Focusing on these five areas, in particular, we’ve compiled a list of innovative applications made possible by CNC machining.
Breaking into aerospace and beyond
The mechanical properties and achievable accuracy of CNC machining mean that it lends itself well to the stringent regulations of the aerospace sector. An AS9100D certification signifies that a CNC machining facility is capable of maintaining the quality standards established by the Society of Automotive Engineers for this industry.
CNC machining applications in aerospace vary from small parts, such as tooling and component housings, through to medium and large components integral to an aircraft’s landing gear, wings, and bodies. This applies to both civil and military vehicles.
At NASA, CNC machining is mission-proven manufacturing technology. The method has been applied at the agency to everything from ground testing and internal engineering projects to its interstellar missions and voyages to the International Space Station (ISS).
Specialist workshops at leading aerospace manufacturers also use CNC machining. The speed brake of the F-15 Eagle fighter jet, for example, is made by Boeing’s proprietary CNC machining methodology.
By selecting CNC machining, aerospace OEMs can consolidate part assemblies, thereby increasing mechanical stability and reducing complexity — which is valuable when it comes to replacement. Over the lifetime of an aircraft, the multiple coating options for CNC machining, like anodizing, also offer a high degree of protection against corrosion from the elements, making it a valuable option for end-use production
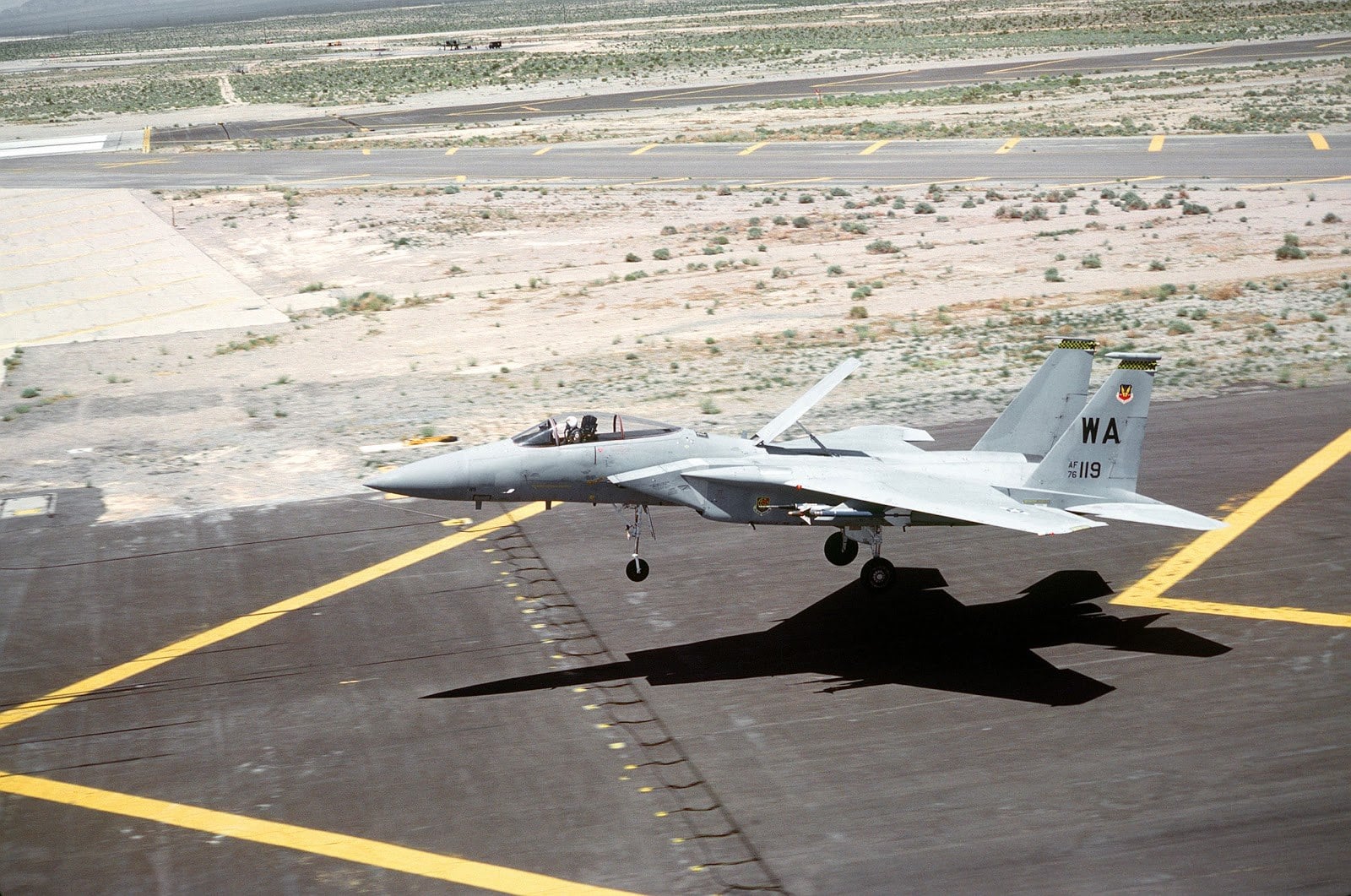
Improving surgical operations
In medicine, CNC machining is especially practical in the rapid prototyping of devices. By matching material selections between a prototype and end-use part, a proof-of-concept medical device can be made to provide the same mechanical performance as its mass-produced equivalent, leading to better testing at those critical early stages.
