At FacFox, we’re dedicated to pushing the boundaries of 3D printing technology, especially when it comes to enhancing the properties of titanium through innovative anodizing techniques. In this post, we’ll explore the three main types of titanium anodizing and their unique benefits for a variety of applications.
What is Titanium Anodizing?
Titanium anodizing is an electrolytic finishing process that enhances the surface properties of titanium by manipulating its oxide layer using electric current. In this process, the titanium item serves as the anode (positive electrode) of an electrolytic cell, hence the term “anodize.”
Types of Titanium Anodizing
There are two commonly used types of titanium anodizing: Type 2 and Type 3. Type 1 is less common and primarily used for specialized high-temperature treatments.
Type 2 Anodized Titanium – Wear Resistance
Type 2 anodizing (dark anodizing) focuses on enhancing wear resistance, protecting the metal surface against friction and wear. When untreated titanium parts rub against each other, they produce titanium dust, which is undesirable, especially for orthopedic implants. Type 2 anodizing provides a wear-resistant surface, preventing seizing or friction between sliding titanium surfaces.
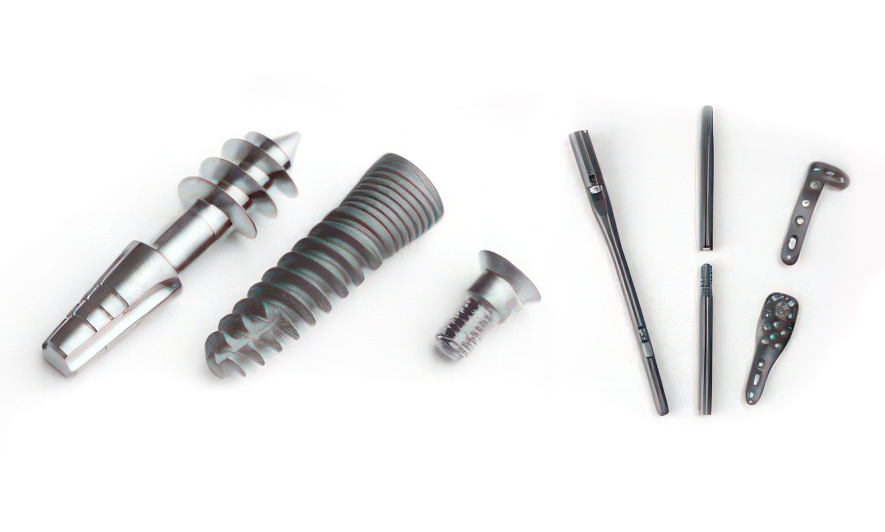
Key Features
- Wear Protection: Prevents titanium parts from producing dust due to friction, crucial for applications like orthopedic implants.
- Reduced Friction (Lubricity): Improves joint mobility in medical devices by reducing friction.
- Compliance: Adheres to AMS 2488 specifications, ensuring compatibility with aerospace standards and applications.
- Corrosion Resistance: Resists corrosion from saltwater and humidity, and withstands extreme temperatures from -70°F to 260°F.
- Distinctive Gray Color: The gray finish makes Type 2 anodized parts easily distinguishable from stainless steel or color-anodized titanium.
Post-Processing
- Bead Blasting: Necessary to remove the white film that forms after anodizing, resulting in the characteristic gray finish.
Type 3 Titanium Anodizing – Color Titanium
Type 3, or titanium color anodizing, is widely used for quick visual identification of parts, especially in the medical field.
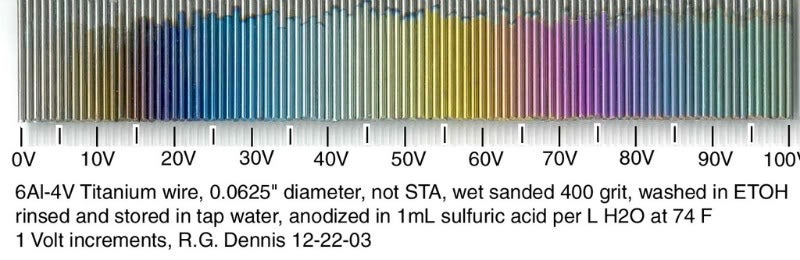
Key Features:
- Visual Identification: Enables easy recognition of parts by color, particularly useful in medical procedures.
- Color Coding: Used for items like bone screws and fixation plates, facilitating quick identification during surgeries.
- Versatile Applications: Though less common in aerospace, it can be used for visual identification in complex assemblies and is popular in jewelry manufacturing.
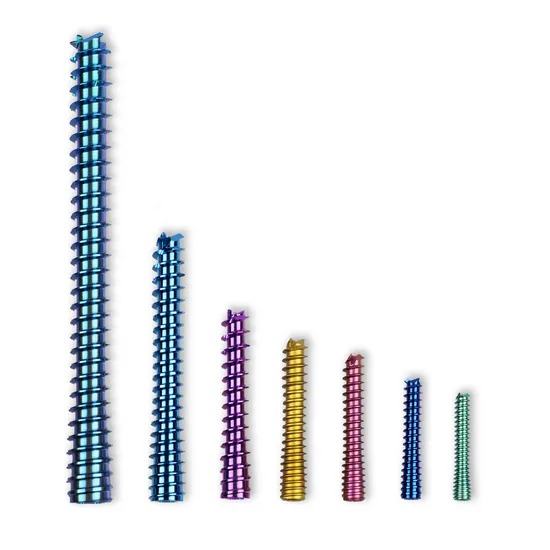
Challenges:
- No Industry Standard: Unlike Type 2, Type 3 anodizing lacks a standard specification like AMS 2488. This can make color matching across batches challenging.
- Process Validation: Manufacturers must establish their own process validation, often consulting experts to ensure consistency and quality.
How Does Titanium Anodizing Work?
Anodizing titanium is an electrochemical process that combines electricity and chemistry to manipulate the oxide layer. The titanium part, acting as the anode, is immersed in an electrolyte solution (e.g., trisodium phosphate).
Applying electrical current causes water molecules to hydrolyze, splitting into hydrogen and oxygen. The oxygen forms an oxide layer on the titanium surface, which can be manipulated to achieve different properties and colors.
How Does Titanium Color Anodizing Work?
A titanium anodizer machine creates an “illusion of color” through an interference phenomenon. Light reflects off the oxide layer and the underlying titanium at different angles, causing wavelengths to cancel out or combine, resulting in perceived colors. Unlike aluminum anodizing, no dyes are used, enhancing the biomedical safety of the finished part.
Oxide Layer Development
- Natural Growth: In atmospheric conditions, the oxide layer grows to about 1-2 nanometers initially and can reach 20-25 nanometers over time.
- Controlled Anodizing: Colors like bronze (300-350 angstroms) and green (500-550 angstroms) are achieved by controlling the oxide layer thickness.
How To Do Type 3 Color Titanium Anodizing
The titanium part is immersed in an electrolyte solution, commonly trisodium phosphate, forming an alkaline solution.
Voltage determines the color, ranging from 15-110 volts. Higher voltages create thicker oxide layers and different colors.
Amperage controls the time required for anodizing. Higher amperage speeds up the process but may risk color inconsistency.
In summary, titanium anodizing, particularly with advanced techniques at FacFox, enhances both the functionality and aesthetics of titanium parts.
Whether for wear resistance or vibrant color finishes, our anodizing services provide the precision and quality needed for high-performance applications.
Discover the transformative power of titanium anodizing with FacFox. Contact us today to learn more!