If you want to build a 3D printed drone from scratch or add parts to a quadcopter, read on to learn all about making your prints fly!
Commonly known as drones, unmanned aerial vehicles (UAVs) are vehicles that are capable of autonomous operation. As such, a drone is not limited to being an aircraft; it could be a car, boat, or even a hovercraft. However, the term has come to define an aircraft with three or more propellers that provide lift and thrust. These are also commonly referred to as multirotors or quadcopters.
In general, UAVs are mechanically very simple, consisting of a frame, a flight controller, motors, propellers, speed controllers, and possibly first-person view (FPV) equipment.
3D printing is no stranger to flight. For recreational drones, 3D printing can be a great way to make a variety of parts. These can be anything from protective bumpers and camera mounts to add-ons that add functionality.
In this article, we’ll be going over what to keep in mind when 3D printing drone parts, including the types of parts to print and where to find models and resources. We’ll close with a few projects to get you started. But first, why would you want to 3D print parts in the first place? Read on to find out!
Benefits
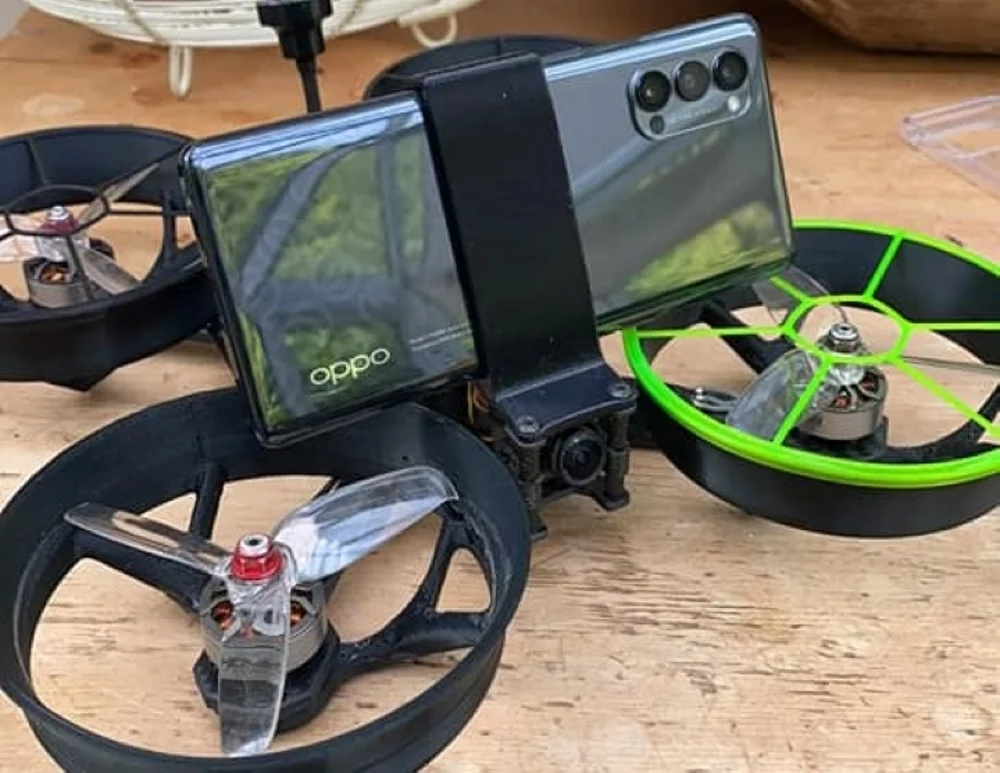
The main advantage of 3D printing parts is that they can be totally custom. In addition, they’re generally inexpensive (assuming you already have a printer and filament), and designs can be quickly iterated from the initial to the final version.
Printed parts can be in your choice of color and material. This way, you’ll be using the material with the best mechanical properties for the part. For example, you could have a blue TPU GoPro mount and nylon propeller guards. (Propeller guards protect the propellers from impact and increase the efficiency by increasing the effective aspect ratio.)
The mount would be best printed in TPU, as it would absorb vibration from the frame and hold the GoPro tightly in place, while the tough nylon can absorb impacts and protect both the propeller and the impacted object. Other strong materials, such as reinforced nylon, could even be used to create airframes, canopies, and camera gimbals.
