When designing a pair of injection-molded thermoplastic parts that need to be mated together, product designers and engineers will often create two distinct halves that can connect to one another. Many times the geometry and complexity of the part guide that decision. But sometimes, if the two halves are similar or identical, it’s worth exploring the cost-effective—though sometimes challenging—design technique of creating a single part that when rotated 180 degrees, can mate to its symmetrical self.
Why Self-Mating Parts are Efficient
This is beneficial in a few ways, the first being that only a single mold is needed to produce both halves of the part, so the cost of additional tooling is avoided. The second benefit is that there’s one part design, not two. When your design is ready to order, both halves go into production; if modifications have to be made to the design, you’re working from a single CAD model. Finally, maintaining the inventory of a single part is easier and less expensive than multiple parts.
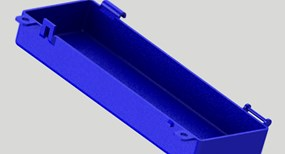
In Figure 1, we illustrate how a single part designed with rotational symmetry can create both halves of a molded rectangular box. Instead of designing one half with hinges and clip holes, and the other with hooks and clip tabs, each side gets one of each—a hook and hinge, clip and clip hole. When placed side by side, they are identical; when rotated 180 degrees, each feature pairs with its complementary connection.
Hinges, clips, pins and sockets, and tongues and grooves are a few ways engineers attach parts to one another. Does the application call for the part to be frequently opened and closed? A clip, for example, can be designed to be re-usable or permanent—a crush pin may only be usable one or two times before it’s damaged beyond re-use.
When looking at materials, softer, more forgiving plastic clips might be the way to go. If it’s a one-time, permanent assembly, then a harder, more rigid thermoplastic may be better. How a material plays with an attachment feature like a clip is hard to predict, however, so adjustments may be needed during iterative development while testing form, fit, and function.
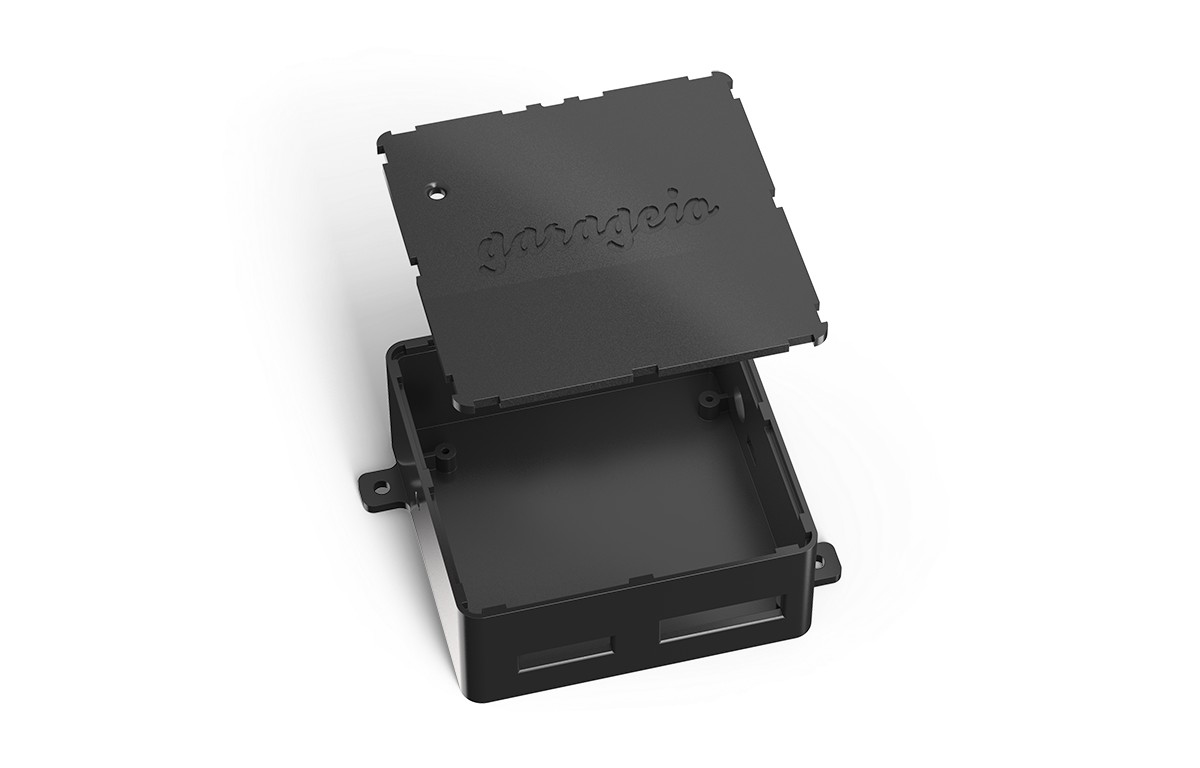
Examples Abound
Self-mating parts live throughout the manufacturing world, often seen in handheld medical devices, television remotes, computer router casings, children’s toys, and pretty much any industry you can think of. Some have completely symmetrical halves, but many do not. Garageio, for example, makes systems that let users control and monitor their garage doors via smartphones. The central communication hub (see Figure 2) is a compact black box that affixes inside a person’s garage. The team at Garageio and an applications engineer (AE) at Protolabs worked together on a design that incorporated an interlocking system of drafted tabs and clips that allowed the top cover to firmly self-mate to the bottom half of the box.
If your part has the potential to be split into symmetrical halves that can self-mate, we encourage you to explore that option as you develop your design. It could save you time and money.
Generally speaking, if you can turn a more manual assembly process that involves screws or ultrasonic welding into a quick self-mating part that doesn’t compromise the final application, it’s probably worth looking into. Our AEs are always ready to tackle any challenging design puzzles, so contact them with questions at info@facfox.com. We also offer a free design cube that, among other things, illustrates clip features that can be used in self-mating parts.