You have probably seen those cool crystal cubes that have super detailed 3D engraved images (a car, a horse, a flower, a logo, etc.) magically “floating” inside. If you have, you’ve no doubt picked it up for a closer look and wondered, “Wow! How on earth did they do that?”
These attention-grabbing pieces are often sold at tourist destinations as souvenirs, as well as for out-of-the-ordinary gifts and awards that people can display on their desk, mantle, shelf, etc. Perhaps you have even seen companies that can take a 3D photograph of someone and engrave that photo inside a piece of crystal with beautiful clarity and amazing detail.
The process is called “3D subsurface laser engraving,” and it is a super cool technology that you really don’t hear a lot about. Well, we are about to talk about it, and even tell you where you can buy the equipment if you are so inclined.
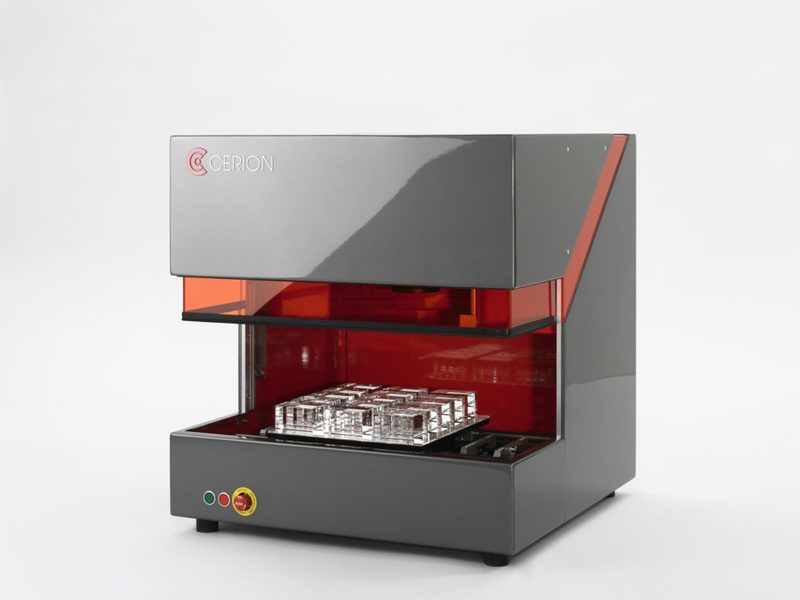
Subsurface crystal engraving is nothing new. It’s been around for a long time, but it has to be one of the least used and least understood techniques in the engraving world. It brings myriad opportunities to the engraver and the customer alike, but there are some stumbling blocks keeping it from being more common than it is.
It all began in 1987 with a Russian scientist, Prof. M.J. Soileau, but the technology was so expensive it didn’t gain much traction. In the early 2000s, however, the Chinese took the technology to a new level with machines that, although still expensive, were far less expensive than the Russian lasers.
First, let’s understand what is meant by subsurface crystal engraving. There are actually several names for the technology. Subsurface laser engraving (SSLE) is the most professional sounding and probably the most commonly used, but there are others. The one that made me scratch my head the most was “bubblegram.” If you try to search for subsurface engraving in Wikipedia, look for bubblegram. There, you will learn that it gets its name from the shape of the tiny fractures the laser makes in the glass—they look like bubbles floating inside the crystal. These tiny bubble-like fractures are positioned inside the crystal so as to create a three-dimensional image of the graphics you are reproducing.
Another really scientific sounding name for this is “volumetric display” but don’t expect anyone to know what you are talking about if you use that term. As I explain what is going on within this technology, however, you will come to understand the term.
