The construction industry is perhaps the latest to adopt 3D printing as a viable manufacturing technology. But the technology has the huge potential to transform the industry by reducing production time and costs, while offering design flexibility and a high level of sustainability.
As highlighted in our Maturity Chart, which explores how 3D printing is evolving across industries, 3D printing within the construction sector remains a relatively novel approach, and there are a number of challenges to be overcome before it can be widely adopted.
To learn more about the current state of 3D printing in the construction industry, we’ll explore the key 3D printing benefits and technologies available for engineers and architects and the most exciting 3D printing projects in construction.
How can the construction industry benefit from 3D printing?
The construction industry has started to embrace 3D printing at a time when the sector is aggressively seeking solutions to address a number of challenges.
One is the minimisation of construction waste. For example, construction waste accounts for approximately 30% of all waste generated in the EU.
Furthermore, engineers and architects are increasingly facing limitations in design freedom put forward by the casting process.
Other issues involve drawbacks of manufacturing formworks on job sites and hurdles in transporting various materials from one location to the other.
Using 3D printing in the construction industry could help solve some of these problems by offering design freedom and a higher level of sustainability and automation.
Design flexibility
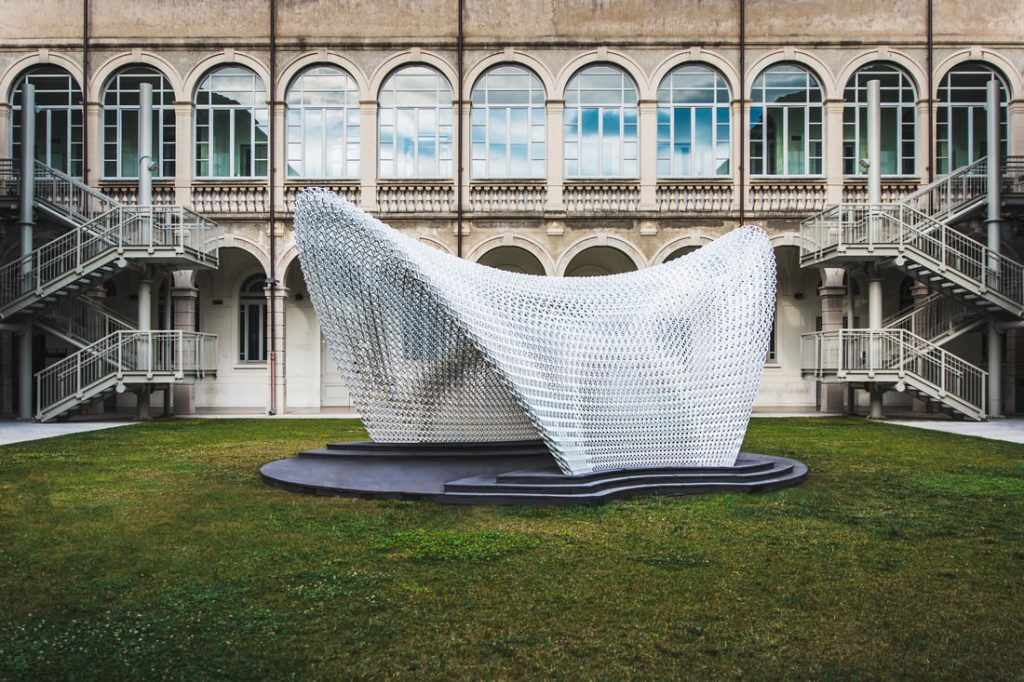
Reduced material waste
Reduced material waste is another benefit, as Additive Manufacturing (AM) builds parts layer by layer, using the precise amount of material required for the project. This could have a positive environmental impact, especially as 3D printing can use recycled and locally-sourced materials.
Reduced manual work
Using autonomous or semi-autonomous 3D printers in construction could mean reduced labour-intensive, manual work. The automation of the printing process also means reduced chances of human error or accidents and injuries on construction sites.
