What is SLS?
Selective Laser Sintering (SLS) is an Additive Manufacturing process that belongs to the Powder Bed Fusion family. In SLS, a laser selectively sinters the particles of a polymer powder, fusing them together and building a part layer-by-layer. The materials used in SLS are thermoplastic polymers that come in a granular form.
SLS 3D Printing is used for both prototyping of functional polymer components and for small production runs, as it offers a very high design freedom, high accuracy and produces parts with good and consistent mechanical properties, unlike FDM or SLA. The capabilities of the technology can be used to its fullest though, only when the designer takes into consideration its key benefits and limitations.
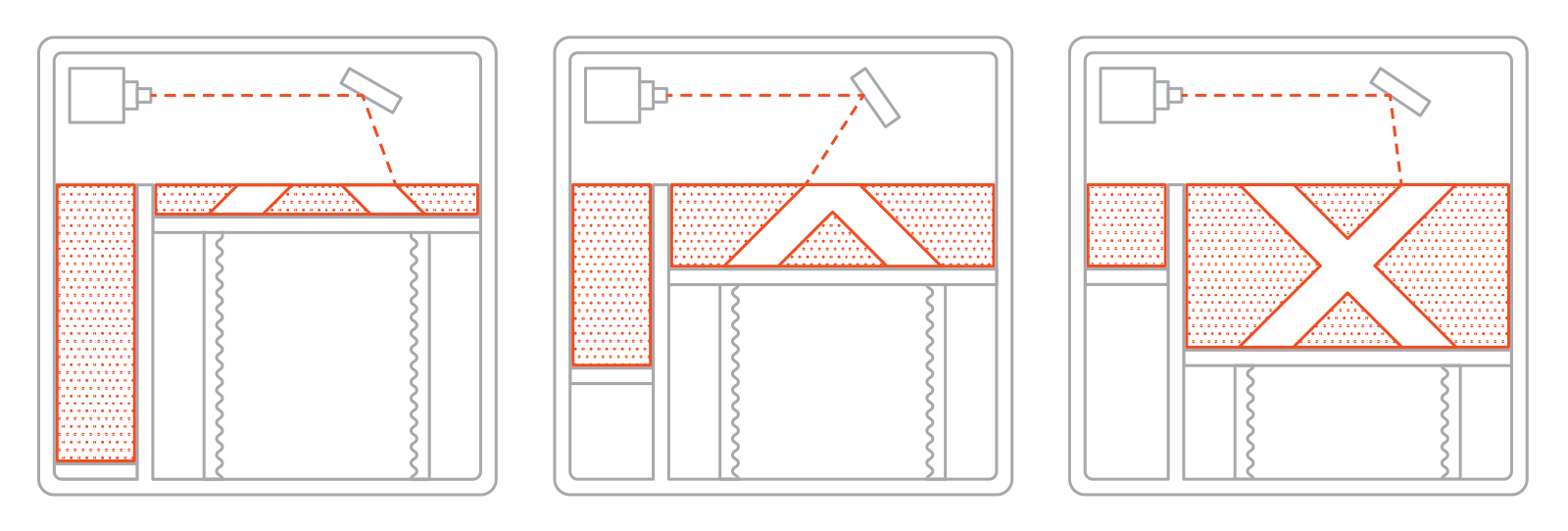
How does SLS work?
Here is how the SLS fabrication process works:
I. The powder bin and the build area are first heated just below the melting temperature of the polymer and a recoating blade spreads a thin layer of powder over the build platform.
II. A CO2 laser then scans the contour of the next layer and selectively sinters (fuses together) the particles of the polymer powder. The entire cross-section of the component is scanned, so the part is built solid.
III. When the layer is complete, the build platform moves downwards and the blade re-coats the surface. The process then repeats until the whole part is complete.
After printing, the parts are fully encapsulated in the unsintered powder and the powder bin has to cool down before the parts can be unpacked. This can take a considerable amount of time (up to 12 hours). The parts are then cleaned with compressed air or other blasting media and are ready to use or further post-process. The remaining unsintered powder is collected and can be reused (SLA powder is only 50% recyclable though).
