3D printing post-processing can make your work look better and improve strength. Learn 10 methods of post-processing PLA, PETG, and more!
Almost every 3D print requires some sort of post-processing after it’s printed. There’s a lot of information and advice about post-processing 3D prints out there, but here we’ve gathered the most important techniques in one place. For each tip, we’ll clearly explain what to do and provide some tips on how to get perfect results every time.
Post-processing can improve a printed part’s aesthetics, but it can also improve the strength and other properties. Once you discover the beauty of post-processing, you’ll never want to leave your 3D prints untouched again. There are many techniques to choose from, and we’ve divided our choices into two categories: “cleaning and prepping” and “finishing”.
Without further ado, let’s dive deeper into post-processing and how to perfect your FDM prints!
CLEANING & PREPPING
We’ll start our journey into post-processing by discovering cleaning and prepping techniques, including basics such as support removal and sanding. Depending on the application of the item, these techniques are usually the first steps in post-processing, but can also be all you do, depending on how far you want or need to go.
Support Removal
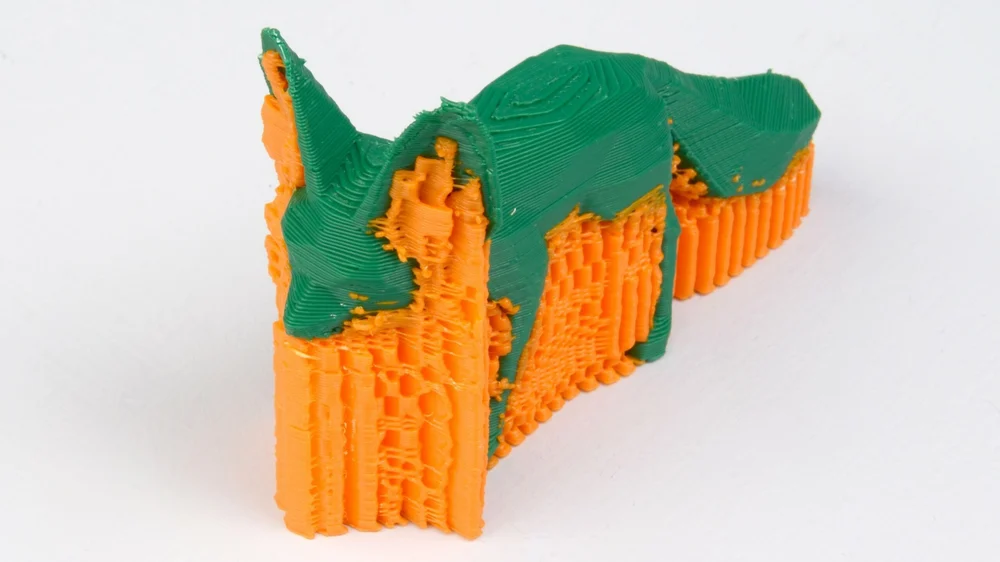
Support removal is the most basic form of post-processing. Usually, support removal doesn’t require much effort, unless there are supports in tight corners or other hard-to-reach places. Depending on what they’re made of, supports can be insoluble or soluble (able to be dissolved in water or another liquid).
Insoluble supports are made from the same material as the main part. FDM 3D printers with a single extruder can only use this type of support, as the part and its supports will be printed from the same spool of filament. Removing insoluble supports is usually done by snapping them with your fingers or cutting them with a pair of pliers.
If you’re lucky enough to have access to a dual-extruder 3D printer, you’ll be able to use soluble supports. Whereas insoluble supports can be very tricky to remove in places that are hard to reach, soluble supports can simply be dissolved by soaking the part in either water or another liquid, leaving little to no marking or residue.
Two of the most common materials for soluble supports are HIPS and PVA. HIPS is used with ABS and dissolves in D-limonene, while PVA is a great fit for PLA and dissolves in water.
