In the world of 3D printing, the introduction of green laser technology has revolutionized the industry, particularly in the realm of metal printing. Among the various metals, pure copper has emerged as a highly sought-after material due to its exceptional electrical and thermal conductivity. However, the 3D printing of pure copper poses significant challenges due to its high reflectivity and thermal conductivity.
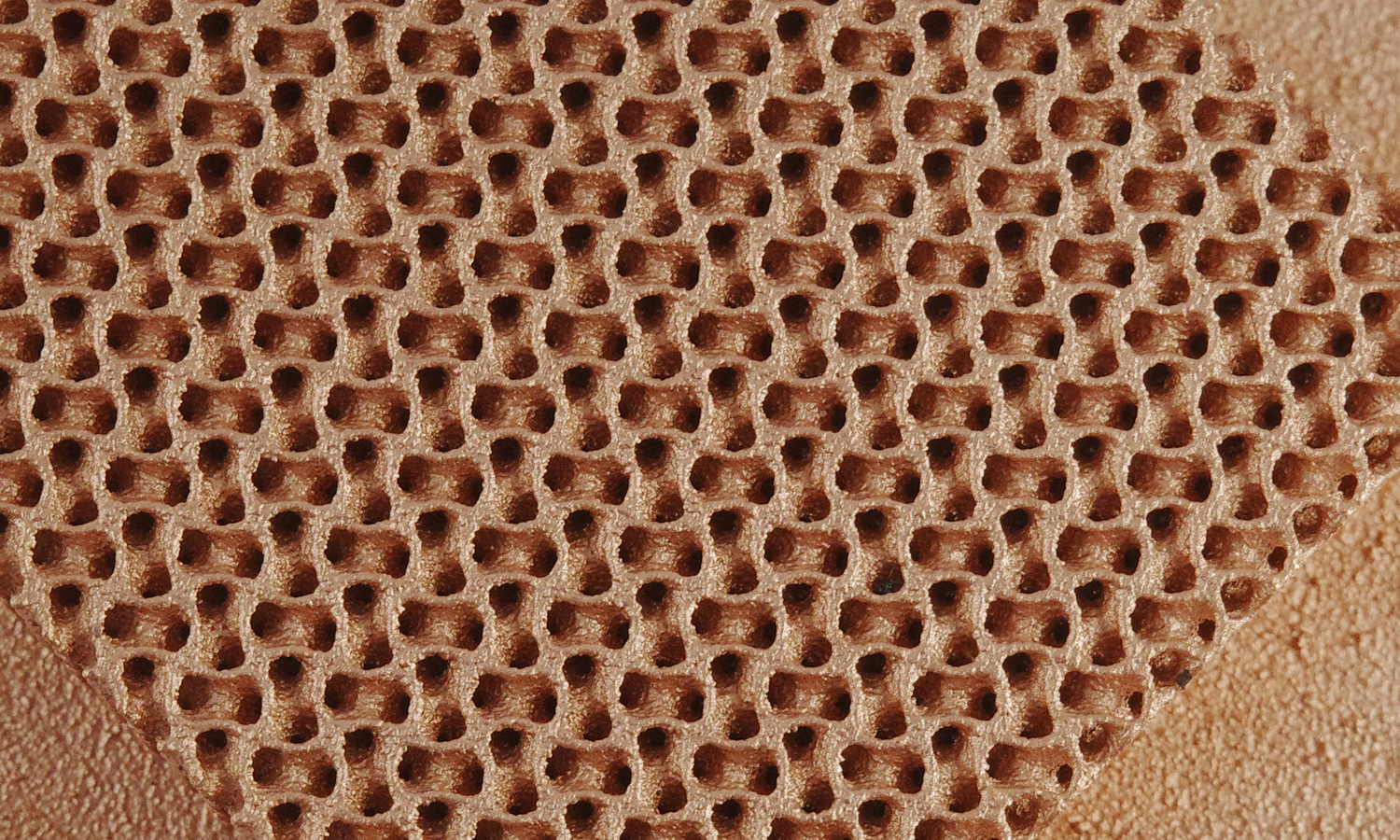
The Challenges of Pure Copper 3D Printing
- High Reflectivity and Thermal Conductivity: Traditional SLM (Selective Laser Melting) technology struggles with pure copper, as its high reflectivity and thermal conductivity make it difficult to maintain a consistent melt pool, leading to low forming efficiency and poor metallurgical quality.
