Have you ever wondered how they built that awesome movie set, or how they created that certain scary creature in the tradeshow booth, or how the cool stuff was built at the theme park, or how that cool lobby display with the 15′ tall statue was built? A lot of the time, those models/objects are built from foam, not the kind that your pillow is made from, but with a much harder type of foam. Typically, polystyrene foam is used. In addition to the foam, it requires sculpting, carving, special finishes, coatings, and a lot of different types of skill sets and knowledge to build these unique models. Fabricating foam models (from small to extremely large) can be used in all kinds of shapes, letters, props, characters, and almost anything you can think of. Here are some specific types of foam model fabrication that we are involved with.
Types of Foam Models
Foam Characters
When walking down the toy aisle in the local retail store, have you ever wondered what a really big character toy would look like? This is where foam character models come into play. Need a towering transformer character, a giant T-rex skull, or a giant Halo 5 video game character? Foam is a great material for sculptors to use in building life-size or super life-size characters for tradeshow displays, tourneys, or that awesome looking hobby room.
Sculptors typically begin the laborious sculpting process with a large block of foam, an electric chain saw, and a maquette (a french word for scale model). The maquette is used to guide the sculptor in making a large-scale replica of the small model. As you can imagine, this process can get very messy very quickly. These finished foam characters can have many different types of finishes from natural organic looking to matte to automotive looking shines.
Foam Sculptures
Foam Sculpting is one of the most popular mediums for sculpting – an art form that produces fast and awesome looking sculptures. Whether for trade shows, museums, theme parks and attractions, retail stores, office complex’s, lobby displays, faux landscape, or special events; foam sculptures can provide a realistic awe-inspiring physical model of the original design.
These foam sculptures can be themed models, statues, animals, creatures, murals, props, architectural, dioramas, letters/numbers, special foam shapes, or unique displays. They can bring-to-life a creature and it’s surroundings, relive your favorite movie scene, attract visitors at a tradeshow, or create that magical environment you have always wanted to participate in. You are only limited by imagination. These sculptures can also be used for tradeshow displays.
Foam Props and Movie Sets
Foam is a great material for creating props, armor, weapons, creatures, and anything that needs to be fabricated quickly and inexpensively. It is very common to see foam being used to create entire movie sets, theater background sets, haunted displays, amusement park backgrounds and structures, and church theming rooms to name a few.
The foam allows for realistic scenery creation or construction of buildings with elaborate background sets. Foam provides the benefits of being lightweight, economical, and efficient in terms of fabrication times. Custom shapes can be created to support any type of imagination. Curious about what movies have used foam in their movie sets? A small list of movies and television shows that have used foam for scenery are: Alien and Aliens, Star Trek – The Next Generation, Battle Star Gallactica, CSI: Miami, The Matrix, Lord of the Rings, Ghostbusters, Batman, Night at the Museum, Eight Below, Jaws, Star Wars, Final Destination 3, Pirates of the Caribbean, James Bond, Saving Private Ryan, Smallville, Harry Potter, X-Men, and many others. Broadway shows that have used foam in the scenery are: Lion King, Mary Poppins, The Little Mermaid, Phantom of the Opera, Blue Man Group, Les Miserables, and Beauty and the Beast.
Foam Letters and Foam Numbers
Large letters, sometimes combined with large numbers, are ideal for making a very bold emphasis on a brand, product, or message. When these letters and numbers are combined to make words or messages, they can be used in many types of oversized displays. At trade shows, these huge words serve as a magnet to attract large crowds and to stand-out amongst myriads of other trade show booths. Retail stores can use them for visual marketing and product branding. Special events can use large letters, numbers, and words clearly to identify the main message points.
The craze today is the ever-popular selfie – various uses of large foam letters can immerse you right into the letters and increase your social media effectiveness. Imagine standing in the middle of a 10′ tall word, replacing the “I” letter with your body – great for a selfie. Inserting a specially constructed chair hidden inside a large letter “O” or “G” can make for a great photo-shooting scene.
Foam Architecture
Foam can be used for all types of architectural shapes and settings. Foam architectural structures can be built to emulate entire buildings and even older style cities. Sometimes foam can be used in building architectural scale massing models.
