location repairs and restoration of metal components, such as military equipment and machinery in the oil and gas industry, saving companies potentially millions in remanufacturing and interruptions in workflows. Repaired parts, in some cases, can be better than new ones.
Cold Spray Metal 3D Printing Tech & Printer
Powder & Wire Direct Energy Deposition (DED)
Directed energy deposition (DED) technologies fuse materials by melting them as they’re being deposited, similar to welding. It’s a manufacturing process that’s often used for repair and maintenance of existing metal parts, but can also quickly construct metal parts.
Several processes that fall under this category and differ in heat source and raw material. One, called wire arc additive manufacturing (WAAM) uses a metal wire and an electric arc to fabricate large metal parts that are then machined to a final shape. Other DED technologies use metal wire with a plasma, laser or electron beam energy source, while there’s also a popular technology using metal powder shot from a nozzle and melted with laser energy.
WAAM! What Is Wire Arc Additive Manufacturing?
This is not an exhaustive list of metal 3D printing methods. More specialized metal 3D printing technologies include metal lithography and micro selective laser sintering for tiny metal parts.
Micro 3D Printing – The Ultimate Guide
Let’s get into it and take a look at the printer manufacturers at the forefront of the current metal manufacturing revolution.
OFFICE-FRIENDLY METAL 3D PRINTERS
Office-friendly in the sense that you don’t need dedicated lines for compressed air or inert gases and they can roll right through the door, these machines are more akin to your typical desktop 3D printer (and in the case of metal filament printers, they actually are).
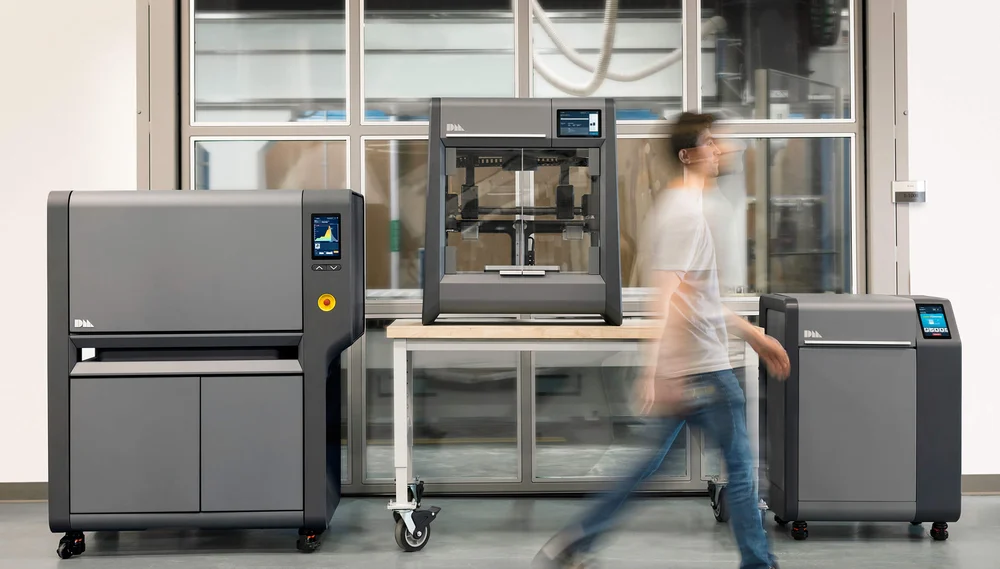
Markforged Metal X
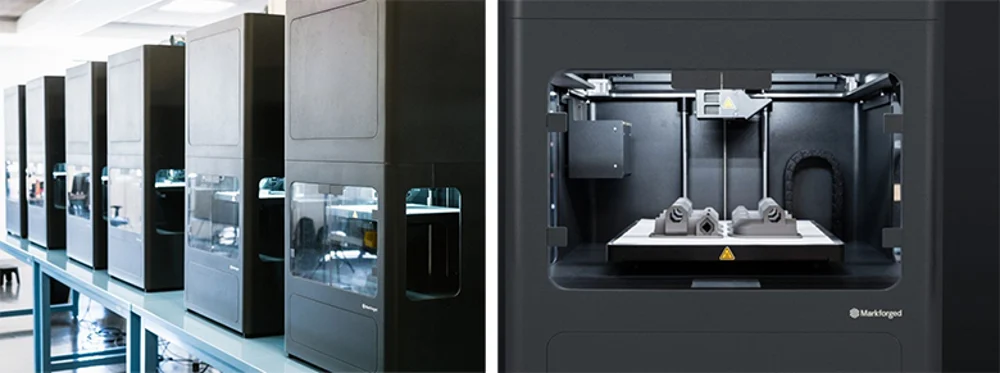
- Technology fused deposition modeling (FDM)
- Build Volume in mm 300 x 220 x 180
- Feedstock bound powder filament
- Price $99,500
Boasting a compact footprint (it’s the smallest metal 3D printing system on this list) and slicing software with printer and print management features, the Markforged Metal X aims to be an easy-to-use machine promising to take your parts from design to fully functional metal parts in as few as 28 hours.
Markforged Metal X: Review the Specs & Use Cases
The metal 3D printing process used in the Markforged Metal X, called Atomic Diffusion Additive Manufacturing (ADAM), involves the process of using a bound metal powder rod. The resulting parts are then put into a debinder and sintered in separately available workstations.
The printer itself ($99,500) and the two post-processing components comprise the complete Metal X setup, with a total price in the region of $160,000, including close support from Markforged itself with its three-year “success plan”.
The main metal feedstock is used as support material, with a fine ceramic interface layer printed between supports and part to ensure clean breakaway post-sinter. The Metal X can print parts from proprietary filaments in 17-4 PH stainless steel, copper, H13 tool steel, Inconel 625, A2 and D2 tool steel.