Another plus when using 3D printed parts is their relatively low density. With 3D printing, settings like the number of perimeters and the infill percentage can be adjusted to decrease weight significantly, the former having more of an overall impact.
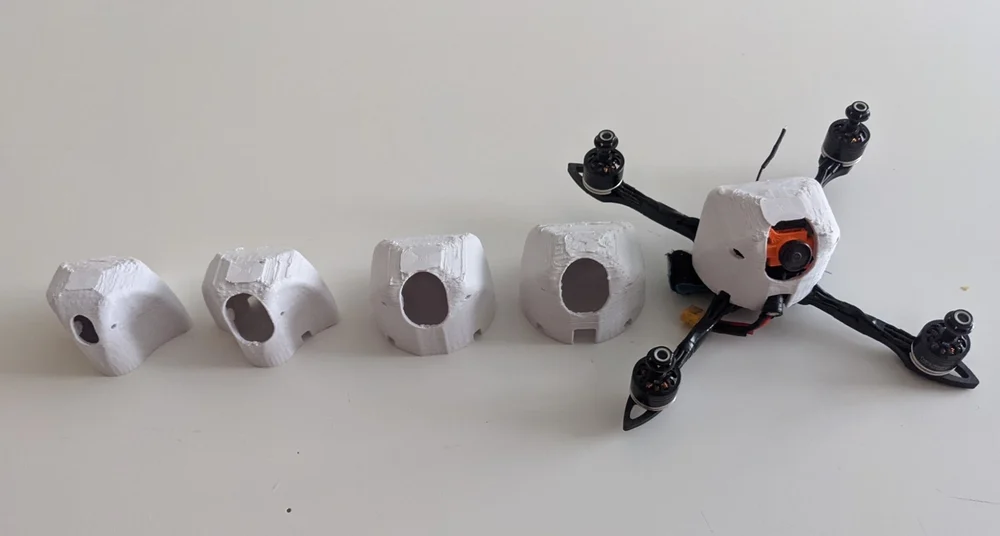
As well as being totally custom and lightweight, parts can be quickly iterated. For example, when designing a canopy, a first version can be printed (likely in an inexpensive material such as PLA), then any required changes can be easily implemented in the next iteration. Once the model is deemed finished, it can be printed in a more expensive material such as carbon-fiber nylon or even, if funding isn’t an issue, carbon-fiber PEEK.
If a part breaks, assuming you already have the filament and a printer, part creation can be started without any delay. Even though many retailers offer fast delivery, it’s likely not faster than (or as satisfying as) printing the part yourself.
Considerations
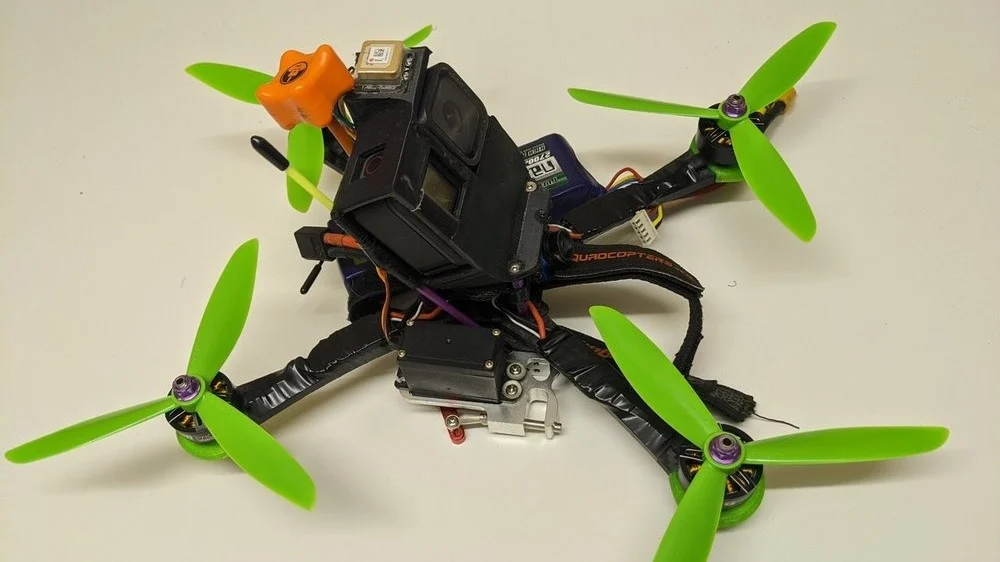
While 3D printing opens up a whole new world of possibilities in terms of additional functionality, the most important thing to bear in mind is the weight of your aircraft. Not everything that can be printed and installed should be! Every gram on the aircraft has an impact on flight time and performance, especially on rotary-wing aircraft. As such, on a craft intended for long flight times, a GoPro mount, head tracker, and drop mechanism aren’t all necessary.
