Wondering if you can 3D print rubber? Flexible material can definitely be 3D printed, but read on to get the full scoop!
Keeping it simple, you can’t 3D print pure rubber. But why not?
This is due to how rubber is made. Broadly speaking, most rubber comes from latex, which comes from trees, and this latex is “natural”. For it to be converted to a more durable “rubber”, a lot of processing is required to harden it and make it industry acceptable. This processing converts the rubber into a thermosetting polymer.
Thermosetting polymers such as processed rubber can’t be re-heated to melt and then re-solidify, unlike thermoplastics like PLA or ABS. Heating a thermosetting polymer will simply burn it as well as cause it to release toxic fumes.
That said, you can easily print flexible materials on an FDM or SLA machine. Both technologies operate rather differently from one another, but both have their own advantages.
In this article, we’ll go over different flexible materials as well as a few suggestions on how to use them depending on your 3D printing technology of choice. Then, we’ll include some popular brands to consider.
The Flexible Scene
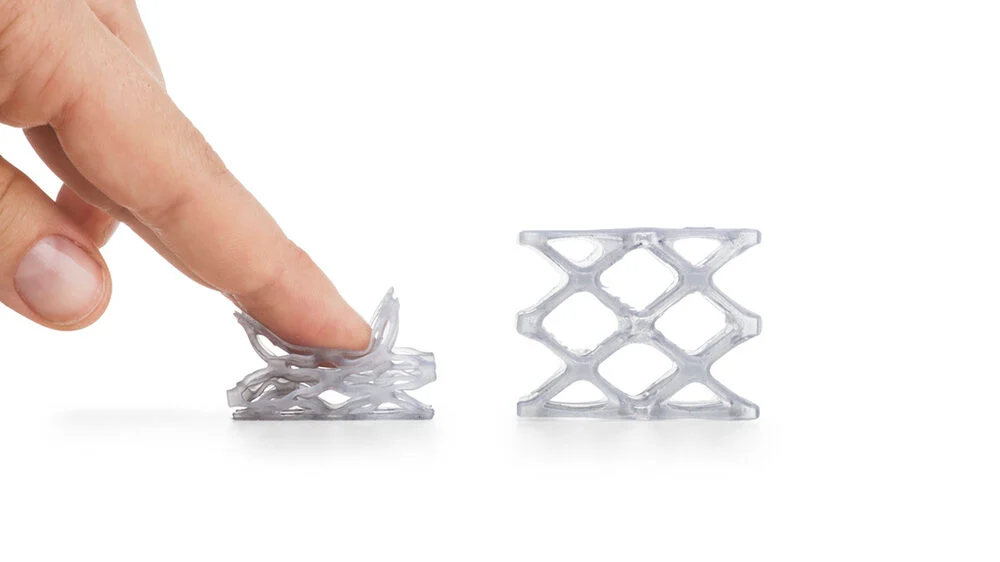
There are many flexible materials available, but the following are the most commonly known and used. Their acronyms are short and sweet – compared to the mouthfuls that are their full name. It’s worth noting that the flexible filaments available are directly based on the following materials, while their resin counterparts mimic these material properties and are chemical-based.
Here are the most recognizable flexible filaments:
- TPU: Thermoplastic polyurethane
- TPE: Thermoplastic elastomers
- TPC: Thermoplastic copolyester
Among the characteristics of flexible filaments, the benefits (if they’re what you’re after) include elasticity, durability, strength, and flame-retardancy, food-safety, and anti-bacterial properties. Given their long-term skin contact approval, flexible filaments are a great choice for 3D printing prosthetics and, for example, watch bands or other complements for wearable electronics. Among the different flexible filaments available, you can also find options made from 100% recycled material.
On the other hand, flexible resins are a type of UV-cured 3D printing resin that mimic the properties of rubber. They’re known for creating firm but flexible parts, and the Shore hardness of the resin when cured will determine their pliability (or stiffness). But what is Shore hardness?