Foam is also commonly used to build all types of architectural elements in new construction from columns, trim, crown molding, arches, caps, brackets, special molding, ceiling accents, railings, shutters, louvres, corbels, medallions, panels, and much more. This special architectural fabrication can be used for outdoor pools, fireplaces, all exterior features of new construction, and even special theming in rooms or the backyard.
A little bit of imagination can bring elegance and beauty to any architectural construction project. EPS foam along with Polyurethane and sometimes cement, can create awesome looking architectural structures.
Technology and Materials
Today’s technologies are making more impressive next-generation models. Combining tried-and-tested technologies of foam sculpting and cutting, along with new 3D printing capabilities and new electronics are allowing model makers to build some pretty awesome models.
- Professional Creations – We have a team of designers, artists, model-makers, painters, air-brushers, sculptors, carpenters, and welders to fabricate that imaginative, immersive, and experiential 3D foam model.
- No project is too large or too small, from a 2′ small statue to a large 50′ tall animal sculpture. If you can design it, we can create a physical model of it. If you can’t design it, we have a team of design professionals who can. We can work with preparing 3D models from scans, drawings, photos, and even napkins.
- Technologies include Foam Fabrication, Hot Wiring, CNC Cutting, Laser Cutting, Welding, and 6 different 3D printing technologies for rapid prototyping or production models.
- Foam themed models, foam letters, foam numbers, foam architectural models, foam props, foam characters, and foam sculptures can all be used to help expand what you are trying to build with foam fabrication.
- Foam fabrication may use other techniques including epoxy clay sculpting, molds, and 3D printing to develop the best 3D foam model.
- Did we mention, we have 60,000 square feet of production facilities in Utah, including the largest capacity of full-color 3D printing in the world.
- Portability and/or mobility may be an issue, especially with trade show displays. We have the team that can create your trade show foam models including custom electronics, lighting, and sound.
- Our in-house spray booth gives us flexibility in different types and grades of paint and finishing capabilities.
Steps to Create a Foam Model
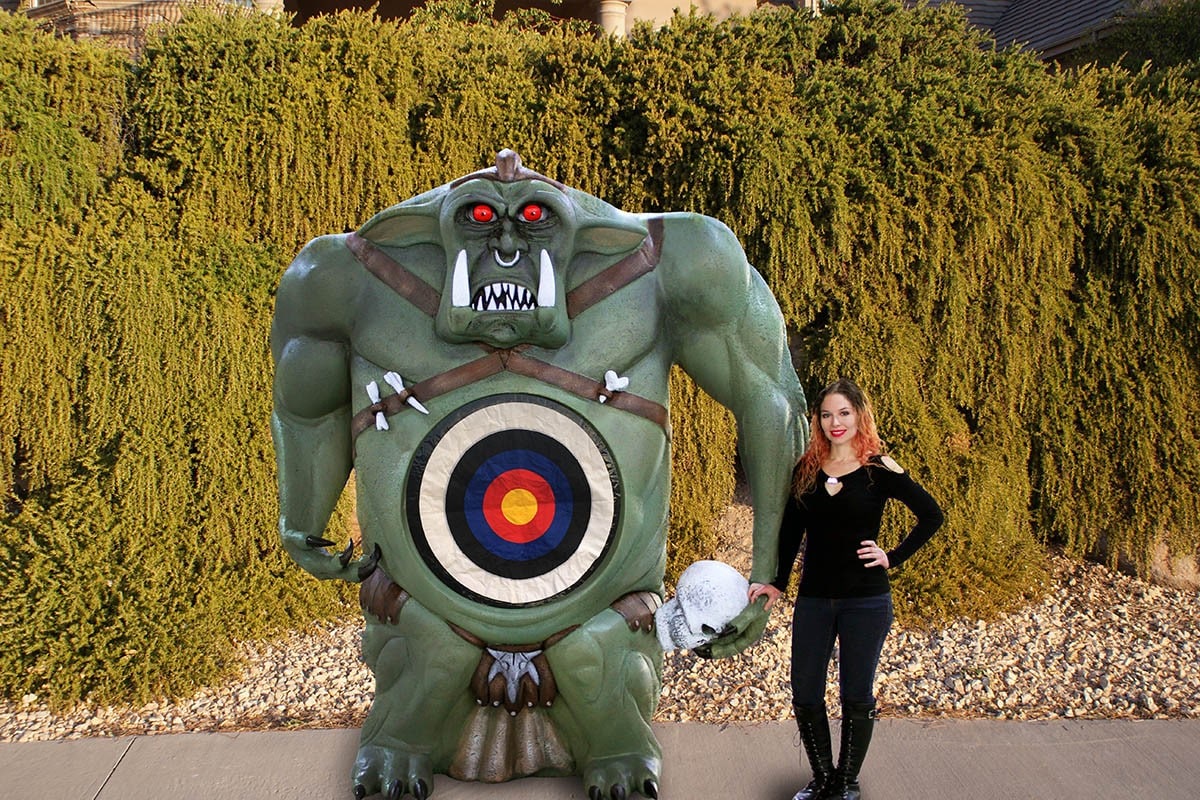
- Choosing the correct foam: Most foam sculptors use polystyrene foam, specifically EPS or expanded polystyrene foam. Some sculptors will use XPS or extruded polystyrene foam (sometimes called “blue foam” or “pink foam”) commonly known by its most popular brand name, Styrofoam – it can be purchased in home improvement stores. We would recommend using EPS. These can be purchased in sheets and glued together to make thicker pieces, or can be purchased in very large blocks, or everything in-between. You can easily insert dowels, PVC, or metal rods into pieces to give them extra support in holding them together. Polystyrene foam comes in common densities ranging from 1 lb to 3 lb. 2 lb density works really well for the best compromise in affordability (lower density is cheapest), ease of use (lower density is easier to cut and manipulate), and durability (higher density allows you to carve finer details).
