When industrial designers are designing schemes and consider adopting various surface treatment processes after 3D printing to achieve metal effects, they often encounter various terms: electroplating, vacuum plating, vacuum ion plating, PVD, evaporated plating, sputter coating, NCVM, VM…
Especially young designers who are new to the field of coating are easily confused by these terms. There are too many types of surface treatment processes, especially now that technology is developing rapidly, more and more excellent processes are being introduced. Facfox will explain all of them to you.
Why should we get parts plated?
- Optimize the part’s performance, such as resistance to metal oxidation, improve wear resistance, electrical conductivity, light reflectivity, and corrosion resistance (copper sulfate, etc.).
- Provide decorative appearances, such as simulating metal surface, adding color and gloss.
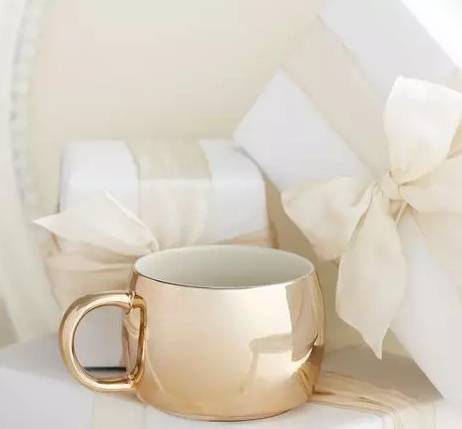
The categories of plating techniques
The plating technique is divided into chemical plating and generalized electroplating. In the coating process, the former doesn’t need to be energized while the latter one does.
What is electroless plating?
Electroless plating is a method that does not require electricity, and uses a strong reducing agent to reduce metal ions to the metal in a solution, and deposits them on the surface of parts to form a dense plating layer.
Common solutions for electroless plating: electroless silver plating, nickel plating, copper plating, cobalt plating, nickel-plated phosphorous solution, nickel-plated phosphorous boron solution, etc.
What is generalized electroplating?
What we hear most often is electroplating. In general concept, electroplating is a process that uses electrolysis to attach a metal layer to the surface of a metallic or non-metallic part.
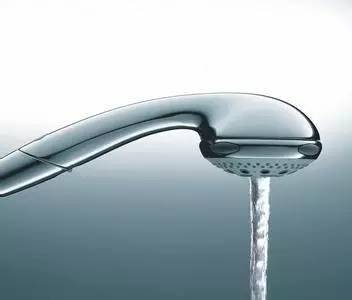
Two types of generalized electroplating
Generalized electroplating can be divided into two species: electroplating, as we usually called; and Physical Vapor Deposition(PVD).
Electroplating
Electroplating mixes the reagent into an aqueous solution and uses a direct current cathode and anode in the plating tank. There are coatings both on the inside and outside of the product.
Why we also call it electroplating one kind of chemical plating? Electroplating changes the metal ions in the solution into metal atoms. The original metal cation will be bound to a certain anion to form a new compound, which generates a new substance.
- Advantages: The principle is not simply covering something on the surface, but combining the coating material and the substrate to form an alloy, which greatly improves the bonding strength; Fast lead time (eg. only 30 seconds for silver plating); Do not require too expensive equipment.
- Disadvantages: Serious heavy metal pollution; Some products need to be chrome-plated, which needs expensive sewage treatment.
PVD = Vacuum Plating
PVD(Physical Vapor Deposition) is characterized by a process in which the material goes from a condensed phase to a vapor phase and then back to a thin film condensed phase. It is a process in which a solid material, often a metal, is vaporized in a vacuum and deposited, atom-by-atom, onto the surface of a part.
- Advantages:Compared to powder coating, PVD coatings are more than 50 times thinner, last longer, and improve UV resistance vs. an organic polymer.Compared to electroplating, PVD coatings have improved scratch and wear resistance, more color options, a cleaner, safer process, and offer the option of use after electroplating for wear-resistance and aesthetics.
- Disadvantages: The process requires complex machines and skilled operators, which means a higher cost. Besides, it has a relatively slow operating speed.
PVD
PVD can be applied to many materials, including plastic, stainless steel, copper, iron, silver, ceramics, glass, aluminum, titanium alloy, zinc alloy, powder metallurgy, liquid metal, etc., but it’s mostly used on metal.
PVD for metallic materials:
PVD technology is mainly divided into three categories: vacuum evaporation coating, vacuum sputtering coating, and vacuum ion coating.
Relative to the three categories of PVD technology, the corresponding vacuum coating equipment also includes the vacuum evaporation coating machine, vacuum sputtering coating machine and vacuum ion coating machine.
In the past ten years, the vacuum ion plating technology has the fastest development, and it has become one of the most advanced surface treatment methods in the contemporary. Most of the PVD coatings we usually refer to are vacuum ion coatings.
PVD for non-metallic materials:
Non-metallic plated materials are mostly used on plastic parts, among which are VM and NCVM.
VM: Abbreviation for Vacuum Metallization, which is the general vacuum coating. The target is aluminum and thus conductive.
NCVM: Abbreviation for Non-conductive Vacuum Metallization, also known as discontinuous plating, non-conductive plating.
The biggest difference between VM and NCVM is that the former is conductive or non-conductive, so almost all 3C products use the NCVM coating method.