Pure copper is a metal material with excellent electrical and thermal conductivity, widely used in many applications such as electronic devices, thermal management systems, aerospace industry, and electric vehicles. However, this material has not been widely used in 3D printing, as it faces several major processing challenges, such as:
- High thermal conductivity, which causes rapid heat dissipation in the melt zone, large local thermal gradients, and easy to cause delamination, warping, and part failure;
- High sensitivity to oxidation, which requires special treatment for the 3D printing process, avoiding oxidation that affects the performance and surface quality of the part;
- High reflectivity, which makes it difficult to process with traditional laser-based 3D printing techniques, requiring special lasers or other types of energy sources.
To overcome these challenges, various types of 3D printing techniques have been developed and improved for the fabrication of pure copper, including:
Due to its wide potential in many application fields such as electronic devices, thermal management systems, aerospace industry, and electric vehicles, 3D printing of pure copper has been widely studied. However, this material has not been widely used as other metals, because there are several major processing challenges that need to be solved for 3D printing of pure copper.
The exploration of 3D printing techniques for pure copper is not stagnant, but has achieved substantial progress. This article summarizes the types of 3D printing techniques for pure copper.
Powder Bed Fusion 3D Printing Copper
The 3D printing technique for pure copper started with laser powder bed printing. Because pure copper has a high reflectivity to the wavelength of the mainstream SLM laser, it is not easy to melt, and may even damage the optical components of the printer. Usually, based on conventional lasers, printing pure copper requires changing the equipment structure, equipping higher-power lasers, etc. Therefore, the development of pure copper 3D printing based on traditional SLM technology is always unsatisfactory.
The real turning point is the development of green and blue lasers. Pure copper has an absorption rate of nearly 40% for 515nm green laser and 65% for 450nm blue laser, which are 8 times and 13 times that of conventional SLM infrared laser, respectively. With the development of high-power short-wavelength lasers, 3D printing of pure copper using SLM technology began to turn around.
In 2017, Fraunhofer Institute for Laser Technology announced that it was exploring the use of green lasers for 3D printing of pure copper. In the same year, Japan’s Shimadzu launched a 100w high-power blue light diode laser module and used it for 3D printing of pure copper. But for these two institutions, there is no dedicated SLM equipment available yet. Fraunhofer said that it will create a reliable high-quality laser for single-mode operation in the future, stably outputting a maximum power of 400w of 515nm band laser.
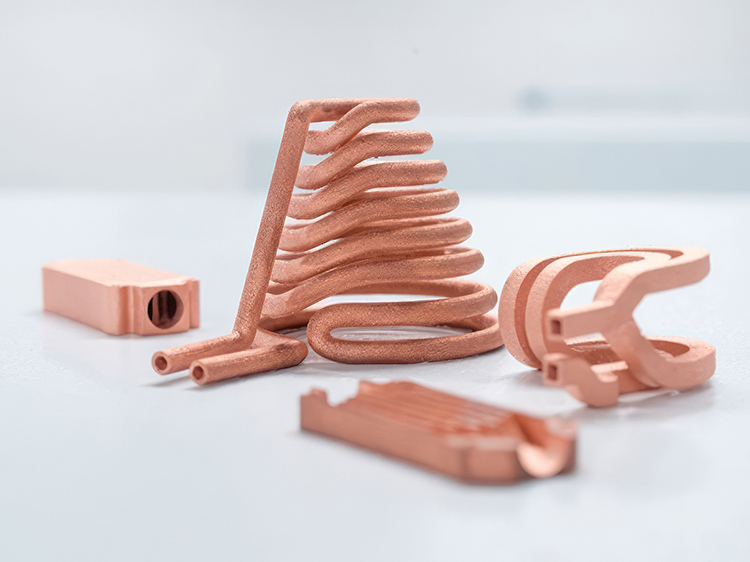
The real commercialization was in 2018, when Trumpf launched the first green laser SLM printer. The device is equipped with a 515nm TruDisk1020 green light laser, which prints parts with a copper content of more than 99.9%, achieving 100% IACS electrical conductivity and 99.9% density.