- Sculpting the foam: Most sculptors draw a grid system on the foam before starting the sculpting process. This grid system can be done a number of different ways – free-hand drawing, using a maquette (scale model) as a guide, printing scaled up gridlines from a 3d design and applying them to the foam, or projecting a lighted image from a 3d design of a model onto the foam and then tracing the model. Once you are ready to begin sculpting, the Polystyrene foam can be cut with a heated wire (except for cutting through glued pieces), cut with a band saw, carved on a CNC cutter, or can be sculpted with larger electric chain saws for the heavy cutting. Then you can do finer sculpting and sanding with the use of many different types of small hand tools such as “Dremel” tools, die grinders, electric knives, handsaws, snap-blade knives, saws, rasps, subforms, and many others.
- Applying textures to the foam: You can glue smaller pieces of foam (that were easier to duplicate or carve as a stand-alone) onto the existing model. You can also add an acrylic monomer, for example, to emulate wrinkled skin. Using epoxy clay allows you to add/carve extreme detail into your foam model that would have been very difficult directly carving into the foam.
- Finish work: There are a lot of methods to finish off the project depending on a number of factors related to project requirements, such as final durability, weather-proofing, temperature, mobility, strength, and flexibility. Typically, you need to seal the surface and apply protective coatings. These finishes may be combinations of painting, air-brushing, flat-to-glossy finishes, natural environment finishes, soft-shell and hard-shell coatings, sealers, and glassing. These can be from latex, acrylic, urethane, polyurea, epsilon, styrospray, polyurethane, and many others.
Another option is to just specify to FacFox what you would like done, and we would be glad to do it for you.
How is Foam Created?
Polystyrene plastic starts with very small pellets (raw beads) about a millimeter in diameter.
The first step involves expanding these pellets to about 40 times their original size – this is done inside of a steam chamber where heat (about 400 degrees Fahrenheit) allows pentane gafs to escape, then air enters the pellets and inflates them. These expanded Polystyrene pellets look like small puffed styrofoam BB’s. These polystyrene BB’s are then put into bags for storage and the next step.
The second step is another manufacturing process where these BB’s are then poured into a block mold machine. The more BB’s that are put into the hopper, the denser the final foam will be. These BB’s are then steam-fused together into a large block, sometimes as long as 24 feet and as wide/deep as 4 feet x 3 feet. The molding process occurs fairly quickly in about 5 to 20 minutes, depending on density.
Common densities of the Expanded Polystyrene (EPS) are 1lb, 2lb, and 3lb per cubic foot. There are other special densities that can also be molded, some as small as .5 lb up to 6 lb. These large blocks of foam can weigh anywhere from 300 to 900 pounds.
These large blocks are stored or shipped for later cutting into more common sheet sizes or special shapes. This cutting process is usually done with heated wires that easily melt through the EPS foam – similar in concept to a warm knife slicing through butter. At this point, there are hundreds of uses for these finished sheets of EPS foam.