In the US, regulations require registration for crafts over 250 grams. As such, the demand for quadcopters below this weight limit has increased significantly.
Additionally, companies such as DJI that sell UAVs and similar aircraft typically supply all the needed mounts and accessories. More 3D printed parts aren’t required as they would simply add weight.
Best Materials
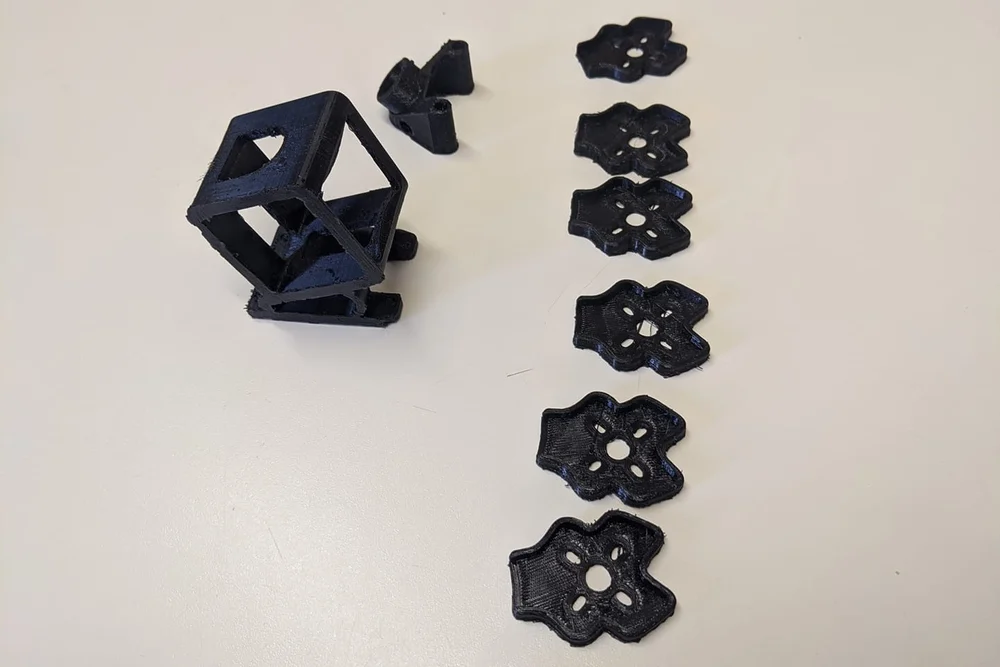
The main material you’ll see, certainly on mini-quadcopters, is TPU. This is because it’s highly flexible and can deform on impact, absorbing energy and protecting the components they’re attached to. Because it’s flexible, it can also absorb vibration, reducing the amount seen in recorded footage. Thankfully, this has become less of an issue with the release of in-camera stabilization.
Another suitable material is nylon. It’s tougher than TPU but still has some flexibility.
Suitability
The main parts that are printed in TPU are bumpers, camera mounts, antenna mounts, and propeller guards. Nylon may also be used for propeller guards, but it’s less common because it’s more difficult to print.
While TPU and nylon have their uses, they’re not suitable for all parts. For applications requiring stiffness and strength, such as custom airframes, a material like carbon-fiber-reinforced nylon is recommended. This combines the toughness of standard nylon with the stiffness of the carbon fiber. It’s also easier to print than nylon, as it warps less and sticks to the build plate better.
One way of protecting the bottom of the craft’s frame and the motor bolts is to add 3D printed “feet”. These are especially useful if flying over surfaces such as concrete. Again, carbon-fiber-reinforced nylon is recommended for this. You could still print the feet in TPU, but the abrasion resistance won’t be as good.