At Galen Robotics, a Californian med-tech developer, CNC machining is combined with other manufacturing processes to develop new solutions for noninvasive surgery. Focusing on the field of otolaryngology, the team seeks to improve surgeons’ means of operating on delicate areas like the ear, nose, and throat. An assistive device conceptualized by the Galen Robotics team has undergone a number of iterations, thanks to the quick turnaround of CNC machining. As a result, the device is now undergoing clinical testing.
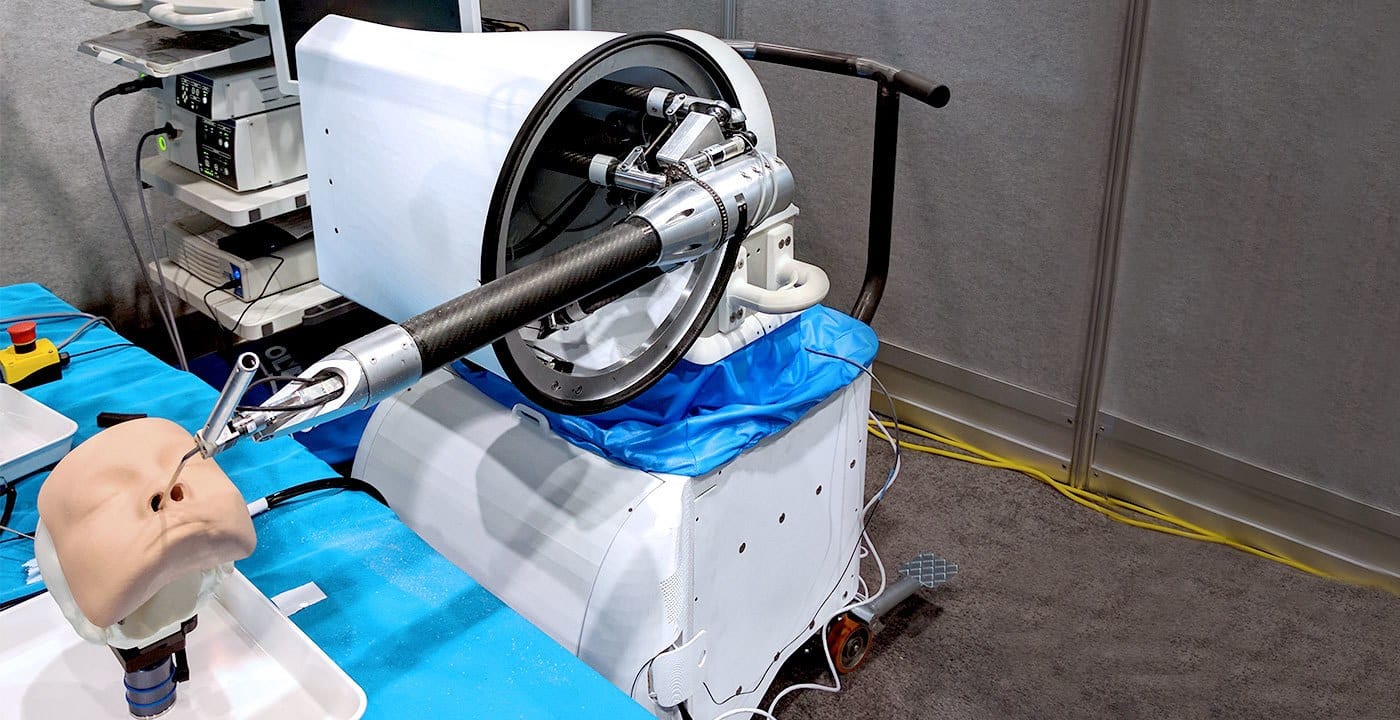
The material selection in CNC machining is also essential to producing end-use devices in healthcare. Common medical-grade materials, such as Titanium 6Al-4V, PEEK, and Stainless Steel 17-4 are all CNC machineable. Both titanium and PEEK have proven to have high biocompatibility when implanted into the body. The precision of CNC machines makes it possible to create a complex surface texture on the implants, which in turn helps encourage the in-growth of live cells and reduces the risk of rejection from human immune systems.
