The Renzo Piano Building Workshop (RPBW) was established in 1981 by Renzo Piano with offices in Genoa, Italy, and Paris, France. RPBW is led by 9 partners, including founder and Pritzker Prize laureate, architect Renzo Piano.
The practice permanently employs about 110 architects together with a further 30 support staff including 3D visualization artists, model makers, archivers, administrative, and secretarial staff.
RPBW has a wide experience of working in multi-disciplinary teams on building projects in France, Italy, and abroad. They have successfully completed over 140 projects around the world.
As architects, the teams are involved in the projects from start to finish. They usually provide full architectural design services and consultancy services during the construction phase. Their design skills extend beyond mere architectural services—their work also includes interior design services, town planning and urban, landscape and exhibition design services.
Read on to learn from Francesco Terranova and Dimitri Lange, model makers in RPBW’s Genoa office, how they create complex architectural models using a combination of traditional tools and digital technologies like 3D printing.
Design to Build
The emphasis at RPBW is on “design to build”, to ensure from the start that every detail works and will represent the final building right down to the tiniest detail. For each project, hundreds of large and small-scale models are made in RPBW’s workshops to test different proposals.
These scale models are an essential part of the architects’ workflow. They often meet around the models of new projects to discuss different ideas for parts of the design.
“Sometimes, the difference is very, very little. For example, an edge is smoother than the one before. At the scale we work, I don’t even know how they can see it,” said Mr. Terranova, smiling.
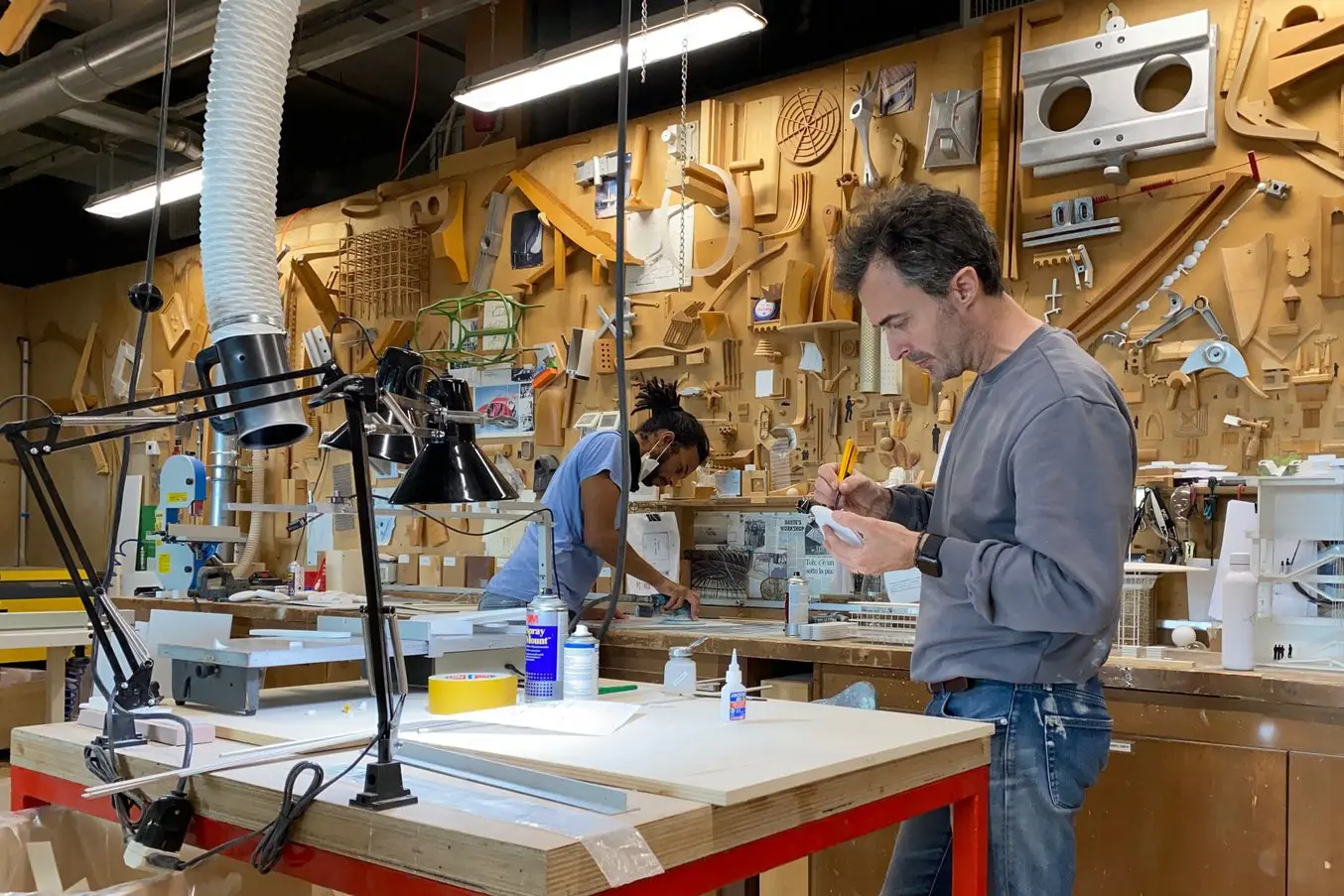
Often, the architects make changes to the models directly, which they can later reproduce in CAD. Every few weeks, clients also come to the practice for an update on the projects, where the models play a crucial role helping to make updates tangible.