Types of Parts
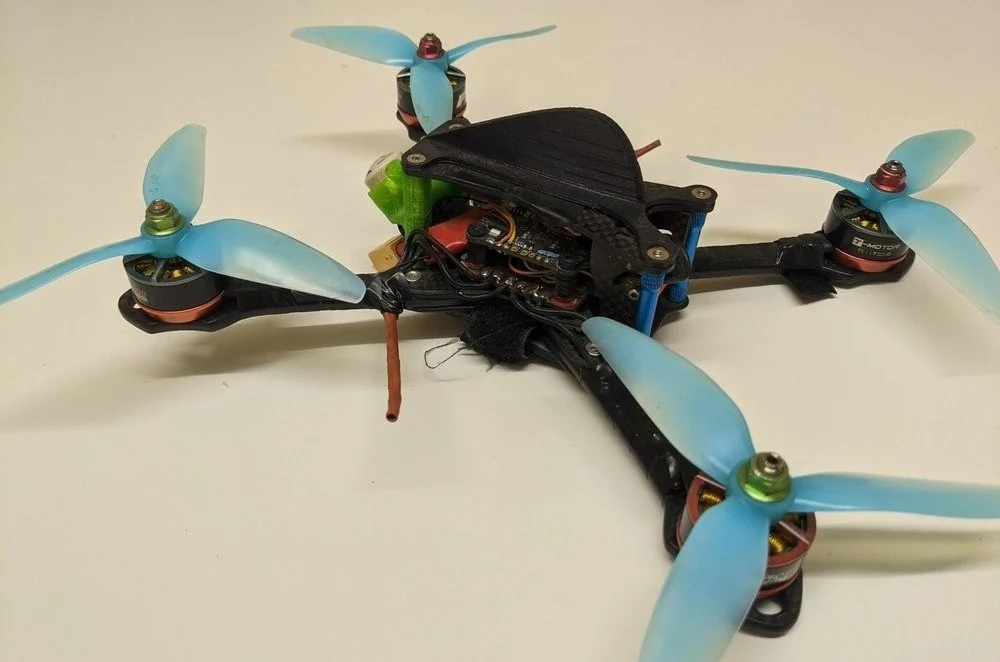
Fins
If racing quadcopters are your thing, you’ll want to try the commonly used top-mounted fins. These are to help with a mode known as “turtle”. When landing an aircraft upside down, two of the motors can be reversed to flip the aircraft over, enabling you to take off again (and complete the race). These are most often printed in TPU and occasionally nylon.
Antenna Mounts
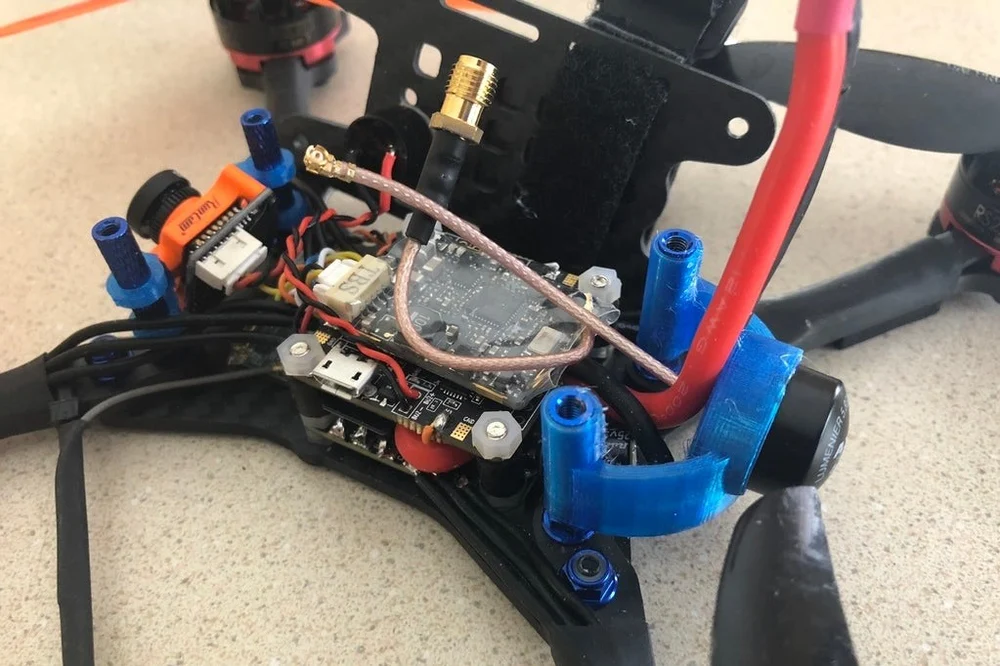
If you’re flying with FPV, the video transmitter antennas are of vital importance. As such, there are many mounting options for these components.
