As additive manufacturing (AM) continues to industrialise, manufacturers will need effective strategies to manage and scale their AM workflows. One of the ways to achieve this is with an Additive Manufacturing Execution System (MES).
Additive MES is workflow software that helps manufacturers manage their AM operations by enabling greater traceability, better data insights, and establishing best practice processes across their entire AM workflows.
In today’s article, we’ll explore:
- What Additive MES software is,
- The key benefits of Additive MES software,
- How to determine whether it’s the right time for your company to invest in the software.
What is an Additive Manufacturing Execution System?
In today’s competitive landscape, manufacturers are under pressure to produce products faster, more efficiently and more cost-effectively.
As a result, companies are looking for ways to implement lean processes and achieve greater efficiency across their manufacturing operations.
Increasingly, manufacturers are adopting additive manufacturing (AM) to help meet these objectives.
As a digital manufacturing technology, AM is enabling companies to develop and manufacture products with more complexity, and greater customisation. And the trend of AM adoption only looks set to continue — a recent report by EY shows that 46 per cent of companies plan to adopt AM for end-part production by 2022.
As AM industrialisation gains traction, the need for a system to help successfully execute, coordinate and manage AM operations is becoming critical.
In traditional manufacturing, these functions are typically fulfilled by Manufacturing Execution Systems (MES). MES is software used to support the execution of manufacturing operations. It provides real-time production visibility, enabling proactive decision-making, resource management and optimised planning and scheduling.
However, while MES solutions have been developed for traditional manufacturing processes, they tend to be highly limited when it comes to managing the unique requirements of AM.
It is well known that additive manufacturing requires a very different approach to design. But AM also requires a different approach to production and process management. For example, the steps needed to manage post-processing operations, prepare builds for print and conduct quality assurance can drastically differ from conventional manufacturing processes.
Because of this, AM has seen the rise of specialist MES software in recent years, developed specifically for additive manufacturing processes.
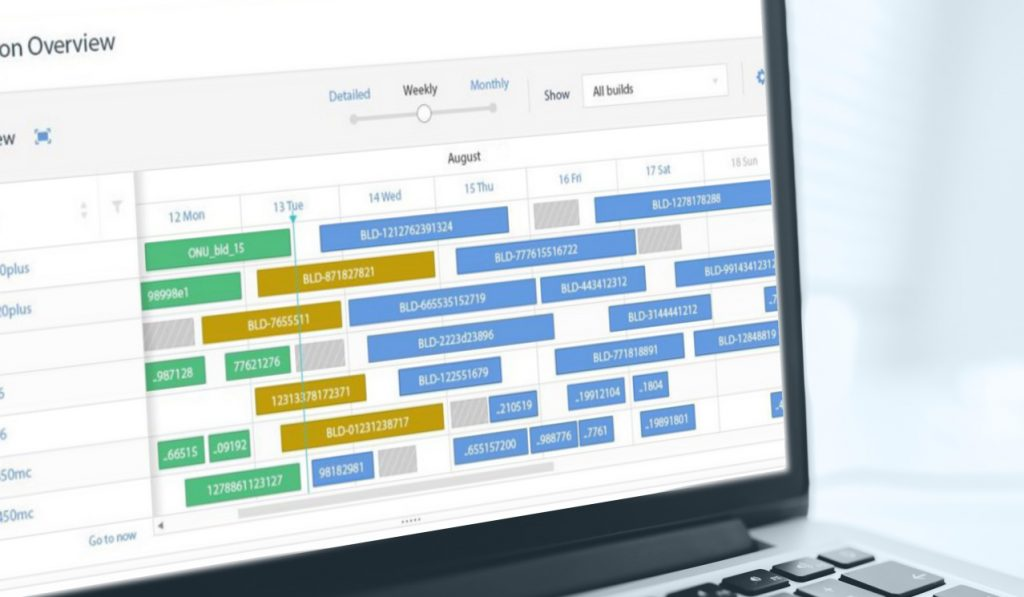
Additive MES software also allows companies to track and document all of its AM production data, such as production costs, material usage and order turnaround time, thus enabling greater process control and maximised efficiency.
5 key benefits of Additive MES software
As manufacturers look to use AM for production, this will mean coordinating their operations across supply chains and production locations. Achieving this level of coordination requires an integrated, end-to-end management process that can only be achieved with workflow software.
Below, we look at 5 key benefits of Additive MES software in more detail:
1. Efficient, automated workflows
Additive MES helps to replace spreadsheets and manual processes with streamlined, digital workflows.
When AM operations expand, collecting data and scheduling production using manual processes can create a number of bottlenecks, including a lack of visibility and the potential for human error.
With workflow software in place, manual, disparate processes can be automated and linked together on a central, digitalised platform. This, in turn, ensures a reduction in manual labour and greater process efficiency across the digital thread.
2. Real-time visibility and traceability
‘Traceability is also about being able to track and document quality. And when it comes to AM, this not only includes the printing of the part, but also all the other steps involved, such as post-processing, 3D data acquisition or preparation’
Timm Kragl, the Senior Consultant at Phanos GmbH
Additive MES software provides complete visibility into the AM operations across an organisation.
It replaces fragmented systems like spreadsheets and standalone databases with a centralised platform that connects the top floor and the shop floor. This visibility and connectivity is particularly useful for companies operating multiple production centres.
Additionally, Additive MES software enables an organisation to track AM production data, such as machine usage, production output, material consumption and time to repair.
For example, an organisation can operational visibility could come in the form of accessible, real-time dashboards. With this, production management teams are better able to track KPIs, identify any potential bottlenecks and take a deeper dive into the key factors that are driving productivity.