Quicker construction
Some construction 3D printers are designed to work on site. This helps to eliminate several time-consuming steps, like making precast formworks.
In construction, formwork refers to a temporary mould into which concrete is poured and formed. Formworks are used to create anything from bridges to foundations and the walls of a building and are typically manually crafted.
Today, there are several companies offering 3D printers that can be used to directly build walls on-site, without using formworks. This leads to a significantly accelerated construction process, which also benefits from reduced expenses on transportation of formworks to the construction site.
3D printing technologies for the construction sector
Depending on the application, several different AM methods can be used within construction:
Extrusion of concrete
One of the main methods used is paste extrusion, which involves using a robot arm or crane equipped with a nozzle to extrude the concrete in paste form onto a build platform.
This creates the contours of a building layer-by-layer, resembling a popular plastic Fused Filament Fabrication (FFF) technology.
An early pioneer of the extrusion process for the construction industry is Bherokh Khoshnevis, the founder of Contour Crafting. The technology developed by Contour Crafting offers a range of materials, including concrete, ceramics and polymers.
In addition to Contour Crafting, other companies offer solutions for concrete 3D printing, such as ICON, CyBE and Apis Cor, to name a few.
Wire Arc Additive Manufacturing
Wire Arc Additive Manufacturing (WAAM) is a method used for metal applications.
WAAM works by melting metal wire using an electric arc as the heat source. The process is controlled by a robotic arm and the shape is built upon a substrate material (a base plate) that the part can be cut from once finished.
The wire, when melted, is extruded in the form of beads on the substrate. As the beads stick together, they create a layer of metal material. The process is then repeated, layer by layer until the metal part is completed.
WAAM equipment can work with a range of metals, such as aluminium, steel and titanium, and the technology can be used to manufacture large structures. One such example of the possibilities of this method is MX3D’s steel bridge.
Sand binder jetting
Binder jetting can be used in construction to create moulds. The technology works by applying a liquid binding agent onto layers of powder material, thereby bonding it.
Binder jetting is particularly suitable for the production of formwork elements for concrete casting. This approach not only helps to save resources but also time and costs.
Another advantage is that complexity no longer plays a role when 3D printing formworks using binder jetting. Curvatures, detailed facades or undercuts can be easily 3D printed, pushing the boundaries of design in construction.
The most exciting examples of 3D printing in construction
3D-printed walls
In recent years, several companies have developed methods of constructing walls of buildings using 3D printing technology. One such example is China-based company, Winsun, which has produced large-scale constructions, such as a five-story apartment block and a 12,000-square-foot (1,100-square-meter) villa.
A large machine– more than 100 metres long – 3D printed hollow walls made of cement, sand and fibres mixture. The walls were transported to the construction site, reinforced and assembled. The potential of such a method could lead to significant savings in time, labour and materials.
Construction 3D printing in Dubai
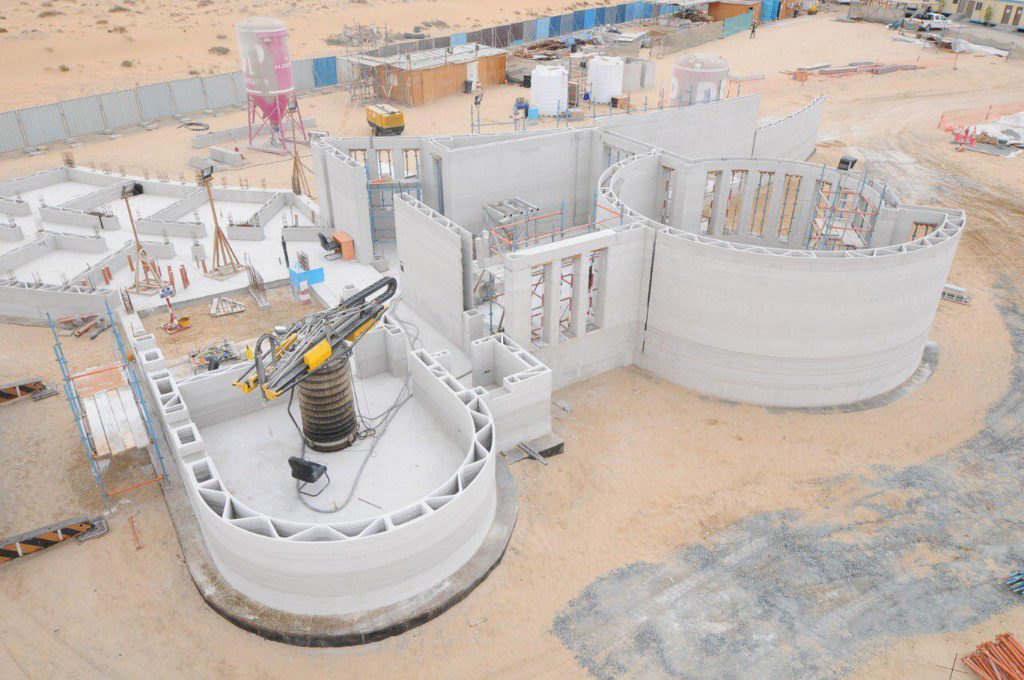
And the progress in this field is already evident.
