Hyperganic, a German company, builds generative design software to 3D print objects as complex as nature. Though it was founded in 2015, it’s just now ready to reveal what its powerful algorithms can do.
Tucked away on a wide, tree-lined street off the glamourous Leopoldstraße in Munich, Germany, is the home of a deep-tech software company capable of transforming additive manufacturing.
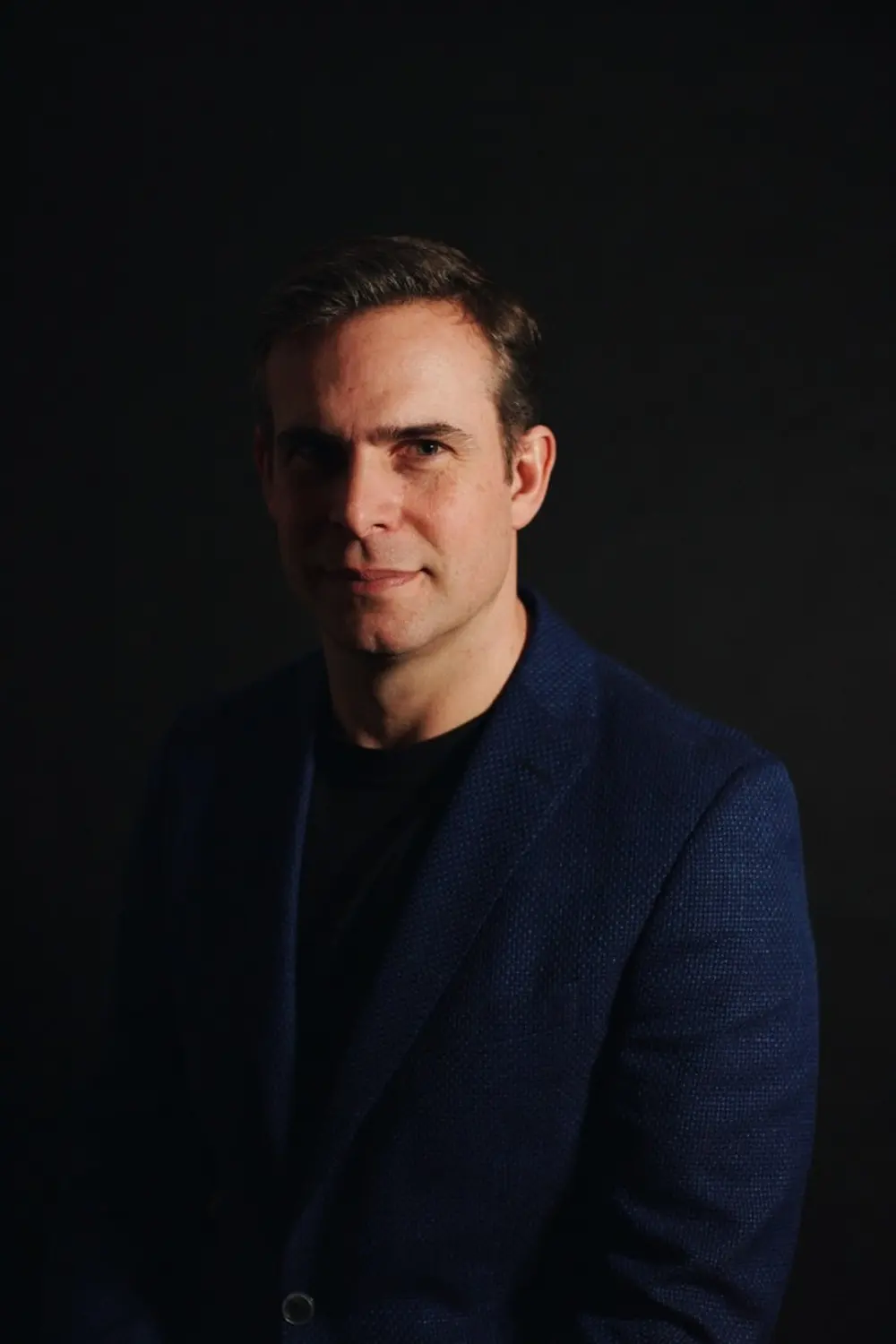
Hyperganic, the latest venture by German entrepreneur Lin Kayser, is on a mission to use 3D printing to produce objects that approach nature’s complexity using generative design.