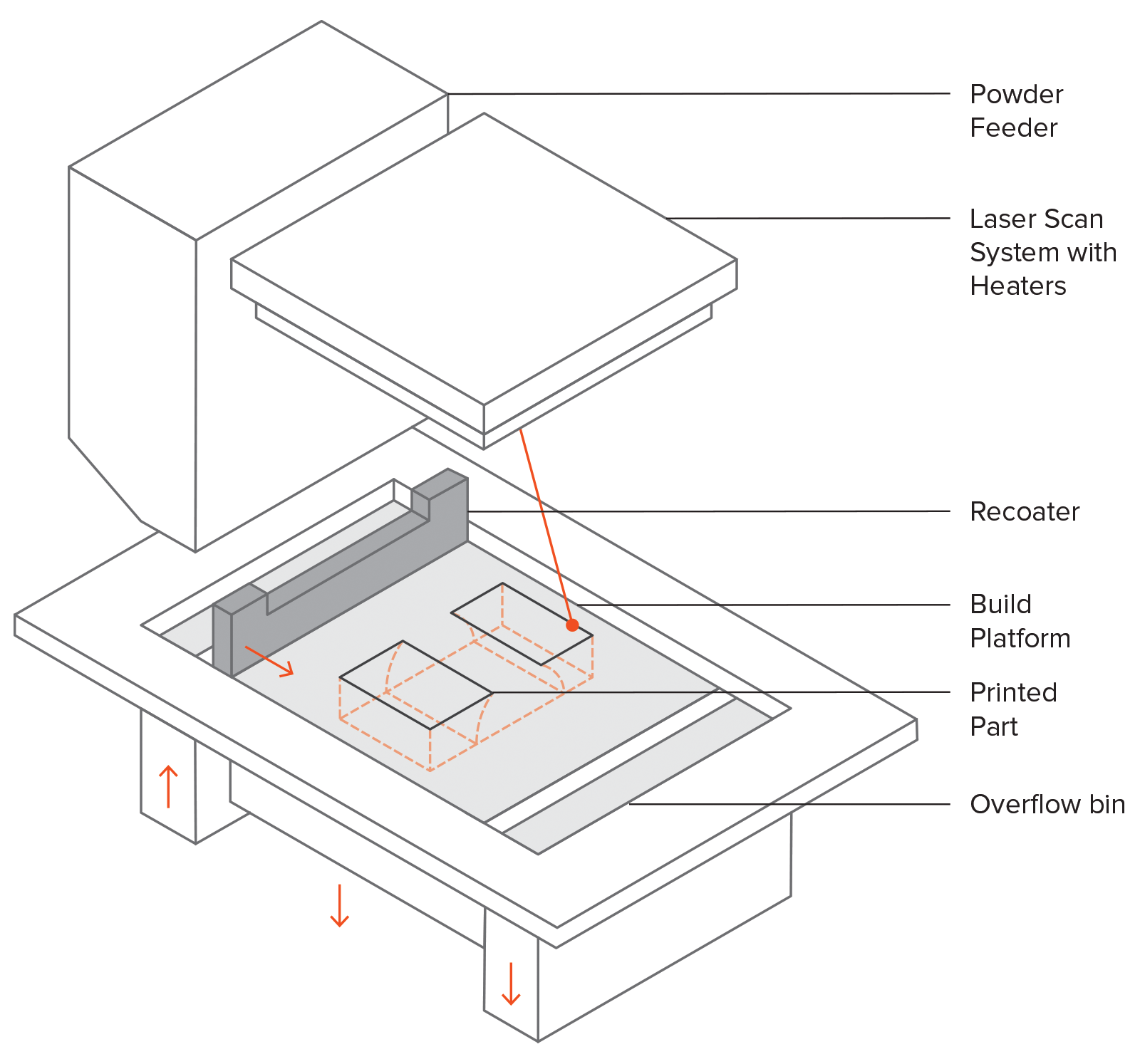
Characteristics of SLS
Printer Parameters
In SLS almost all process parameters are preset by the machine manufacturer. The default layer height used is 100-120 microns.
A key advantage of SLS is that it needs no support structures. The unsintered powder provides the part with all the necessary support. For this reason, SLS can be used to create freeform geometries that are impossible to manufacture with any other method.
Taking advantage of the whole build volume is very important when printing with SLS, especially for small batch productions. A bin of a given height will take about the same time to print, independent of the number of parts it contains. This is because the re-coating step determines the total processing time (laser scanning occurs very rapidly) and the machine will have to cycle through the same number of layers. Bin packing may affect lead times of small orders, as operators usually wait until a bin is filled before starting a print.
Layer Adhesion
In SLS, the bond strength between the layers is excellent. This means that SLS printed parts have almost isotropic mechanical properties.
