The aerospace and defense industry is known for producing complex and advanced products—jet engines, aircraft, rockets, satellites, drones, and more—that move fast in a highly regulated environment. It is no wonder that these factors of speed, complexity, and policy compliance play key roles in the manufacturing process. This design tip explores how to improve aerospace development cycles through:
- accelerating production with digital manufacturing
- reducing components, which helps in lightweight part design, cuts items in an overall assembly, and reduces costs
- using a range of manufacturing methods and materials, which can accelerate development and add value to your designs
- streamlining quality and compliance assurances
1. Use Digital Manufacturing to Accelerate Product Development
At FacFox, we understand the importance of speed. Working extensively with companies in the aerospace and defense industry, we have accelerated the development over the years of a range of metal and plastic aerospace parts and products that include:
- Heat exchangers
- Manifolds
- Turbo pumps
- Liquid and gas flow components
- Fuel nozzles
- Conformal cooling channels
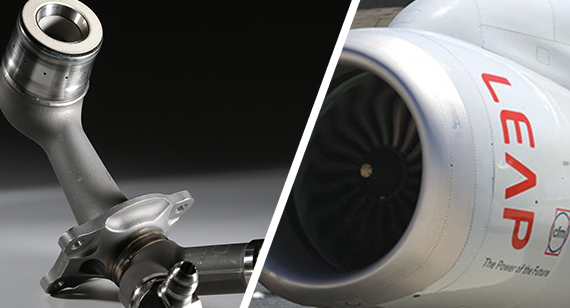
One of the drivers in our success is through experience and rigorous development of digital manufacturing tools. We have found the right blend of working with autonomous digital tools and hands-on application engineers to meet aerospace demands.
When starting the digital manufacturing process with many manufacturers, it can be easy to upload a CAD file into multiple online quoting tools.
Unfortunately, some manufacturers’ online quoting tools don’t take into account all of the back-end requirements, or offer all of a manufacturer’s processes. This is where we choose to be upfront so that each step required for the part or project is reflected in the initial quote.
When using online digital tools, quoting software can greatly accelerate development and production cycles.
However, to get the most out of these tools, make sure you are working with software (and a manufacturer) that includes the following:
- Takes into account all requirements and steps of the build or project
- Offers all available processes and materials
- Offers trained and experienced staff with years of manufacturing experience
A major challenge in the aerospace and defense industry is on-time delivery and quality. Industry sources say around 80% of orders generally show up on time. Yet, when those orders do show up on time, about 25% of parts do not meet the required quality. A common complaint from aerospace companies is when vendors promise a lead time with a cheaper price but could not deliver within the timeline quoted. Delays have led to missed deadlines and greater costs to fix than if they would have just started with the higher-priced vendor.
Our online, interactive quoting system turns your CAD model into a quote with immediate design analysis and feedback. Your design can be reworked to determine the ideal balance of processes, materials, time, and cost. This greatly increases efficiency as it isn’t necessary to talk with someone every time a part is needed. But when you need a knowledgeable person on your side, we have a team of applications engineers ready to back up our automated tools. All contacts, customer or not, get free access to our responsive team that understands how to design for our processes, reduce cost, and answer a myriad of other technical questions.
2. Reduce Components to Benefit Product Design
You may want to reduce overall components in a part or product design for several reasons.
First, lightweight is crucial in aerospace. Companies know just how many ounces of fuel it takes to fly a gram of weight in flight, for example, so slight reductions drive major gains. The choice of materials, and sometimes the method of manufacturing, also factor into this lightweight equation. But trimming part count helps, too.
Second, cutting costs is important. Plastics and metals can be expensive, and so can assembly time. Accordingly, if designs can lessen the number of components or parts, this can reduce materials and assembly time.
