By laser processing bending cut geometries or ‘kerf cut’, sheet materials that are rigid such as acrylic and wood can be bent. We have tested a wide variety of different materials including acrylic and wood from 3-5 mm, and have provided the appropriate graphic templates for download for you on a select few.
Different cutting techniques you can process
Click to download files of all the patterns here: Kerf-cut
Kerf 1: Straight cut lines
Cutting straight lines will form a solid radius and the further apart that each cutting line is, the greater the bending radius will be. Depending on your specific material and graphic, a distance up to 0.5 mm between the lines can be processed.

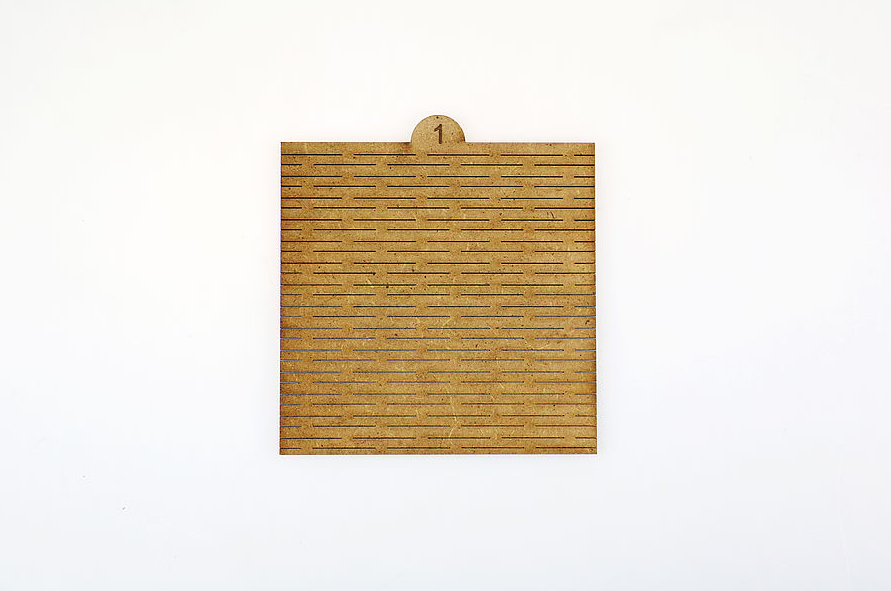
Kerf 2: Small waves
Cutting small interconnected waves will give the material a large bending radius and flexible appearance. This technique is best suited for materials that are up to 3 mm thick.
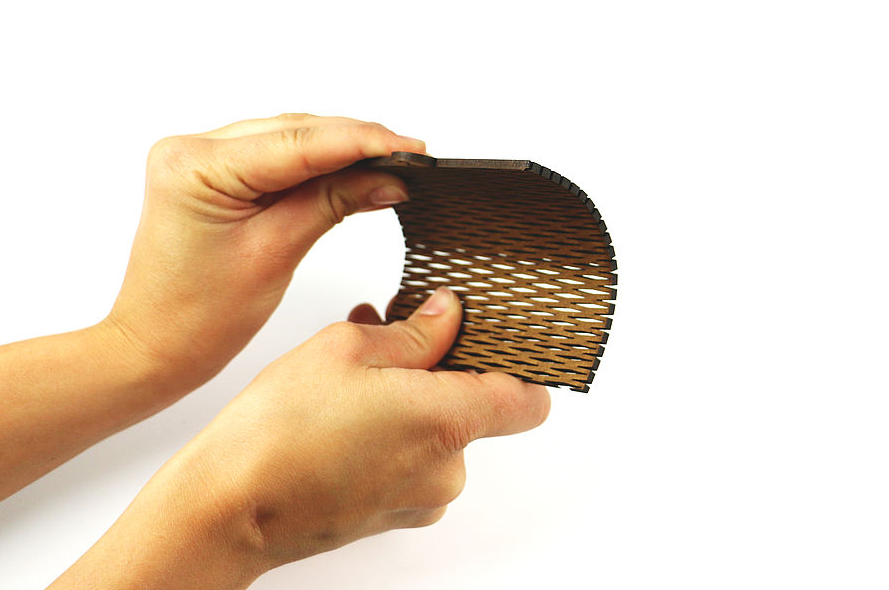
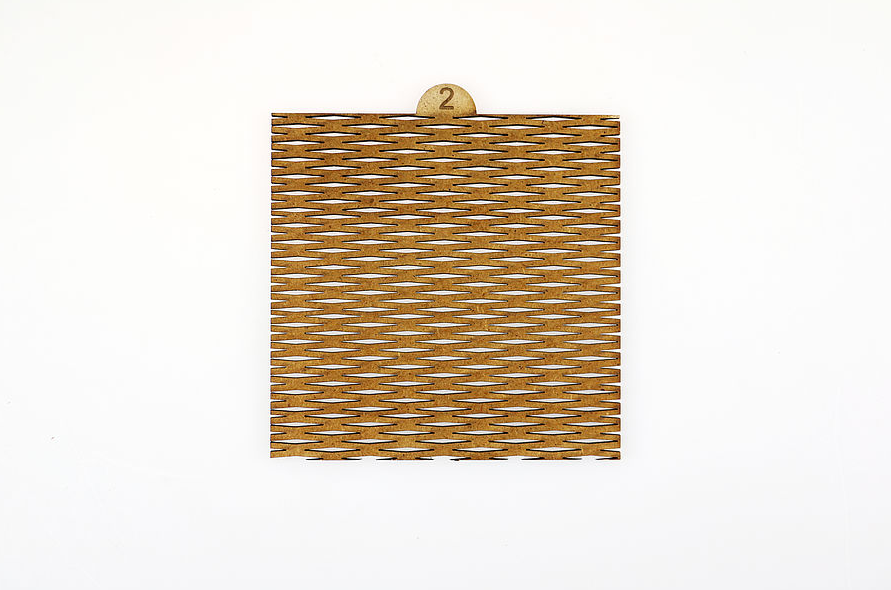
Kerf 3: Large honeycombs