Shore Hardness
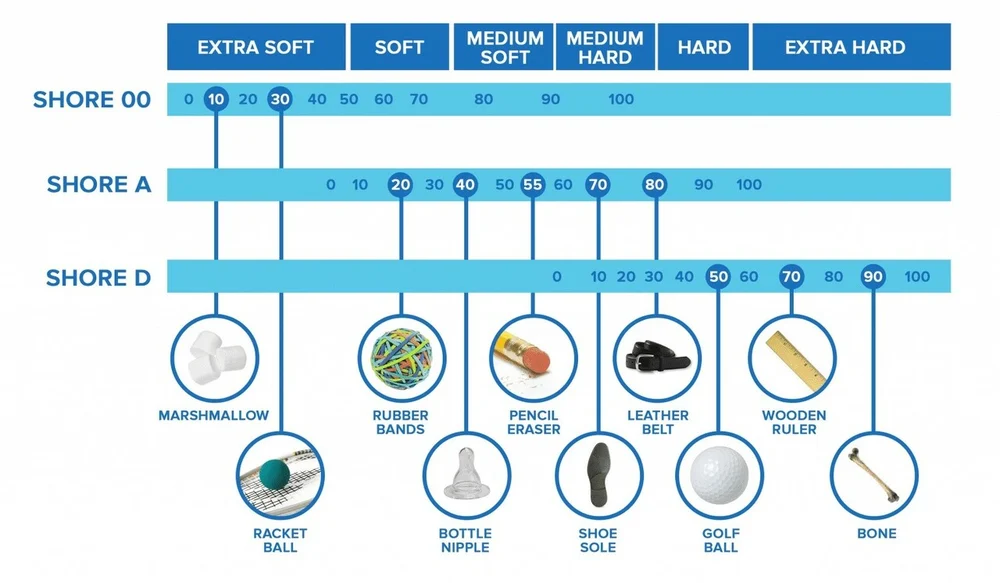
Shore hardness, also known as the Durometer scale, is a scale used to measure, well, the hardness of a material. The Durometer test is typically done on materials when a Rockwell test – a hardness test – can’t be completed due to the material being too soft.
The “Shore” level falls under three categories:
- Shore 00: Used for extremely soft materials such as gels and rubber
- Shore A: Used for flexible rubber and rigid plastics
- Shore D: Used for rigid plastics and hard rubber
For general reference, 3D printing flexible resins usually have a Shore hardness of around 80A, which, as seen above, is similar to a rubber shoe heel (harder than a shoe sole) or comparable to a leather belt.
Knowing the Shore hardness of the material you’re printing with is useful if, for example, you’re printing a mold. You’ll know that a softer material with a Shore hardness of around 30-40A will produce a flexible mold that you’ll be able to easily extract things from. If the mold is too rigid, then the removal of the part can lead to the part breaking or cracking.
FILAMENT
Printing with Flexible Filament
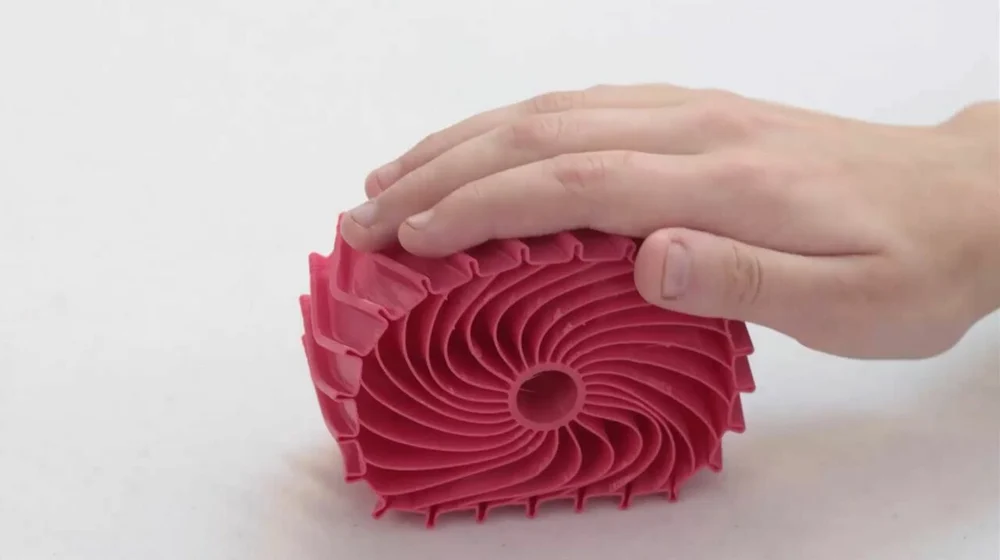
To ensure the best results, there are some things to think about when it comes to printing with flexible filaments.
To begin with, keep your filament as dry as possible. This is a given for all filaments, regardless of whether you’re using flexible filament or not. If you don’t prevent moisture from entering your material, air pockets will form within your filament and you’ll get a poorly extruded result. Proper storage and drying techniques, such as a dry box or dryer, are great ways of ensuring that a material is ready for printing.
For the printer itself, it’s best to use direct extrusion. While it’s not gospel, using direct extrusion over a Bowden feeding system for flexible filament is recommended. And to avoid issues with adhesion, opting for a glass bed may be the way to go for a successful first layer.
When it comes to the settings, a good way to go is to reduce overall retraction within your slicer settings. When printing with flexible filaments, you may find that they produce a lot of stringing or curl up around the nozzle. When it comes to TPU, a good retraction setting is about 2-4 mm. Keep in mind, if you retract too much material too quickly, it won’t have enough time to complete a full retraction due to its elasticity!