“Our models change every day, or even every hour. Because the architects change the project very quickly, most of the time, we don’t have enough time to do it by hand. Therefore, we have to find a way to do it quicker,” said Mr. Terranova.
How Scale Models Are Made
“We normally start printing the model in scale on paper to understand the real size of the model. If we have a model that is 1 meter by 1 meter, we have to understand how to divide it because often, if the model is too bulky to be moved or transported, we must consider building it already divided into two or more pieces, to be reassembled once it reaches its destination,” said Mr. Terranova.
The model makers use a combination of traditional tools for hand-making models as well as digital tools like 3D printers, CNC milling machines, and laser cutters to create various parts.
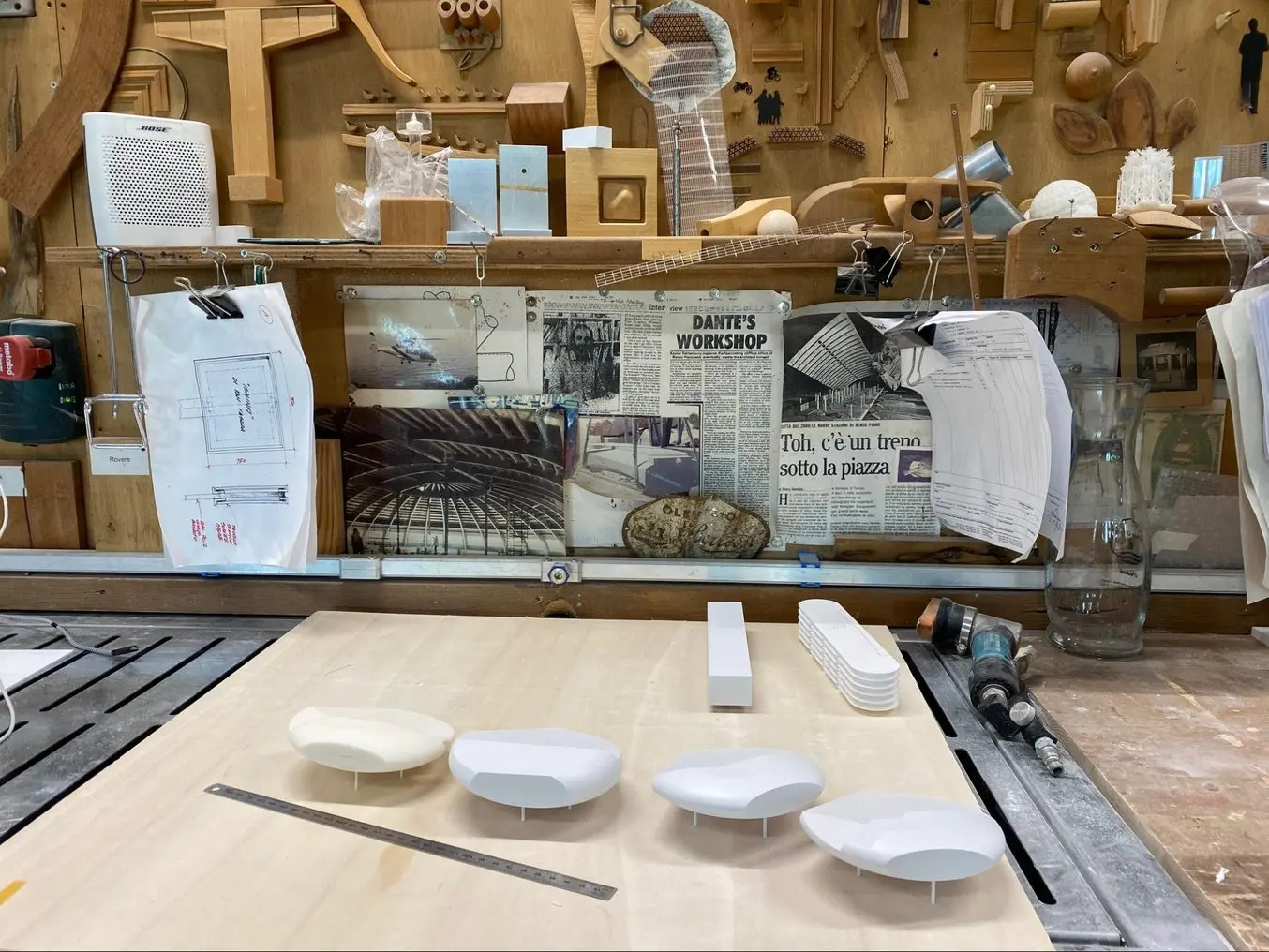
“Most of the time, a model is made using all these technologies together. For example, for the base of the model, often it’s better and less expensive to use the CNC machine and hard materials. Some buildings are CNC milled and laser-cut,” said Mr. Terranova.