With large honeycombs, the curves are cut out of the sheet and tapered at each end. Because of the large honeycomb, wooden boards can be used with flexibility up to about 5 mm thick. This pattern is most commonly used in model making.
The honeycombs can be easily taken apart as well as put together, and can also be combined with connections, such as with bracelets for example.
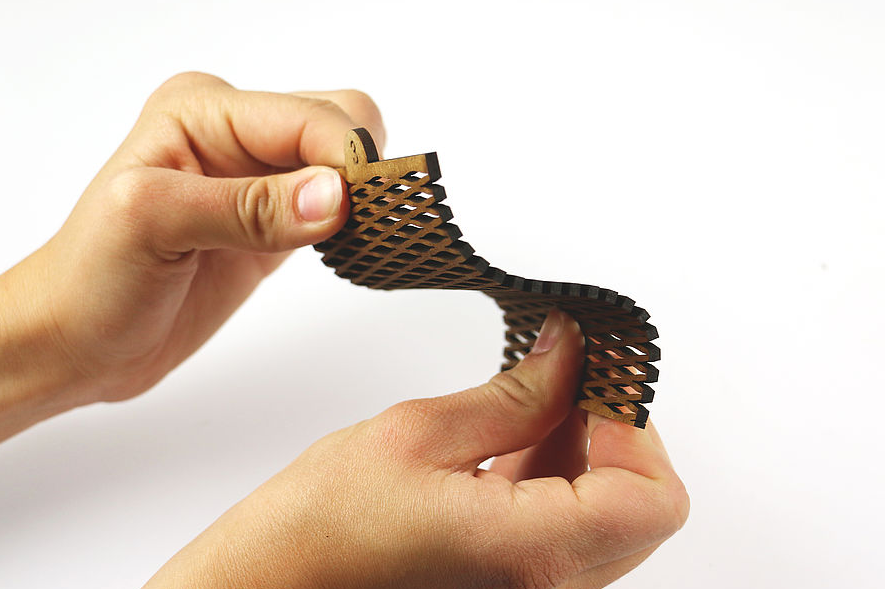
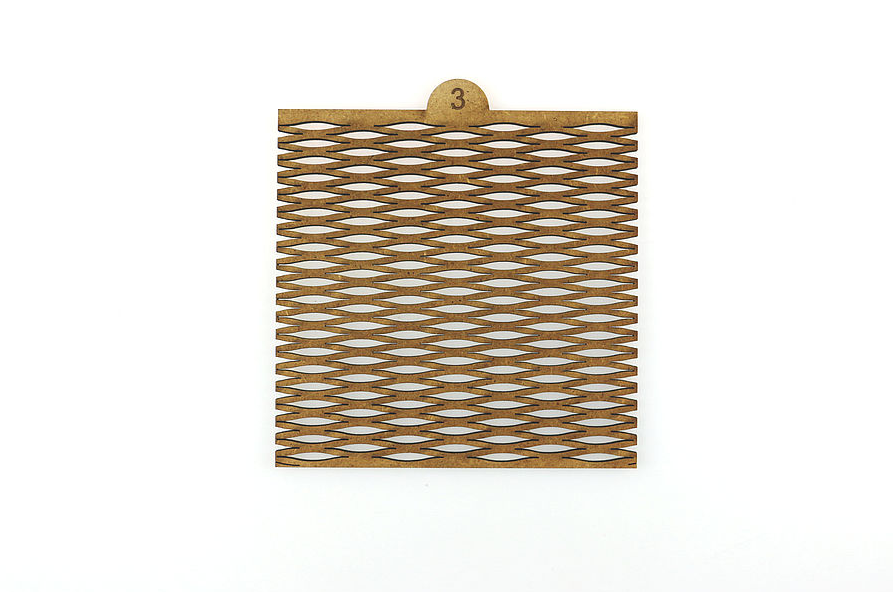
Kerf 4: Wavy cut line
Similar to pattern 1, this laser cut pattern consists entirely of cut lines, but offers different bending properties as it is much more flexible.