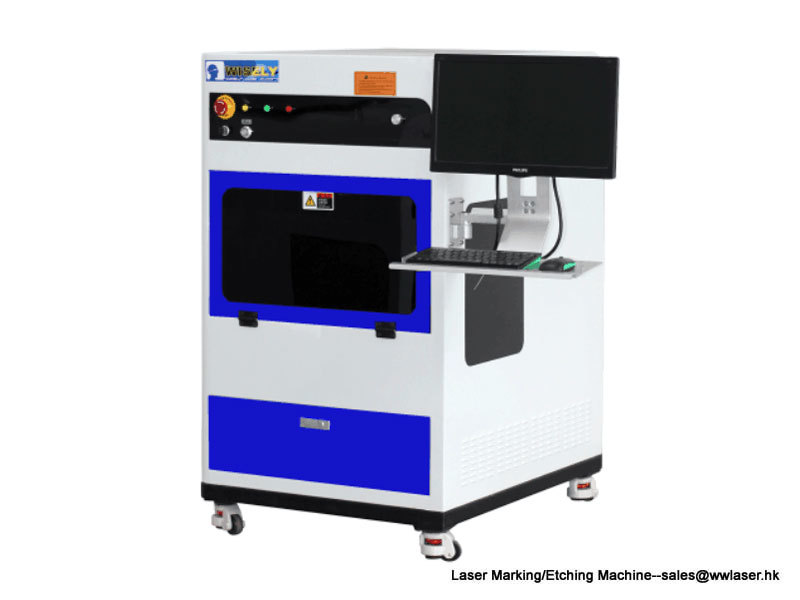
To make all this work, we need a “green” laser. Like a fiber laser, these are solid state, pulsed lasers but green lasers work at a wavelength of 532nm (nanometers) as compared to a fiber laser with a wavelength of 1062nm (about twice as long as a green laser) or a CO2 with a wavelength of 9.4-10.6µm (micrometers), or 10,600nm, which is substantially longer yet. This illustrates the uniqueness of a green laser compared to the lasers most of us have.
You are probably a little familiar with green lasers. Many of the laser pointers sold on Amazon or eBay are green lasers. Of course, they are very low power, nothing near what is needed for engraving glass. You might have heard about green lasers in relation to those that have been used to blind airline pilots. Even low power lasers travel for miles if unobstructed, and some planes have nearly been brought down by someone on the ground pointing a green laser at a passing airliner. Green lasers are also used in concert visuals and fireworks displays to create images in midair such as an eagle flapping its wings or an American flag waving in the breeze.
Green lasers are also used in medical procedures of various kinds, including MRI scans, but I mention that only as a bit of information since we are unlikely to ever cross paths with anything other than the business end of those lasers.
In terms of green lasers for 3D SSLE, I find it interesting that I could not find a single manufacturer for green lasers in the United States—at least not one used for engraving 3D images in crystal. Nearly all come from China although there are a few from India and one company in Germany. There is, however, at least one U.S. distributor for the equipment. Headquartered in Rancho Cucamonga, CA, GlassWorks North America (https://glassworksna.com/), originally a company involved in the production of subsurface and surface laser engraved awards, is now the exclusive distributor for CERION Laser GmbH, a Germany-based company that manufactures green lasers for 3D SSLE. Among other models, GlassWorks offers the CERION c-jet compact subsurface laser engraving system which is designed for engraving crystal products ranging from small keychains up to an 11.8” wide x 11.8” long x 5.9” high crystal item. This system features a multi-mode operation that allows multiple crystal items to be engraved in a batch, with the same or different images, is air cooled and is fully transportable.
As a side note, I personally find comfort in buying from a USA manufacturer when possible or at least a company with a U.S.-based distributor for a number of reasons, not the least of which is service and support. I also like to know that machines shipped from Asia are checked prior to my receiving them. Laser cabinets are often damaged in shipping which can cause damage to the internal components of the machine and, although all the Chinese companies promise good service, that hasn’t been my experience.
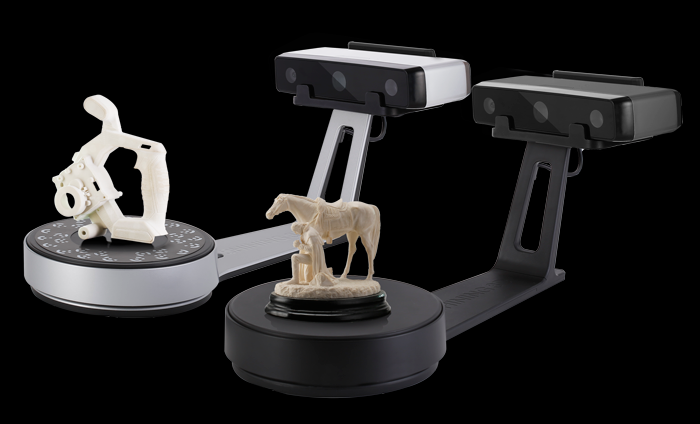
Prices for these specialized green lasers vary widely depending on the supplier, the size of the machine, features, etc., but in any case, there is a substantial investment involved. The Chinese lasers range anywhere from $20,000 to $65,000 or more. The CERION lasers from GlassWorks range from about $60,000 for the c-jet up to about $130,000 for their much larger professional model.
