The vat photopolymerization of ceramic materials is a big topic. Read on to learn more about it and its applications.
Additive manufacturing is gaining ground as a convenient way to make customized advanced ceramic parts, and it’s also less expensive and opens new doors to increasing design freedom.
Advanced ceramic materials are known for their outstanding properties, such as high-temperature resistance, hardness, chemical inertia, higher wear resistance than metal and plastic, and also for usually having electrical and thermal insulation. These materials are incorporated into industrial designs when demanding conditions require a material that is robust and reliable. The thermal, electrical, and biocompatible properties of technical ceramic materials allow them to be used in a variety of sensors and mechanical seals in the automotive industry, bone implants and dentures in the medical industry, and heat shields for space satellites, among others.
However, conventional ceramic fabrication methods are usually related to costly molds, which makes it unfeasible to manufacture ceramic parts on a small scale. On the other hand, ceramic additive manufacturing can overcome this obstacle by providing customized ceramic components at a lower cost and reduced lead times. In addition, functionality optimization requires higher complexity in parts and components, and 3D printing ceramics offers greater flexibility than traditional methods and can produce shapes not possible before.
In this article, we’ll look at different applications of ceramic vat photopolymerization and the different stages of the process, as well as certain considerations. But first, let’s get into the context.
The Context
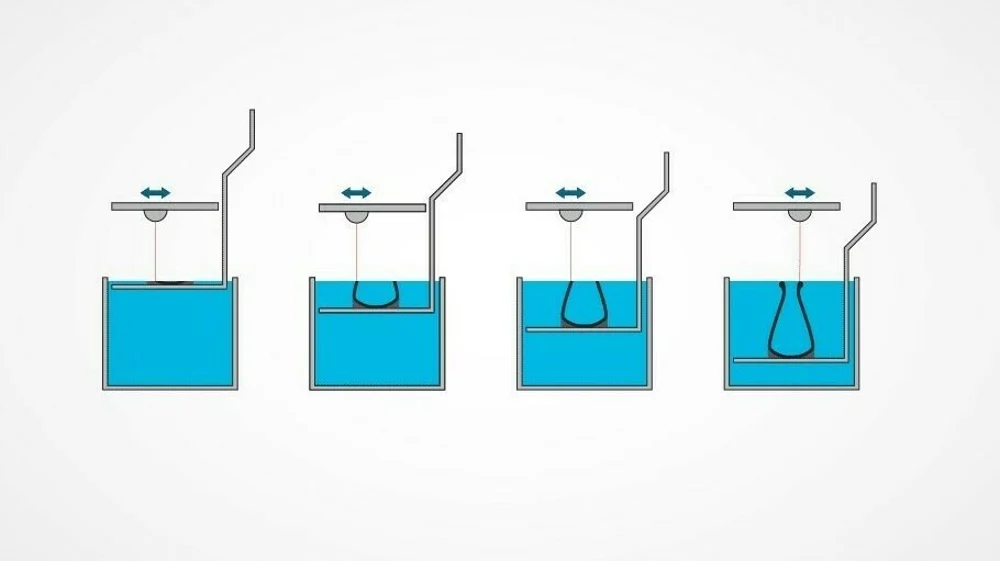
Ceramic additive manufacturing can be performed by several technologies such as binder jetting, direct ink writing, and selective laser sintering. However, all of these technologies aren’t suitable to produce dense parts, thus their applications are quite restricted. On the other hand, vat photopolymerization is the most mature additive manufacturing technology for ceramics, being able to produce dense structural parts.
In this context, ceramic vat photopolymerization stands out for being able to produce high-performance parts with excellent resolution and surface quality. According to ISO/ASTM 52900:2015, vat photopolymerization is an “additive manufacturing process in which liquid photopolymer in a vat is selectively cured by light-activated polymerization”, such as the well-known DLP or SLA processes used by resin 3D printers.
Although this process may be divided according to how the light pattern is formed to create each layer or by light source, this article won’t distinguish between types of vat photopolymerization, since all can be used in the manufacture of ceramics.