The model makers also use 3D printing for intricate parts like stairs and trees, which would be time-consuming to manufacture by hand. For example, they 3D printed the complex joints of the columns for the model of the new San-Giorgio motorway bridge in Genoa that has recently replaced the Morandi bridge that collapsed two years ago.
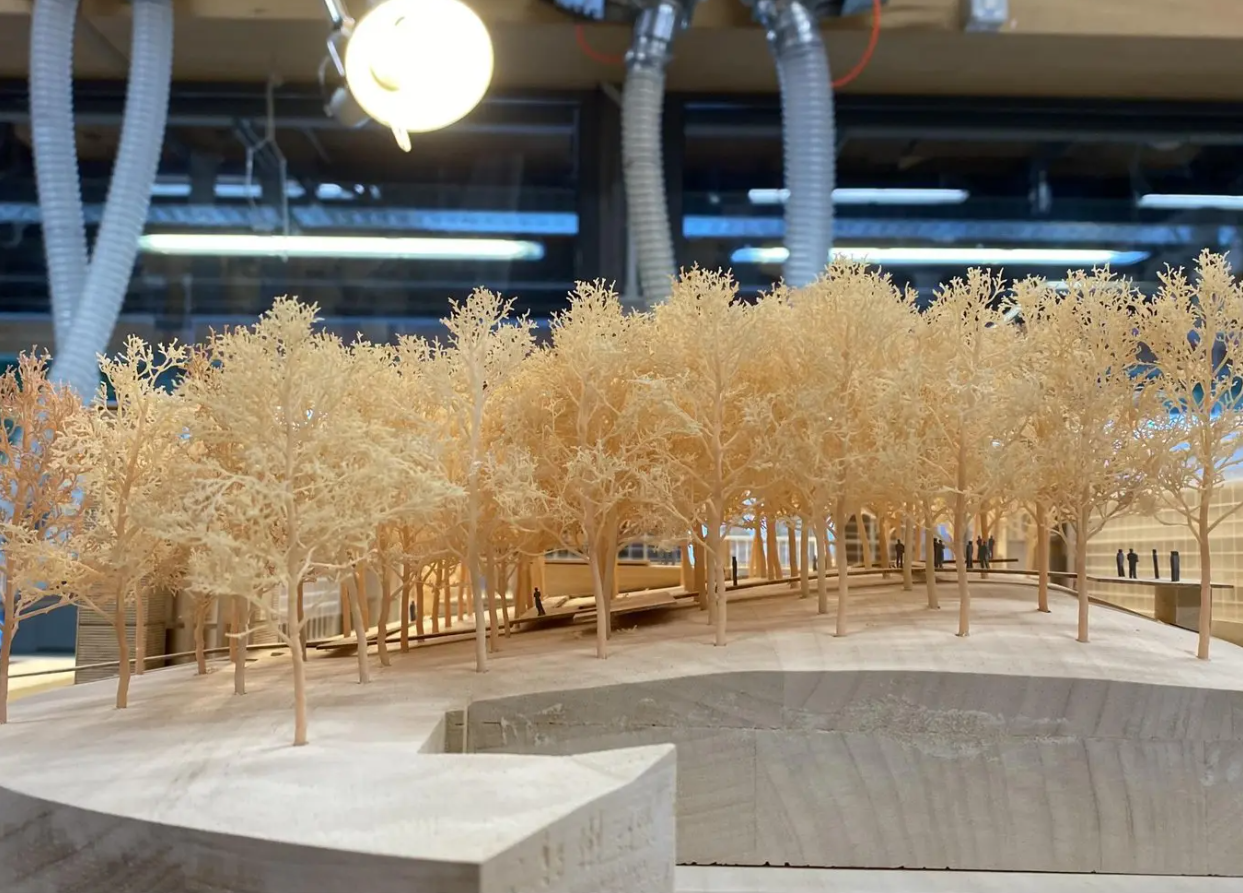
While the architects use Autodesk Revit CAD software to create digital files, these cannot always be used to create the physical scale models directly.
“What they export is not ready for us. The buildings are complete with everything; pipes, taps, furniture, etc. We don’t need these details on a model scale. So we have to clean the file and we also have to consider the thicknesses that we can use. For example, a wall that is 10 cm thick, on a 1 to 200 scale, becomes 0.2 mm. That doesn’t work on machines, so we have to manage the files and adapt the 3D model,” said Mr. Terranova.
Digital files for 3D printers also need to have a closed volume surface. Some designs can be corrected automatically, but often the model builders have to redraw the entire model.
Choosing the Right 3D Printing Technology
The model building studio in Genoa got its first 3D printer six years ago. Since then, they’ve expanded their fleet to three machines, using three different technologies, and they have also tried many more.
“Six years ago, we started with a powder-based machine [that uses binder jetting technology]. It was not very useful because it was very sensitive to the humidity and the precision was not what we needed. So, we moved to the Form 2, [which uses stereolithography (SLA) 3D printing technology]. Then, we added a 3D Systems [large-format material jetting printer] that prints with the resin. And we also have a small FDM 3D printer that works with PLA and ABS,” said Mr. Terranova.
“What we appreciate very much with the Formlabs machines is the solidity and the strength of the material, and also the precision of the models. Formlabs resins, once printed, are very easy to sand. That is a very good thing because we always need to paint the model. Even if we use White Resin, the white is not exactly the same white that we use with our models. We actually have to paint the model made with 3D printers and also the rest of the model made with the CNC machines and other tools. So it’s very useful that we can sand it easily,” said Mr. Terranova.