- Rapid Heat Dissipation: Pure copper cools rapidly during the printing process, causing issues such as warping and delamination, which affect the overall quality of the printed parts.
- Material Purity and Microstructure Control: Developing pure copper printing materials with good flowability, low shrinkage, and high stability is crucial. Optimizing material formulations and printing parameters is necessary to achieve excellent mechanical, physical, and chemical properties.
- Cost and Post-Processing: High-performance pure copper materials are expensive, and the complex post-processing steps, such as debinding and sintering, further increase production costs and difficulty.
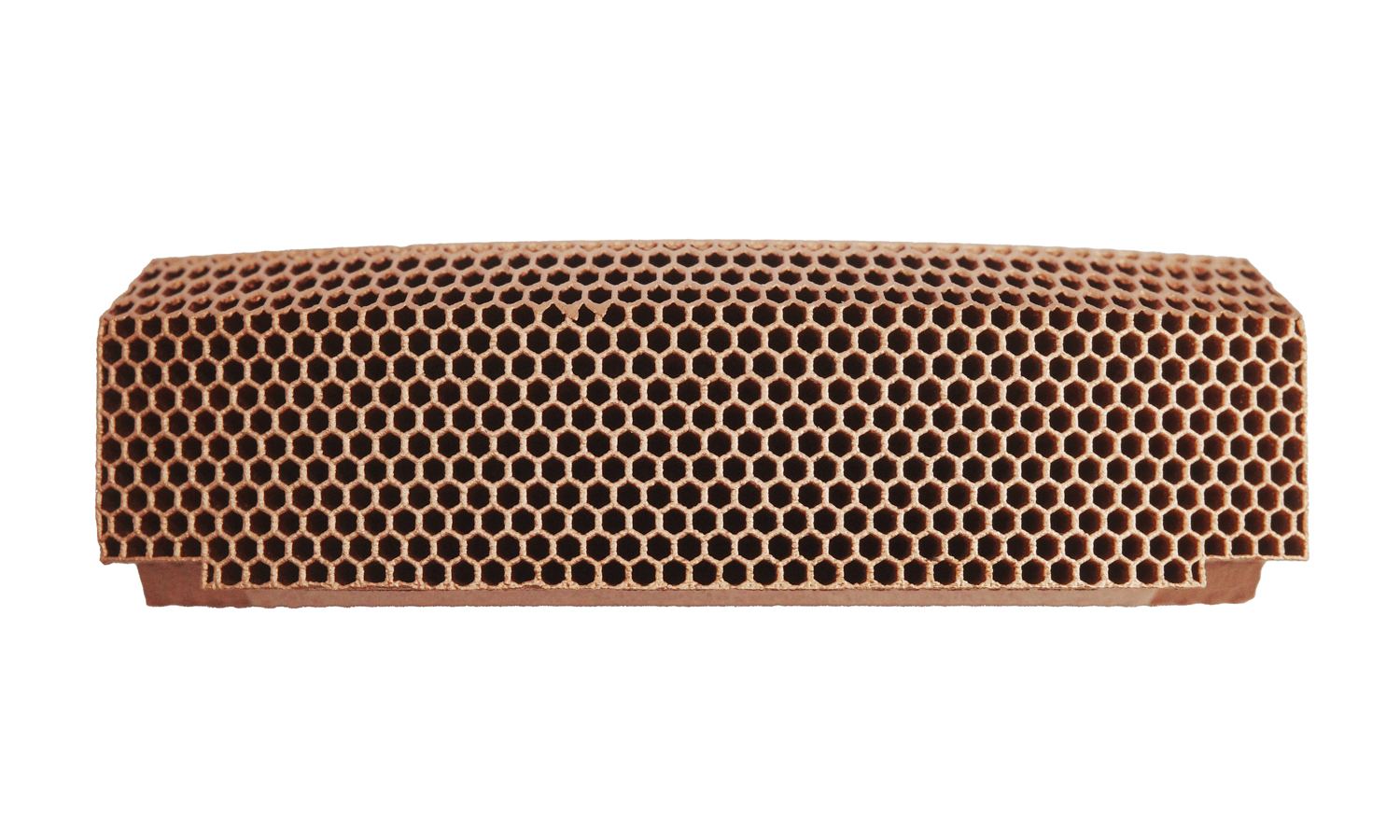
Innovative Solutions
The advent of green laser technology has provided effective solutions to these challenges:
- Green Laser: Utilizing green lasers significantly enhances the detail resolution and capability of additive manufacturing with pure copper, reducing recoil pressure and defects.