Raw material, equipment, and post-processing, however, present challenges in the 3D printing of ceramic pieces with vat photopolymerization processes. Let’s go deeper into applications, though, before jumping into the processing.
Applications
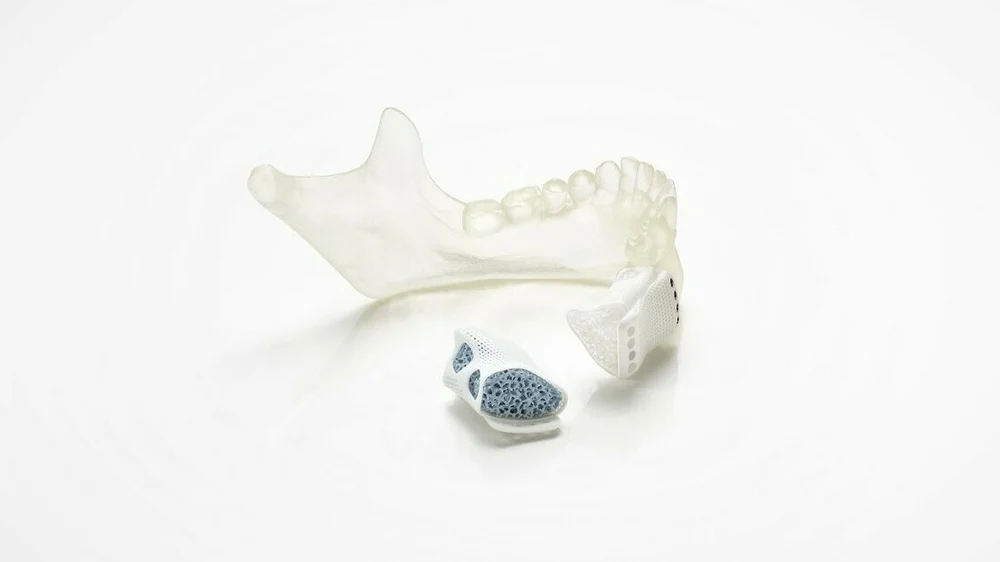
Ceramic vat photopolymerization allows for the fabrication of customized ceramic components with increased geometric freedom and lower cost. Thus, products that would be unfeasible by other manufacturing methods have become a reality, and a number of areas have benefited from the technique. The following are a few of them.
Dentistry
In the dental industry, diverse ceramic dental restorations (i.e. copings, crowns, and bridges) produced by vat photopolymerization have been studied using zirconia, alumina, and glass-ceramic materials. Also, commercial solutions for fully anatomical crowns for minimally invasive restorations with perfect aesthetics and strength are already available.
Tissue Engineering
In terms of tissue engineering, there’s the fabrication of customized scaffolds for bone repair made of bioceramics. Ceramic vat photopolymerization allows for the mimicking of structures present in nature, such as bovine trabecular bone, in both complex geometry and chemical composition. Applications such as cranial or maxillary implants are already possible and present commercially available solutions.
Other Engineering Applications
In engineering applications, better performance can be achieved with geometry optimization enabled by the technique in diverse areas such as catalytic applications (from the automotive industry to biocatalytic applications) and heat exchangers. Thus, the use of customized components for each case achieves greater efficiency in processes, increases gains, and enables new applications.
Next, we’ll go over the ceramic vat photopolymerization process, starting with the materials supply.