The competitive edge in car racing and renovation
Ever dreamed of renovating a classic car? CNC machining could help with that, too. Ideal for producing legacy parts no longer in production, this method is perfect when sturdy construction is required. Vintage Volkswagen camper vans sold by GoWesty in Los Osos, California, aim to be “in better shape than when they came off the factory line” after renovation. Roller bearings used on the sliding doors of the vans and sections of the electronic fuel injection (EFI) system are just a handful of the parts made for GoWesty.
In race car development, CNC machining is also useful when seeking a competitive edge. Several parts for UPenn Racing Team’s electric race car have been made using this technique. High-performance parts for their record-breaking vehicle include method blocks to hold the battery in place and enable an acceleration of 0 to 60 mph in less than 3 seconds. The bellcranks, vital to the performance of the suspension system, are also produced using CNC machining.
One of the main advantages CNC machining offers to the automotive sector is its flexibility. Parts from pre-production to volume batches can be made with the technology, retaining high-performance characteristics. As in aerospace, there are also many coating options available for CNC machined car parts, these include electrophoretic coating, conversion coatings, and paint finishes.
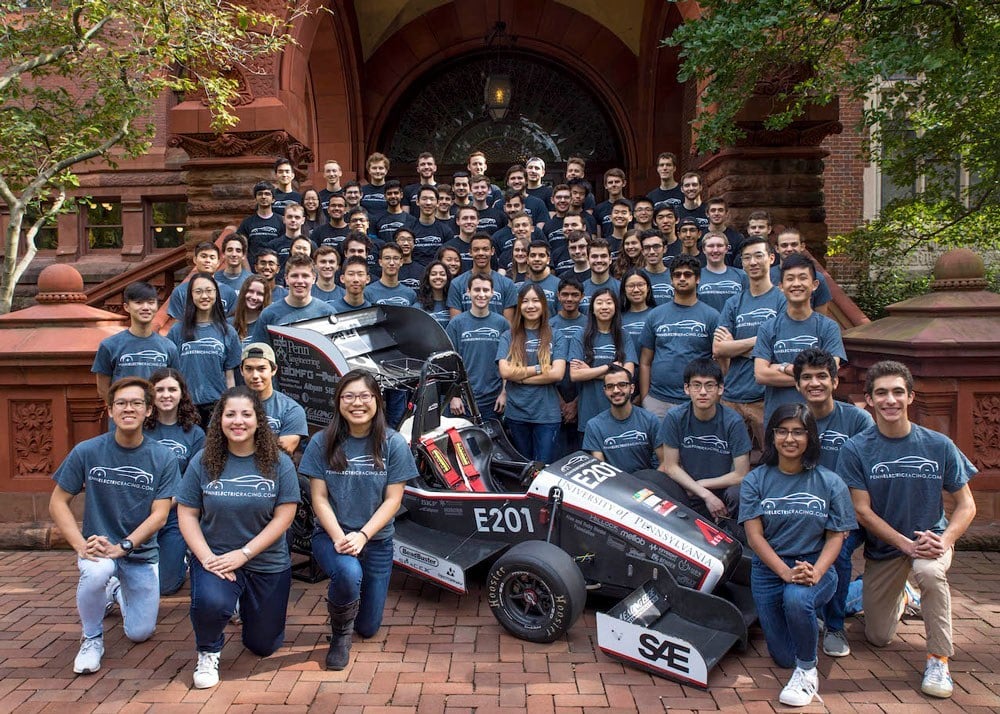
CNC turning industrial piping and mold-making into savings
The industrial sector encompasses a broad segment of manufacturing across heavy machinery, machine tools, industrial robotics, petrochemicals, power generation, and oil and gas. The applications therein are incredibly varied, including the production of pipes, tool heads, and couplings. By opting for CNC machining in these cases, manufacturers in some cases are able to reduce machine downtime and to deliver more competitive production costs.
If a gear breaks in a machine, this causes a halt in the production line. In order to attain the gear from a supplier, the manufacturer would typically have to wait more than one month for delivery. In addition, the part may have to be ordered in bulk, resulting in a financial loss and potentially added cost of keeping the inventory.