- Indirect 3D Printing: Techniques like PEP (Powder + 3D Printing) involve printing a green body first, followed by debinding and sintering, avoiding the high thermal conductivity and reflectivity issues associated with high-energy laser beams.
- Electron Beam Melting (EBM): EBM technology effectively handles pure copper materials, offering high energy utilization and production efficiency.
- Binder Jetting: Although less common for pure copper, binder jetting has proven successful in metal injection molding, indicating its potential for high-density and high-conductivity pure copper parts.
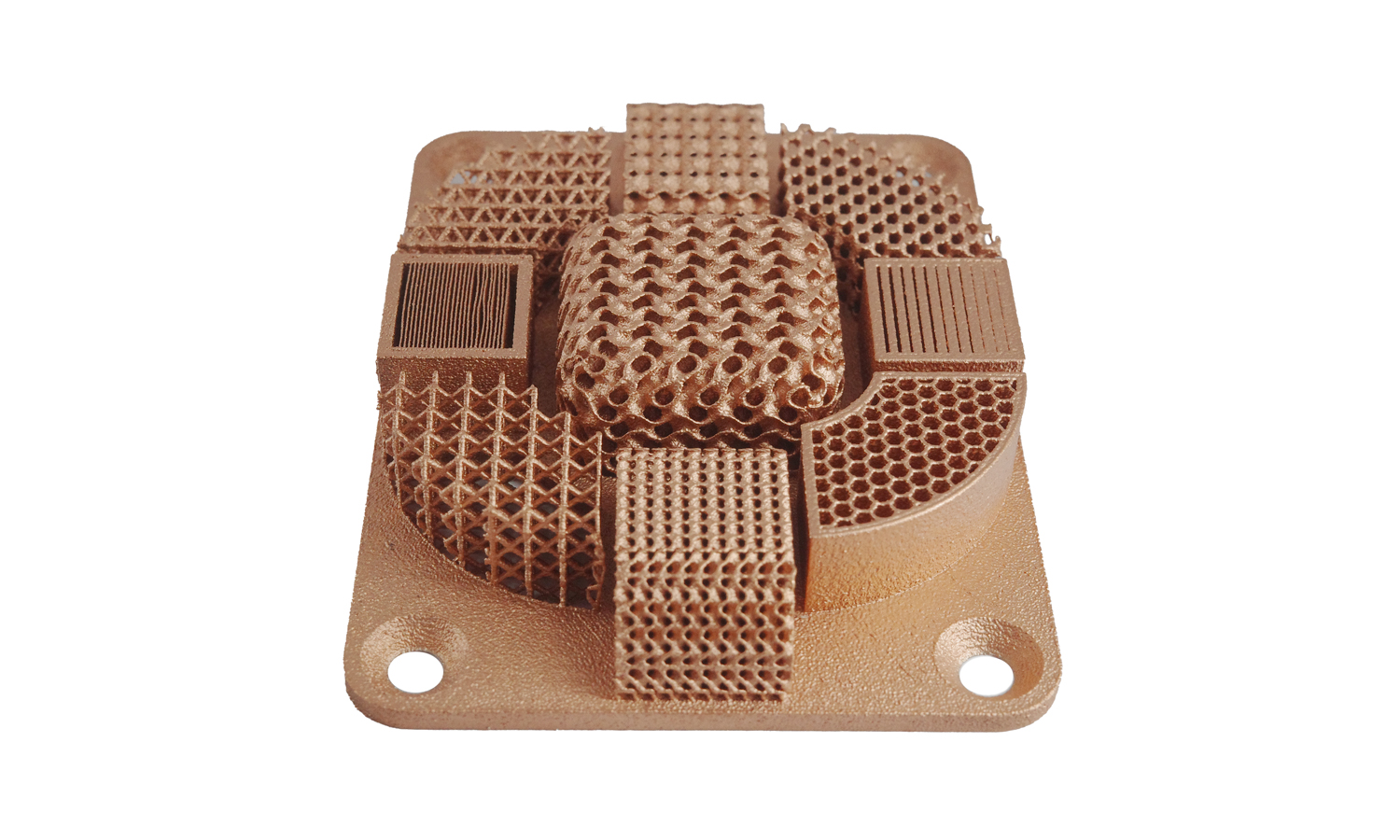
The Role of Green Laser in Metal 3D Printing
Green laser technology has made significant strides in metal 3D printing, particularly for high-reflective materials such as copper and precious metals.
- Why Green Laser? Green lasers have shorter wavelengths (510nm-560nm), which result in higher absorption rates for most metals compared to infrared lasers (1064nm). This translates to a smaller heat-affected zone, concentrated energy, and the ability to achieve high-precision, high-performance forming.
- High Energy Utilization: Green lasers minimize material reflection, reduce melting splatter, and ensure stable, continuous operation.