Using powerful algorithms, Kayser has created a voxel-based software that strips away the design constraints of STL files.
“Manufacturing is undergoing a transformation as fundamental as the move to mass production 100 years ago,” explains Kayser.
“The design of these objects requires a radically new approach, where they are not engineered visually, but with their functional intent at the core,” he says. “We foresee a world where parts, assemblies and entire machines are specified by the engineer on an abstract level and then created using algorithms, using a process of digital evolution.”
His vision is grand, but it isn’t Kayser’s first time building a successful business. Hyperganic’s office was formerly home to his company IRIDAS, which Adobe acquired in 2011.
The office is decorated with a nod to the opulence and glitz of Old Hollywood. There are chandeliers hanging in most rooms, a feature Kayser says was both a design choice and a practical one, since they were cheaper than other lighting options.
It’s here that this new technology has come to life.
The Freedom to Design Without Limitations
Though Hyperganic has been around since 2015, it’s just now coming out of “stealth mode”, says business development director Markus Finke.
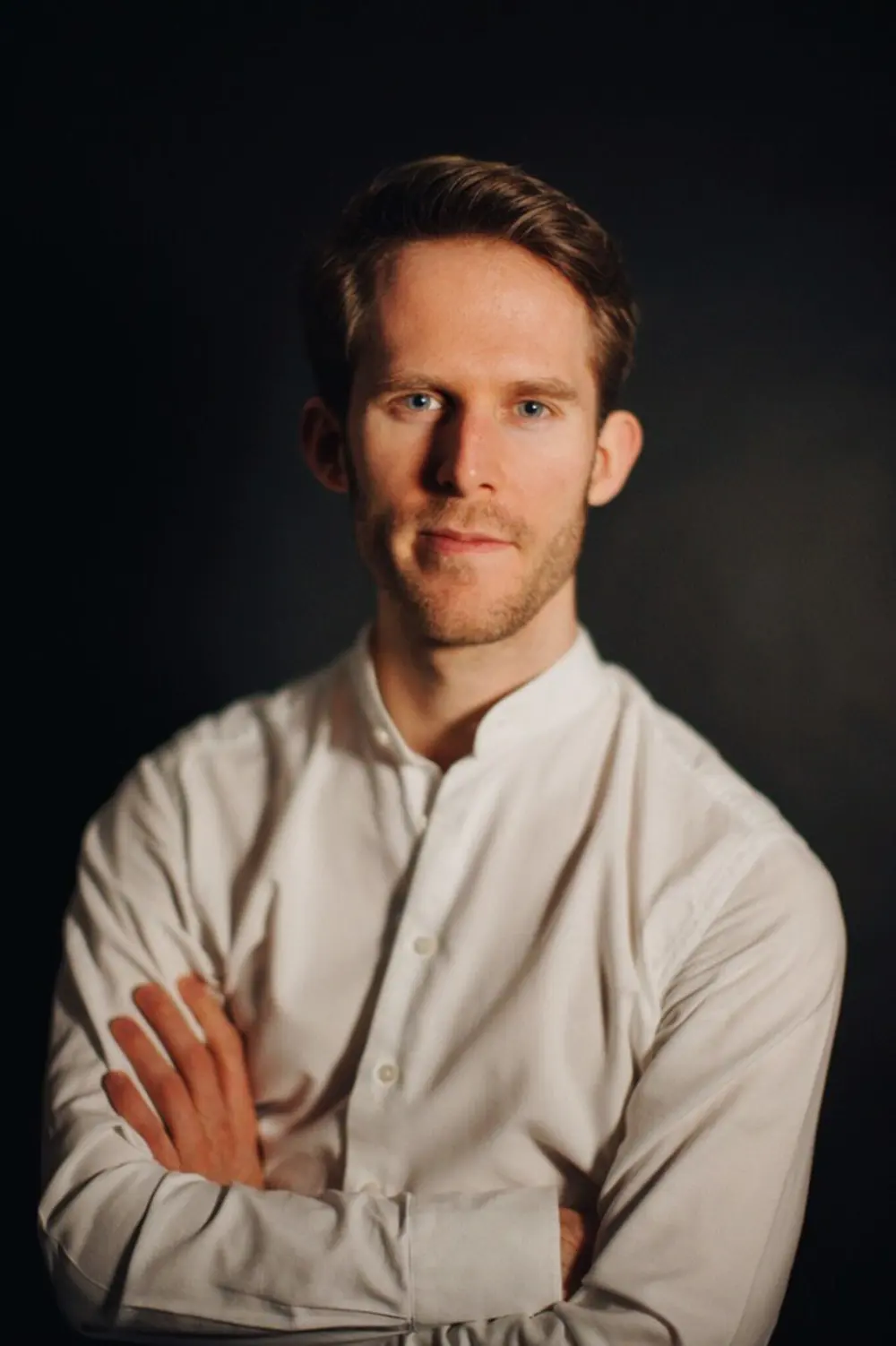
The company’s website is fairly “cryptic”, admits Finke, but he is nonetheless eager to extoll the potential impact the technology could have.