So how do these machines perform their magic? When working with glass or even acrylic, a CO2 laser can effectively mark the surface of the material. A fiber laser’s beam just passes through any clear material without leaving a mark, but a green laser can be focused anywhere within a clear material. To achieve this with a green laser requires an extremely clear optical grade crystal (the same quality used to make precision lenses). Ordinary glass will not work due to its lack of clarity and inability to reflect light in the way the laser requires. This type of crystal isn’t particularly expensive, but it is unique. It is available from industry suppliers of crystal such as Topmost World (www.PrismCrystal.com) and Crystal D (www.CrystalD.com).
The way all lasers mark glass is by heating the elements in the glass until the glass fractures. To create an image inside a crystal cube, the size and position of the fracture must be controlled. This becomes tricky since even a small image of 1” will require tens of thousands of tiny fractures that measure in the millionths of an inch. If two or more of these micro-fractures get too close to each other and overlap, it can cause what is sometimes called a “crash” (also referred to as “cracks”) which is a larger fracture or crack. Too many crashes and the image won’t be recognizable.
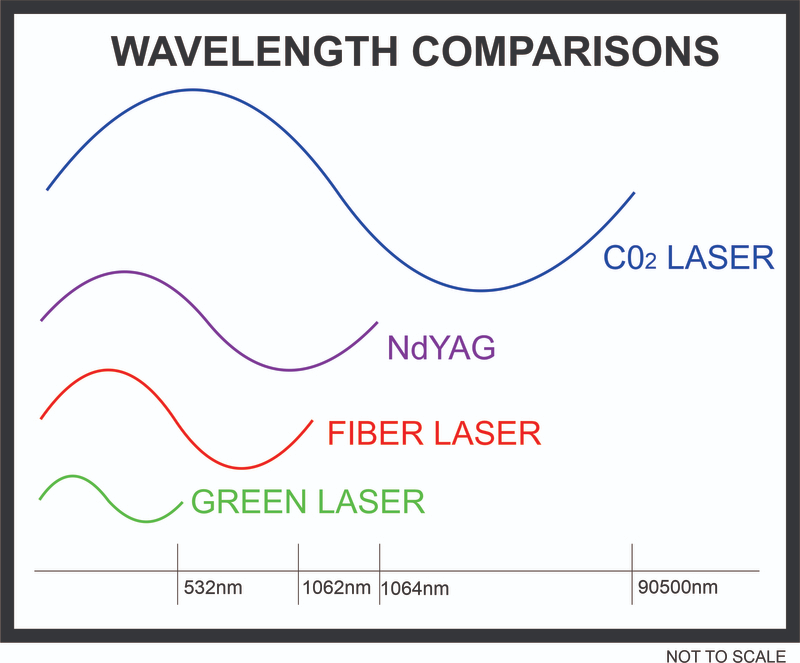
The position of each micro-fracture is both computer generated and computer controlled using specialized 3D software. The 3D software generates these images in one of two ways. The simplest is to position the desired points or bubbles on a horizontal or vertical plane. This helps prevent crashes but doesn’t create as good an image as the second method which just places the points wherever they may fall. This method is more likely to create crashes but generates a higher quality image.
The reason these points are often referred to as “bubbles” is because of their shape. Rather than creating tiny points or shards within the glass, the laser creates a relatively round fracture or void in the glass that is hollow in the center and, thus, referred to as a bubble. Consequently, the image is referred to as a “bubblegram.” Another name for the process is “laser induced damage” because the laser physically damages the crystal while producing the product.
To generate a bubble, the software tells the laser where to focus (X, Y and Z positions) and then tells it to fire one burst of energy. The point where the laser fires reacts by creating a tiny void in the crystal. 3D images can require a million or more points, depending on the size and complexity of the image. Still, the process is fast and an average cube can be engraved in just a few minutes. The size of the void is typically in the tenths of a millimeter and the accuracy of a good laser is less than 100µm.
If you would like to see how the software works, go to https://www.youtube.com/watch?v=tlqInX3Vtws. There you will see a 3D program called “ShapeMG” from a company called Logistic Technology. CERION Laser has also developed software called “Crystalab Pro” (http://cerionlaser.com/c-3d-laser-3d-software.htm) which is designed to produce high-resolution grayscale images in 2D and 3D.