Feedstock
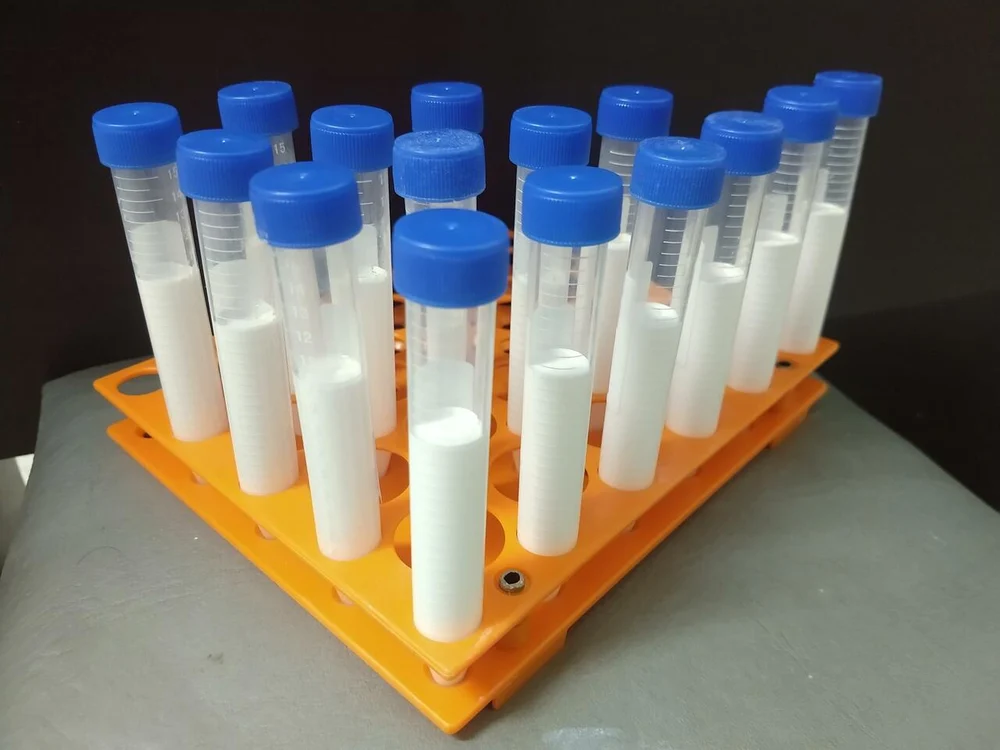
Ceramic 3D printing suppliers also offer raw materials compatible with their equipment. Thus, a wide variety of ceramic feedstock is already commercially available as aluminum oxide, zirconium oxide, and hydroxyapatite. In addition, a large number of researchers around the world have recently been working to improve the development and optimization of these raw materials, and some have achieved promising formulations of ceramic suspensions for vat photopolymerization.
The feedstock for ceramic vat photopolymerization is a suspension composed of a mixture between photosensitive resin, ceramic powder, and additives. The suspension should satisfy the process requirements, namely having a high amount of ceramic filler as well as moderate viscosity.
However, meeting both requirements is challenging, as the higher the solid loading, the higher the viscosity. Additionally, a suspension with negligible sedimentation is desirable. Finally, several requirements related to the rheological behavior of the suspension have to be fulfilled.
Thus, the suspension components should be carefully selected. For example, the ceramic particles should have a suitable particle size and specific surface area, and an effective dispersant should be selected to promote interaction between the resin and the ceramic powder, among others.
In addition, proper preparation should be used to provide a homogeneous suspension. The mixture of the raw materials is usually processed in a ball mill for several hours.