Desktop Metal Studio System 2
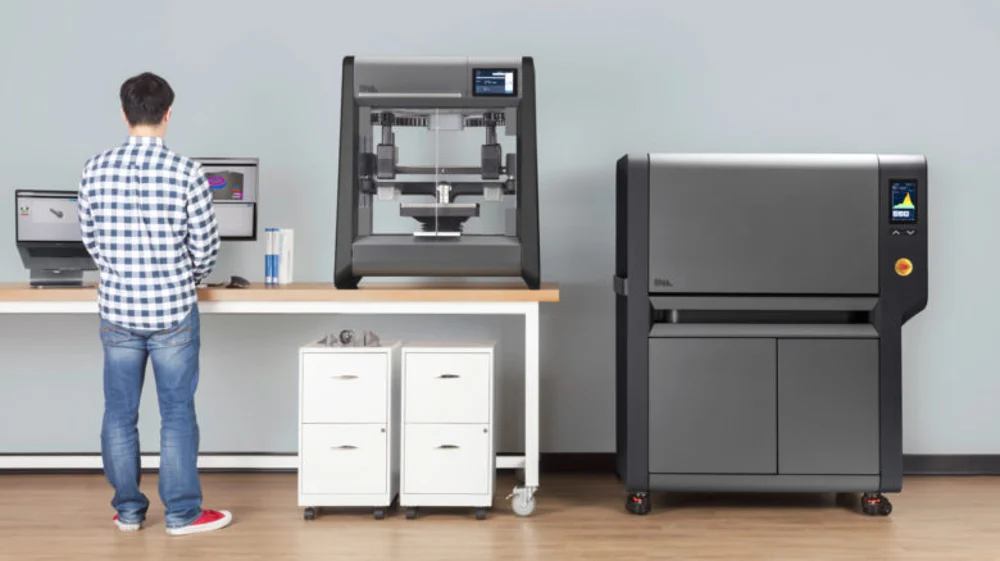
- Technology fused deposition modeling (FDM)
- Build Volume in mm 300 x 200 x 200
- Feedstock bound powder filament
- Price $110,000
Desktop Metal’s Studio System 2 metal 3D printer extrudes a metal filament (in the form of rods) to create the desired geometry (similar to the Markforged above), but it doesn’t need a debinding step to remove the plastic binder that holds the metal powder into a filament – or the associated equipment – when printing with 316L stainless steel. Prints from the Studio System are moved directly into the accompanying furnace that first heats parts to remove all binders from parts, then ramps up the temperature to near-melting for sintering.
Desktop Metal offers a separable supports technology that automatically generates seams throughout support structures, and prints a reformulated ceramic interface material between the support structure and the part, allowing parts to easily be removed by hand.
Desktop Metal Studio System: Review the Specs
Easing you into the process of printing metal parts is the company’s software called Fabricate that automates a lot of the metallurgy, such as automatically scaling your part (to account for sinter shrinkage), orienting it for ideal print and sintering success, and generating the separable supports. Upload your design and follow the onboard UI for step-by-step guidance, the company says.
The Studio System 2 is also compatible with proprietary materials, including H13 tool steel, 17-4 PH stainless steel, 4140 steel, copper, titanium Ti64, and D2 tool steel, but these require a separate debinding station. So far, only the 17-4PH stainless steel, 4140 low-alloy steel, D2 tool steel, and 316L stainless steel are printer-to-sinter compatible.
The Desktop Metal Studio System 2 sells for approximately $110,000 for the complete system, including the furnace station.
Rapidia Metal Designlab
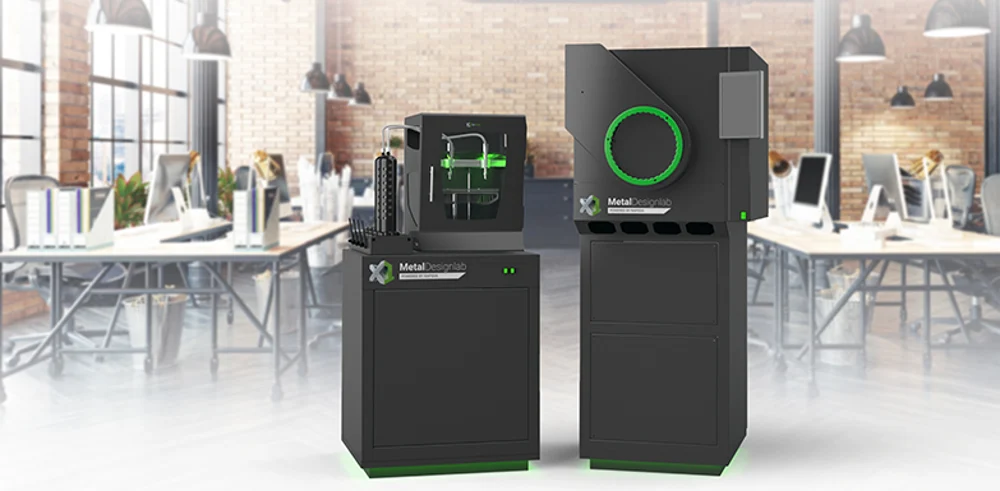
- Technology fused deposition modeling (FDM)
- Build Volume in mm 200 x 280 x 150
- Feedstock bound powder filament
- Price $100,000
Designed for an office environment and easy to operate, the Metal Designlab from Rapidia is offered with a sintering unit and intuitive software.
This office-sized, entry-level machine isn’t technically FDM because it doesn’t use filament, but it is an extrusion-based technology. It uses a water-based paste material inlaid with metal or ceramic powders. Parts do not require a debinding step before sintering. The HydroFuse paste replaces 98% of the plastic binder with water, which evaporates while printing. Rapidia eliminating the debinding requirements, accelerates final part delivery times to a simple overnight sintering.
The company’s printer is paired with the X1F furnace. Further cutting costs, the X1F sinters some common metals, such as 316L, without the need for hydrogen or forming gas. Instead uses a small amount of ultra high purity Argon, which is a fraction of the cost of other sintering gasses. Next to the metal, gas is the second largest expense in a system that requires sinter post-processing.
Current materials include 316L stainless steel, 17-4PH stainless steel, and a general purpose ceramic. In development, the company says, are Inconel 625, copper, zirconia, tungsten chrome carbide, H13 tool steel, alumina, maraging steel, and titanium.
