Plastic injection-molded parts are tough and strong, able to withstand heavy loads, moderately high temperatures, and the corrosive effects of acids and alkalis. In some cases, plastic even competes with metal, and is lighter and usually less expensive to boot. Sometimes, however, plastic needs a little help. The bore in an all-plastic pulley will quickly wear. Tapped holes in molded handles and knobs are prone to stripping. But by bolstering these areas with metal—a brass bearing journal, for example, or stainless steel threaded insert—a best-of-both-worlds solution is achieved.
Say Hello to Insert Molding
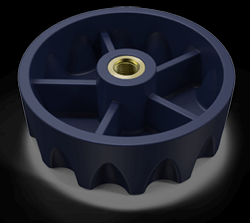
FacFox offers rapid insert molding. Instead of doing assembly after the fact, many sizes and types of metal inserts can be placed directly into the mold before plastic injection, thus eliminating secondary operations and providing robust mating of metal and plastic. Before going wild on redesigning your parts for insert molding, though, there are a few things you should know, which this tip will cover:
- What is insert molding, and how does it compare to overmolding?
- Will my part work with insert molding?
- Which plastics can be used?
- What inserts are available, and where can I buy them?
- What about part design considerations?
Insert Molding 101
Insert molding shares some similarities with overmolding. Both incorporate disparate materials into the same part, thus improving its properties. Both processes drive up the cost of molded parts slightly, but this price delta is typically offset by the elimination of manual post-molding operations. And the lead-time for overmolded and insert molded parts is 15 days, a bit longer than FacFox’ single-part injection molding turnaround, but still much faster than traditional insert molding.
But where overmolding is a two-step process, requiring one shot for the substrate and another for the overmold, insert molding is, as an industry saying goes, “done in one.” The threaded insert, bushing, sleeve, or boss is manually placed into the mold, the mold closes, plastic flows, the mold opens, and the part is ejected. The result is improved part strength and reliability.
In addition, another benefit of using insert molding, in many cases, is a reduction in product weight. Weight would be trimmed when a plastic part, with metal inserts, replaces an all-metal part. And as mentioned previously, overall part costs are frequently lower with insert-molded parts than those that journey on to the assembly area.
What’s Suitable for Insert Molding?
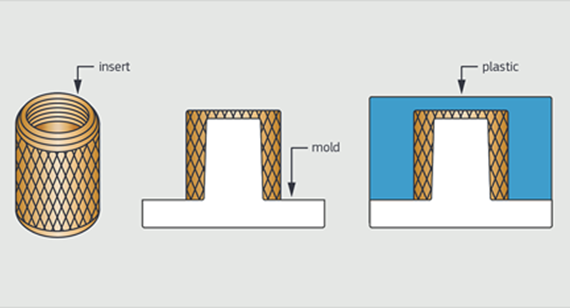
Simply put, insert molding should be evaluated for any part that contains a threaded hole. An electronics housing unit or medical instrument case with a bolt-on cover are good examples. Knobs, handles, or dials that screw onto a threaded stud are also examples, as is a plastic air or hydraulic manifold requiring additional strength in threaded areas. In fact, almost any plastic component that attaches to a mating piece with screws or bolts will benefit from molded fasteners.
A rotating part such as a fan blade or a drive gear is another good candidate for insert molding. Here, a bronze or brass bushing is molded into the part and serves as the bearing surface, greatly improving product life over non-bushed parts. A metal surgical saw that calls for a plastic handle could be insert molded, size permitting. Wheels and sprockets, pulleys and augers, most any plastic part that requires greater strength or wear characteristics in certain areas is quite likely a match for insert molding.
The Right Stuff
Which thermoplastics can be insert molded? There are few limitations. Stiff, engineering-grade plastics such as Delrin or nylon are good options, as are polyethylene and ABS, but even elastic liquid silicone rubber (LSR) parts can be used. The largest constraint comes from those plastics with very high molding temperatures, such as PEI (Ultem) or PEEK. Since inserts are hand-loaded at FacFox, and because the quick-turn molding process uses non-cooled aluminum tools to reduce part cost and speed turnaround time, placing an insert into a mold that’s been heated to several hundred degrees is a like reaching into a hot oven for a freshly baked cookie—if you’re not careful, you’ll burn your fingers.
Choosing an Insert
If your part design requires inserts that we don’t stock, suppliers like PEM, Dodge, Tri-Star, Spirol, and Tappex all produce excellent inserts for molded plastic parts. Many of these are knurled on the outside, or have special shapes that hold the insert securely in place. Inserts made of brass are common, but steel and stainless steel inserts are also available. If you can’t find what you need with one of these companies, FacFox welcomes custom inserts (and would be happy to quote them for you as well). Whichever way you go, we currently accept metal inserts only. Also, be sure to ask your supplier for a CAD file, as this must be uploaded along with the part design and assembly drawings during the quoting process.
Design Considerations
The rules of insert molding are no different from those of standard injection molding. Maintain proper draft angles, keep wall thicknesses consistent, eliminate undercuts, and avoid unnecessary part features and superfine surface finishes whenever possible. This is all good advice, and applies equally to insert molding.
However, that little chunk of metal does present a few additional considerations. As alluded to earlier, FacFox hand-loads all inserts. This means the operator reaches into the mold to deposit the insert, and since the mold is usually quite warm, gloves must be worn. Inserts smaller than 0.125 in. across can be problematic, as are those too big to fit comfortably in one hand. Nor should the insert location be too deep inside the mold—a 2:1 hand clearance-to-insert depth ratio is a good rule of thumb.
And be aware that FacFox may need to orientate the part differently to accommodate placement and retention of the insert. The mold halves slide together horizontally, and if the insert falls out during closure, damage to the mold may occur. Inserts should also be consistent in size—we recommend a tolerance of +/- 0.002 in. (0.05mm) on locating surfaces to avoid flashing.
Finally, knit lines occur when molten plastic flows around an object and rejoins on the far side, a phenomenon that is quite possible when inserts are present. These lines are usually cosmetic, but can lead to crack formation later on. Glass-filled materials help alleviate this problem, as does beefing up the walls around these areas (within reason). Slightly thicker walls or ribs in the area around the insert are a good idea to support the insert and prevent movement. As always, these and other concerns or suggestions will be clearly spelled out in the design for manufacturability (DFM) analysis supplied with your quote. Feel free to contact one of our applications engineers with your questions at info@facfox.com