PROS
- Relatively easy to do
- Doesn’t require much equipment
- Soluble supports provide more design flexibility
CONS
- Even when removed carefully, supports can leave marks
- While sometimes structurally necessary, supports don’t improve the appearance or properties of a part
3D Printing Supports – The Ultimate Guide
Sanding
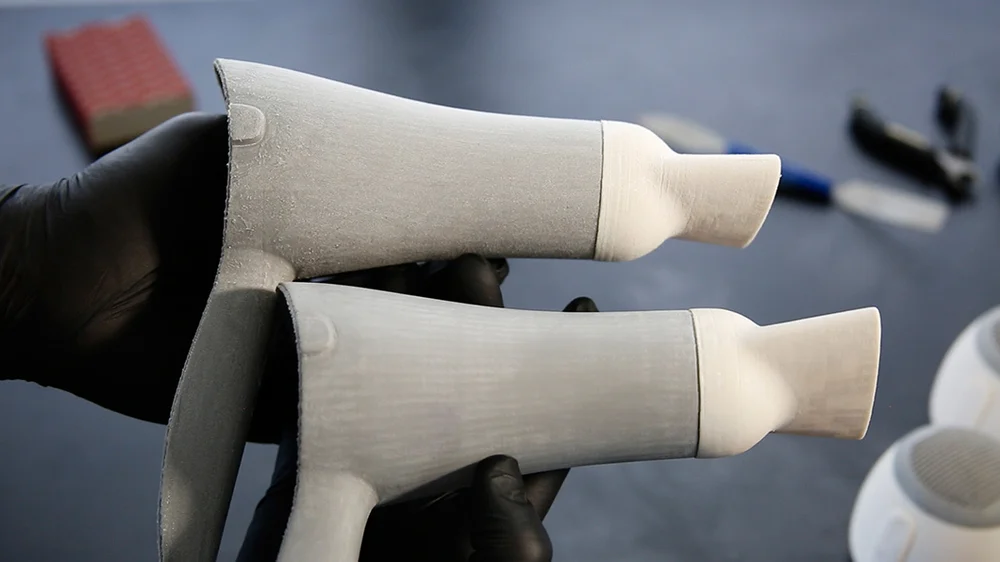
Apart from support removal, sanding is the most common form of post-processing. Generally, FDM 3D prints can have a slightly rough surface, and sanding is the easiest way to smooth it.
After printing, a part might have a few blobs left on its surface, or there might be some nasty marks remaining after you’ve removed supports. The ideal way to remove such blemishes is by using sandpaper. It’s always best to start with low-grit sandpaper (150-400) and move towards higher grit sandpaper (up to 2,000) in a few stages of sanding.
A couple of key tricks to sanding are wet sanding and circular movement. As you’re sanding the part, friction between the sandpaper and the surface generates heat, which could have a negative effect on the fine features of the print, especially with heat-sensitive filaments. To avoid this, simply wet your part before sanding to absorb any excess heat.
Especially with FDM parts, where layers are easily visible, it’s important to sand the parts in a circular motion. If you sand the parts parallel or perpendicular to the layers, you could ruin the visual appearance of the parts.