“What we’re looking at is designing objects that can have any complexity you like,” he says. “And on the other side, we have the potential to completely automate workflows. And that’s really the new big thing.”
All objects designed today come from a traditional manufacturing approach. You begin with a block and carve out parts or add bits to get the machine you want. This has worked well, but it limits the complexity you can achieve.
3D printing, though it theoretically offers an escape from this, is similarly hampered because all files are mesh-based and only concerned with the surface of a build.
“Once you go additive and you want to design really complex shapes like plants or objects that have the complexity of nature, then it becomes very difficult,” says Finke.
You have the potential to have information about volume with 3D printing, which is produced layer by layer, and not just the exterior shape. But CAD programs are notoriously bad at this because they’re not designed for that.
Hyperganic’s software solves this by creating voxel-based 3D models you can use on any CAD viewer, while also providing the volume information they cannot offer.
“We give people the freedom to design without limitations: Whatever you can dream, whatever you can imagine, you can essentially build it,” says Finke. “It’s possible to do that, complexity-free.”
Bringing Customization to the Masses
Another advantage of Hyperganic’s software is customization.
“Why are you not wearing the perfect shoe that fits right from the beginning?” asks Finke. “By the way, these hurt a lot,” he gestures to his own brown leather pair.
“This morning, I sprayed softener in there and now it’s a little better. But why?” he asks again.
The ideal scenario would be where the technology makes customization as easy as hitting CTRL P, says Finke. Customers can walk into a store, have their feet scanned for custom-made shoes and insoles, for example, and after paying for their order, the optimal shoe and insole can go straight into production, without any human guidance.
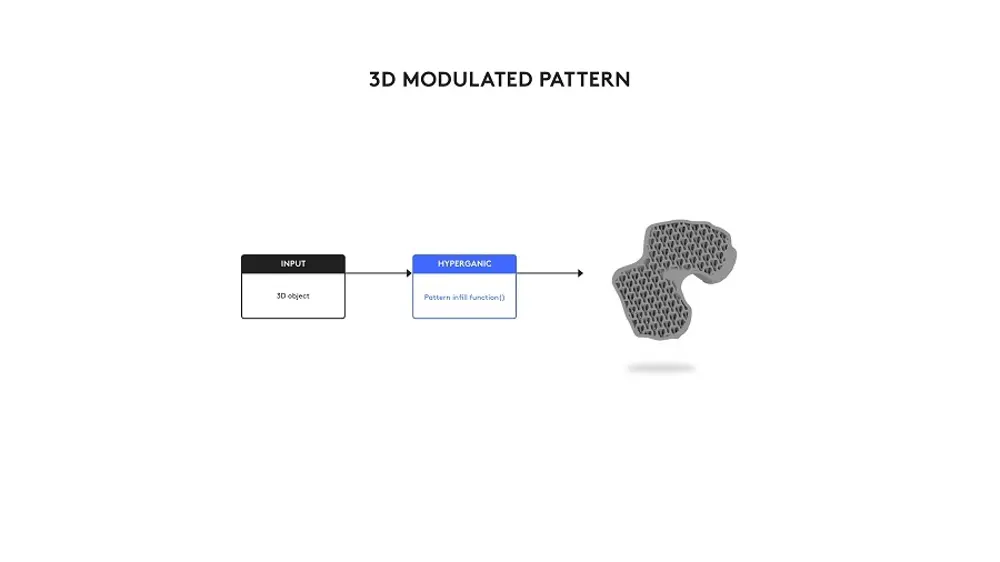
Though the process at present can be somewhat automated, there still needs to be a person to run it, and the end result isn’t a fluid shape that is truly a one-to-one copy of your foot, says Finke.