The mechanical properties of SLS specimens printed using standard polyamide powder (PA 12 or Nylon 12), the most commonly used material in SLS, are shown in the next table and compared to the properties of bulk nylon.
X-Y direction | Z direction | Bulk PA12 | |
---|---|---|---|
Tensile Strength | 48 MPa | 42 MPa | 35 – 55 MPa |
Tensile Modulus | 1650 MPa | 1650 MPa | 1270 – 2600 MPa |
Elongation at break | 18% | 4% | 120 – 300% |
SLS parts have excellent tensile strength and modulus, comparable to the bulk material, but are more brittle (their elongation at break is much lower). This is due to the internal porosity of the final part.
A typical SLS printed part is about 30% porous.
Porosity gives SLS parts their characteristic grainy surface finish. It also means that SLS parts can absorb water, so they can be easily dyed in a hot bath to a large range of colors but also that they require special post-processing if they are to be used in a humid environment.
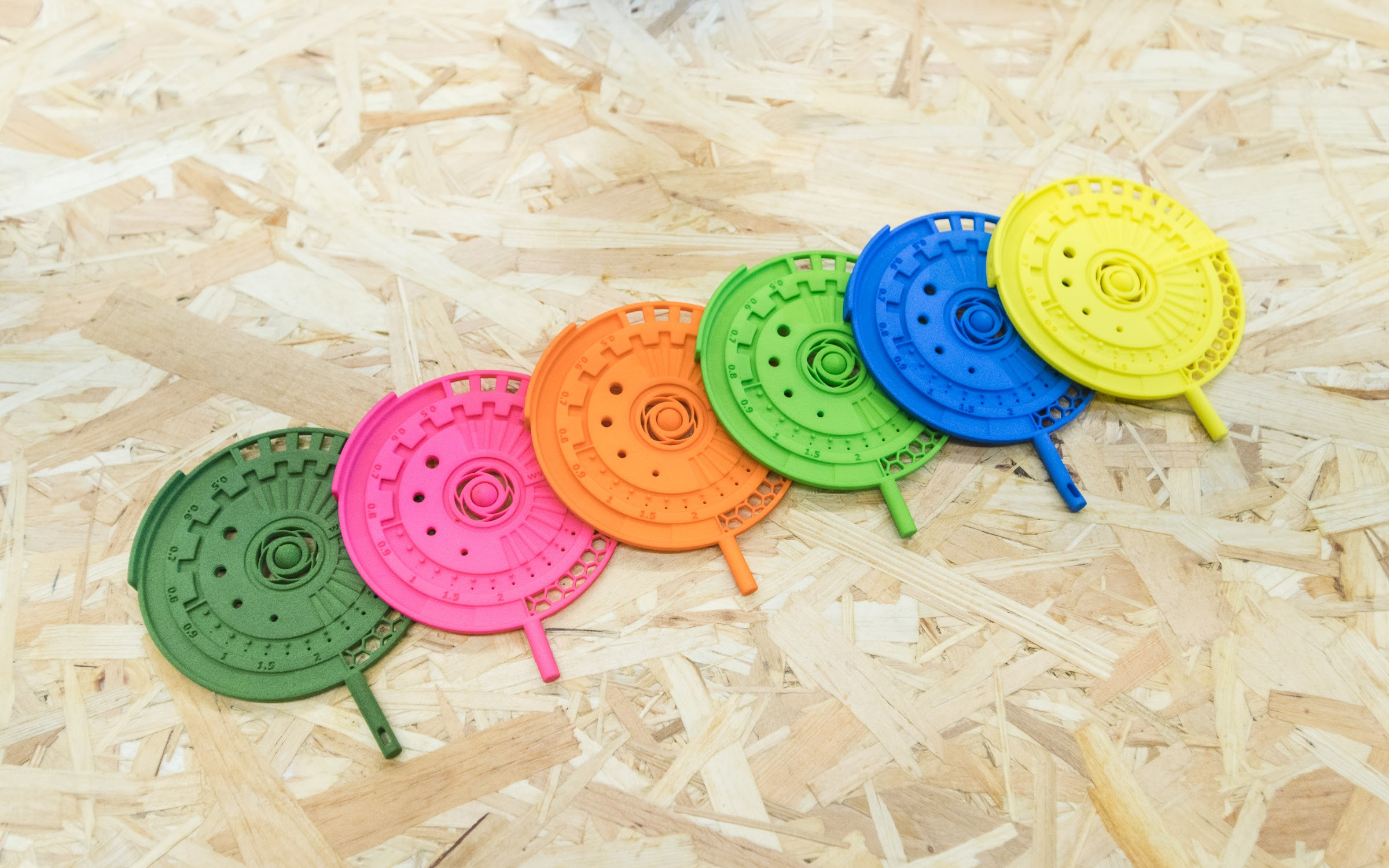
Shrinkage & Warping
SLS parts are susceptible to shrinkage and warping: as the newly sintered layer cools, its dimensions decrease and internal stresses buildup, pulling the underlying layer upwards
3 to 3.5% shrinkage is typical in SLS, but machine operators take this into account during the build preparation phase and adjust the size of the design accordingly.
