North American vehicle manufacturer General Motors has teamed up with award winning software company Autodesk in the development of its future product designs. Combining 3D printing with generative design, the company’s approach to vehicle development is “completely transformed,” says Ken Kelzer, VP of Global Vehicle Components and Subsystems at GM.
Through paring these technologies the design process becomes “fundamentally different to co-create with the computer in ways we simply couldn’t have imagined before.”
Trends in generative design
Generative design brings a natural element to the traditional means of 3D modeling. Instead of stock shapes, or sculpted geometries, the process works using a set of parameters that essentially allow a design to “grow” thousands, or millions, of potential parts.
The automated process enables the creation geometries at odds with conventional shape, and 3D printing, a method that allows the fabrication of previously “impossible” objects, is its perfect partner.

New York based advanced CAD developer nTopology is a well known name in generative design. 2018 3D Printing Industry Awards nominee Frustum Inc. is a startup that has developed a generative design platform specially for additive manufacturing, and at SOLIDWORKS World event in LA Desktop Metal previewed its Live Parts platform making use of the technology.
“Generative design is the future of manufacturing, and GM is a pioneer in using it to lightweight their future vehicles,” comments Scott Reese, Autodesk Senior Vice President for Manufacturing and Construction Products. “Generative technologies fundamentally change how engineering work is done because the manufacturing process is built into design options from the start.”
In the automotive world, computer design startup Hackrod is also working with Autodesk generative design to create custom hotrods.
The upper hand on part design
As identified by Reese, a helping-hand for light weighting is one the advantages of adopting generative design over other more conventional design methods. GM is committed to reducing the mass of vehicles, through generative design and otherwise, to optimize interior space for drivers/passengers, and improve car performance.
From 2016 – 2018 GM has released 14 vehicle models with an average mass reduction of more than 350 pounds per vehicle. One example is the 2019 Chevrolet Silverado, which has had mass reduced by up to 450-pounds.
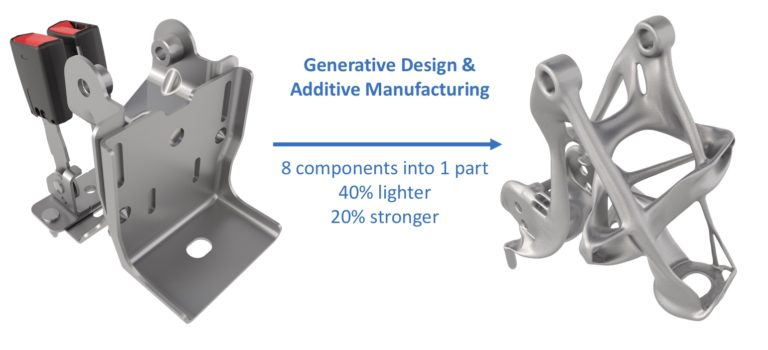
In addition to lightweighting, Reese says, “GM engineers will be able to explore hundreds of ready-to-be-manufactured, high-performance design options faster than they were able to validate a single design the old way.”