PROS
- Great prepping technique before polishing or painting
- Nicely smooths the surface
- All FDM materials can be sanded
CONS
- Can be time-consuming
- Tough to perform on small features and details
- Can affect dimensional accuracy
Welding
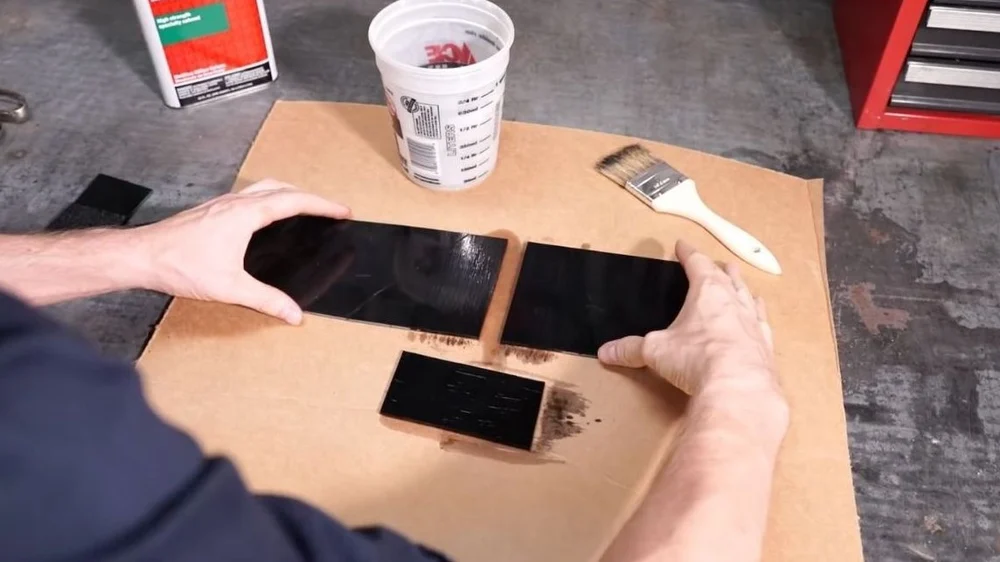
If you’d like to 3D print a large object using ABS, but the build volume of your 3D printer is too small, welding is the perfect solution for you.
Welding, in this case, doesn’t have anything to do with metals. In FDM 3D printing, welding refers to connecting ABS parts using acetone. Acetone has the ability to melt ABS, so this means that ABS parts can be joined using acetone welding.
The process is fairly simple but requires a calm hand. Apply a little bit of acetone onto the part you’d like to “glue”. This will slightly melt the plastic, and at that moment, attach the other part to the melted edge to weld them together.
PROS
- Stronger than other joining methods
- Inexpensive
- Low skill-level required
CONS
- If too much acetone is applied, the entire part can be ruined
- The weld is not as strong as the rest of the part
- Only ABS can be welded with acetone
Gluing
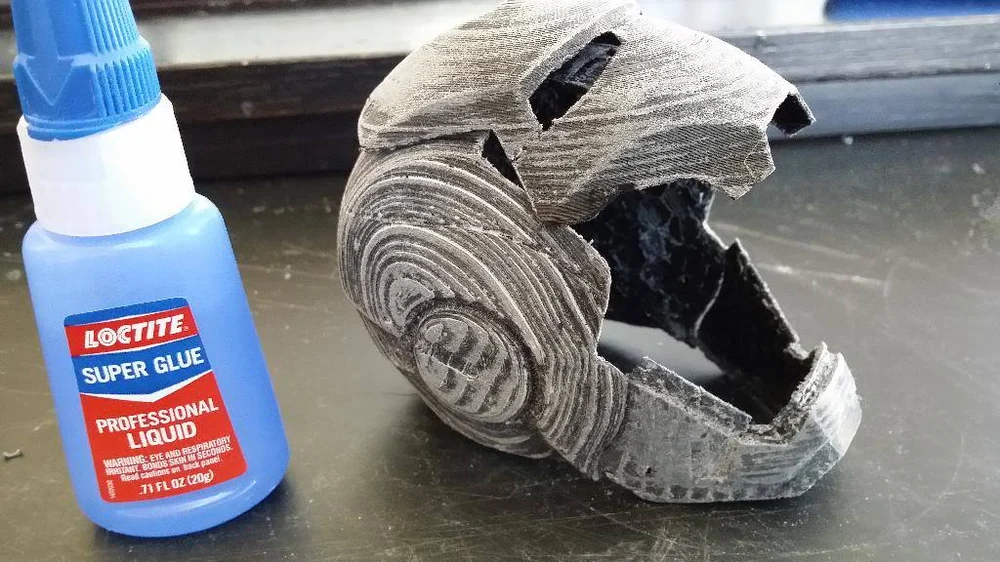
While welding is a great method of merging multiple 3D printed parts, it’s only possible with parts printed in ABS. Luckily, 3D prints made with other materials can still be joined by gluing. Similar to welding, this is generally used when something can’t be printed in a single piece due to the dimensional constraints of the printer.