Large flat surfaces are most likely to warping. The issue can be mitigated somewhat by orientating the part vertically in the build platform, but the best practice is to reduce its volume, by minimizing the thickness of the flat areas and by introducing cutouts to the design. This strategy will also reduce the overall cost of the part, as less material is used.
Oversintering
Oversintering occurs when radiant heat fuses unsintered powder around a feature. This can result in loss of detail in small features, like slots and holes.
Oversintering depends both on the size of the feature and the wall thickness. For example, a 0.5 mm wide slot or a hole with 1 mm diameter will print successfully on a 2 mm thick wall, but these features will disappear when the wall thickness is 4 mm or larger. As a rule of thumb, slots wider than 0.8 mm and holes with a diameter larger than 2 mm can be printed in SLS without fear of oversintering. See this article for more design guidelines.
Powder Removal
Since SLS requires no support material, parts with hollow sections can be printed easily and accurately.
Hollow sections reduce the weight and cost of a part, as less material is used. Escape holes are needed to remove the unsintered powder from the inner sections of the component. It is recommended to added to your design at least 2 escape holes with a minimum 5 mm diameter.
If high stiffness is required, parts must be printed fully solid. An alternative is to make a hollow design omitting the escape holes. This way tightly packed powder will be entrapped in the part, increasing its mass and providing some additional support against mechanical loads, without an effect on the build time. An internal honeycomb lattice structure can be added to the hollowed interior (similar to the infill patterns used in FDM) to further increase the stiffness of the component. Hollowing a part this way may also reduce warping.
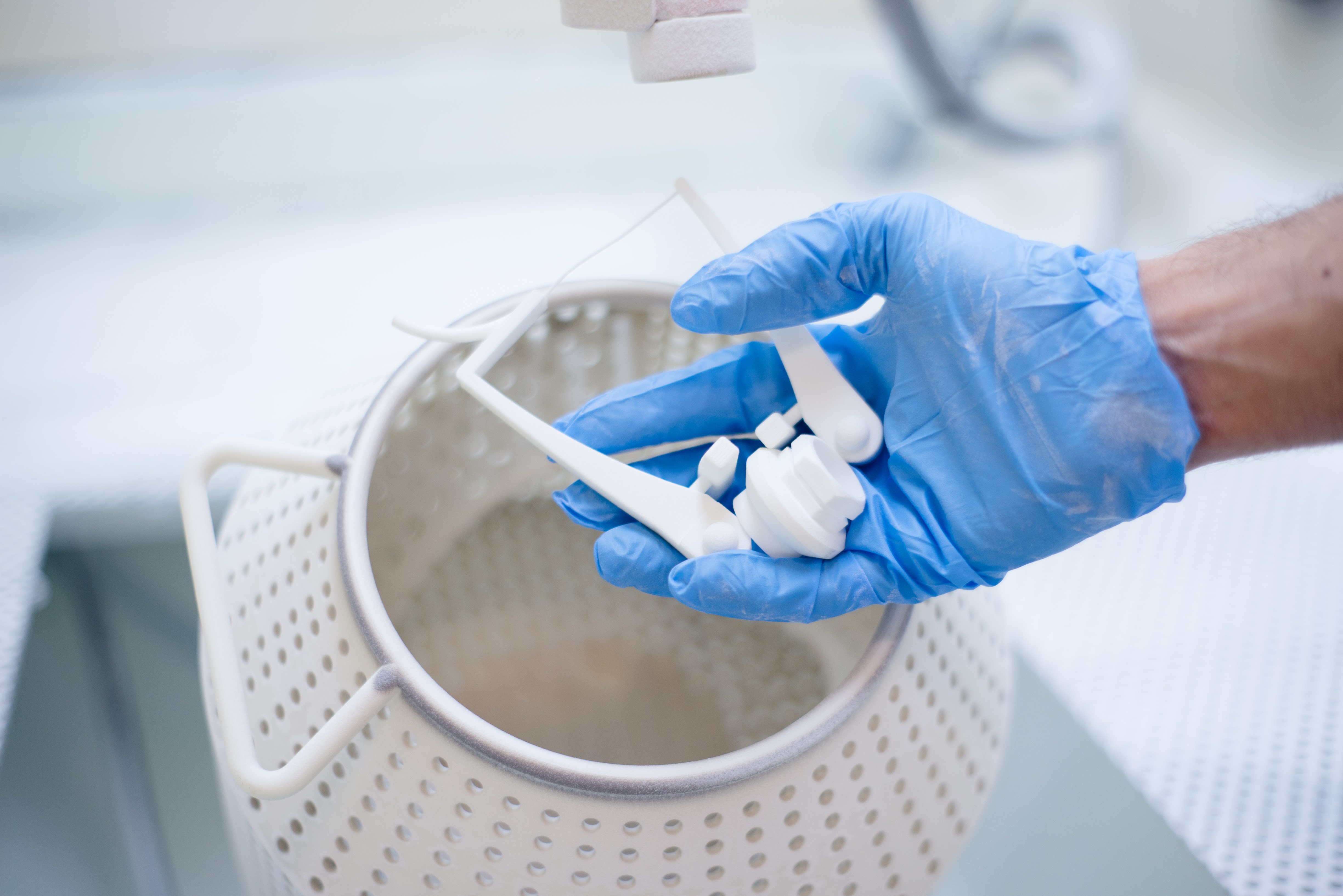
Common SLS Materials
The most widely used SLS material is Polyamide 12 (PA 12), also known as Nylon 12. The price per kilogram of PA 12 powder is approximately $50 – $60. Other engineering thermoplastics, such as PA 11 and PEEK, are also available but are not as widely used.
Polyamide powder can be filled with various additives (such as carbon fibers, glass fibers or aluminum) to improve the mechanical and thermal behavior of the produced SLS part. Materials filled with additives are usually more brittle and can have highly anisotropic behavior.
Material | Characteristics |