And last but not least, slow down your travel speed. To ensure a flexible material will get a good connection to your build tray, you need to print slowly. TPU can print well with a speed of 25-35 mm at a temperature of 215-222 °C.
Filament Options
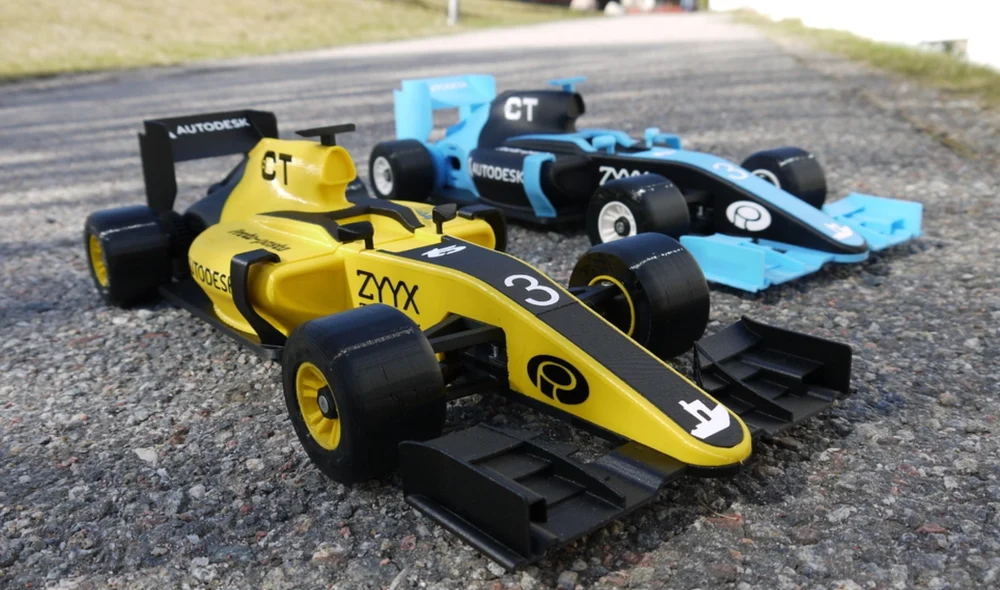
Now that we’ve gone over what to consider when printing flexible filaments, let’s take a look at three of the best options that you can buy today.
NINJATEK
NinjaFlex has a Shore hardness of 85A, yet it’s very flexible, soft, and squishy. The filament boasts that it’s chemically resistant and ideal for fasteners and protective cases due to its high toughness and abrasion-resistant properties. This makes this flexible filament an excellent candidate for an engineering and science environment where parts or components are subjected to multiple tests. It also offers an excellent amount of elongation before fracturing.
COLORFABB
ColorFabb’s nGen Flex is a flexible material suitable for tougher jobs. It has superb layer-to-layer adhesion and it also allows users to print at 40-60 mm/s, which is a major bonus for flexible materials. nGen Flex is excellent at resisting high temperatures, which makes it ideal for, for example, steam sterilization, a common technique in ortho and pharmaceutical practices. It can also be used for prosthetics, apparel, and tools.
RECREUS
Reciflex is created from 100% recycled material. Different versions come with hardnesses of 70A, 82A, and 95A. The primary reason for this filament choice is its origin, as there are few filaments available that are completely recycled.
RESIN
Printing with Flexible Resin
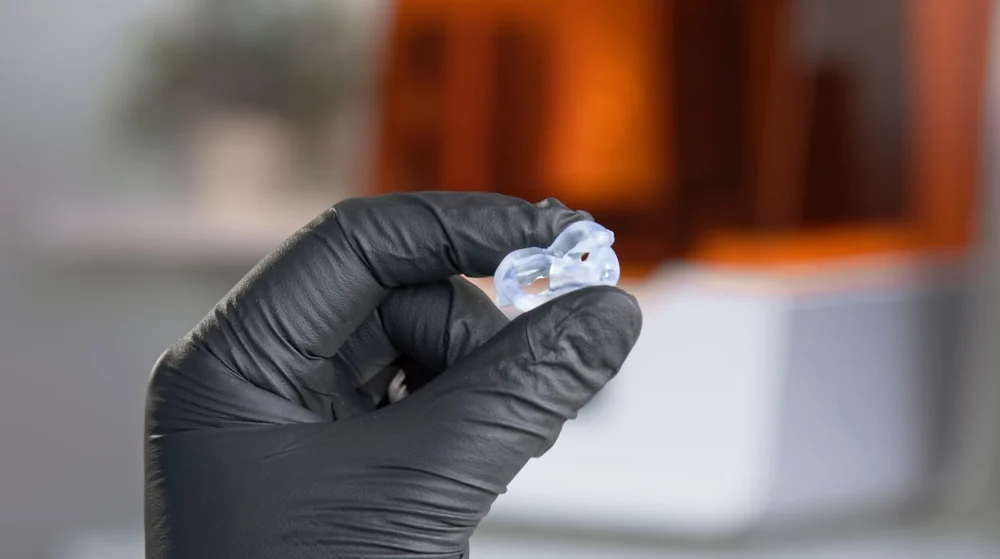
Flexible resin has elastomeric properties that allow users to print flexible and resilient parts. Depending on the size of the walls, prints may be more flexible (thin walls) or more rigid (thicker walls).