SHOP FLOOR & PRODUCTION METAL 3D PRINTERS
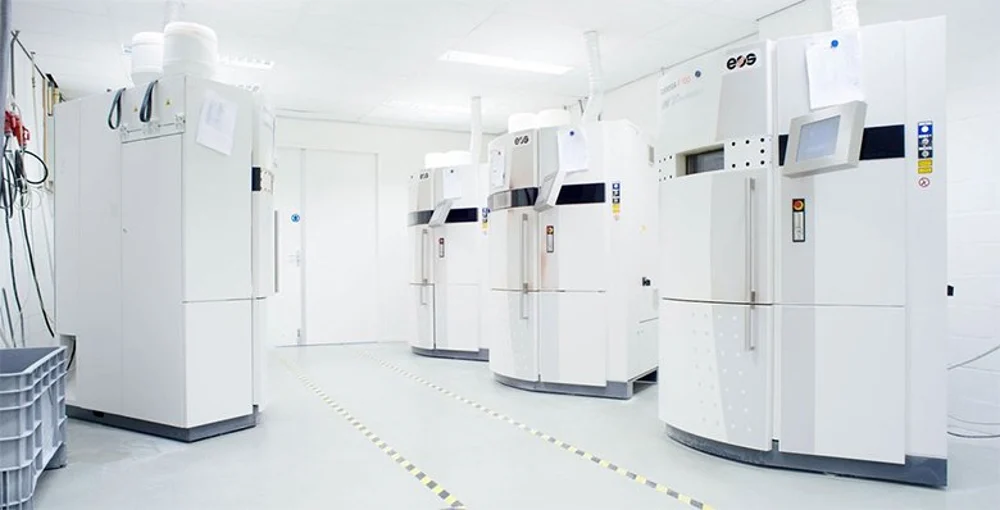
Below we feature the top names in metal 3D printers focusing on their entry-level offerings. Many of these companies also offer a range of larger, production-ready machines so it’s worth keeping your growth plans in mind when shopping for a metal printer and consider companies offering scalable systems. All of these printers are ideal for custom parts, low-volume runs, and experimentation.
Desktop Metal Shop System
- Technology binder jetting
- Build Volume in mm 350 x 220 x 200
- Feedstock metal powder
- Price $150,000
Where Desktop Metal’s Studio System 2 provides an efficient route to metal one-offs, prototypes, and custom tooling, the Desktop Metal Shop System scales things up, swapping bound metal deposition for binder jetting technology to enable faster throughput of parts – all in a modestly-sized workshop-suitable form.
Designed with machine shops in mind, the Desktop Metal Shop System is available in a variety of build volume configurations (up to 12-liter capacity) and offers the capability to group different batches of parts into single print cycles – tooling-free – rattling off the full volume of parts within a typical shift.
The Shop System uses Desktop Metal’s own spin on binder jetting, with more than 70,000 nozzles depositing droplets of binder in a single pass onto the company’s proprietary metal powders. The company claims surface finishes as fine as 4 Ra microns are possible post-furnace.
In a nutshell, the Production System uses a form of binder jetting the manufacturer has titles Single Pass Jetting (SPJ). This technology increases the time the printer spends actively printing, in comparison to other binder jetting systems.
A fixed build volume of 490 x 380 x 260 mm in the larger P-50 model provides ample space for high density production runs. Desktop Metal also offers the P-1 model, designed to bridge the gap between benchtop development and mass production. It has a smaller build chamber at 200 x 100 x 40 mm but uses the same SPJ tech to produce equally high-quality results as its bigger sibling. P-1 also supports direct process transfer to the P-50 for production scale-up.
Desktop Metal also offers the larger Production System scaling production capability even more. The Production System’s open platform accepts low-cost non-uniform powders, such as those used for metal injection molding. That means manufacturers can continue to use their preferred MIM powders, or source locally. The Production System’s print parameters are adjusted to match.
Flexibility and agility come on the back of features, such as inert processing to ensure powder uniformity and a cold printing process that allows for immediate transferal from printer to debinding.
Desktop Metal qualifies 420 stainless steel and nickel-chromium superalloy, nickel alloy IN625, for its Production System in Oct. 2021 and added DM HH stainless steel, a custom stainless steel alloy in 2022.
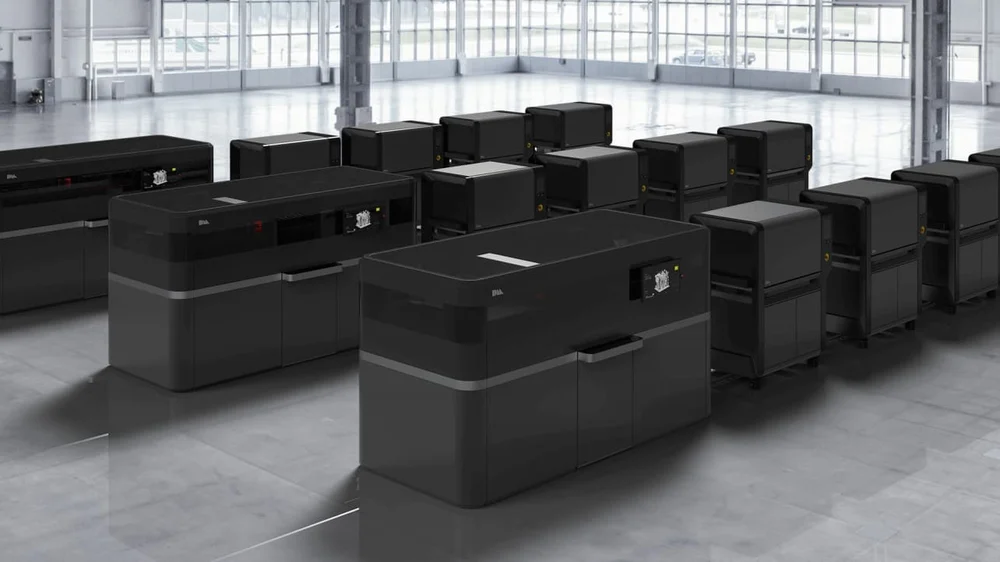
3D Systems DMP Flex 100
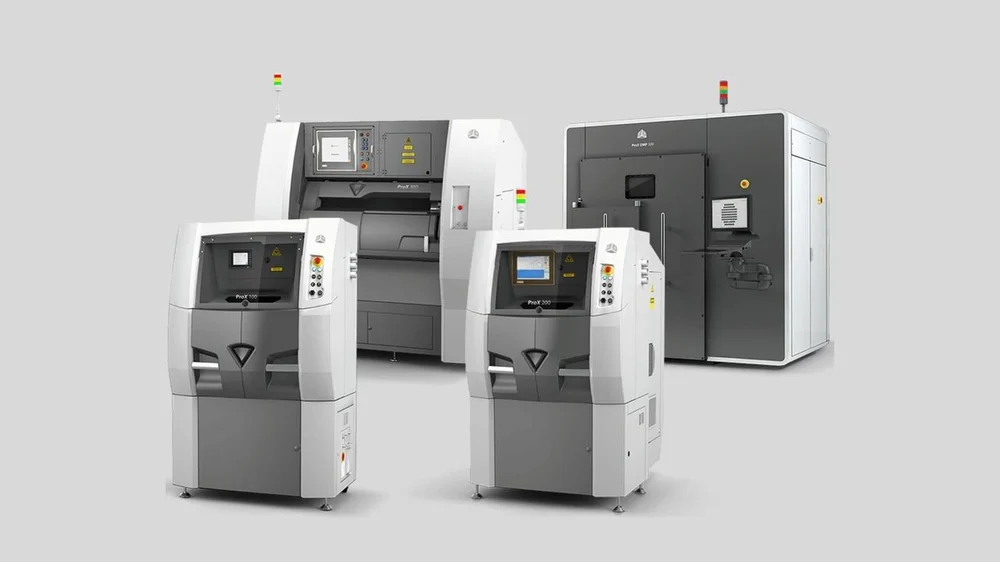
- Technology laser powder bed fusion (LPBF)
- Build Volume in mm 100 x 100 x 90
- Feedstock metal powder
- Price $150,000
3D System’s entry-level DMP Flex 100 metal 3D printer offers a build volume of 100 x 100 x 90 mm and the ability to print parts with overhangs down to 20 degrees without supports. Surface features as fine as 5 microns should mean a minimal need for post-processing. 3D Systems calls its technology Direct Metal Printing, where each layer is melted on to the previous one creating a strong and dense part (up to 99.9%).