3D Printers
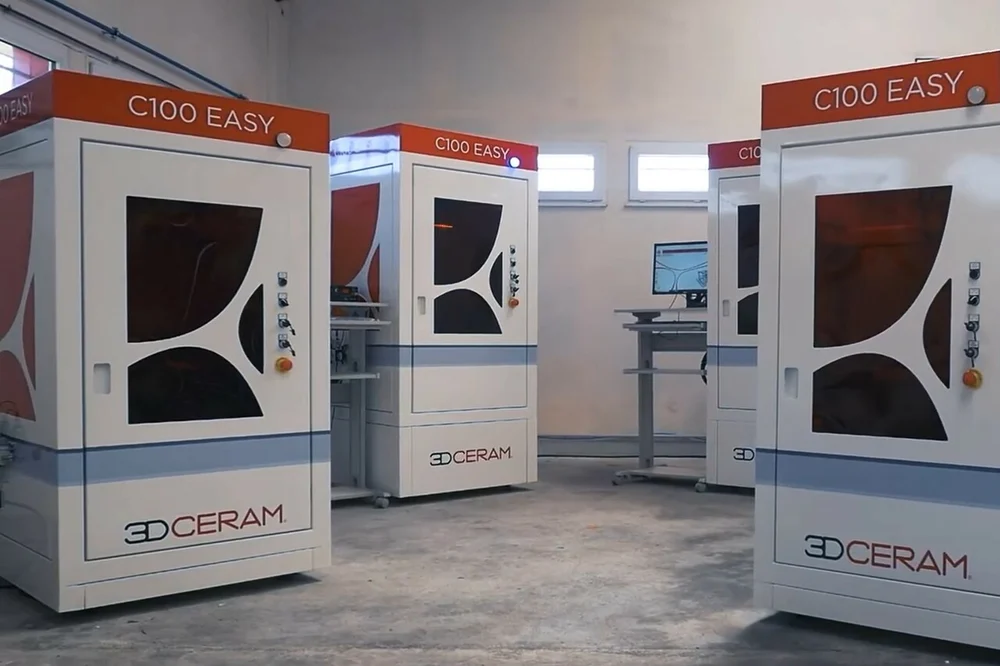
The high solid loading of the ceramic suspensions generates viscous raw materials. Such a feature makes it difficult to create layers in the vat photopolymerization process. Thus, most commercial resin 3D printers weren’t designed to manufacture advanced ceramics. Special equipment with dedicated recoating systems is frequently used when working with such materials.
Although most ceramic vat photopolymerization 3D printers have emerged in the last five years, there are well-established companies – Lithoz and 3DCeram, for example – who have been working in this area for years. It’s important to note, however, that these are industrial machines whose prices may limit widespread adoption of the technique.
On the other hand, research using home-built prototypes and ordinary 3D printers (commonly used in the manufacturing of resin parts) has gained importance, and it may lead to the expansion of the technique to labs and small industries. Still, the non-industrial 3D printers have significant usage restrictions, generally using suspensions with lower ceramic loading, providing parts with reduced mechanical properties.
Post-Processing
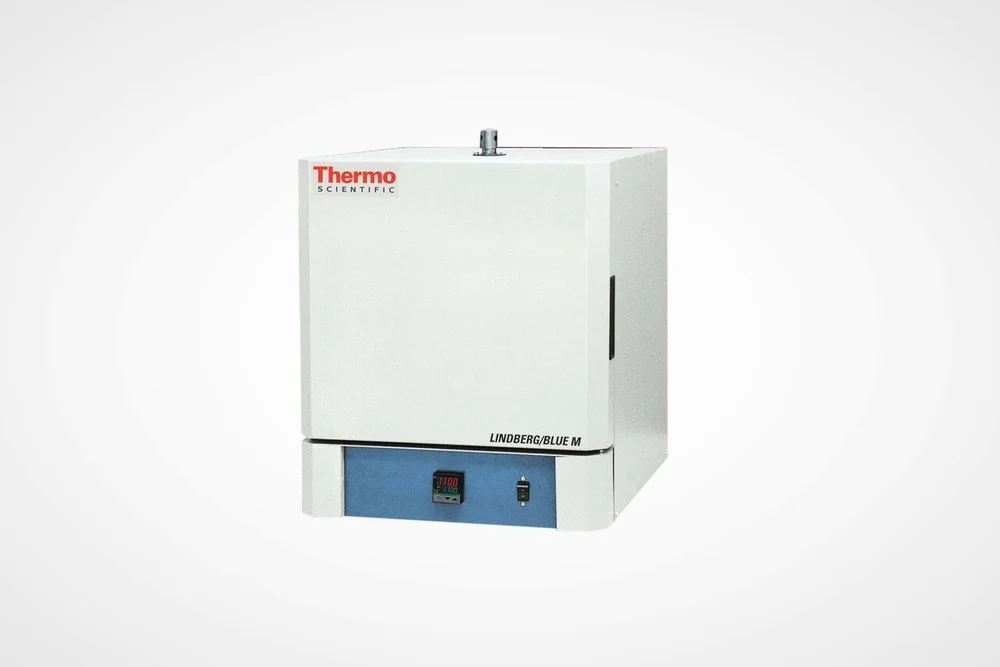
Ceramic vat photopolymerization is an indirect process, that is, a “green” body composed of ceramic powders and binder is created and must go through later stages until obtaining the final ceramic component. This post-processing is a heat treatment that takes place in a furnace, which is traditional equipment in advanced ceramic processing and can be seen in the image above.