PLA and PETG are examples of materials that can easily be glued together using bonding agents like super glue, or custom products like 3D Gloop!, for example.
PROS
- Works with common filaments (PLA, PETG)
- Inexpensive
- Not time-consuming
CONS
- Not as strong as welding; parts are weak at the gluing point
- Can be messy
FINISHING
Finishing techniques are the final step in 3D printing post-processing. We’ll explain how techniques such as painting, smoothing, polishing, and dipping are performed on FDM 3D prints.
The extra effort that goes into performing finishing techniques certainly pays off in the end. By applying these techniques, you’ll be able to get rid of visible layers and create the smoothest possible surface. No one will ever suspect your parts came off a 3D printer!
Priming & Painting
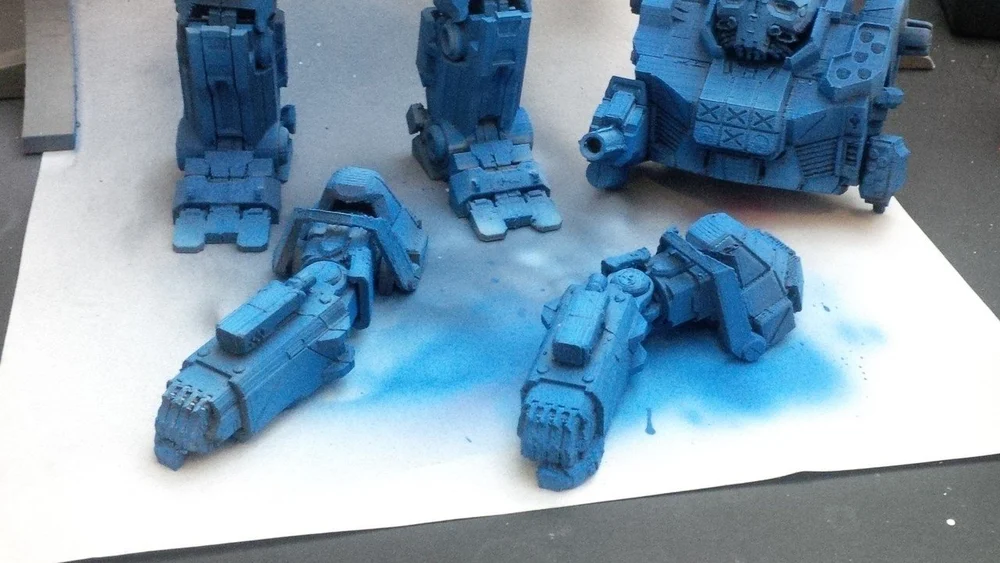
Priming is a post-processing technique that’s used for preparing a surface for painting. It simply means coating the part with either primer paint or primer spray, which acts as a base layer for the paint that will be applied later.
Before you apply the primer, it’s best to first sand your part with low- and then medium-grit sandpaper. This removes layer lines and smooths the surface. After sanding the part, apply two coats of primer, allowing it to try in between.
Once everything is dry, you can start painting your 3D print using a brush or spray. If you want to achieve sharp color intersections, using masking tape is a perfect solution.
Priming and painting are best done in a well-ventilated area or outdoors and while wearing a mask to avoid breathing in unwanted fumes.