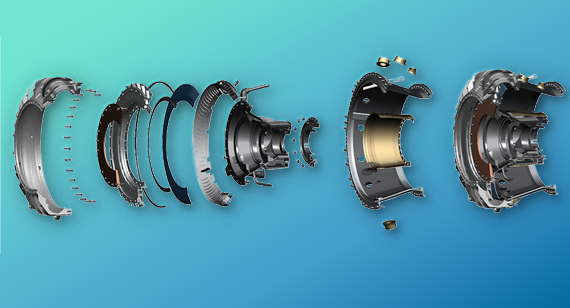
With these lightweight and cost considerations in mind, which materials work best for aerospace components? Titanium is often a go-to choice, available through machining and 3D printing services. This lightweight and strong material offer excellent corrosion and temperature resistance. Aluminum, and its high strength-to-weight ratio makes it a good candidate for housing and brackets that must support high loading. Aluminum also is available for both machined and 3D-printed parts. Inconel, a 3D-printed metal, is a nickel-chromium superalloy ideal for rocket engine components and other applications that require high-temperature resistance. Stainless steel also is a frequent materials choice. For example, SS 17-4 PH is used in the aerospace industry due to its high strength, good corrosion resistance, and good mechanical properties at temperatures up to 600 degrees F. Like titanium, it can be machined or 3D printed. Liquid silicone rubber is also widely used in the industry. This elastic fluorosilicone material is specifically geared toward fuel and oil resistance while optical silicone rubber is a good PC/PMMA alternative. Common applications in aerospace include soft-touch surfaces, gaskets, seals, and O-rings.
Finally, beyond lightweight and cost-cutting issues, the aerospace industry faces unique benefits and challenges with high risks and rewards. Companies are concerned with development cycles, prototyping, hot-fire testing, and production. So, while component reduction can help reduce part weight and assembly time, the real savings are in the reduction of the headaches and overhead associated with the supply chain and paper trail for each part. In aerospace, each component that goes into the final product has a tremendous amount of validation behind it such as material traceability, shock and vibe tests, rigorous inspections, and much more. In such a regulated industry, reducing parts can provide great value by reducing inventory, having fewer documents to track, and streamlining your supply chain.
3. Deploy a Range of Manufacturing Methods, Materials
If you have an internal machine shop but have to deal with a lot of different types of manufacturing in a small space, you might have taken projects to outside vendors for development work. It is important to find the right vendor with the capacity to meet your high demands for quality and speed. You may know but it bears repeating that there are no universal processes or materials. You need all the tools in your arsenal to find the best solutions to stay on the cutting edge. Therefore, work with companies that are able to offer a range of manufacturing processes and materials. We offer CNC machining, sheet metal fabrication, injection molding, and six different industrial-grade 3D printing (additive manufacturing) methods. Additionally, you can choose from hundreds of commercial-grade plastics, metals, and elastomers that are suitable for both prototyping and production. See our Materials Comparison Guide for a complete list.
CNC machining methods, specifically three- and five-axis milling, are frequently used in manufacturing today. For the aerospace industry, common materials are 6061-T6 aluminum, hard metals such as 304, 316, and 17-4PH stainless steel, and titanium.
What isn’t common are the size and geometric dimensioning and tolerancing (GD&T) capabilities of many shops. While it is common for the customer to state what tolerances are needed, look for companies that state what size and GD&T they can deliver.
Most aerospace customers have complex parts that can be more advanced than even our automated machining facilities can handle.
To solve this problem, we introduced our high-requirement or precision-machining option, which can accommodate larger parts and more complex geometries. This option helps our aerospace customers by repeatedly and reliably delivering on more complex parts as programs progress toward end-use production. Also, this high-requirement option is able to read both a CAD file and a drawing, accommodate larger parts with more complex features, provide tighter tolerances, perform secondary operations, and offer quality reporting options.
For detailed information on these high-requirement or precision-machining options, including tolerances, minimum and maximum part dimensions, and other design guidelines, visit our precision machining page. In addition, visit our website for basic design guidelines for CNC milling.
Additive Manufacturing—Processes and Materials:
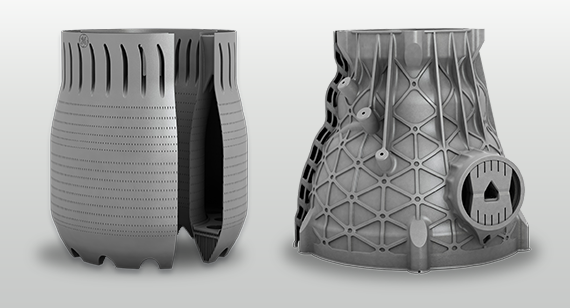
A considerable amount of aerospace and defense parts are metal. Accordingly, when it comes to metal 3D printing or additive manufacturing, most common materials are Inconel 718, the aluminum alloy AlSi10Mg, stainless steel (304 & 17-4), titanium, and cobalt chrome (CoCr). Again, the difference here will be the material and additive manufacturing processes available.