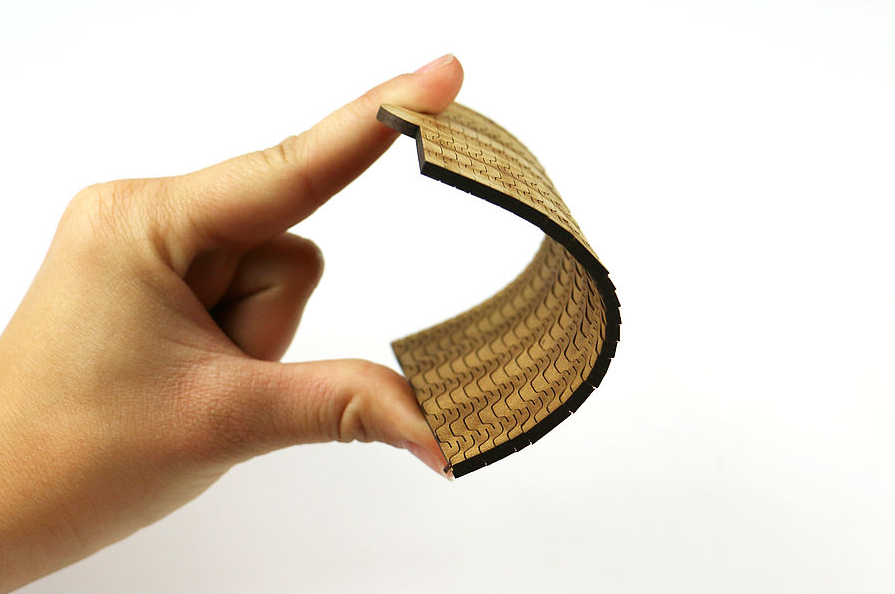
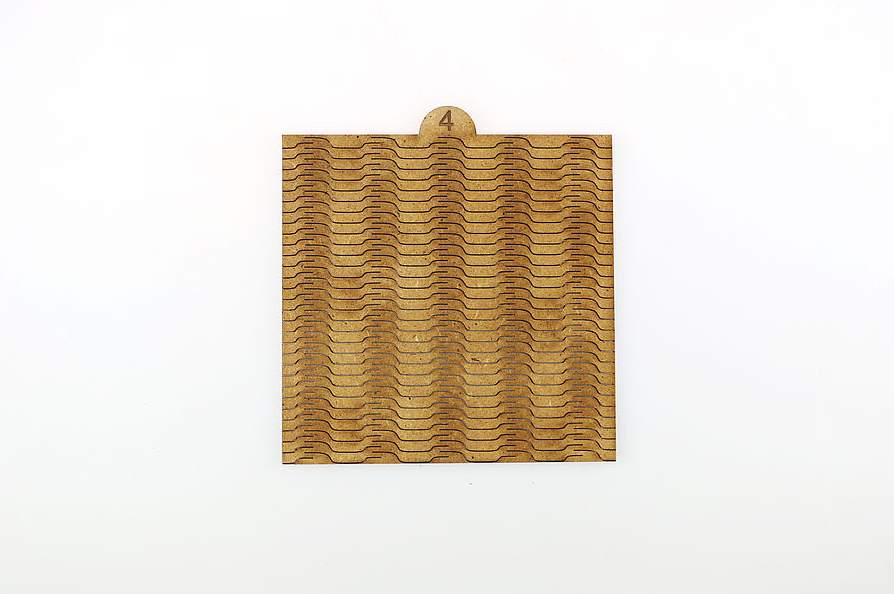
Kerf 5: Honeycombed cut line
The uniquely formed pattern of this bending cut offers flexibility in all directions, which makes a variety of creative applications possible, such as in bag design for example.
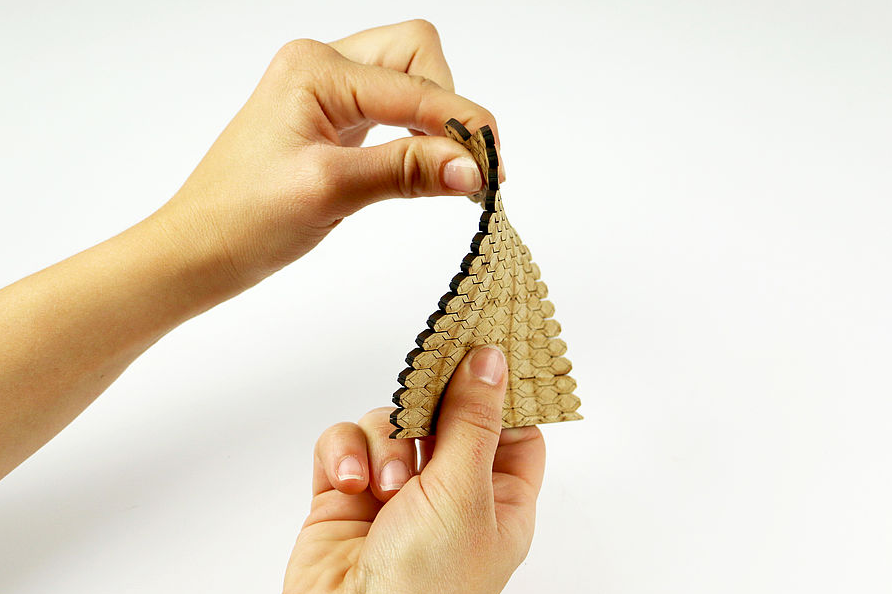
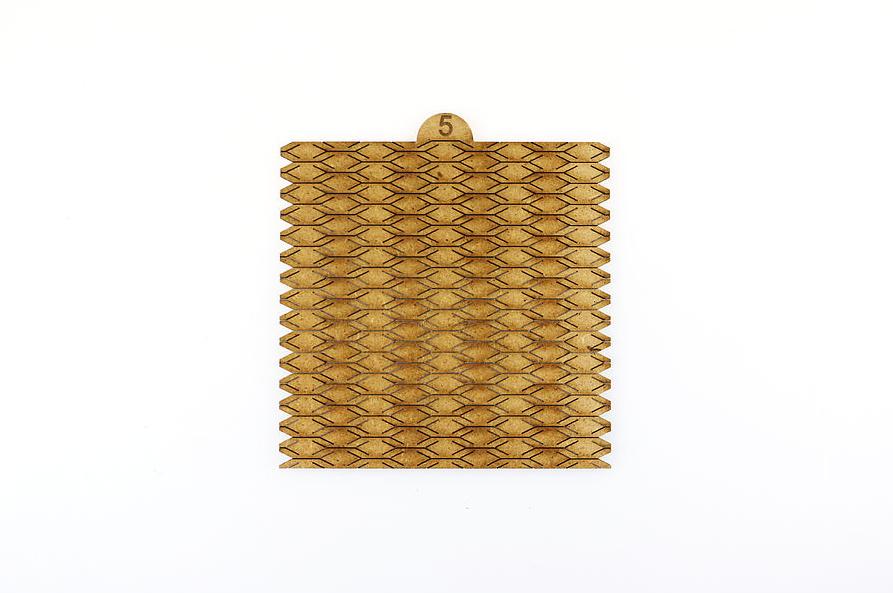
Kerf 6 and 7: Wide and narrow waves
These cuts are versatile and work well with several different types of materials. The shape given to the individual cut lines allow for flexibility and stability.