3. Scalability
As an organisation’s AM operations grow, it will need workflow software that is flexible enough to accommodate this growth and respond to the evolving needs of the business.
The right Additive MES is one that enables an organisation to easily scale its operations and successfully accommodate an increase in production volumes.
4. Standardised processes
Workflow software helps to establish standardised AM processes within an organisation and across the supply chain.
A robust Additive MES platform establishes a logical sequence of process steps and ensures that everything needed is correctly in place, is configured and set up correctly. In this way, an MES provides active quality management, establishing a set of procedures and best practice processes to ensure operational efficiency and continuous improvement.
Furthermore, manufacturers, particularly in high-value industries like aerospace and medical, must establish a system of controls and documentation to ensure that standards are met. Additive MES software facilitates this by providing a centralised, standard platform that enables a company to achieve the maximum level of traceability.
5. Reduced operational costs
The increased degree of automation enabled by Additive MES results in a streamlined workflow, which helps to reduce operational costs.
For example, job status monitoring is often done manually, with an operator manually checking off jobs in a log as they finish. Automating this process results in savings in labour related costs, as well as enables operators to prioritise other, higher-value tasks.
Another example is using Additive MES to track material consumption and thereby reduce wastage. In this way, Additive MES makes it possible to control costs and optimise production.
Why should my organisation consider Additive MES software?
When adopting AM for production, it’s not uncommon for companies to face a lack of connectivity and traceability within the AM workflow. This is often complicated by a lack of connection between the top floor and the production floor.
An additional challenge lies in scaling AM production. 3D printing hundreds or thousands of parts per month requires the right software architecture to effectively manage the ever-increasing workflows.
Additive MES software helps to establish a scalable operation for high-volume production. With Additive MES software in place, a production manager can not only schedule jobs more efficiently but also identify any potential bottlenecks before they become critical. This, in turn, enables complete visibility of real-time operations.
By implementing an Additive MES, companies can also track and document data throughout the production workflow, enabling stakeholders to access key information at any stage of the process. Armed with this historic and real-time data, manufacturers are able to react faster to any operational bottlenecks.
At what stage should my organisation consider Additive MES software?
Since successfully adopting AM for production requires data, traceability and automation, workflow software should be a core element of your company’s additive manufacturing strategy.
This means that you should begin to consider in which capacity you’ll be using the software at a relatively early stage, in order to be able to expand more quickly.
Below are a few tips on how you can assess whether it’s the right time to invest in Additive MES software:
1. You need more traceability across your AM operations
‘Where Additive MES software is really necessary is when traceability and transparency become key priorities for the company.’
Timm Kragl, Senior Consultant at Phanos GmbH
With an increasing amount of orders and production jobs to keep track of, it can be a struggle to maintain visibility and accountability. This challenge becomes even more acute when separate production centres lack clear visibility into each other’s operations.
MES software can eliminate this by offering full visibility and accountability for each stage of the AM workflow. It integrates all files, orders, statuses and lead times within a single system, allowing the workflow to be easily monitored and adjusted as needed to meet objectives.
2. You plan to scale your AM operations
As you progress in your AM journey, your long-term planning will inevitably involve strategies to add more machines and scale your AM operations in due course.
Expanding your AM operations will require you to optimise your workflow management accordingly to support the growth. This will involve establishing the right software architecture to be able to process the increased amount of orders.
At this stage, you’ll likely need to invest in an Additive MES solution that can accommodate your needs as your operations expand.
3. You’re operating multiple production sites
If your AM operations span multiple production sites, you will need to consider an MES platform to provide visibility and collaboration across these locations.
Additive MES software establishes a centralised way to manage operations across multiple sites. It provides a standardised management process that can be deployed multinationally. For example, Additive MES software features a standardised interface for ordering, thus optimising the order management process and facilitating better communication between stakeholders.
Furthermore, you may have tasks like post-processing jobs that you outsource to a supplier or another internal production centre located. This process can be difficult to coordinate in real-time, resulting in inefficiencies. In such a scenario, Additive MES software can provide a platform to integrate and engage with your network of suppliers.
‘Be thorough in analysing what your process is currently lacking and how you may be able to fill that gap with software.’
Timm Kragl, Senior Consultant at Phanos GmbH
Why do I need Additive MES software if I already use ERP software?
Many organisations using AM already rely on enterprise software such as Enterprise Resource Planning (ERP) to manage key areas of their operations. However, ERP leaves many gaps when it comes to managing shop floor execution and resources. Essentially, ERP manages key areas of the entire company, like HR, supply chain, logistics, and covers the long-term strategic planning.
While Additive MES software may appear to have overlapping functionality with ERP systems, it primarily focused on the real-time execution of the AM production processes. Central to an MES is the “execution” aspect, versus “planning”, as in Enterprise Planning.
Tasks such as request management, order pricing and scheduling of 3D printers are all handled by Additive MES software. It allows manufacturers to connect manufacturing operations to the entire company.
Additive MES can and should be integrated with ERP, and other enterprise software, to encourage the seamless flow of data between different areas of an organisation.
Additive MES software: Taking full control of 3D printing workflows
Managing AM operations, especially as they expand, can be a challenge. Additive MES & workflow software is becoming an essential piece to this puzzle, as it can support scalability and compliance, helps to reduce manufacturing costs and improve the overall efficiency of the AM process.
For a company looking to take full advantage of AM, adopting an MES platform is no longer an option – it is the key to future-proofing additive manufacturing operations for competitive advantage and profitability.