---|---|
Polyamide 12 (PA 12) |
Good mechanical properties
Good chemical resistance
Matte, rough surface
|
Polyamide 11 (PA 11) |
Fully isotropic behaviour
High elasticity
|
Aluminium-filled nylon (Alumide) |
Metallic appearance
High stiffness
|
Glass-filled nylon (PA-GF) |
High stiffness
High wear & temperature resistance
Anisotropic behaviour
|
Carbon-fiber filled nylon (PA-FR) |
Excellent stiffness
High weight-strength ratio
Highly anisotropic
|
Post Processing
SLS parts produces parts with a powdery, grainy surface finish that can be easily stained. The appearance SLS printed parts can be improved to a very high standard using various post processing methods, such as media polishing, dyeing, spray painting and lacquering. Their functionality can also be enhanced by applying a watertight coating or a metal plating. An extensive article on post processing of SLS parts can be found here.
Benefits & Limitations of SLS
The key advantages and disadvantages of the technology are summarised below:
- SLS parts have good, isotropic mechanical properties, making them ideal for functional parts and prototypes.
- SLS requires no support, so designs with complex geometries can be easily produced.
- The manufacturing capabilities of SLS is excellent for small to medium batch production.
- Only industrial SLS systems are currently widely available, so lead times are longer than other 3D printing technologies, such as FDM and SLA.
- SLS parts have a grainy surface finish and internal porosity that may require post-processing, if a smooth surface or water tightness are required.
- Large flat surfaces and small holes cannot be printed accurately with SLS, as they are susceptible to warping and oversintering.
Detailed design guidelines for each of the aspects discussed here are given in a later article of the Knowledge Base. The main characteristics of SLA are summarized in the table below:
Selective Laser Sintering (SLS) | |
---|---|
Materials | Thermoplastics (usually nylon) |
Dimensional accuracy | ± 0.3% (lower limit of ± 0.3 mm) |
Typical build size | 300 x 300 x 300 mm (up to 750 x 550 x 550 mm) |
Common layer thickness | 100 – 120 microns |
Support | Not required |
Rules of Thumb
- SLS can produce functional parts from a large range of engineering plastics, most commonly Nylon (PA12).
- The typical build volume of an SLS system is 300 x 300 x 300 mm.
- SLS parts exhibit good mechanical properties and isotropic behaviour. For components with special requirements, additive-filled PA powders are available.