- Copper Absorption: With an absorption rate close to 40%, green lasers are nearly eight times more effective than near-infrared lasers for printing high-reflective metals like copper.
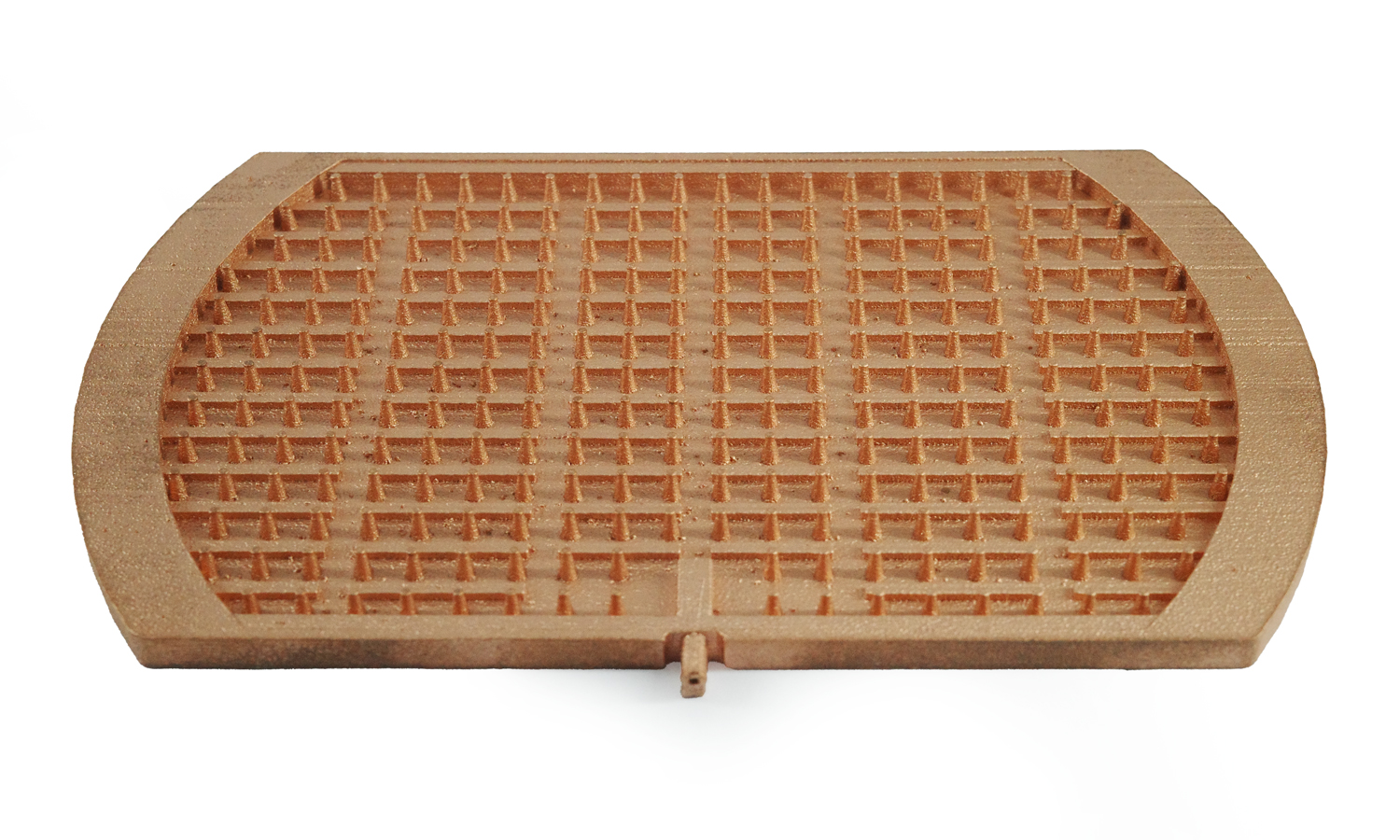
FacFox’s Metal Printing Excellence
FacFox stands at the forefront of green laser 3D printing, equipped with advanced machines like the XH-M160G and XH-M350G. These machines are designed for pure copper and copper alloy metal printing, featuring 532nm single-mode continuous green fiber lasers with customizable power options (500W, 700W, 1000W).
- XH-M160G: This printer offers a build volume of 160x160x200mm, making it ideal for creating intricate, high-quality pure copper components.
- XH-M350G: With a larger build volume of 350x350x500mm, this printer meets the demands for larger and more complex parts, providing efficient solutions for high-reflective materials.
Feature | XH-M160G | XH-M350G |
---|---|---|
Build Volume | 160 x 160 x 200 mm | 350 x 350 x 500 mm |
Laser Type | 532nm single-mode continuous green fiber laser | 532nm single-mode continuous green fiber laser |
Laser Power Options | 500W, 700W | 500W, 700W, 1000W |
Suitable Materials | Pure copper, copper alloys | Pure copper, copper alloys |
Advantages | Ideal for intricate, small-scale parts | Suitable for larger, more complex parts |
Applications | Electronics, aerospace, thermal management | Electronics, aerospace, thermal management |
Unique Features | High precision, efficient for small items | Larger build volume, versatile for various sizes |
Applications and Future Prospects
Green laser technology’s unique advantages in metal 3D printing have opened new possibilities in various industries:
- Copper and Copper Alloys: Enhanced printing quality and efficiency for applications in electronics, aerospace, and thermal management systems.
- Precious Metals: Effective 3D printing of gold, platinum, and other precious metals, overcoming the low absorption rates of traditional infrared lasers.
- Other High-Reflective Metals: Suitable for titanium alloys, stainless steel, and high-temperature alloys, expanding the scope of additive manufacturing.
As green laser technology continues to mature and become more widespread, its potential for large-scale applications in diverse fields grows. FacFox’s commitment to leveraging this technology ensures that they remain at the cutting edge of metal 3D printing, providing innovative solutions and high-quality products to meet the evolving needs of the industry. Contact us today!