When printing on your resin machine, ensure that your build plate is level, that you have adequate ventilation, and that your work surface is covered with paper towels in case of splashes. Resin printers are also known to produce volatile organic compounds (VOCs), which can cause respiratory issues if inhaled, so a secondary enclosure or an air filter may also be worth considering.
If you’re going to print a curved item like a watchstrap, then you should design it so that it prints with that shape. Otherwise, because of the properties of flexible resin, it will “return” to a flat origin shape.
Printing your parts at a slight angle will help reduce elastic stress within your part, reducing further possibilities of distortion if you were to print your part flat on the build plate. When curing your flexible resin, it’s also recommended that you source curing settings directly from the resin supplier.
You can also print with a 50/50 mix of flexible resin and normal resin if you wish to experiment with how you can alter the rigidity of the final product.
Resin Options
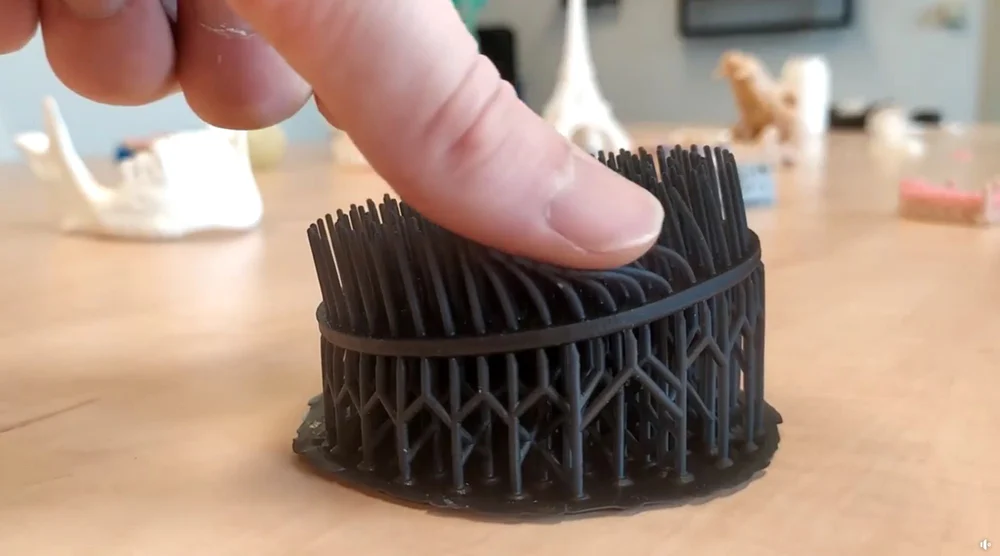
We’ve included our top picks of flexible resin below. These materials have been chosen with a mix of practical and hobby-based designs in mind.
FORMLABS
Formlabs’ Flexible 80A has a Shore hardness of (you guessed it) 80A, which is significantly harder than some, once post-processed. This makes this resin ideal for functional, everyday objects, such as gaskets and watch straps. Its hardness mixed with its durability allows for an expensive but very reliable resin.
PRUSA RESEARCH
PrimaCreator Flexible is made in-house by Prusa Research, so you know it’s made by makers! PrusaSlicer has all its resin profiles integrated, which makes setup for users that are new to resin printing significantly easier. It also means that they’ll automatically get an idea of the general settings required for resin printing. PrimaCreator Flexible, having excellent elastic properties and withstanding heavy impacts, is ideal for modeling and creating casts for jewelry and orthopedic components. It’s very easy to print with and post-process.
LIQCREATE
Liqcreate specializes in resins for SLA printing. Their Flexible X is an extremely flexible resin that offers a range of mechanical properties. The Shore hardness of 55A is softer than some, but it makes this resin ideal for general purpose hobbyists and makers. Its mechanical properties include excellent elongation and rebound properties, high durability, and good tear strength.
3D Printing Service
If you want to try out a model without investing in a whole spool of filament or bottle of resin, you can opt for a 3D printing service like FacFox.
The steps for getting your prints to your door can’t get easier than this:
- Upload your 3D model to Craftcloud via an encrypted system to ensure your files are protected.
- Select from over 60 materials with multiple colors and finishes available, and choose between the different manufacturers and quotes.
- Your parts are then printed by a manufacturer and shipped directly to your door.
As easy as one, two, three!