But, this will eventually be possible using Hyperganic’s technology, he says.
A helmet is another such example. While it may sound simple to make a scan of your head and then create a helmet that fits perfectly, it’s actually not easy with standard technology.
However, “if you work in a voxel space with a high-performance voxel engine, this is a relatively simple mathematical equation. You just say ‘I have the basic shape, I want to subtract the shape of the head,’ and in the end, you have the optimal helmet that can go straight into production — so you can automate that as well.”
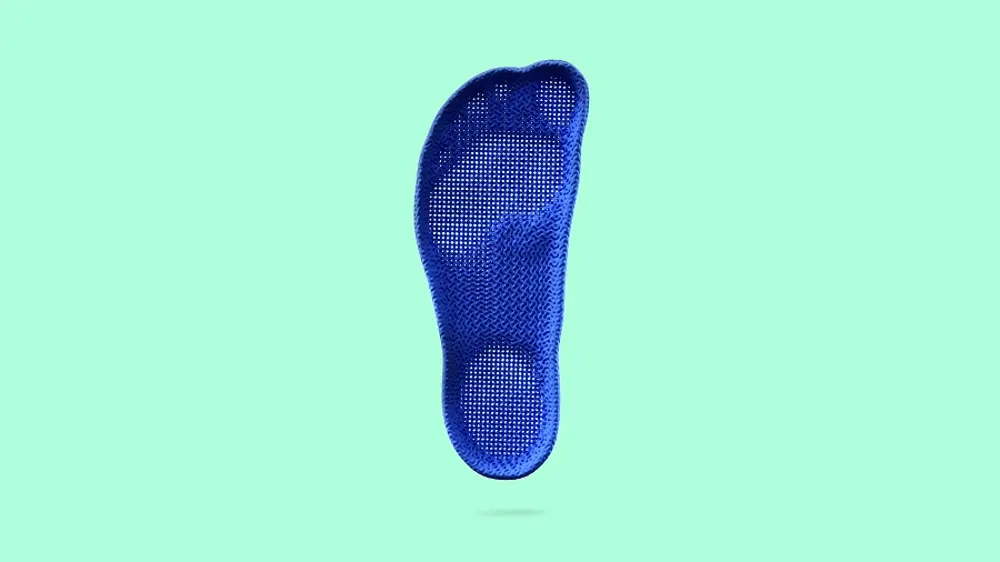
Hyperganic Already Finding Innovative Solutions to Design Problems
While flying under the radar, Hyperganic spent the last two years building up its first commercial applications, says Kayser. During that time, it had the luxury of approaching clients in a range of fields that they’d like to work with themselves.
“We went about it very selectively, saying, ‘I think that would be a really good use case to apply this kind of technology,’” says Finke.
And despite its vague website, Hyperganic’s recent public exposure through a talk at a TEDx event has already attracted new customers — and it’s expanding into fields that are ripe for disruption, says Kayser.
“People approach us with the craziest challenges, things they couldn’t solve previously with the current mesh-based system,” Finke says, adding, “And we solved them.”
Though he’s hesitant to speak about clients and the work they’ve done due to privacy concerns, Finke points to their statement piece, a rocket engine created with their own technology, to highlight what they can do.
Uli Langer, a partner manager at AM Ventures, which invests in additive manufacturing technologies and was established by the same founder as EOS, describes working with founder Kayser as a “lucky coincidence.”
