Technical ceramics are ideal materials for parts that need to be corrosion and mechanical wear and tear-resistant even at high temperatures. Technical ceramics include aluminum oxide (alumina), zirconium oxide (zirconia), aluminum nitride, silicon carbide and silicon nitride, to name the most common types. And it is now possible to 3D print parts made of these special or advanced engineering ceramics. In this article we have a brief look at some advanced ceramics and discuss the different methods to 3D print these materials.
When mention ceramics, the first thing that comes to mind is the traditional pottery ceramics, where pots are made from clay and sand, mixed with liquid (usually water). Or we might think of porcelain, which is a type of ceramic, for its use as an electric insulator.
But the field of ceramics has since been expanded by the creation of different ceramic composites to be used in technological applications far more complex.
These modern industrial ceramics can be made to be as tough as the hardest metal, or turned into superconductors, or can be made into porous structures for membrane and filter technology.
These materials are referred to as technical, advanced, industrial, or engineering ceramics.
They are special ceramics that are used for a wide range of specialized applications in different industries. From automotive, aviation, aerospace, electronics, energy to the biomedical field.
Oxides and non-oxides ceramics
Within this class of ceramics we distinguish two main groups: the oxides and non-oxides. In addition, we would find different types of composites.
The first group comprises the metal oxides alumina, zirconia and silica. The other group, the non-oxide ceramics, is made up of materials such as silicon carbide, silicon boride and silicon nitride among others.
What makes these technical ceramics an interesting material group for industrial applications is that they have superior mechanical, electrical, thermal, biological and chemical properties compared to most metals and polymers.
These properties are: high strength, high dimensional stability (low coefficient of thermal expansion), low density, high resistance to abrasion and corrosion and exceptional chemical stability as well as heat resistance.
Lets have a closer look at some of these ceramics, since each material has its own particular characteristics and strengths.
Oxides
In this group oxide fibers are added to the ceramic mixture to provide added strength and reinforcement and add make the final component withstand oxidation.
Alumina
Alumina (aluminum oxide) is the most widely used of the technical ceramics, it is also the most cost-effective (cheapest) material of this class. Alumina has many excellent properties the most important being: high levels of hardness (nearly three times the hardness of stainless steel) as well as good corrosion and temperature resistance.
Components made from alumina are electrically insulating and puncture-proof and are therefore suitable for a wide range of applications, such as substrates in the electronics industry.

Zirconia
Zirconia (zirconium dioxide) is based on zirconium which is a metallic element. Zirconia’s main characteristics are: low thermal conductivity with excellent thermal insulation, and very high resistance to crack propagation.
They offer a very good compromise between hardness and toughness, which makes them very useful for a wide range of applications. Zirconia ceramics are less brittle than other ceramics. They can be used to make ceramic knives for example.
You will also find zirconia in dentistry applications such as dental prostheses, and other medical devices.
Also available are composites or variations of these materials, for example:
Alumina toughened zirconia: great biocompatibility and resistance to wear and thermal shock, recommended for biomedical and industry applications.
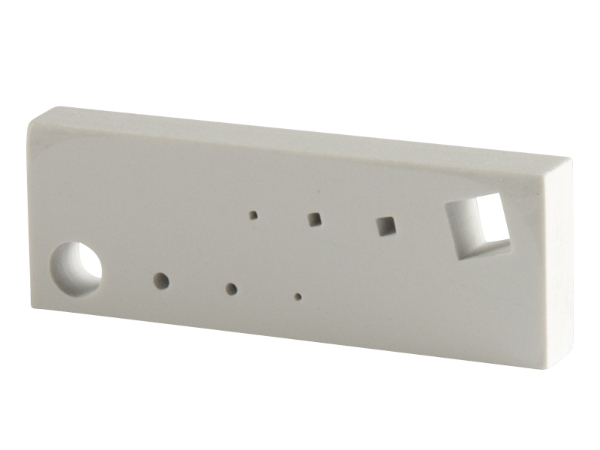
Silica
Silica (SiO2) is well known for its thermal shock resistance and leachability (chemical dissolution). For these reasons, it is commonly used for the production of shells and cores in investment casting for aerospace and energy applications.
And Silica-based materials for casting cores used for the production of casting cores for investment casting.
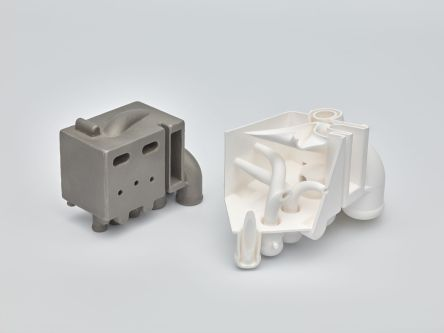
Non-oxide ceramics
Non-oxide ceramics perform better in extreme environments, for example, high heat, then oxide ceramics. Silicon carbide and silicon nitride, two commonly used non-oxide ceramics can for example withstand temperatures up to 2400 degrees Celsius.