First, the binder (resin and additives) is eliminated by thermal decomposition in a process called debinding. Subsequently, the sintering step takes place, and the bodies in the process are subjected to higher temperatures (which may exceed 1,500 °C) without fully melting the particles, aiming to increase the density of the ceramic parts.
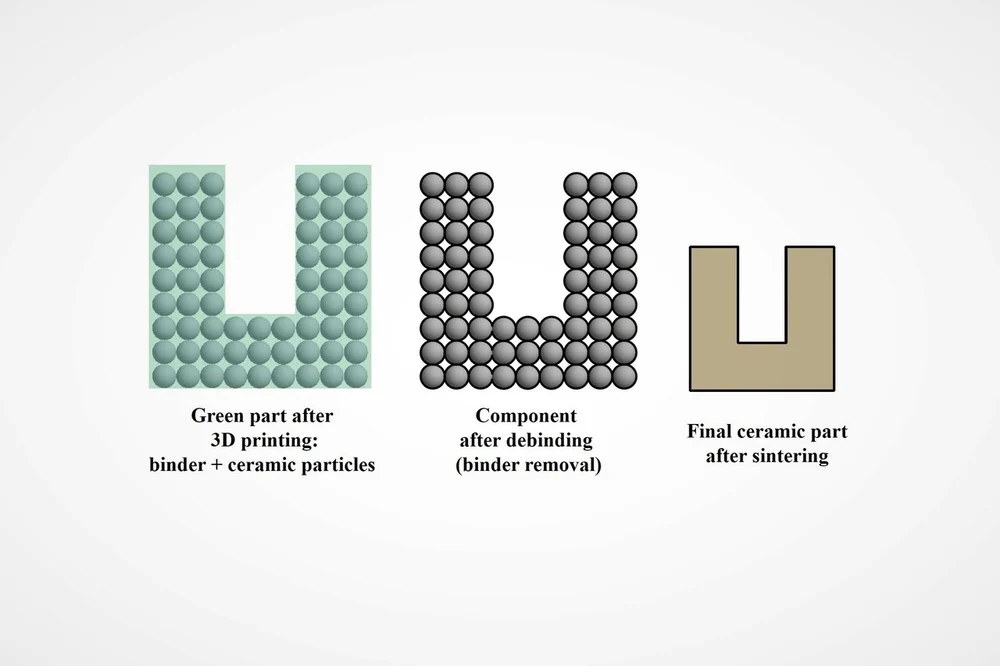
The post-processing described and illustrated above is a key factor in obtaining ceramic parts. The 3D printed green part presents a high amount of organic material to be eliminated. Thus, adequate heating rates must be employed to avoid failures, which can range from totally broken pieces and deformed parts to cracks that are invisible to the naked eye but that impair the properties of the manufactured components.
Post-processing is a time-consuming phase that may take several hours, and a lot of research has been done to optimize such a process. The duration of the entire process depends on several factors, such as part geometry, amount of binder used, thermal decomposition characteristics of the binder used, among other aspects.
Moreover, the debinding of thick sections may lead to cracks, as the thickness may interfere with the thermal decomposition process. Therefore, suppliers specify 10 mm as the maximum wall thickness of parts to be produced by ceramic vat photopolymerization.