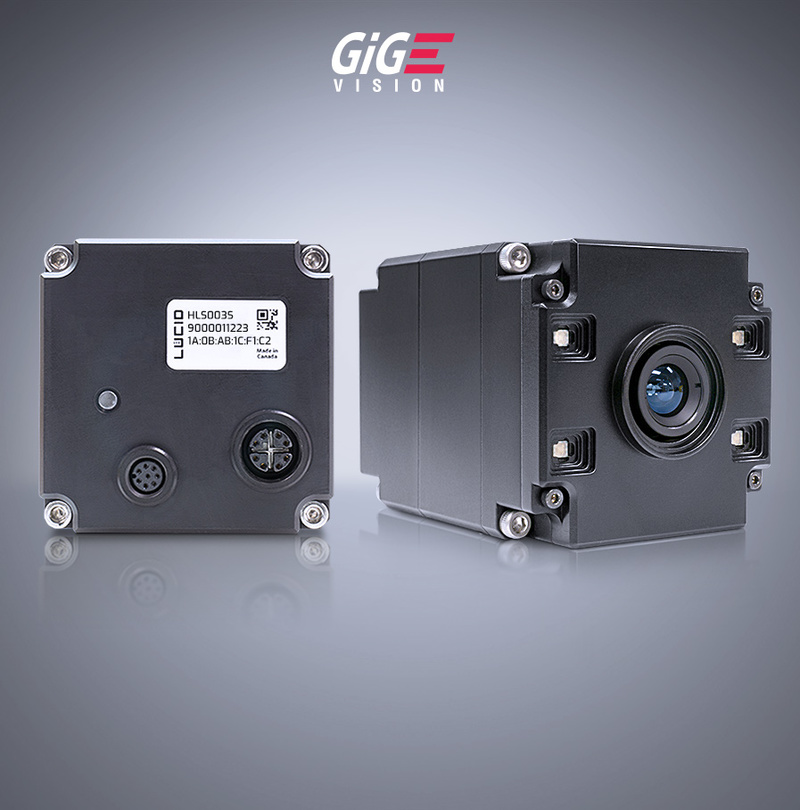
Sophisticated software for 3D SSLE lasers not only breaks a bitmap into thousands or even millions of points, it can also convert a 2D image into 3D by a process called “re-rendering” and, interestingly enough, it doesn’t require an unusually powerful computer to do it. Of course, the more powerful the computer, the faster the image can be created. Some of the lasers are capable of “engraving” up to 220,000 bubbles per minute. Most modern CAD programs are capable of performing this task.
To create shades of gray in an image, the software is used to change the amount of power applied with each pulse of the laser. The so-called grayscale is actually an optical illusion because the bubble created by the laser with reduced power isn’t as bright as those generated using more power.
If you want to get involved in 3D SSLE, you might want to consider a 3D camera and/or scanner so you can take pictures of customers or objects and then reproduce them in crystal. Let’s consider a camera first.
A camera for a 3D engraving has to be a 3D camera, obviously. There are a number on the market that range from a few hundred dollars to over $10,000. GlassWorks sells a 3D camera for $18,000 that is specifically designed for taking photos of people. For simplicity, I opted to share a basic camera for 3D engraving.
You have probably seen the older 3D cameras. They can be distinguished by their having two lenses separated by several inches. The separation is critical for a 3D effect and those are still used, but there is a new sheriff in town for taking pictures of people and that is what we will focus on.
3D cameras are far more common than they once were because of the advent of 3D television. People are using them to take home movies that can be shown on their 3D TV sets and, theoretically, these cameras could be used for engraving 3D images, but they are intended more for making movies than stills and they are color. What we need is a really high-resolution 3D camera that is small, portable, dependable and reasonably priced. I also want a manufacturer I can depend on that understands 3D engraving.
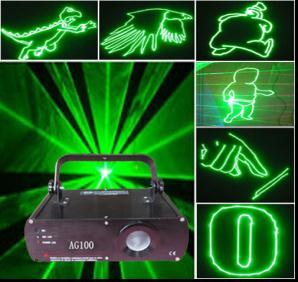
I researched a camera from Lucid Vision Labs. They offer a 3D camera that has something new. It’s made by Sony and is called a “Depthsense” or “Time of Flight” sensor. Unlike the 3D cameras of old that used two lenses (having two lenses sometimes introduced more problems than it solved), this camera (the people who know these things call them sensors, not cameras) creates a 3D image by sending out a light wave and measuring the distance it travels by how long it takes to reflect back to the sensor. Here is how Lucid (www.thinklucid.com) explains it:
Current Assisted Photonic Demodulator (CAPD) Time of Flight technology works by measuring the time delay of light traveling from a light source, reflecting off a scene, and into a sensor. The specific type of Time of Flight the Sony IMX556 CMOS sensor uses is called continuous wave (CW) modulation, also known as CW phase-shift or Indirect Time of Flight. Instead of measuring the time delay of a single light pulse, the Helios camera emits continuously modulated light, and the phase-shift between this emitted light and the reflected light is used to calculate distance. In order to accurately calculate the phase-shift, the IMX556 utilizes a current assisted photonic demodulator (CAPD) pixel structure that samples incoming light synchronously with emitted light….
