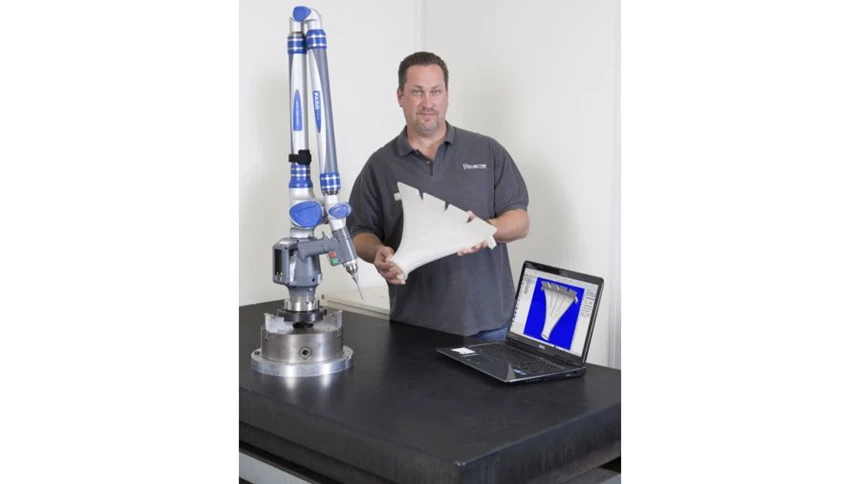
Roc-Aire stands out as a “can do” contract manufacturer for aerospace parts known for solving problems and overcoming obstacles. “We strategize with our customers on engineering, materials and processes to make sure the parts we are producing are as good as, if not better than the originals,” says General Manager Jason Collins. This strategy includes using reverse engineering and 3D printing to improve the company’s engineering and build processes and to reduce development time, whether for new parts or maintenance, repair and overhaul (MRO) applications.
Roc-Aire routinely reverse engineers legacy aircraft parts using Verisurf Reverse software, then 3D prints them as high-precision prototypes to evaluate form, fit and mechanical function. The finished prototype is then inspected using the original STL mesh model as the nominal, which maintains a digital workflow throughout the entire process.
“Reverse engineering and 3D printing has proven to be an essential part of our development workflow. We use the high-precision, demonstrable prototypes for much more than just form and fit. Quite often we rely on the prototypes to support customer engineering discussions. Projects move forward more quickly with better end results,” says Collins.
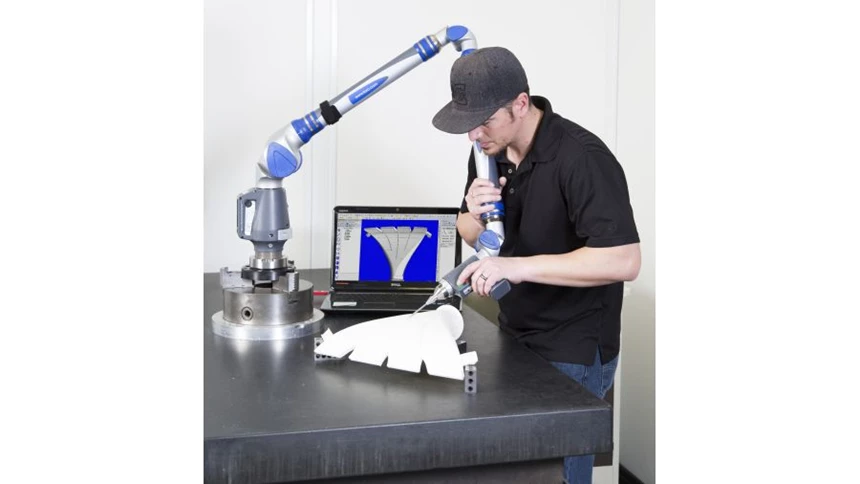
With today’s portable measurement solutions, a non-critical part can be reverse engineered, modeled, produced, inspected and installed with just three visits to the aircraft, all during routine maintenance stops:
- Scan the part to collect reverse engineering data;
- Perform a fit check using 3D printed prototype; and
- Install the new part.
For example, when parts for an older aircraft need to be replaced, oftentimes no spares, CAD data or original tooling are available. After years of use the original design specifications for the parts, such as duct work, may no longer fit as designed. In some cases, an originally designed part may have a design flaw that has been amended. In each case, reverse engineering and product realization provide practical ways for engineers to identify problems and apply recommended solutions. A part that would typically take eight to 16 weeks to create, can now be produced as a high-precision model in just a couple of days. The customer is then able to do a fit check using the model and approve production with confidence.
The process is straightforward. First the original part is disassembled and each component carefully reverse engineered using Verisurf software. Depending on the environment, the data can be captured using a CMM or portable CMM with either a touch probe or laser scanner head. “Contact probing provides greater measurement accuracy over non-contact scanning. Non-contact scanning is typically better for checking large surface areas for deviations or capturing/inspecting complex surface profiles,” says Collins.
Verisurf Reverse Software converts the captured point cloud data into STL mesh models suitable for 3D printing and again into 3D solid models for export to popular CAD formats. Design modifications are then made and final prototype components output to a Stratasys Dimension 1200es 3Dprinter.
Following design review and approval, the 3D prototype can be used as a representative model for subcontractors involved in the manufacturing process, such as machining, welding, coating and final assembly. “No number of drawings or computer models can replace the value of a 3D part to fully understand design intent, avoid costly mistakes and speed production,” says Collins.