For example, in 2019, Apis Cor, a US-based manufacturer of concrete 3D printers, collaborated with the Dubai Municipality to create a building, featuring two stories and some very complex architecture.
Apis Cor developed a gypsum-based material to run through the printer, which was sourced from a local producer.
The printing took place out in the open, to prove that the technology could handle a harsh environment without humidity and temperature control.
The building is reportedly one of the largest ones created with the help of on-site 3D printing.
Bridges
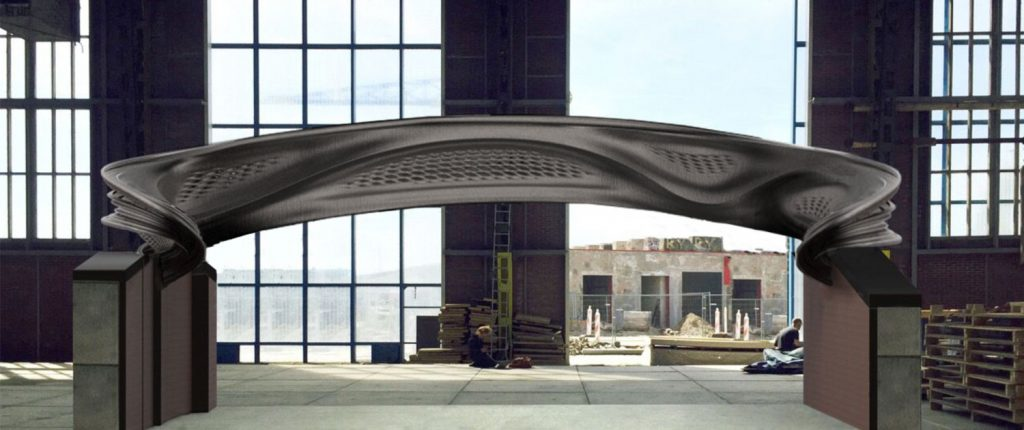
Madrid is home to the first 3D-printed concrete bridge, while the Netherlands has seen the construction of an 8 metre-long 3D-printed bridge for cyclists. The process took a total of 3 months for robots to create the concrete blocks for the bridge, made up of 800 layers which were then assembled to create the bridge.
Furthermore, the Netherlands-based Dutch robotics startup MX3D is developing a 3D-printed steel bridge equipped with smart technologies like sensors.
Made out of stainless steel, the curving structure of the bridge showcases the freedom of design provided by AM.
In 2019, the MX3D bridge passed its first testing phase of 20 tons and should be placed in its final destination over an Amsterdam canal later this year.
Interior design
The possibility of creating complex, intricate geometries opens up a completely new scope of creativity for interior designers. A recent example is Bottlepot – a London store with a 3D-printed interior using sustainable materials. This project demonstrates how 3D printing can be used to reduce waste in construction and shape the future for sustainable design.