In addition to laser powder bed fusion technology, electron beam also has advantages for 3D printing of pure copper, but the surface quality of the parts printed by this process is not good, which brings inconvenience to the post-processing of applications such as copper induction coils.
Binder Jetting 3D Printing Copper
In theory, materials that can be used for metal injection molding can be formed by binder jetting. However, the representative company of this technology, Exone, has only launched official certified materials such as 17-4PH, 304L, 316L, M2 tool steel, etc. for a long time, and pure copper has never appeared in the material list of the same technology type company.
In fact, before using the binder jetting technique to form pure copper, some scholars have used SLS technology to study the mixture of copper and PMMA powder. PMMA acts as an intermediate binder, melting to bond copper powder to form a green body during laser scanning, and then debinding and sintering. This method is similar to the binder jetting technique, both of which form the shape of the part from copper powder, but the method is different. The researchers found that in this indirect SLM process, the density of pure copper was much lower than the theoretical density (about 77-78%), there were many pores, and the impurities produced by the debinding process were left in the material.
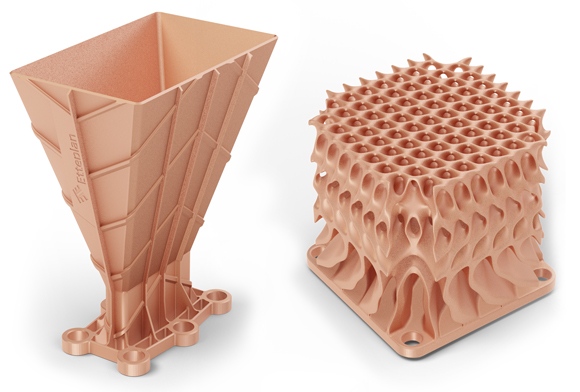
Whether it is metal injection molding, binder jetting or laser sintering, the reasonable powder particle size distribution, binder selection and debinding process control are all key factors for the formation of pure copper. Compared with laser sintering, binder jetting technology is easier to control the content of the binder, which avoids the fixed ratio problem caused by the one-time mixing of copper powder and binder in the former, and is more flexible in the process adjustment and research process.
Previously, foreign researchers have used Exone’s equipment to conduct research on pure copper materials, but the density and other properties of the prepared materials are not high, and they need to undergo hot isostatic pressing to achieve densification (and only when the sintering density exceeds 90% is necessary); at the same time, it was also found that the powder particle size distribution, ink composition, etc. are all key factors affecting the performance of the parts. Digital Metal launched pure copper 3D printing materials, becoming the first equipment manufacturer to provide official certification of pure copper materials and processes for binder jetting 3D printing systems. According to the data released by the company, the density of pure copper formed by binder jetting technology is 96.6%, and the copper purity is 99.9%, but it is not known whether the company’s post-processing process also includes hot isostatic pressing.
Fused Deposition Modeling (FDM) 3D Printing Copper
In February 2020, Markforged announced the launch of pure copper 3D printing filaments and processes, and successfully applied them to heat sinks and automotive manufacturing. In December 2020, Desktop Metal launched pure copper materials and processes based on its Studio desktop 3D printing system.
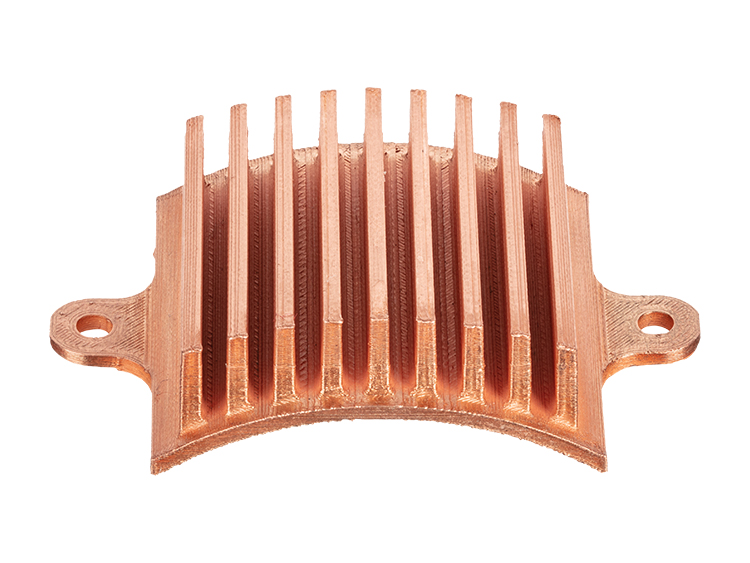
Like binder jetting technology, metal 3D printing based on fused deposition modeling also requires debinding and sintering. Desktop Metal claims that the newly launched pure copper material can achieve a density of 98%, and can produce parts with complex geometries and internal channels. With its Fabricate software, it can automatically execute complex metallurgical processes, thereby producing high-quality parts with similar density and feature accuracy to casting.
