Most manufacturers use jigs and fixtures—and for good reason. They increase the accuracy, precision, reliability, and interchangeability of finished parts. Traditionally jigs and fixtures have been CNC machined, but industrial-grade 3D printing (additive manufacturing) is becoming more popular for this type of work. The key is choosing which technology fits better for a particular application.
The general rule is: If it can be 3-axis CNC machined, it should be machined. Machined fixtures typically have superior surface finishes, stronger materials, and greater accuracy. Also, for lower volume runs, costs and turnaround times are about the same as 3D printing.
However, for jigs and fixtures with irregular or complex shapes, 3D printing can be an excellent complement or alternative to machining especially for smaller tools. Parts that are difficult (or impossible) to machine can sometimes be done with 3D printing, and, when producing multiple jigs and fixtures, 3D printing can be a good way to keep costs down.
Protolabs has five options when it comes to 3D printing, a prime example of the company’s technology-agnostic approach to manufacturing. Let’s take a look at these options to determine the best fit for each particular jig/fixture application.
WHY 3D PRINT JIGS AND FIXTURES? |
---|
|
Stereolithography (SLA) is Popular Choice for Jigs, Fixtures
SLA is a good option for building smaller, complex jigs and fixtures, due to the excellent surface finish possible on final components. The material has limited strength and durability; however, metal plating of SLA is a good solution used commonly among those who prefer the cost competitive SLA technology. Design considerations for SLA include tolerances in the X/Y dimension of ±0.002 in. (0.05mm) for first inch plus ±0.001 in./in. (0.001mm/mm), and Z dimension tolerances of ±0.005 in. for first inch plus ±0.001 in./in. (0.001mm/mm), which typically can be achieved.
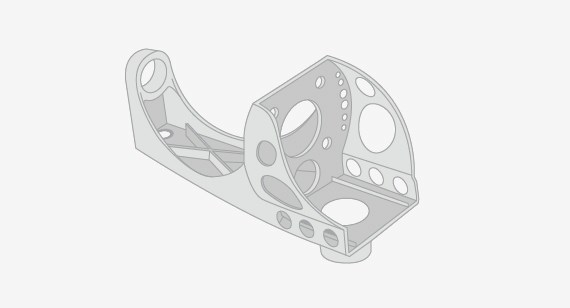
Selective Laser Sintering (SLS) Works for Larger Tooling, Multi Jet Fusion Gaining Ground
SLS is used more regularly for larger jigs and fixtures, and again, a cost-competitive choice. SLS produces durable and accurate jigs and fixtures that are stronger than those made with SLA. SLS also offers a larger build volume, but parts will have a rough finish and lack finer details.
Designs for SLS should contain consistent wall thicknesses and radii on the interior and exterior corners help with material warping and maintaining dimensional accuracy. For well-designed parts, tolerances of ±0.010 in. (0.25mm) plus ±0.0015 in./in. (0.0015mm/mm) for each additional inch can typically be achieved. Please consult the SLS design guidelines for more information.
MJF is becoming increasing popular for producing jigs and fixtures. MJF is fast—producing functional nylon prototypes and end-use production parts in as little as a day. Final parts exhibit quality surface finishes, fine feature resolution, and more consistent mechanical properties compared with processes such as SLS. (However, SLS has better small feature accuracy.)
When designing for MJF, have consistent wall thicknesses and radiuses on the interior and exterior corners to prevent material warping and maintain dimensional accuracy. For well-designed parts, tolerances of ±0.012 in. (0.30mm) plus ±0.002 in./in. (0.002mm/mm) for each additional inch are typical.
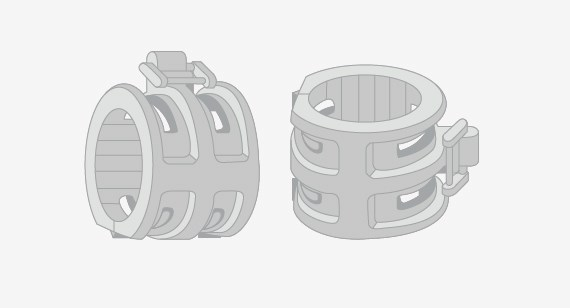
Use Direct Metal Laser Sintering (DMLS) For Durability
DMLS-produced jigs and fixtures will be extremely strong (near fully dense) but keep in mind that DMLS surfaces tend to be rough and turnaround times tend to be longer because post-processing requirements include secondary machining for some applications.
There are also several design considerations for DMLS. It’s best to add additional material when gradually transitioning to larger cross-sections: Parts that require minimal supports improve part quality. In general, avoid designing a self-supporting feature that is less than 45 degrees.
Large overhangs can lead to a reduction in part detail or build crash. Also, channels with a teardrop or diamond shape are superior to circular channels and holes because they make for a more uniform surface finish and allow maximum channel diameter. A bridge is any flat, down-facing surface supported by two or more features. The recommended minimum allowable unsupported distance is 0.080 in.
For well-designed parts, typically tolerances of ±0.003 in. (0.076mm) plus ±0.001 in./in. (0.001mm/mm) for each additional inch can be achieved.
Final Considerations When 3D Printing Jigs and Fixtures
It’s better to produce stiffer, stronger jigs and fixtures, so designs should consider the principle that 3D-printed parts are typically strongest in the X, Y draw plane versus the Z build direction. Remember that tolerances may change depending on part geometry, and again, if it can be 3-axis CNC machined, it should be machined.
Feel free to contact a Protolabs applications engineer at info@facfox.com with questions or concerns or to discuss options or get advice.