If the craft is intended for long-range flying, encasing the active part of the antenna in TPU isn’t a good idea because there will be a detrimental effect on the video signal. Remember, legally you must stay within the visual line of sight. For these, TPU is the preferred choice because it’s highly elastic and can deform without lasting damage.
FPV head tracking can also be enabled, where the FPV camera is mounted on a rig, enabling it to move in two or three dimensions according to your goggles. This way, the camera moves in parallel with your head, furthering the immersion. For this, you should use a non-flexible material like PETG, ABS, ASA, or even PC. The stiffness is required to eliminate play in the components.
Functional
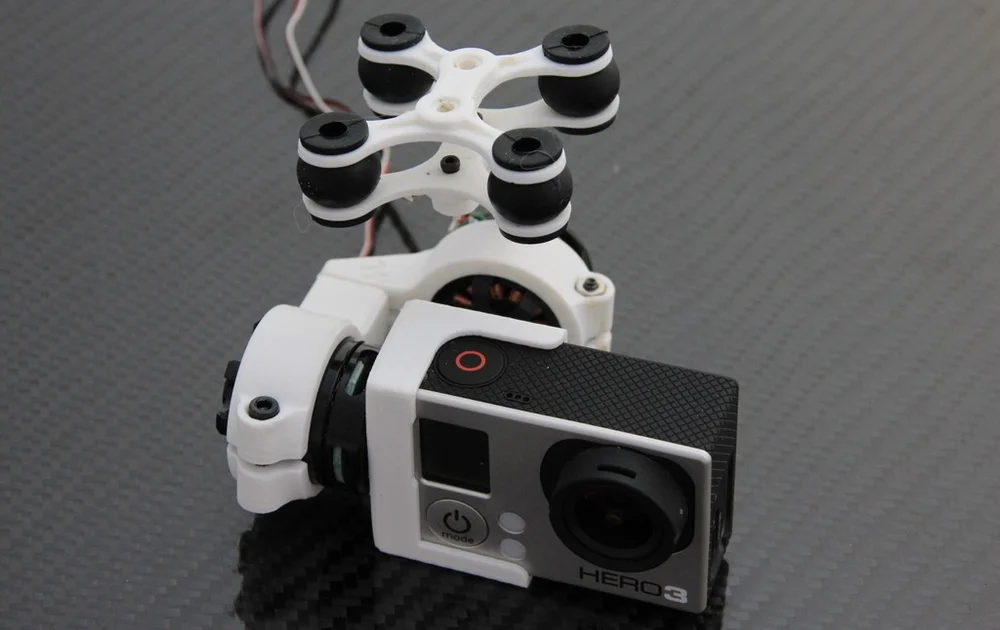
If flying FPV or racing isn’t for you, you can always print parts for increased functionality. Perhaps a camera gimbal for aerial photography or videography, or a mechanism to carry and drop items?
For a gimbal, the moving parts should be printed in a non-flexible material to eliminate play. When mounting the gimbal onto the aircraft, there should be a flexible part to isolate it from vibration.