The system’s 100-watt fiber laser, while lower power than those of the larger metal 3D printing solutions in 3D System’s line up, is powerful enough to handle a broad selection of the company’s metal powder library, including a variety of titanium grades.
Tailored to niche uses that demand fine detail, the DMP Flex 100 makes use of dedicated gas lines to achieve the vacuum necessary to print 3D System’s additive manufacturing-optimized powders. As such, it requires the necessary building infrastructure to facilitate this.
If you’re ready to move up from entry-level machines, 3D Systems offers five other, larger production units plus a networked factory solution.
Trumpf TruPrint 1000
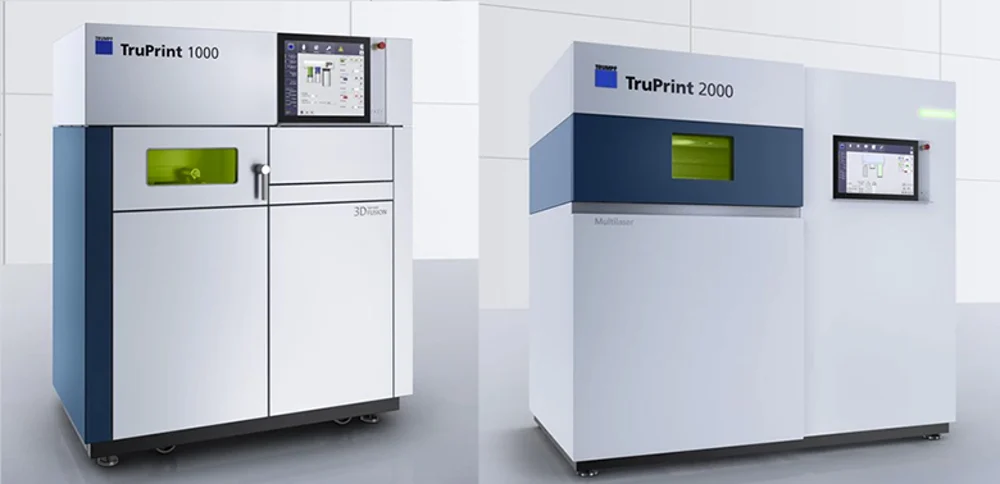
- Technology laser powder bed fusion (LPBF)
- Build Volume in mm 100 x 100 x 100
- Feedstock metal powder
- Price $170,000
Trumpf, based in Ditzingen, Germany, offers the TruPrint 1000 metal 3D printer for the production of small industrial parts. The compact machine with quick installation brings to the table high productivity and great detail, with a minimum layer thickness of 10 microns. Trumpf calls its laser powder bed fusion technology Laser Metal Fusion.
The printer’s two 200-watt fiber lasers scan the build area simultaneously, which the firm claims can increase productivity by up to 80% when compared to similar machines. A powder bed monitoring system analyzes each layer for maximum part quality. A tilting recoated makes the powder application process faster, which further increases production speed and cuts part costs.
As a unique note, TruPrint 1000 can process amorphous metals. These materials make it possible to produce parts with high elasticity and corrosion-resistance, while simultaneously cutting down on wall thicknesses. This reduces production times and final part weight.
Trumpf has seven other metal 3D printers in its portfolio of varying sizes and capacities. The TruPrint 1000 Green Edition features a green laser that enables it to 3D print highly reflective materials, such as copper and its alloys. Other machines in the company’s catalog scale power and production capacity up to higher-volume applications.
Desktop Metal (ExOne) InnoventX
- Technology binder jetting
- Build Volume in mm 160 x 65 x 65
- Feedstock metal powder
- Price $250,000
If you’ve heard about the excellent ExOne binder jetting metal printers, don’t worry they’re not gone. ExOne was acquired in 2021 by Desktop Metal, which has rebranded the printers as the X-Series.
The entire family of metal 3D printers is designed as a scalable system that can can take you from prototyping to serial production on the same printhead engine.
An introductory binder jetting 3D printer suited to R&D environments, the InnoventX is the company’s most compact metal printer. It’s compatible with a variety of metal powder feedstock to form one-offs and small batches of parts. More for research, verification, and experimentation than production, this flexible system uses ultrasonic dispensing technology to prepare uniform layers of powder for binding. This technology allows InnoventX to use rougher low-cost metal powders with good quality results.
Desktop Metal’s other and larger metal additive manufacturing machines, the X25Pro, has a 400 x 250 x 250 mm build volume and a build rate of more than 1,200 cc/hour for metal part production.
The X160Pro is the world’s largest binder jet 3D printer (800 x 500 x 400 mm build volume) for the production of metal, ceramic, or composite parts. This system is designed for continuous 24/7 production, yet supports short-run production, rapid product development, and even research and prototyping.