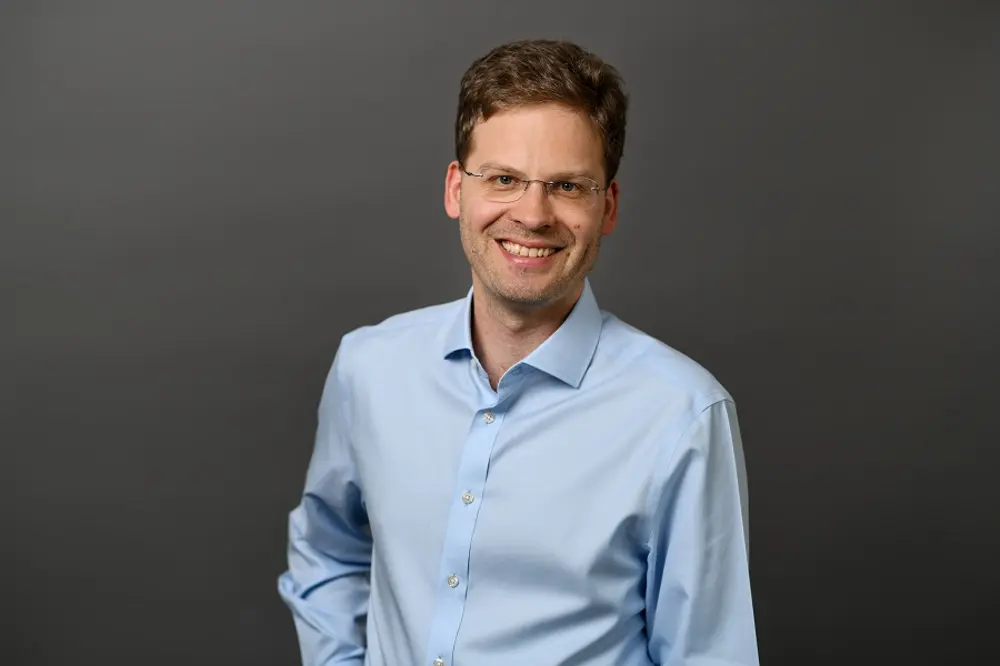
It paid off. Hyperganic used one of AM Ventures’ metal 3D printers, an EOS M 290, to print a rocket engine to showcase the technology.
The rocket is silver, created with aerospace-grade metal, and resembles a sculpture or piece of art, with blood vessels lining the sides — in short, radically different from a traditional rocket engine.
That’s because it was created by Hyperganic’s software, which uses generative design, and not by engineers.
“Nobody would have designed a rocket engine like this,” says Langer. “This is very interesting for us because now we can approach the customers with a different offering.”
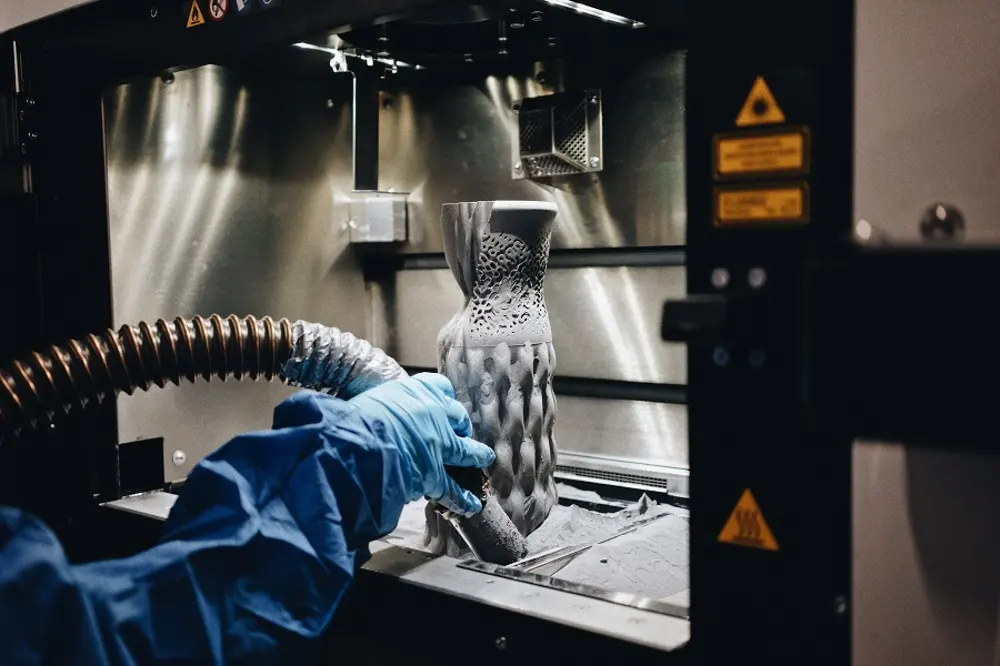
Instead of asking what an object should look like in the manufacturing process, the question becomes what the object should be able to do. The software then comes up with a design optimized for this purpose, that will potentially look completely surprising.