PROS
- Enhances the look and feel of a part
- Provides a smooth surface finish
- Works on all FDM materials
CONS
- Relatively time-consuming
- Can be costly due to the equipment needed (paints, sprays, sandpaper, masks, and brushes)
- Some skill is required to achieve great results
Smoothing
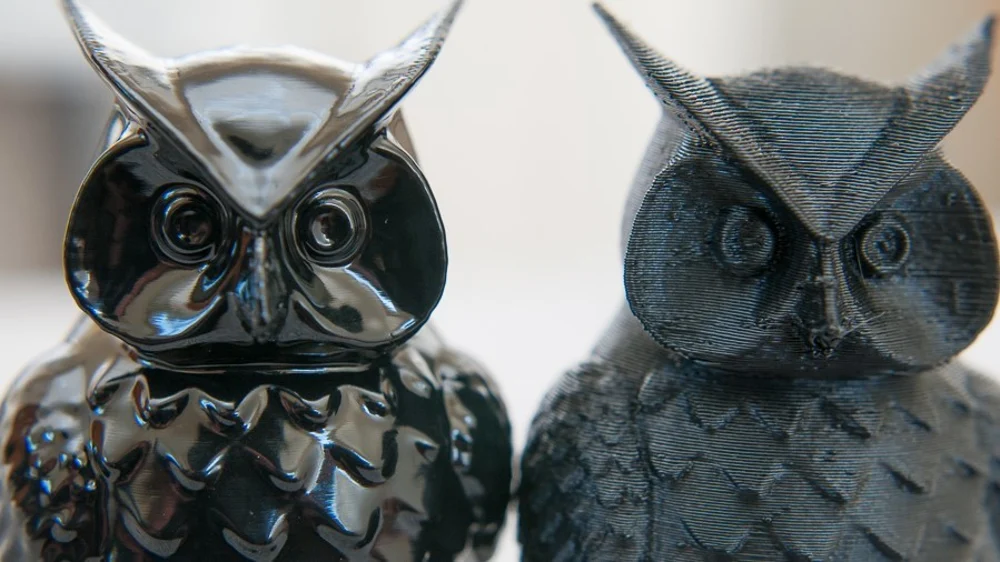
Smoothing is a popular post-processing technique, especially for ABS prints. Acetone has the ability to melt ABS and therefore smooth away the layer lines visible on a part’s surface.
The simplest method is to pour acetone into a large container (which can be plastic, but glass is recommended) then place your prints on a platform above the acetone. Close the container lid for 10-20 minutes so that the vapor can melt the outer layer of the parts. You want the vapor to still be able to escape the container rather than building up, so if the lid is one that seals tightly, consider drilling a few holes beforehand.
If you don’t have an appropriate container, you can apply small amounts of acetone with a brush onto the surface of your 3D prints. But a warning: Acetone is highly flammable and can explode. Therefore, proper precautions should be followed while carrying out either of these processes. Even just the fumes can be harmful if inhaled, causing irritation and other negative effects. Always work in a well-ventilated area and make sure to wear gloves and a mask.
As for PLA, smoothing can’t be done with acetone as it doesn’t melt it, and it could even destroy the entire print by making it “gummy”. PLA can be smoothed with chemicals like THF or MEK, but the results won’t be nice as acetone-smoothed ABS.
In case you have some 3D prints made from PVB filament, you can use isopropyl alcohol to perform the smoothing.