GE Additive
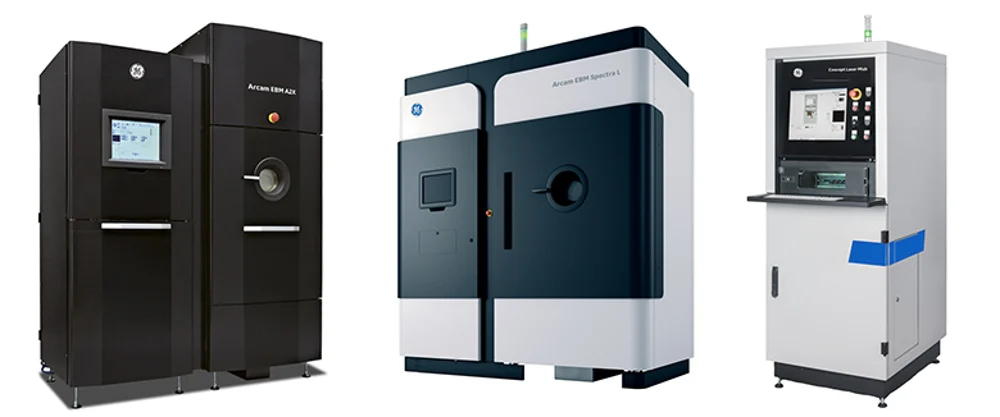
- Technology laser powder bed fusion (LPBF)
- Build Volume in mm 800 x 400 x 500
- Feedstock metal powder
- Price $250,000
Industrial powerhouse GE currently offers 11 metal 3D printers – five Arcam EBM machines and six Concept Laser SLM machines – and is developing a binder jetting option that should launch in 2022.
The Arcam line boasts dimensionally accurate parts quickly and efficiently with a high-power electron beam for high melting capacity and productivity. The Concept Laser machines use lasers to melt layers of fine metal powder and create complex geometries Several different machine envelope sizes — including the largest powder-bed metal additive system in the world, the X Line 2000R.
The X Line 2000R features an 800 x 400 x 500 mm build volume and brings two 1,000-watt lasers to bear in order to keep production times down. With an eye on the production of large metal parts for the automotive and aerospace industries, the X Line 2000R turns prints jobs around at a clip thanks to two rotating, reciprocal build modules.
This metal printer uses Concept Laser’s laser powder bed fusion technology it calls LaserCusing, can 3D print objects from alloys of steel, aluminum, nickel, titanium, and precious metals, with the operator’s need to handle reactive powders minimized by closed recycling loop. Excess powder is siphoned off for inertized sieving and reprocessing stations before feeding back to the machine.
Renishaw RenAM 500Q
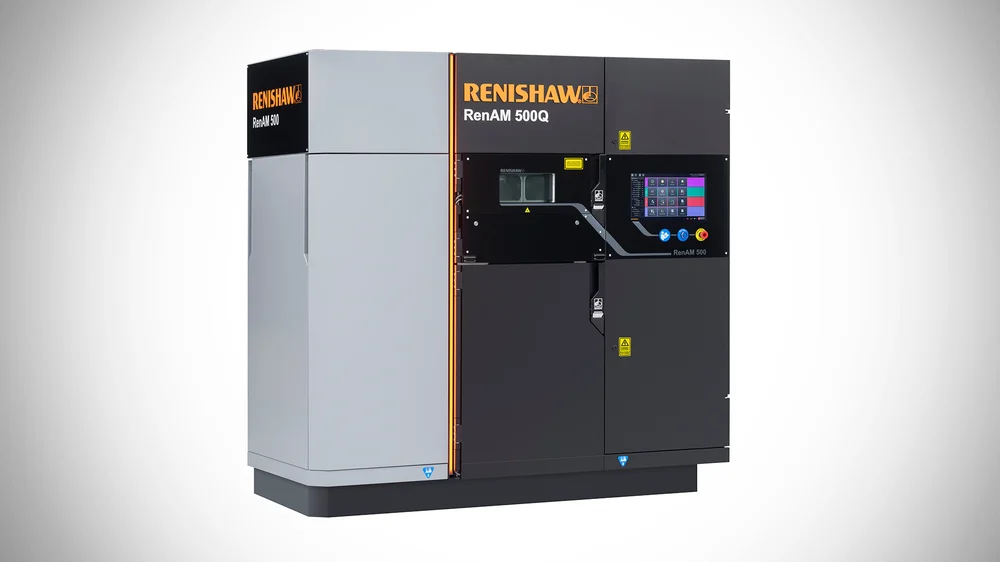
- Technology laser powder bed fusion (LPBF)
- Build Volume in mm 250 x 250 x 350
- Feedstock metal powder
- Price $250,000
Placing emphasis on productivity, Renishaw’s RenAM 500Q system builds on the company’s established range of metal printers and amps throughput with an array of four 500-watt lasers, each capable of hitting the entirety of the build volume. This enables the RenAM 500Q to accomplish full-layer sinters quicker than single-laser systems, increasing output and, consequently, reducing cost per part.
A number of inbuilt automation systems – such as sieving and powder recirculation – for material and atmosphere management complement the printer, ensuring operator safety and reducing the time required to operate and maintain the machine. An intelligent gas flow system reduces both argon consumption and emissions.
The RenAM 500Q features a typical build volume of 245 x 245 x 335 mm (substrate dependent) and can output some 150 cm3 per hour, depending on the geometries being printed and other material variables.