We use multiple additive processes: stereolithography, direct metal laser sintering (DMLS), selective laser sintering, Multi Jet Fusion, Carbon DLS, and PolyJet. DMLS has proven to be a desirable process in the aerospace industry because it offers:
- large range of materials
- increased functionality
- ability to accommodate the complexity and organic designs
DMLS does have a limited build space. However, we also offer large-format metal parts. We can build production-grade metal parts as large as 31.5 in. x 15.7 in. x 19.7 in. (800mm x 398mm x 500mm). We are initially focusing on Inconel 718 as a material to use to better serve the demand for larger complex parts in the aerospace industry. This large-format metal 3D printing, from our GE Additive Concept Laser X-Line machine, also is an example of how our company is technology agnostic, using machines, equipment, and processes sourced from a variety of companies.
Beyond the manufacturing methods referenced (subtractive and additive), we also offer a number of secondary or finishing options, if your design calls for these applications:
- Post-process machining – for 3D-printed metal parts
- Heat treatment – including HIP for 3D printed parts
- Additional plating
- Anodizing
- Basic assembly
- Chromate plating
- Cleaning
- Electroless nickel plating
- Part marking
- Passivation
- Powder coating
- Press fit and hardware
- Silkscreening
If you need several vendors for different processes or secondary processes, remember the benefits mentioned earlier about using one supplier with multiple processes. We offer many processes and materials while operating as a local vendor to reduce time and costs.
In addition, as we recently noted in our trend report on aerospace manufacturing, often the best solutions for aerospace and defense will involve a hybrid approach using multiple technologies in concert. Just as a traditional toolbox contains both hammer and pliers, so too do today’s advanced manufacturing operations house both additive and subtractive manufacturing systems and know-how.
4. Rely on Quality and Compliance Assurance
Finally, aerospace product designers and developers need to carefully navigate government and safety policy and compliance issues. Working in such a highly regulated industry, it is important to find vendors familiar with aerospace requirements. Traceability, documentation, testing, and certified parts that are USA/ITAR compliant in an ISO 9001 environment can decrease much of the work needed to be done, tested, or verified in-house.
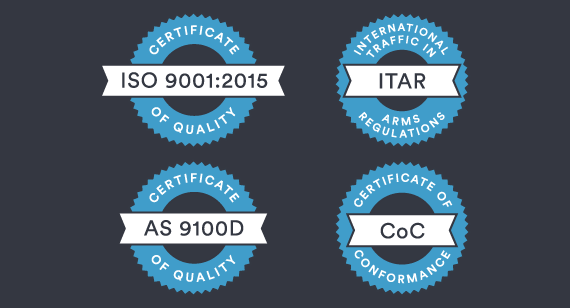
Governing bodies are continuously working on standards for additive manufacturing, so knowing exactly what is needed may be difficult to find for non-traditional processes. However, standards or certifications for finished parts apply no matter how it was manufactured. You will want to make sure vendors have certified materials, powder analysis, material traceability, and more depending on your needs.
We have already invested heavily in digital manufacturing methods to provide you with automated tools, documentation, testing, and traceability, all supported by our applications engineers, delivering you a streamlined and efficient digital thread. We offer the following quality documentation and report options in an ISO 9001, AS9100 certified, USA/ITAR compliant environment:
- Material certifications and heat lot numbers
- Certificate of conformance (CoC)
- First article inspections (FAI) – including AS9102 FAI for 3D-printed parts
- Various other inspection requests such as CMM, X-Ray or CT scanning
Ultimately, we will work with you to find the best solution and consider all steps of your project. If you would like more information, contact our applications engineers at 877-479-3680, email us at info@facfox.com, or start your design today by uploading your 3D CAD model to receive an interactive quote within hours.