Architectural models
One of the biggest impacts of 3D printing within construction has been in the production of architectural models. 3D printing has revolutionised the architectural modelling process by enabling a quick and digitised process for model-making.
An additional benefit to this is that 3D printing allows for quick and cost-effective design iterations, saving considerable time and reducing costs in the process.
Building components
3D printing has also proved suitable for manufacturing specific components and tools used in construction.
UK-based contractor, Skanska, is one of the first companies to have used 3D printing to manufacture building components like cladding.
In one project, Skanska used 3D printing to produce polymer cladding nodes for the roof of the 6 Bevis Marks business-centre in London. This approach has introduced a more advantageous alternative to traditional techniques in terms of time and cost savings.
3D-printed formworks
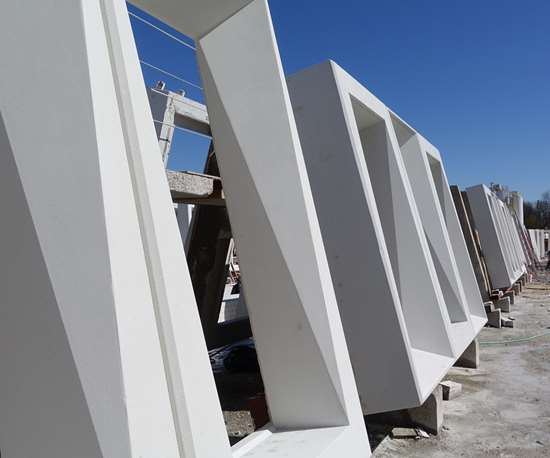
Another example involves using 3D-printed formwork in a large-scale renovation project for a 42-story residential and commercial building in New York City.
Gate Precast, a company which had been working on the new facade for the building, found that creating wooden moulds for the project would be a major undertaking that could take up to 9 months to complete. The moulds required were large – some of them measuring up to 2.6 x 1.7 x 0.5 m, further adding to the long production times.
To speed up the process, the company decided to experiment with 3D printing, partnering with Oak Ridge National Laboratory (ORNL) to use its BAAM technology.
Thanks to BAAM, the company was able to print moulds between 8 and 11 hours each, with an additional 8 hours of machining to achieve the desired surface finish. The moulds were made with carbon fibre-reinforced ABS, a common thermoplastic mixed with chopped carbon fibres for additional strength.
The result is a strong mould that can support as many as 200 concrete pours in its lifetime, compared to 15-20 pours for a wooden mould.
The company believes that without the 3D-printed moulds and BAAM, it would have been impossible to create the forms within the timeframe required for this project.
Challenges to adopting 3D printing in the construction industry
While AM holds huge potential for the construction industry, here are still a number of barriers to wider adoption.
One of the key issues is that of quality control. 3D printing has raised questions over how it performs compared to traditional construction materials and methods: Will a 3D-printed home last as long as a traditionally built home? Will it be structurally sound and safe in the event of a fire or natural disaster?
Regulation for construction is unsurprisingly stringent, and the new technologies and materials offered by AM are still to be incorporated into building standards and codes.
Furthermore, 3D printing requires experienced operators and designers, meaning investment in training to make the most of automated technology and software skills.
Another barrier to overcome is the limited range of construction materials that can be 3D printed. That said, research is being conducted, particularly with regard to concrete and bio-based renewable materials.
The future of 3D printing in construction
Despite visions of entirely 3D-printed buildings, the technology will not replace traditional construction methods – at least not in the short term.
Perhaps one of the biggest use cases of AM technology may lie in the production of complex components, such as joints, facades and formworks, leveraging the benefits of freedom of design that AM provides.
In addition to design flexibility, on-site 3D printing can also help reduce waste on construction sites, serving as a good stepping stone into a more sustainable future.
Looking at the bigger picture, 3D printing can be one of the key solutions to the current challenges in the construction sector, as it gradually advances to become a more sustainable, flexible and automated construction technology.