Digital Metal DM P2500
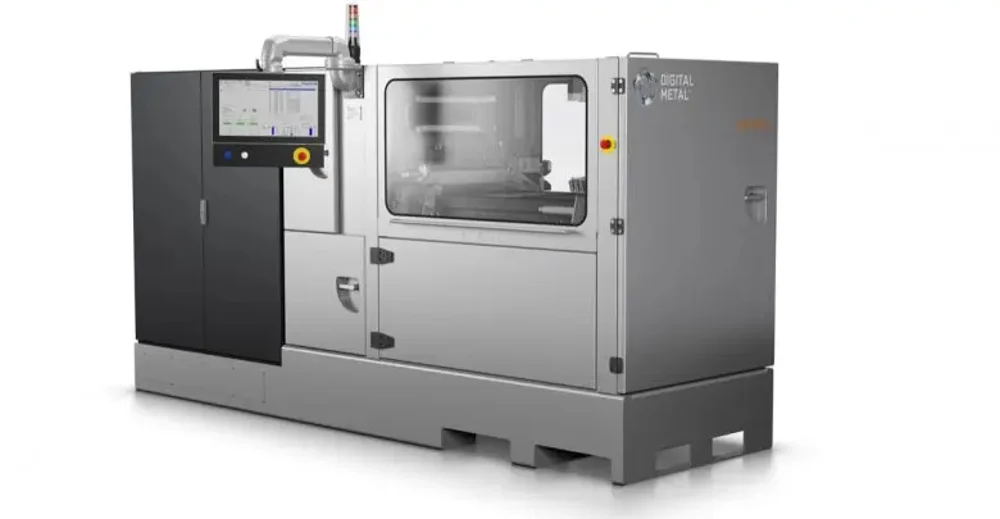
- Technology binder jetting
- Build Volume in mm 203 x 180 x 69
- Feedstock metal powder
- Price $250,000
The Swedish manufacturer Digital Metal is a pioneer in high-precision metal binder jetting systems for industrial use. Its parent company, Höganäs, is the world’s largest producer of powdered metals giving the company a leg up in R&D when it comes to metal part production.
The Digital Metal DM P2500 is a robust machine for both serial production and prototyping with a focus on fine tolerances, surface finish, and resolution for small complex components. Small part sizes means there is plenty of room for large numbers of components to be printed simultaneously. Like other powder bed fusion printers, the DM P2500 does not require any support structures or involve any heat transfer, which means you can pack the build box densely.
With Digital Metal technology, your part can have a surface quality of 6 microns without any post-processing, while other AM processes typically leave a much rougher surface. Surface quality is important for components with internal channels, as post-processing of those surfaces is very challenging.
The company added DM 4140 low-alloy steel and DM 718 alloy steel to its menu of materials late last year bringing the number of metals for this machine to 9.
There’s also a rather unique automated depowdering machine.
Optomec CS250
- Technology direct energy deposition (DED)
- Build Volume in mm 250 x 250 x 250
- Feedstock metal powder
- Price $225,000
Optomec is one of the most rapidly growing metal 3D printer makers offering the LENS line of directed energy deposition 3D Printers for metal component production and repair.
LENS stands for laser engineered net shaping, and it is Optomec’s take on DED using lasers and jetted powdered metals, alloys, ceramics, or composites. The atmosphere-controlled, multi-axis systems feature optional hybrid CNC capabilities.
The smallest of Optomec’s five DED machines is the CS250 featuring a 500 to 2000 W fiber laser, and a novel front powder loading system compatible with all common alloys, including steels, titanium, and aluminum.
Although the CS250 is aimed at universities and research, the LENS 860 Machine Tool Systems offers a larger build volume and higher power capabilities for additive and hybrid manufacturing metal processing. The LENS 860 system is ideal for building, repairing, or coating mid- to large-size parts.
EOS M 100
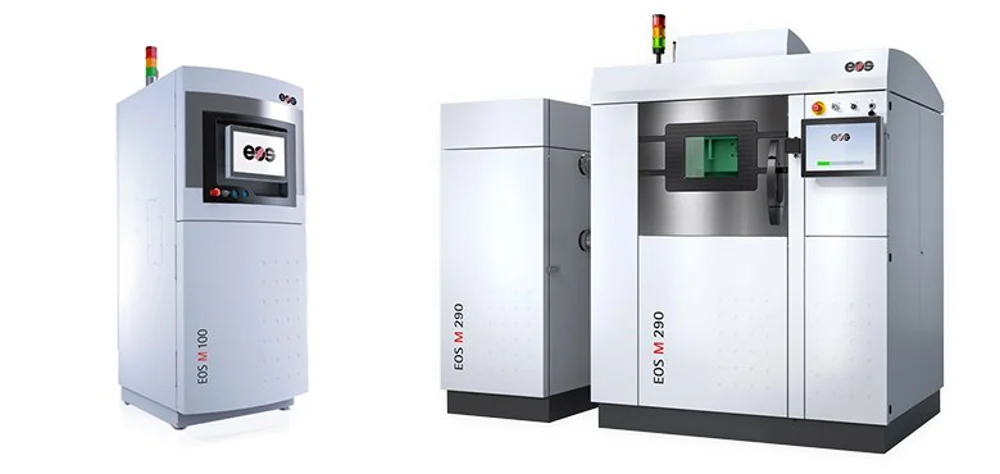
- Technology laser powder bed fusion (LPBF)
- Build Volume in mm 100 x 100 x 95
- Feedstock metal powder
- Price $350,000
The M 100 metal 3D printer is EOS’s entry-level system for metal printing. Featuring direct metal laser sintering (DMLS) technology, this machine is equipped with a 200-watt fiber laser to melt and fuse fine metal powders. The small laser spot enables fine resolution, making it ideal for geometrically complex metal parts.
The M 100 is optimized to reduce post-processing and cleaning time, which in turn allows for parts to be produced quickly and more effectively, EOS says. It also has a modular inner design and powder supply bin, which should make operation and maintenance easy. EOS is pushing the machine especially toward the medical field, to which the M 100 is particularly suited with EOS’s certified medical-safe metal materials. The company highlights the printer’s suitability for producing dental bridges and crowns.
The manufacturer is constantly releasing new metal powders, with the latest nickel-chromium NickelAlloy IN939 material launched in February 2021. Do note that the M 100 is compatible with a limited number of EOS materials, and may not be able to process some of the more high-end powders.
If you’re in the market for a metal 3D printer for production capacity, EOS has you covered. The German manufacturer offers industrial 3D printing systems that can be flexibly integrated into existing production environments with a range of different build space sizes, laser power ratings, and scalability.