Digital Light Processing (DLP) for 3D Printing Copper
In March 2021, the US company Holo announced the launch of pure copper 3D printing materials based on DLP technology. Using the company’s proprietary PureForm technology, it uses a high-resolution optical imager to 3D print a slurry made of pure copper powder and photosensitive resin, and combines the mature metal injection molding (MIM) backend process to debind and sinter the printed green body, and finally produce high-performance parts.
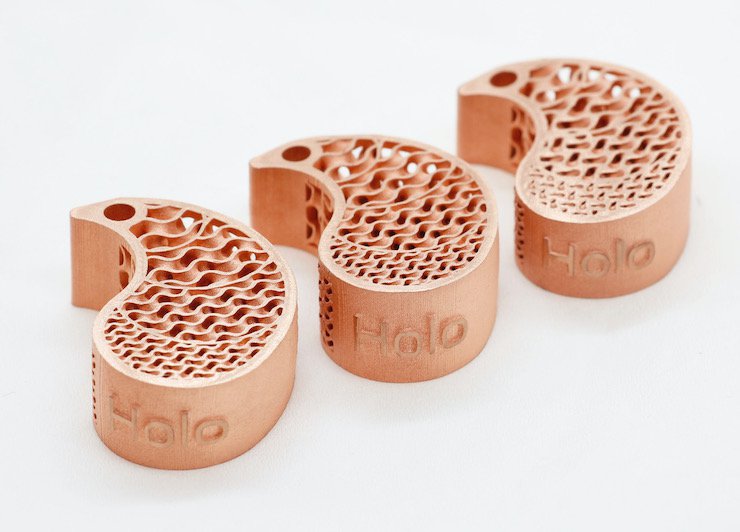
Holo’s slurry has excellent dispersion, and can form uniform layer thickness during the printing process. The printer can solidify a new layer in less than 10s. Currently, the density of pure copper formed by Holo using DLP+debinding and sintering process is 96-98%, which is enough to reach 95% of the thermal conductivity and electrical conductivity of bulk copper. In addition, this process may also reduce the cracking problem caused by laser printing.
Based on the mature process, Holo focuses on the development and manufacturing of heat dissipation devices, rather than selling 3D printers. Its current trial production line can produce 20,000 pure copper small parts per month, and hopes to produce millions of copper heat sink parts per year.
END
In today’s rapid development of electronic components, heat loss and heat safety issues are increasingly prominent. Designing compact, efficient, and integrated heat sinks has important application space, and these characteristics are the biggest advantages of 3D printing compared to traditional processing techniques.
In addition to thermal management systems and heat exchange devices, pure copper 3D printing can also be used for radio frequency cathodes and induction heating coils. For uncomplicated devices, pure copper 3D printing may not be particularly necessary, and its role lies in product development, special structure manufacturing, etc.
Currently, there are actually other types of pure copper 3D printing techniques, but most of them are limited to a few companies that have made breakthroughs, and there is still a lot of room for development, which is closely related to the research and development of lasers, materials and post-processing techniques.
If you are interested in 3D printing pure copper, you may want to check out FacFox’s pure copper 3D printing services. FacFox is a leading online 3D printing platform that offers various types of 3D printing techniques and materials, including pure copper. FacFox can help you design, print, and deliver your pure copper parts with high quality and efficiency. Whether you need a prototype, a small batch, or a large-scale production, FacFox can meet your needs and expectations. Contact our engineers via info@facfox.com today!