FacFox’ quoting system provides you with manufacturing analysis with each quote. You can upload a 3D CAD model in one of many different file formats that are accepted. A quote is generated and sent back to you within hours. You not only get configurable pricing, you also get valuable feedback from the quote to understand how your design impacts the manufacturability and cost of your part.
At the heart of the quoting system lives FacFox’s manufacturability analysis of part designs that we provide to ensure you get well-molded parts. Within the quote analysis, you’re able to access an interactive three-dimensional image of your part design, which allows you to review your part geometry and assess any potential design issues that are highlighted. Some issues will be identified in the required changes tab, and those changes will need to be modified before your parts can be made. Issues that are not critical to part production will be listed as advisories. Those advisories do not require change, but do indicate design considerations for optimal performance in the manufacturing process you choose.
By moving the transparency slider in in the 3D viewer to fully transparent, you’re able to hide all of the areas of your part that do not need to be addressed, leaving only the important design considerations. It brings into focus any areas that need further review. Those may include undercuts, draft, surface finishes, wall thickness, and material flow.
Undercuts. The process supports simple undercuts in your part geometry. A side-action can be built into your part design to create a through-hole undercut feature, if needed. The maximum side-core dimensions are: 8.419 in. (width), 2.377 in. (height) and 2.900 in. (pull).
Draft. If your part has very little to zero draft, a required change or advisory may appear in your quote. Draft is recommended on all parts, and FacFox recommends adding 0.5 degree of draft on all vertical faces, if possible. In most cases, applying 2 degrees of draft where possible is best for molding, but is not required. If you choose to ignore a draft advisory, FacFox will make your part as-is, without draft in the noted area, but issues can arise such as drag marks, distortion from ejection stresses, or other effects that can cause delays.
Surface finishes. Depending on the surface finish you select, additional draft may be suggested. With textured finish on your part, PM-T1 (light bead-blast) generally requires at least 3 degrees of draft, and PM-T2 (medium bead-blast) generally requires at least 5 degrees of draft.
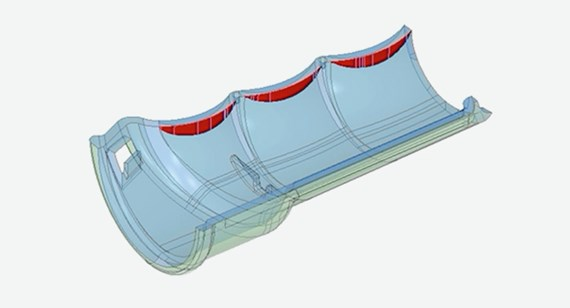
Wall thickness. Uniform wall thickness is recommended on all parts to help minimize sink and warp, but if you have any features that are too thin or thick, our manufacturability analysis will pinpoint those issues in the interactive CAD model and provide a precise thickness measurement that those features can be adjusted to. If a feature is too thin, fill problems can occur; if it’s too thick, sink is possible. Note that recommended wall thicknesses vary by resin type.
Material flow. On certain parts, we’ll run a program fill analysis that shows an animated display of resin flow through your part. Various colors represent the pressure field on an indicated scale. If the virtual resin flow is poor, adjustments may need to be made in either part geometry or material type.
You’re also able to make adjustments to the surface finish, material, and delivery of your parts within your quote as well as modify sample and production quantities as needed. Because it is an interactive quote, total cost will update in real time to reflect any changes you make, and a quote remains active for 30 days. Note that our production calculator can provide updated per-part pricing based on volume desired.
If you do not identify a material when uploading your 3D CAD model, FacFox will default it to an ABS plastic; you can easily change your desired material within the quote, however, knowing your preferred material upfront will result in a more accurate quote.
Hot keys. Keep in mind that some keyboard shortcuts can that make your DFM analysis easier to use:
~ = orthogonal views
D = Dimensions (place mouse cursor on surface/location you want to start dimension measurement from and drag crosshair to surface/location you want to measure to)
F = Draft
Remember, FacFox staffs applications engineers who are available to work with you on any required changes and moldability advisories, if needed. When your final 3D CAD model is uploaded, and parts are ordered, our mold designers will place ejector pin and gate locations, which you’ll see before production beings. If you have a 3D CAD model ready, upload it now.