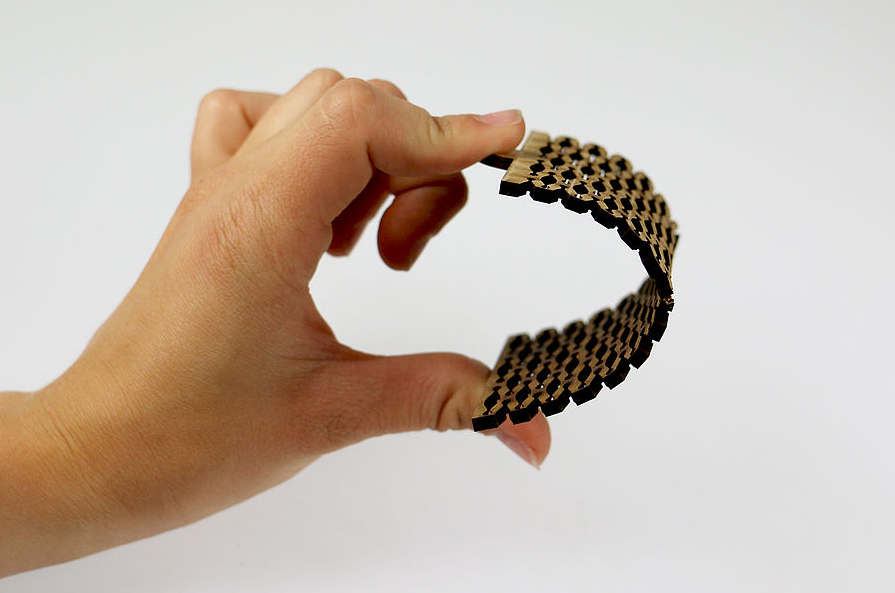
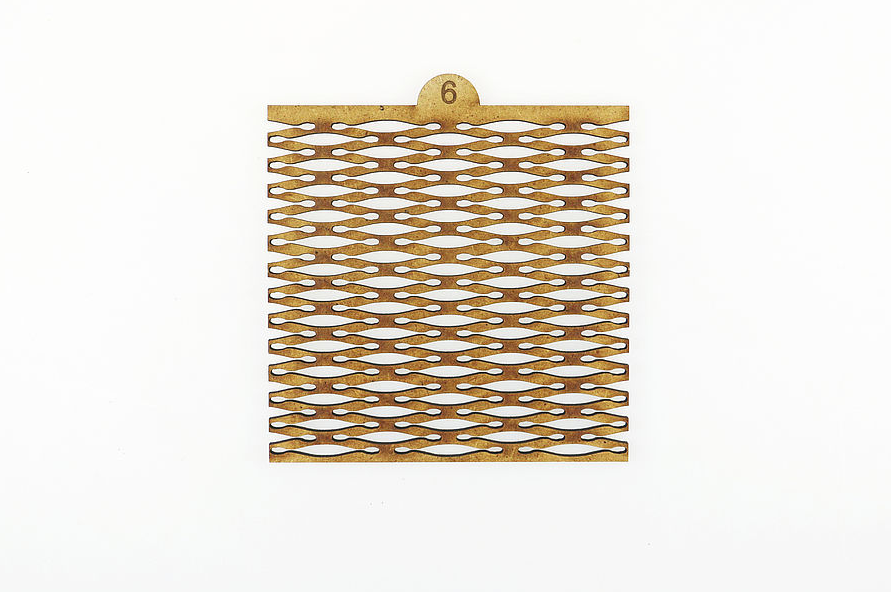
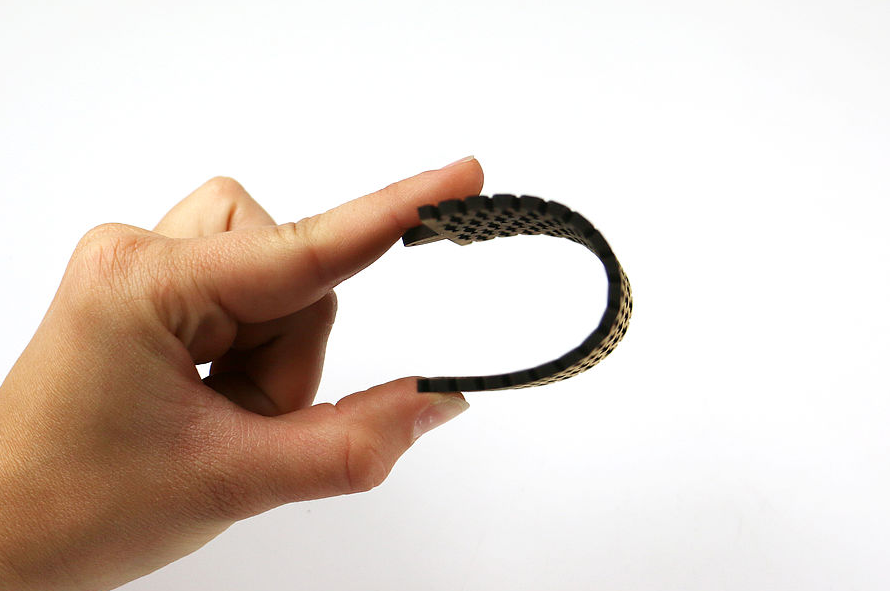
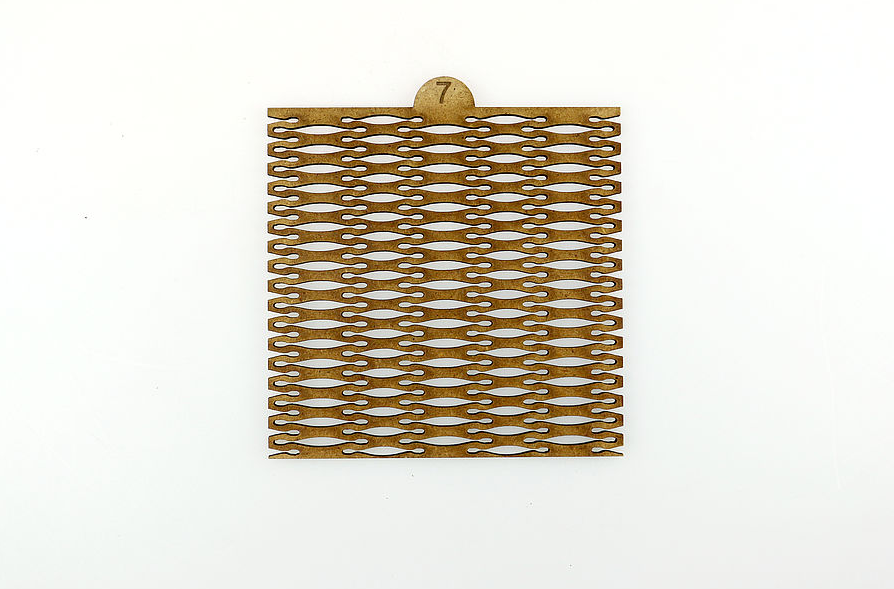
Kerf 8: Triangular shape
Due to its design, this cutting pattern is most commonly used as a graphic element and can be bent in all directions.