The long and short of that is the farther away from the camera each part of the face is, the longer it takes for the reflected light to return to the camera’s sensor. This tells the camera how to create the image in 3D.
Of course, what we want to end up with for 3D lasering purposes is a bunch of points or nodes. As noted earlier, these can’t touch each other when engraved. This super-critical step is all performed in the software.
There are other technologies that are similar to CAPD such as the one that uses a low power laser to measure distance, but this is undesirable because lasers and human eyes don’t get along well together. Although it is unlikely these low power lasers would cause blindness, who wants to take that risk?
Then there are scanners. 3D scanning is a technique used to capture an image which can then be laser engraved (or 3D printed). 3D scanners come in a variety of different types that range from a few hundred dollars to many thousands. Many of the scanners available have significant limitations such as lighting issues (shadows equal poor images), size of the files and color variations. These are the same issues we struggle with in 3D printing only the issues for 3D printing are exacerbated by the amount of detail and depth of field needed to produce a 3D object as opposed to an image.
A Chinese company called Shining 3D has a nice solution for scanning small items in their EinScan-SE and EinScan-SP desktop 3D scanners. These devices feature a revolving turntable with a scanner mounted next to it. Place the object you want to scan on the table and let it turn while the scanner records the image. The EinScan-SE is available on Amazon for $1,399 while the SP version sells for $2,599.
Shining 3D also has a handheld version that allows you to walk around a stationary object (or person) to scan. These aren’t nearly as precise and probably wouldn’t be suitable for high resolution 3D printing but seem to work for subsurface engraving since the 3D subsurface software does the major work in processing the image. Still, I am sure it takes some practice to get a workable image with the handheld device. This device is also available on Amazon for about $5,500.
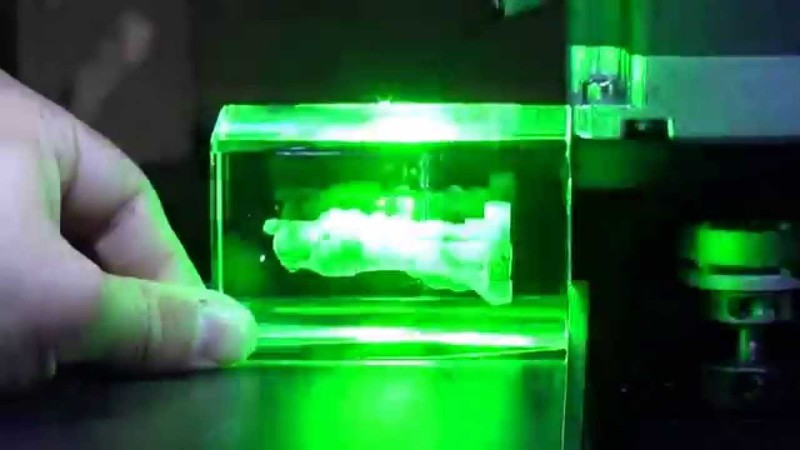
What is the future of subsurface laser engraving? Color! That’s right; technological advancements are being made to do subsurface crystal engraving in color! Explaining how this will be done is easy—I haven’t got a clue and those who do, are being very quiet about it. Still, if you can trust what you see on the Internet, at least one company, Wisely Laser (www.wwlaser.com), is promising this ability in the not-so-distant future. You can see several finished pieces at https://www.youtube.com/watch?v=gEfDNlbK-UQ.
3D subsurface laser engraving is a fascinating technology and one that produces beautiful products that aren’t possible with any other method. There’s no question that you could charge a premium price for subsurface engraved crystal products. A stroll through the Internet reveals that a small 3D engraved product like a wine stopper can sell for around $80 or more while one website shows a large cube subsurface engraved with a photograph priced at $2,500! The marketing possibilities for these products are vast—corporate gifts and incentives, personalized gifts (weddings, new baby, graduation, etc.), awards, promotional products, and on and on.
SSLE has evolved over the years to become better, easier and at least somewhat accessible to personalization businesses. Maybe it’s something to look into for your business. Who knows what the future might bring?