“Basically, it’s interesting for every startup that is somehow related to the design of parts,” says Langer.
Hyperganic’s technology isn’t for everyone though, he points out.
“If a customer says this is the part I want, just print it for me, the Hyperganic software can’t help you anymore,” he says. “It can only help you if you have a certain freedom of design where you can use the power of the algorithms to optimize the design.”
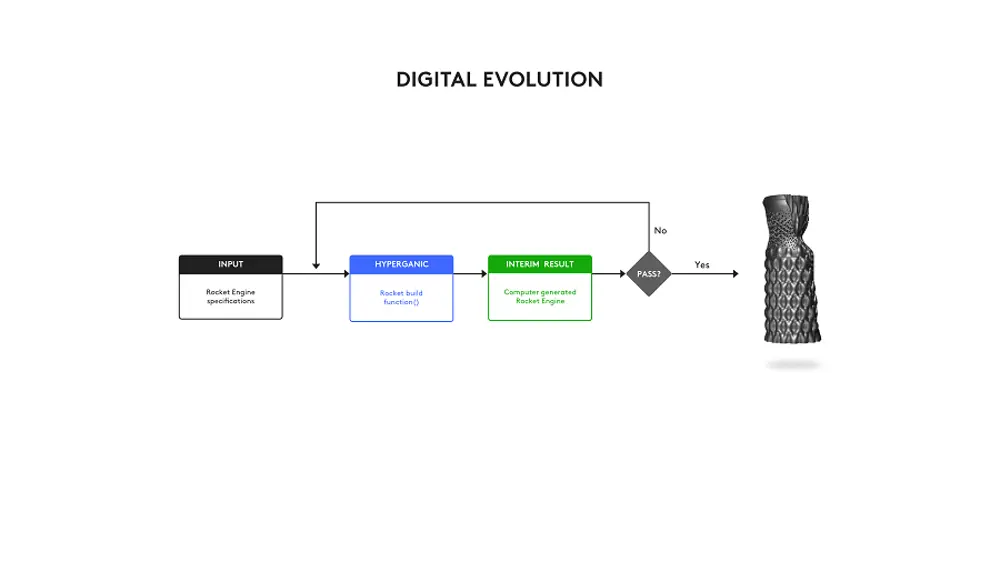
Not Just for Big Companies
When it comes to pricing, Finke is coy. Their technology costs “a lot,” he laughs.
However, he will say that the company is profitable.
Hyperganic doesn’t sell its software. Instead, it sticks to the success parameters of its customers, says Finke. In many cases, this could mean creating a revenue sharing model.
In an ideal setting, Hyperganic sets up the entire workflow and receives an upfront commitment from the customer.
Finke won’t comment on the exact cost of a rev-share model but says, “I think we’re well worth the money in the end.”
Though the costs of using their software may seem to make it out of reach for smaller companies or startups, Finke says this isn’t the case since these companies are more agile and able to disrupt the industry.
“You can really enable small companies to do great things with this (technology),” he says.
In fact, Hyperganic is in talks with five startups in AM Ventures’ ecosystem, says Langer, but they haven’t implemented anything yet.
As for what’s next, Kayser says they plan to focus on applications “that are not possible with traditional technologies. Over the next five years, we expect to become the dominant platform for computer-generated, AI-driven design and engineering.”
Source: Hyperganic: Voxel-based Software for Complex 3D Printing | All3DP