PROS
- Smooth and shiny surface
- Acetone is relatively cheap
- Quick to achieve
CONS
- Acetone smoothing is only possible for ABS prints
- Dimensional accuracy can be compromised
- Risk of warping for larger prints
Polishing
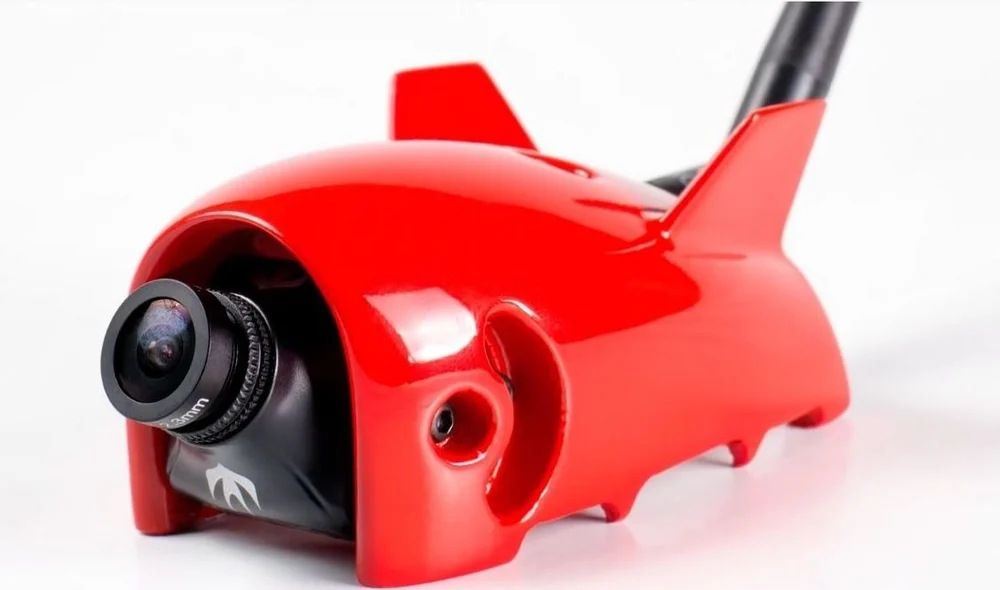
This 3D printing post-processing technique is used to achieve the smoothest possible surface. Polishing 3D prints can be done with plastic polishers and tools available at almost every hardware store. A microfiber cloth and a plastic polisher are all you need, but if you’ve got the enthusiasm and a few more dollars, using a Dremel tool will make this process even easier.
Before a part can be polished, it needs to be sanded properly, finishing with the finest sandpaper. After sanding, rinse your parts and make sure there are no particles left. If you’re using a cloth, apply the polisher to the sanded part and move the cloth in a circular motion until you’re satisfied with the result. A Dremel buffer will do much of the work for you, but make sure it’s moving evenly along the surface.
PROS
- Produces smooth and mirror-like surface
- Inexpensive, unless you invest in a Dremel
CONS
- Dimensional accuracy can be compromised
- Moderate skill-level required
Hydro Dipping
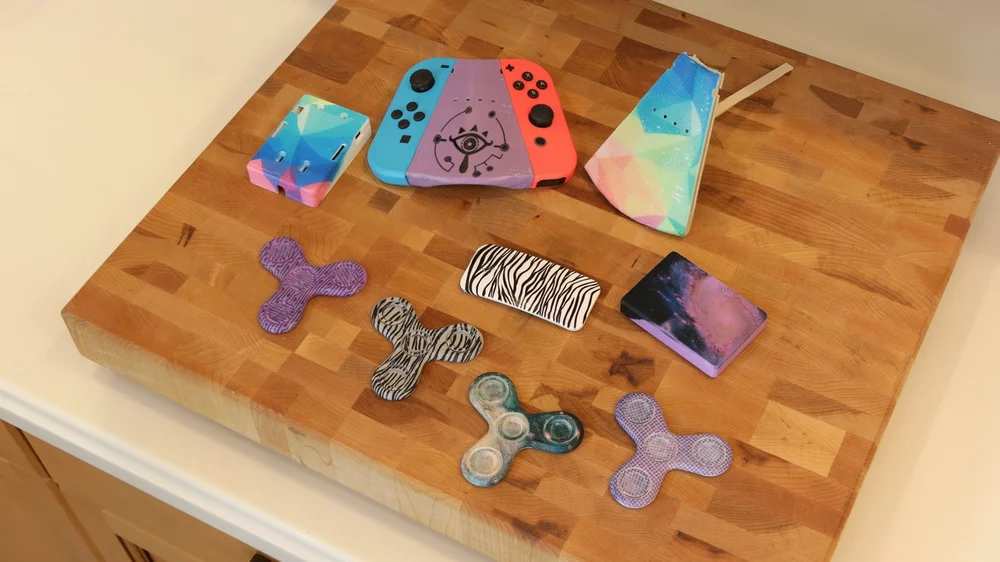
Though typically used on a large scale for industrial products, small-scale hydro dipping can easily be applied to 3D printed parts for a great look. Also known as water transfer printing or water transfer imaging, hydro dipping is a process of applying printed graphic designs to solid objects using special water transfer paper. This paper has one side made from PVA, onto which graphics are printed with an inkjet printer.