In addition, they show high corrosion resistance, hardness, and oxidation resistance.
Silicon carbide
Silicon carbide is hard (four times harder than stainless steel) and when silicon infiltrated silicon carbide becomes one of the world’s hardest metals. It is much lighter and harder than other ceramics and is resistant to acids. Silicon carbide, is the most corrosion-resistant ceramic. It is used in mechanical seals and pump parts, car brakes, car clutches and ceramic plates in bulletproof vests are made from this material.
Boron carbide
Boron carbide is particularly interesting in high temperature applications due to its extremely high melting point (> 3000°C), high oxidation resistance, and high thermal and electrical conductivity; This material can be a good candidate for a variety of applications, such as refractory linings, electrodes, microelectronic devices and cutting tools as well as applications for military and defense use like tank armour, bulletproof vests etc.
Aluminum nitride
The high mechanical properties of this ceramic, combined with high thermal conductivity and electrical insulation, are highly recommended in the electronics industry.
Silicon nitride
The Silicon Nitride is among the hardest and most resistant technical ceramics. It exhibits a very low density, a high fracture toughness, good flexural strength, and excellent thermal shock resistance. Its application is found in the components of pumps and valves, semiconductors among others.
Technical ceramics in aerospace and medical applications
As we have seen, technical ceramics are used in different industries, in chemistry, machinery, electronics, semiconductors as well as in the aerospace and biomedical fields.
The last two industries are especially interesting for the use of these advanced ceramics, because of their excellent properties that are sought after in these industries, The aerospace industry likes lightweight, hard, heat resistant resistant materials, while the biocompatibility, chemical inertness and corrosion resistance are beneficial for medical applications.
For medical applications such as hip, knee, and dental implants ceramics are seriously looked at as an alternative to metals like titanium because of the superior chemical inertness of the material.
But it might be a while before this becomes a reality.
As both these industries are highly regulated and parts need to meet high standards of safety. Obtaining and meeting certification and qualification can be challenging.
3D printing with technical ceramics
Having briefly discussed the different materials, let us now look at the 3D printing methods available and developed to manufacture parts with technical ceramics.
Technical ceramics are hard to form using traditional manufacturing techniques. Machining of ceramic components is extremely difficult owing to their hardness and brittleness, this is especially true for larger parts. Furthermore to create complex and detailed parts with ceramics can also be challenging.
Additive manufacturing can therefore be the method to advance the field of ceramic manufacturing. Using additive manufacturing it is possible to produce parts with highly complex geometries one cannot using traditional machining or molding techniques.
Ceramics can be 3D printed with a variety of 3D printing processes, from Stereolithography to Selective Laser Sintering to laminated object manufacturing. A ceramic feedstock is available in different forms as required for each of these processes.
3D printing processes for ceramics
Ceramic paste for Stereolithography
Stereolithography (SLA) uses ceramic slurry or paste as feedstock.
The ceramic slurry is a mixture of photosensitive resins and a solid load of ceramic powder.
Ceramic components are built up by successive layers using a laser which polymerizes a paste composed of photosensitive resin and ceramic.
The parts are then subjected to a heat treatment which eliminates the resin (debinding) and densifies (by sintering) the ceramic.
Ceramic pastes or slurries can also be printed using related technologies such as Direct Light Printing (DLP) and Lithography-based Ceramic Manufacturing (LCM) technology.
Ceramic powder for SLS
Then we have ceramic powder for Selective Laser Sintering (SLS) and Selective Laser Melting (SLM)
Ceramic filament for LOM and FDM
And ceramic in solid form for methods like laminated object manufacturing (LOM) and Fused Deposition Modeling (FDM), the latter using ceramic filaments of bound powder in a thermoplastic matrix.
Of these processes Stereolithography or related photopolymerization techniques such as DLP are most used. One can achieve a nice surface finish using this method.
The high melting points of ceramics can make printing with SLS or SLM a bit of a challenge.
Also note that SLA and DLP machines are much cheaper than SLM systems.
FacFox offers SLA, DLP and LCM technology on its platform.
Conclusion
Technical ceramics are great materials for applications that require hardness and high heat resistance. These materials are hard to form using traditional methods. Additive manufacturing can be the impetus to more widespread use of ceramic materials in the industry.