The triangular shape of this cutting technique is well suited for materials up to around 3 mm of thickness, and becomes inflexible and rigid after 5 mm or more.
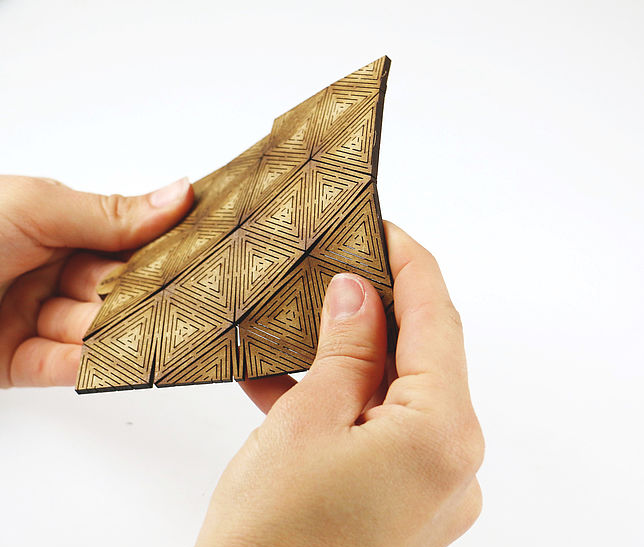
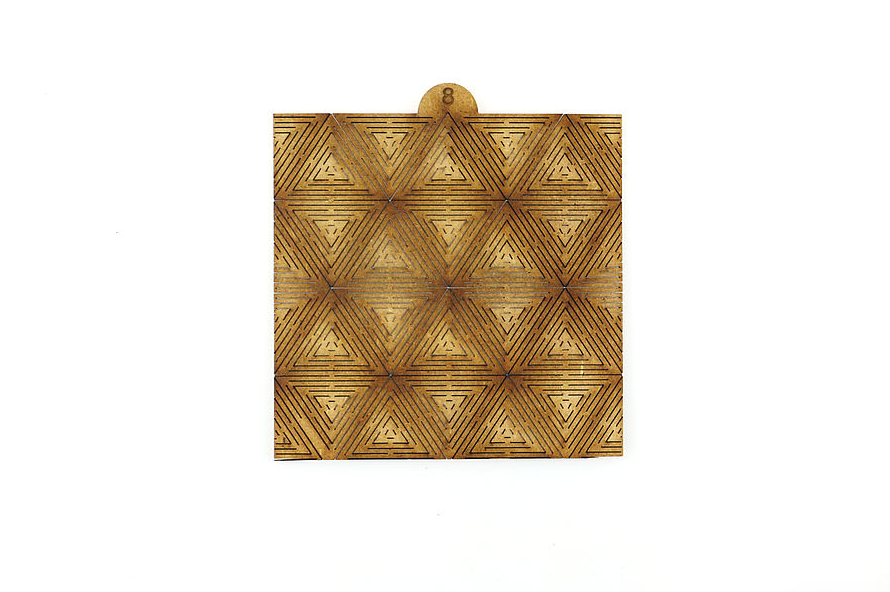
Techniques for wood cutting
Most types of wood will adapt extremely well to cutting techniques with bending applications. With that being said, it is important to be mindful of the wood type being used, and the following distinctions will need to be considered:
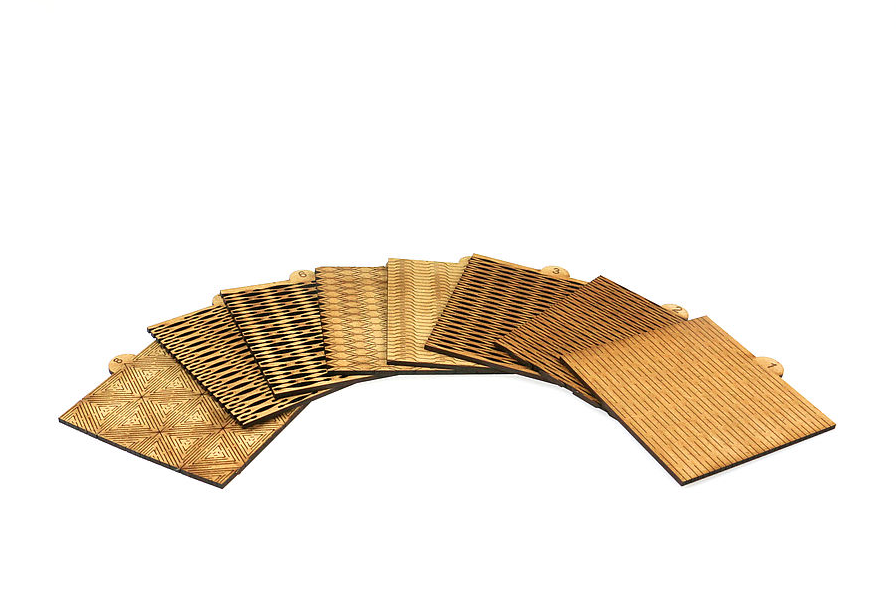
- Plywood
Plywood is very suitable for the use of bending applications, and by gluing the sheets, the wood will become flexible in all directions and can be bent to a narrow radius. - Solid wood
For solid wood boards up to around 5 mm of thickness, cutting techniques for bending applications with recesses, such as Kerf 6, will allow for much more flexibility than a straight cut or cut without recess (Kerf 1). For this reason, it is important to laser cut your workpiece in the direction of the grain to avoid a loss in flexibility or material damage. - MDF