HP Metal Jet
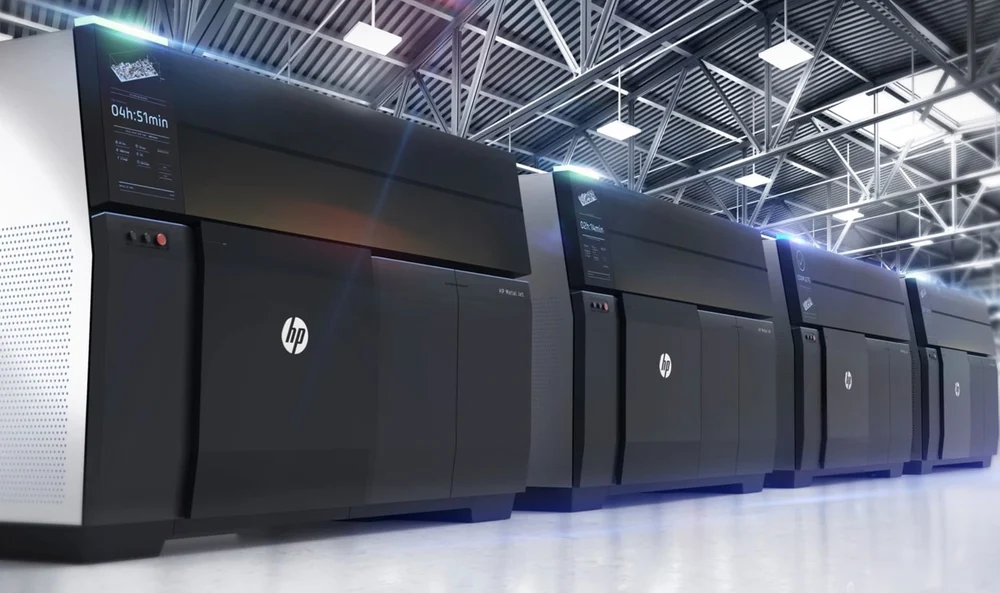
- Technology binder jetting
- Build Volume in mm 430 x 320 x 200
- Feedstock metal powder
- Price $399,000
HP’s Metal Jet metal 3D printing solution builds upon the company’s success with multi-jet fusion (MJF), a proprietary offshoot of binder jetting.
HP Metal Jet builds on the workflows and technologies that HP developed for printing 3D plastics with the goal of being a quick and economic option for metal part production while delivering quality and productivity. Using a thermal inkjet to precisely deliver HP binding agent to a powder metal bed of industry-standard materials, the Metal Jet yields green state parts that are up to 99% metal by volume. This also cuts down on the time-to-part by drastically reducing the need for debinding. HP Metal Jet parts, once printed, need only decaking and can be directly sintered in the furnace, before further finishing steps.
While the technology was originally only available via the services of GKN and Parmatech, select customers are now said to be also be using the technology in-house. HP plans to sell the Metal Jet system from approximately $399,000.
SLM Solutions SLM 125
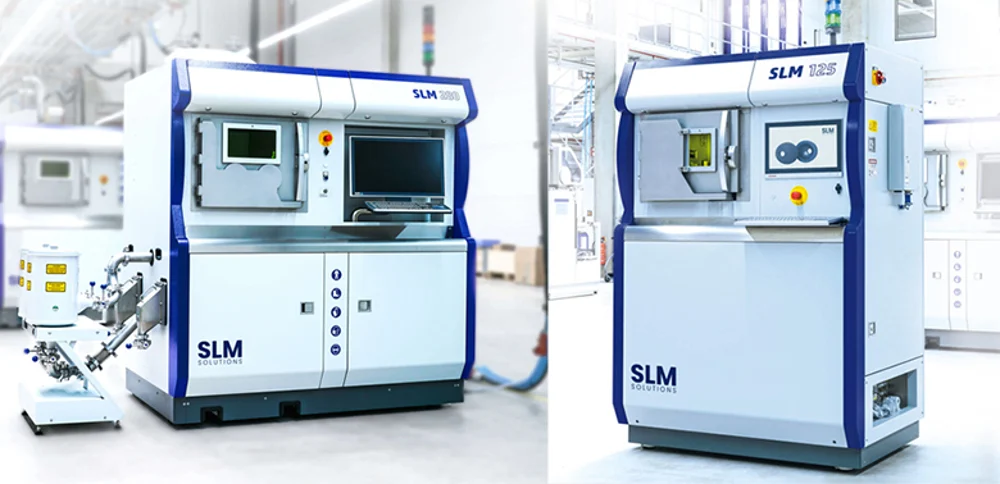
- Technology laser powder bed fusion (LPBF)
- Build Volume in mm 125 x 125 x 125
- Feedstock metal powder
- Price $400,000
Germany-based SLM Solutions’ smallest metal printer, the SLM 125, is the little engine that could. Its 400-watt fiber laser has more power than the lasers of other similarly sized machines, the manufacturer claims, which cuts powder consumption by up to 80%. SLM markets the printer toward research work and low-volume manufacturing.
The printer can process both reactive and non-reactive metal powders, and its reduced number of powder-transporting components makes swapping materials quick and easy. Laser power monitoring and layer control systems constantly check both laser output and layer consistency for high accuracy, eliminating irregularities. The 125 x 125 x 125 mm print envelope is sufficient for one-off parts and prototypes, especially with the wide variety of materials including stainless steel, aluminum, and titanium. Research institutes and parts producers looking for power in a small package shouldn’t dismiss the SLM 125.
A nice feature in SLM Solutions’ technology is the ability to directly scale the production process with the company’s expansive catalog of other printers. The firm has a machine for pretty much every production level, with the latest model addition being the generously sized industry-level NXG XII 600 launched in late 2020. Its 12 1,000-watt lasers and a 600 x 600 x 600 mm build volume provide not only size but speed – the company claims this is the fastest SLM 3D metal printer on the market.
Velo3D Sapphire
- Technology laser powder bed fusion (LPBF)
- Build Volume in mm 315 x 315 x 1000
- Feedstock metal powder
- Price >$500,000
The Velo3D Sapphire “next-gen” metal 3D printer sets itself apart as a volume production system with the advantage of support-free 3D printing and a one-meter tall build volume. Using dual 1-kilowatt lasers in its 315 x 312 x 1,000 mm print space, the Sapphire can print in aluminum F357, Inconel IN718, Ti 6Al-4V Grade 5, and Hastelloy (a nickel-chromium-iron-molybdenum alloy) C22 and X, plus recently added the nickel-based superalloy powder Amperprint 0233 Haynes 282.
For Velo3D, support-free geometries mean the Sapphire can achieve prints with overhangs of zero degrees – flat surfaces on the horizontal plane, basically. In addition to saving time on post-processing prints, the printer able to realize internal channels and volumes without consideration for support structures.
Velo3D also offers the new Sapphire XC printer, the name standing for “Extra Capacity.” True to its name, the Sapphire XC can increase production by five times compared to its sibling and reduce cost-per-part by 75%, the company claims. This XC has with a build volume of ø600 x 550 mm and eight lasers.