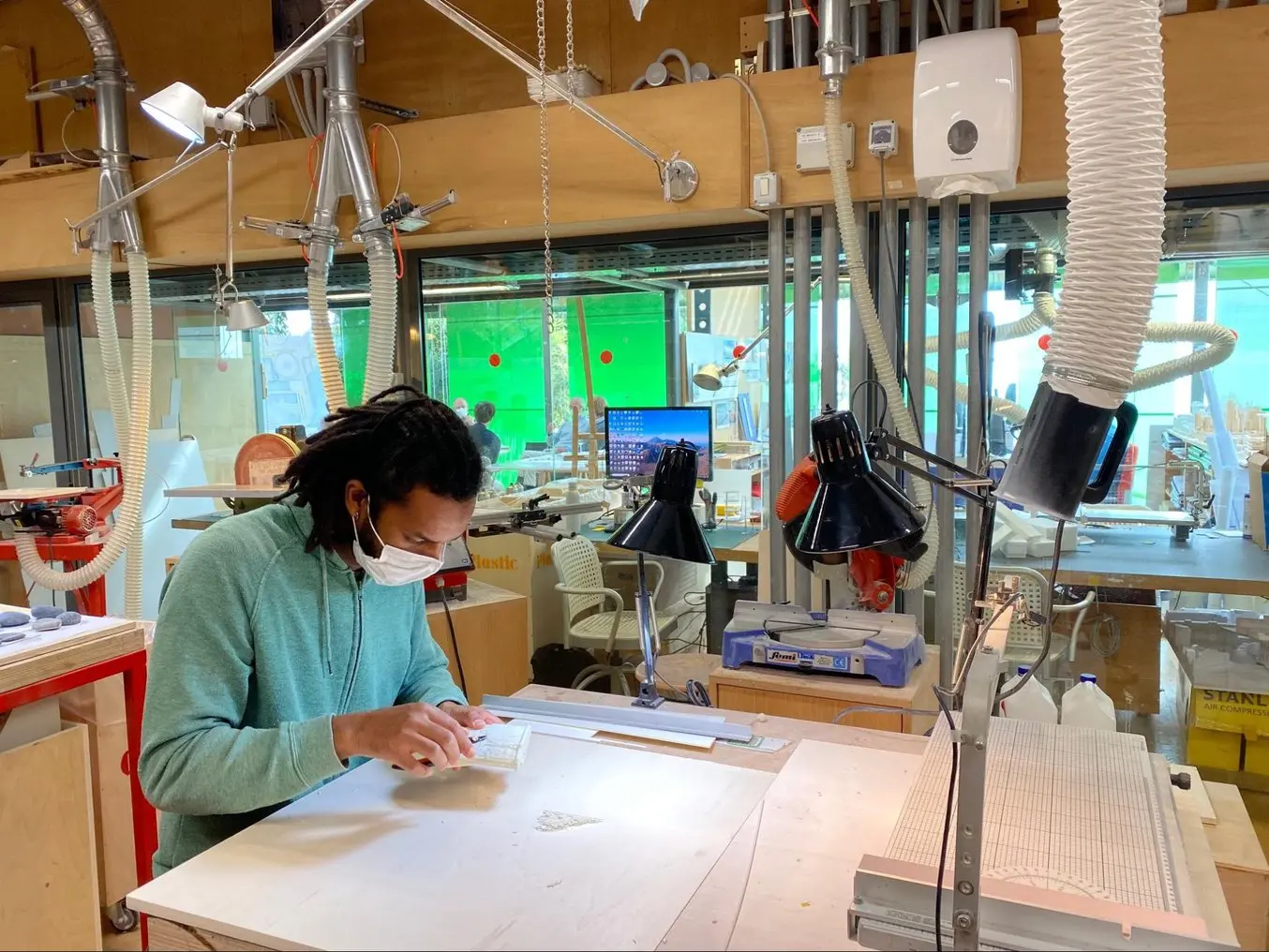
“With the FDM 3D printer, we don’t have absolutely the same accuracy. We see all the layer lines, and for us, it is not a good result. The 3D Systems printer is very accurate and for large-scale architectural detail models (1: 5, 1:10), it is useful. But the material is not so solid after you clean it. For example, if we 3D print trees with that machine, after half a day or less, the trees fall down. They seem to melt,” said Mr. Terranova.
Most recently, the studio also upgraded their Form 2 to Formlabs’ newest Form 3 SLA printer, which has allowed them to print some of the most complex models, while also saving time on post-processing.
“The trees were a big problem because they are very fragile, very thin. We tried to do it with the Form 2 [and the other printers, but they’d break]. With the Form 3, we don’t have the same problem and it allows us to 3D print trees. Removing supports with the Form 3 also seems to be easier, because we can use smaller supports,” said Mr. Terranova.
The Future Of Model Making
The Genoa studio recently moved their Form 2 to the New York office, so now all three RPBW offices use 3D printers for model making. Mr. Terranova and Mr. Lange hope that the use of digital tools will also encourage knowledge sharing between the offices.
Mr. Terranova also believes that in the future 3D printers will be essential tools in most architectural workshops and practices.
“I think it’s the future, for sure. Some changes have to be done before, to allow every model maker to use this technology. For example, the price has to go down. But [Formlabs] already did this step,” said Mr. Terranova.
Source: https://formlabs.com/blog/renzo-piano-architectural-models-3d-printing/