Once that’s done, find a container big enough to accommodate your part and fill it with hot water. Remove the back of the paper so that you’re left with only the clear PVA with a printed graphic. Carefully lay it down into the water and wait for the PVA to dissolve so that your graphic is floating on its own.
Then, slowly submerge the part into the graphic at a 45-degree angle. You can either hold it with one hand or attach a stick to be able to work from a distance. Once the part is fully submerged, shake it a few times and you’re all set to pull the finished part out of the container.
Hydro dipping is only used for enhancing the aesthetics of the object and does not change the feel or any dimensional properties. However, the possibilities are infinite with the graphics you can add to a part, so this is one of the best ways of making your 3D prints eye-catching.
If you need some more support, this Instructable is very helpful.
PROS
- Dimensional accuracy is maintained
- Complete design freedom
- Works on all materials
CONS
- Paper transfers can be expensive
- A few attempts are needed to get the feel for performing this technique
- Not resistant to scratches or other surface damage
Epoxy Coating
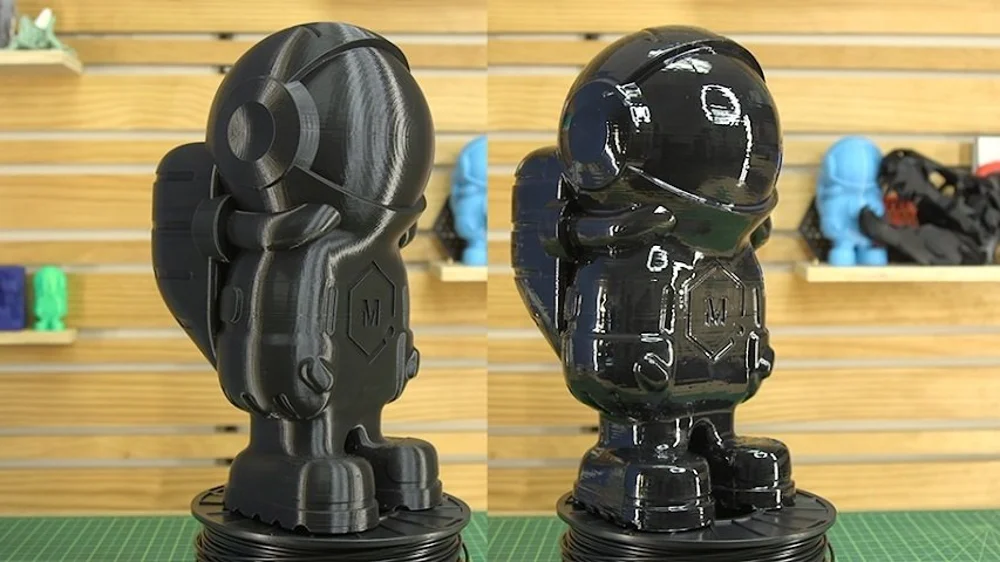
Epoxy coating your 3D prints improves strength, but it can also seal porous parts of the print and act as a great protective layer overall. The epoxy coat consists of two different chemicals: the epoxy resin itself and a hardener.
When you buy chemicals for epoxy coating applications, the brand you choose will provide mixing instructions. The ratio of hardener and resin must be correct to achieve good results, or you could end up with a coating that never dries! Once you’ve got the mixture ready, it’s time to apply it to a 3D printed part.
We suggest using a foam applicator or sponge to apply the coating. When you’ve done the first coat, leave the part to dry, and then sand it with either 1,000- or 2,000-grit sandpaper. With that done, you’re ready to apply the second and final coat of epoxy.