CNC machining makes it possible and economical to produce a single gear or small runs of the product. By using the right manufacturing service provider with multiple global locations, the turn-around time for this part is typically reduced to within one or two weeks.
At home with electronics
Practically all consumer electronics devices today are made using CNC machining. Custom electronics housings and the PCBs inside these devices, as well as smartphones and tablets, are all beneficiaries of the machines. For PCBs, in particular, CNC milling is advantageous because it doesn’t require the use of chemicals integral to other fabrication processes. For Mac users, interaction with CNC milling is part of the daily routine. Casing for the Apple MacBook laptop is milled from a single piece of aluminum, delivering the rigidity and performance of the solid bulk material. Named the “unibody enclosure,” this essential piece of Apple hardware has been part of the production line since 2008.
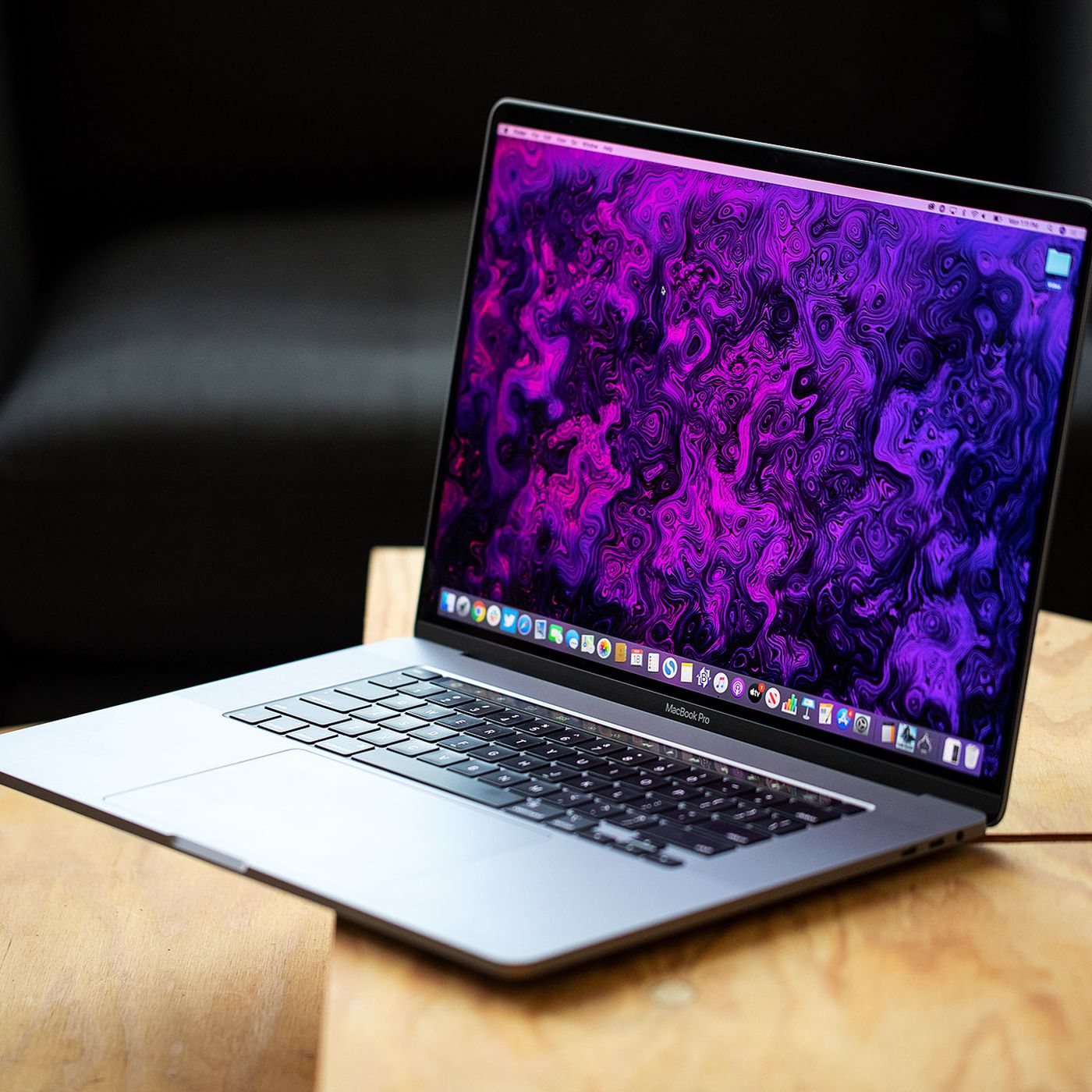