Farsoon FS121M
- Technology laser powder bed fusion (LPBF)
- Build Volume in mm 120 × 120 × 100
- Feedstock metal powder
- Price >$500,000
Farsoon, the large Chinese 3D printer manufacturer, aims to cover all the bases of metal printing with a wide range of printer sizes. Its smallest is the FS121M. This flexible and open system enables you to select between multiple laser spot sizes, different recoating blades, and powder choice.
The FS121M features a 200W Yb-fiber laser, inert gas supply, and over-sized protective filter systems to create a safe environment for the product and your staff.
Materials include 316L, 17-4PH, Maraging steel, HX, Cu, CuSn10, CoCrMoW, and CoCrMo.
Farsoon’s larger FS273M laser powder bed fusion 3D printer (275 × 275 × 355 mm) has dual fiber lasers (2 × 500W) or a single 500W fiber laser. Its recoater design enables faster speed and more stable powder delivery throughout the whole manufacturing process, a preheated base-plate, removable overflow containers, and a back-up powder supply sufficient for a full build.
The FS721M is an open platform system, which means that all machine parameters are unlocked for the user as well as an open material policy. Currently the machine is compatible with stainless steel 316L, TA15, Ti6Al4V, AlSi10Mg, copper, maraging steel, and others.
Not quite ready for prime-time the FS273M is open for early adopter program application.
BLT S210
- Technology laser powder bed fusion (LPBF)
- Build Volume in mm 105 x 105 x 200
- Feedstock metal powder
- Price –
BLT (Bright Laser Technologies) is the metal 3D printer giant from China offering 12 metal 3D printers employing laser powder bed fusion technology, a massive metal print service, metal powders, and engineering expertise as a service. Supporting a long list of global manufacturers with hubs in China, BLT machines are widely used in automotive, aerospace, medical, and tooling applications.
The company’s smallest LPBF machine, the S210, features a 105 x 105 x 200 mm build volume, a 500-W laser, real-time monitoring, and a modular design. It runs on Materialise Magics software and BLT’s own BLT-BP and BLT-MCS. For materials, the S210 can handle titanium alloys, aluminum alloys, superalloy, cobalt-chromium alloy, stainless steels, tool steels, copper, tungsten, tantalum, and magnesium alloy.
Moving up in size and complexity and rest of BLT’s printers offer larger build volumes, higher wattage multiple lasers, bi-directional recoaters, and more production-ready features helping you track and monitor batch volume metal prints.
Considered the company’s flagship machine, the S310 features single or dual 500-W lasers and a 250 x 250 x 400 mm build volume.
DMG Mori Lasertec 12 SLM
- Technology laser powder bed fusion (LPBF)
- Build Volume in mm 125 x 125 x 200
- Feedstock metal powder
- Price >$500,000
DMG Mori started off in Germany as a tool-making company in 1948 and has grown with the times now offering a wide range of machines for turning, milling, grinding, and some acclaimed metal 3D printers. The company’s hybrid laser DED machines feature fast DED metal production with the fine-tuning of CNCing all in the same machine.
The Lasertec 12 SLM is a laser powder bed fusion 3D printer with a 200 W or options 400 W laser featuring a 125 x 125 x 200 mm build volume.
Layer thickness can get down to just 20 microns and DMG Mori boasts an open platform enabling you to adjust parameters to your heart’s content and pair the machine with nearly any metal powder.
The machine’s automated rePlug powder handling tech integrates powder recycling for maximum efficiency and highest work-safety due to the closed material cycle.
The company’s larger, Lasertec 30 Dual SLM features two 600-W lasers.
METAL 3D PRINTING SERVICES
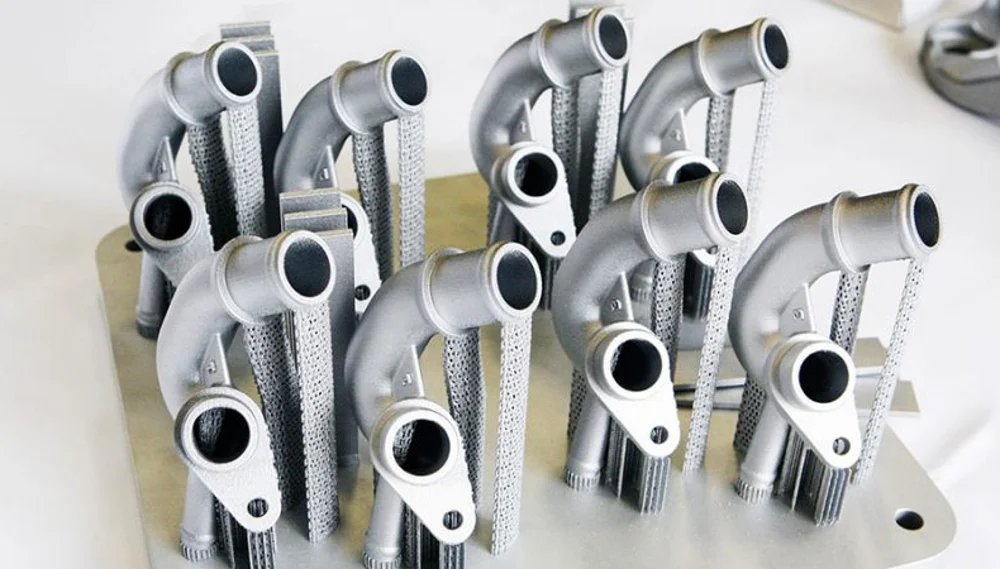
Investing in a metal 3D printer is no small decision, and part of any good due diligence is ordering sample parts. You can order these from the manufacturer, but many printer manufacturers on this list also offer print-on-demand services. For smaller projects, one-offs, and tests, outsourcing your 3D prints to a metal 3D printing service can dramatically save on the capital cost and overhead of operating your own system.
Third-part print services, such as Shapeways, i.Materialise, Sculpteo, and 3D Hubs, also offer metal printing. But choosing the right printing service for your needs can be a challenge. The best first step is to visit Craftcloud, the 3D printing service marketplace where you can instantly compare metal 3D printing prices for multiple parts in the same basket. The Craftcloud platform mixes and matches offers to give you the lowest cost and quickest turnaround time.
The Best Metal 3D Printing Services of 2022
Source: https://all3dp.com/1/3d-metal-3d-printer-metal-3d-printing/