If you’d like to give epoxy coating a try, there are 3D-printing-specific epoxy-coating products, such as XTC-3D.
PROS
- Improves the strength of the part
- Adds a durable protective layer
CONS
- Layer lines won’t be gone entirely
Electroplating
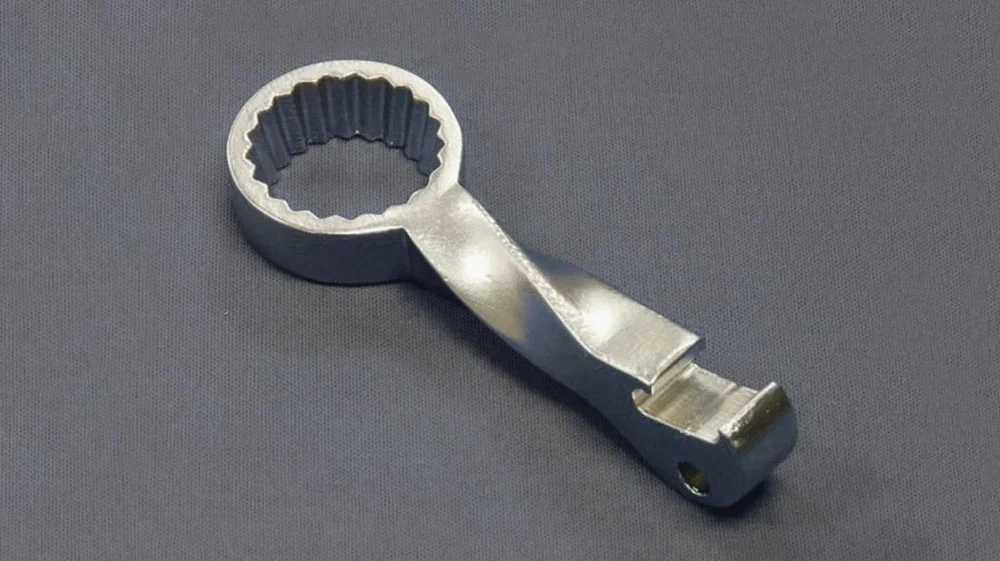
Electroplating is a process that adds a metal coating to other metals or parts with a conductive surface. It’s a great post-processing technique that can significantly improve both strength and visual appearance. The process itself can seem complicated at first, but it’s not as technical as it seems.
Electroplating is basically transferring a metal coating from one metal to another (or a part with a conductive surface). Electroplating is possible thanks to a chemical process called electrolysis. Two main tools for electrolysis are a power source (battery or rectifier) and an electrolyte.
The electrolyte is a mixture of a metal salt (of the metal that you want to coat your part with), an acid, and water. An electric current is needed to initiate the reaction between the cathode (connected to the power source’s negative pole) and the anode (positive pole).
The anode is made from the metal you want to use as coating, and the part to be plated acts as the cathode. Both the anode and the cathode are then dipped into the electrolyte.
The salt in the electrolyte contains cations and anions (positively- and negatively-charged ions), which need to move to the cathode and anode to enable the metal transfer. Turning on the power source adds electric current into the electrolyte, causing the anions to move to the anode and the cations to move to the cathode.
Let’s say you’d like to coat your 3D printed part with copper, so the electrolyte you’ll be using is copper sulfate (CuSO4). Once the electric current starts, the Cu2+ cations move to the cathode and coat your part.
The most common metals used in this process are copper and nickel, but it can also be done with materials such as brass, gold, silver, chrome, and others.
Because 3D printed parts are plastic and non-conductive, You’ll need to properly sand them and apply conductive paint before attempting electroplating.
PROS
- Parts become stronger and are conductive
- If done properly, dimensional accuracy won’t be compromised
- Visual appearance is improved
CONS
- High skill-level required
- Can be dangerous if you’re not wearing safety equipment (gloves and glasses)