Protection
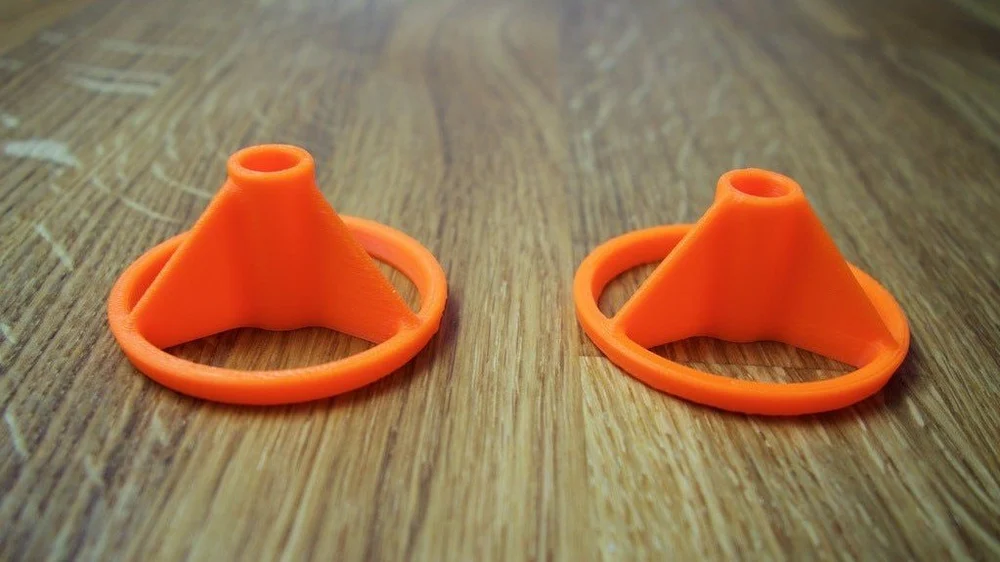
Finally, parts to protect items, such as the control sticks on the radio transmitter, are another good option for printing. These can be in either a flexible or nonflexible material, depending on your requirements.
Sources for Models
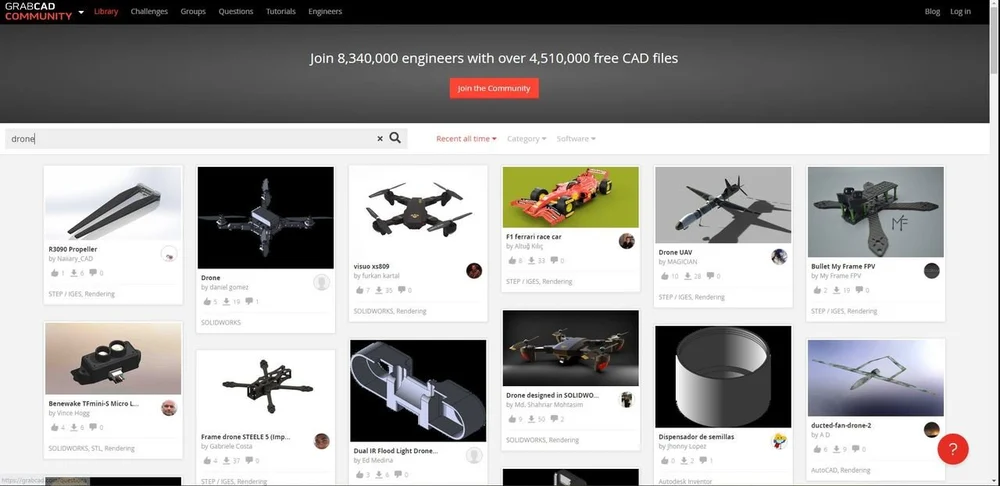
Thingiverse is a great free resource to find mounts for commonly available cameras (GoPro, Insta 360, etc.) and frames (TBS Source One, ImpulseRC, Iflight, among others).
GrabCAD is another free resource that tends to have engineering-focused models available. You can use the search bar to find drone models, and if you’re specifically looking quadcopter-related models, searching “quadcopter” returns quite a few results. Note that you’ll need an account to download models (not so with Thingiverse).
If you download models from any repositories (including the websites above), be sure to check the license it’s under. It may be the case that you can freely sell the model, or you may be required to credit the original designer.
If you have a specific frame and camera, often the manufacturer will have designs available to download and print. These are useful because the probability of the part fitting your frame can be higher than from a third-party website.
If you can’t find what you’re after anywhere, you can design your own parts in CAD software or commission someone to design them for you.