Similar to plywood, MDF is very easy to work with. Because of the mixture of grains, aligning the cut lines is not required however.
Techniques for acrylic cutting
Cutting techniques associated with acrylic are best for rigid bends, e.g. boxes or cases where the bending radius is very rarely changed. With a continuous load of the cutting pattern, e.g. with a book, the webs can easily break.
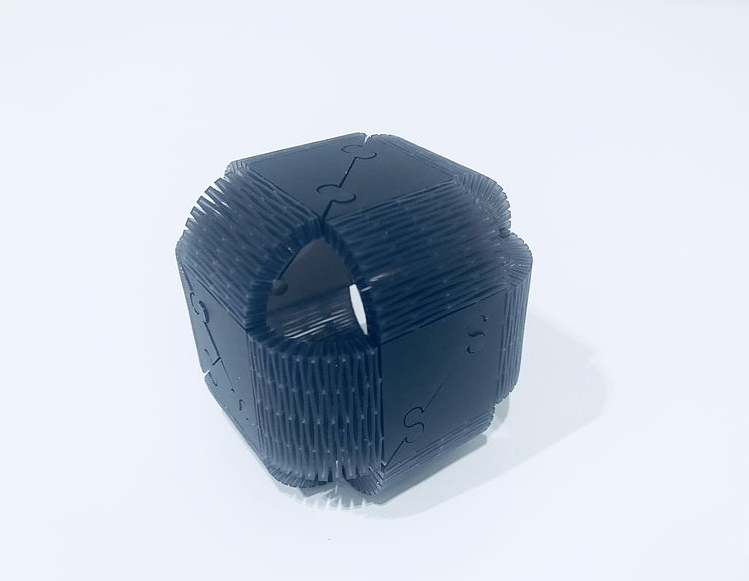
When processing acrylic, the following points must be observed:
- A 2” lens (at minimum) should be used for laser cutting with bends. Since acrylic will melt from the heat of the laser beam, if the focal length of the lens is too small, it may result in the cut areas sticking back together.
- We suggest using a cutting distance of around 1-1.5 mm. If melting occurs even with the appropriate lens being used, try increasing the distance between the individual cut lines. However, if the distance used is too large, bend flexibility will decrease.
Important tips for achieving the best bending result:
In summary, the following factors should be considered when creating the design:
- Material properties and composition
- Grain direction
- Distances of the cuts
- Material thickness