Resources
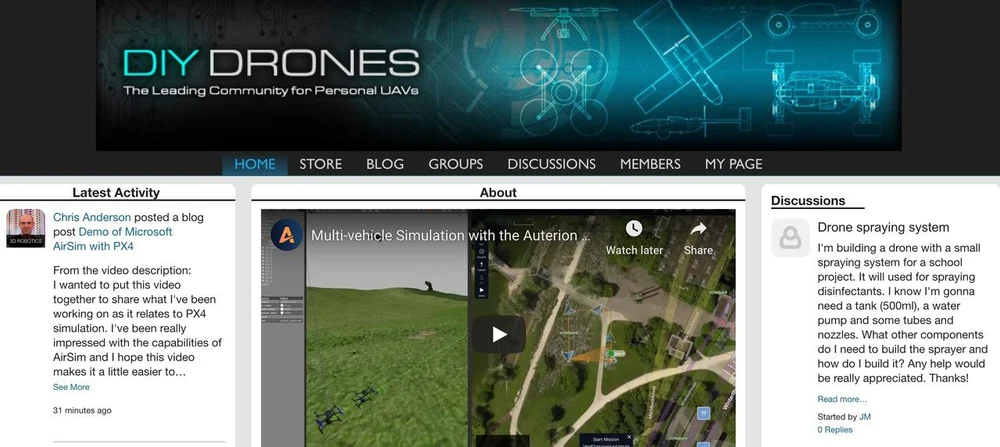
While many individual components can be downloaded from the sites listed above, additional resources such as forums also exist.
The main forums for drone makers are DIYDrones and RCGroups. A full list of printed airframes on RCgroups can be found in one helpful thread, and similar lists can be found on DIYDrones. Additionally, there’s a subreddit for drones that includes discussions about 3D printing, as well as a subreddit for DIY drones.
Projects to Get You Started
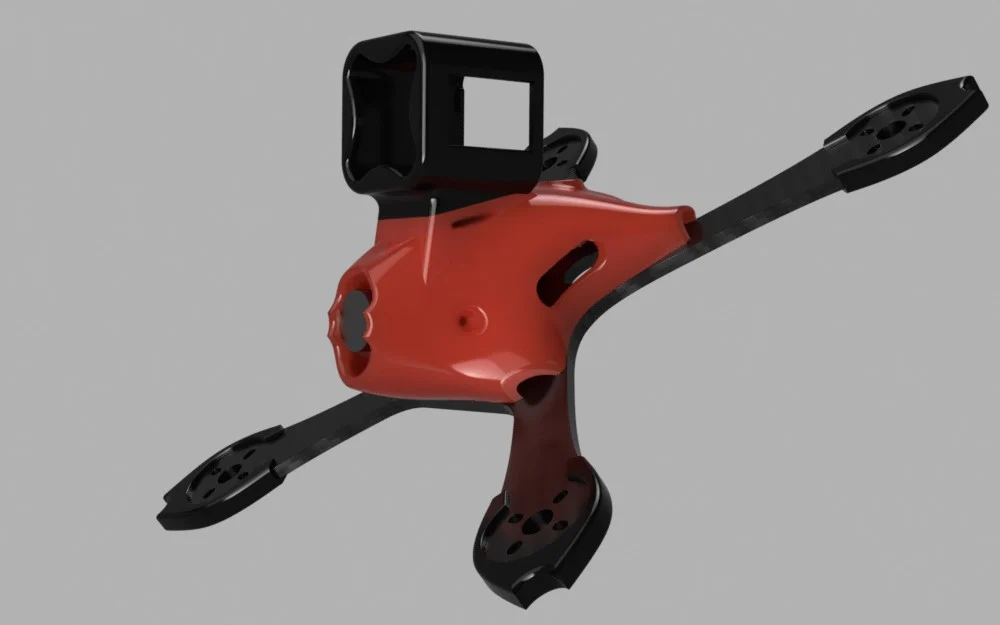
The only real limitation to what you can print is your imagination! You’ll need to consider the intended purpose of both the craft and the part as well as the impact of any additional weight.
Check out the following for ideas from Thingiverse on what can be printed, whether whole frames or just single parts:
- Quadcopter: Frame family that can be entirely 3D printed (dozens of Makes and Remixes)
- Gimbal protector: Protect the sticks on RC transmitters while in transit
- Canopy drone: An example of a canopy that can carry a GoPro (pictured above)
For additional DIY drone project ideas, check out Instructables. There are quite a few projects on the site, some of which incorporate 3D printed parts as well as other components such as Arduinos, Raspberry Pis, or custom-designed electronics.