Metal 3D Printing is becoming a great complement to Metal Injection Molding (MIM) and the decision to use one or the other largely comes down to the volumes required. The added bonus with metal 3D printing is that you can update a part without needing to invest in a brand new mold.
Manufacturers today who are searching for a cost-effective way to make small and complex metal parts for production by and large only have two options: metal injection molding (MIM) or investment casting. Casting has been around for thousands of years, and MIM was created ~40 years ago. Metal 3D printing is the new entrant to the scene, and for the first time in a long while adds another option to the engineer’s toolkit. New low-cost, high volume metal 3D printing technologies (like FacFox) are beginning to change conventional manufacturing wisdom.
Low-Cost Metal 3D Printing Comes of Age
Setting aside investment casting, let’s explore how the economics play out between MIM and the new low-cost bind & sinter technologies such as binder jetting.
The Long Road of MIM
Today MIM has matured into a core manufacturing technology and is widely used in the production of small components for a variety of industries and a large number of material options. This was not always the case — when MIM first came onto the manufacturing scene over 30 years ago, it suffered setbacks due to a lack of process understanding and new entrants flooding onto the scene. Part repeatability, voids, and fatigue issues plagued many MIM providers and the poor part performance soured the reputation for many manufacturing engineers. It was seen as a manufacturing technology of last resort, only to be considered when all other avenues of production had been exhausted or when cutting costs was prioritized over part performance.
MIM has come a long way since the early days, and today’s best MIM operations have proven that MIM is capable of reliable high-volume production and strong material properties. There are still pros and cons associated with MIM, which this article will further explore.
Who Uses MIM Today?
MIM is used to create components in numerous markets including medical, firearms, general industrial, and many others. When a part design is not likely to change for the next 5 to 10 years because it is part of a long design-in cycle and the volumes will be in the hundreds of thousands to millions, then investing in MIM tooling can make a lot of sense from an economic perspective. One of the main headaches for manufacturing engineers when using MIM is having to write the check for the mold (which can cost as much as $50K – $100K). If you know the cost of the mold will be quickly amortized over millions of parts, then the investment could make a lot of sense.
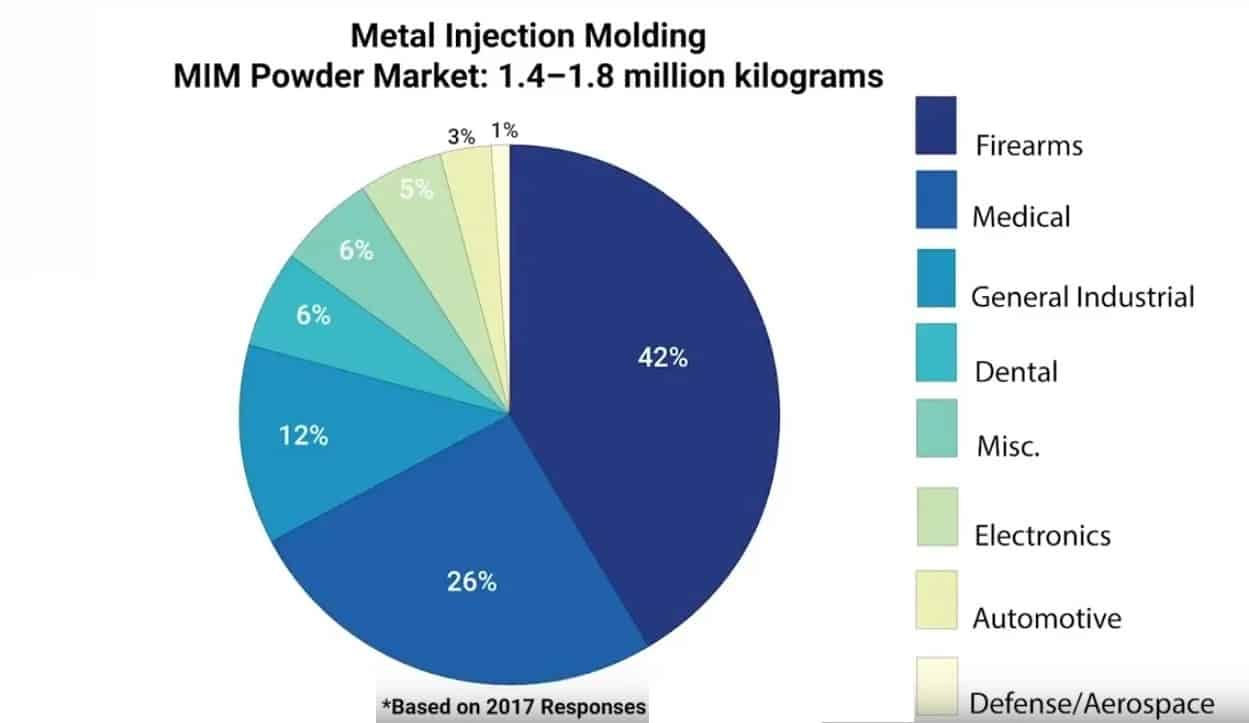
Metal 3D Printing – Freedom from the Mold
While MIM has been the choice for very high volumes of small and complex components of late, many design and manufacturing engineers have been rooting for a metal 3D printing technology to find a way to make printing metal parts an economical alternative to MIM. Most engineers’ frustration with MIM, aside from the high-cost tooling, is being limited to a single component per mold. If you want to make 10 different parts, you need to invest in 10 different molds. Do you want to make a small feature change? Yes, that means modifying the existing mold, fixing the parts in post-processing, or getting a completely new mold.
Metal additive manufacturing holds the promise of freedom from the mold. Changing the design of the part is as easy as updating a computer file.
What has held metal additive manufacturing back from high-volume production has been a VERY high cost per part. The machines for powder bed fusion technologies such as DMLS can cost well over a million dollars, and materials can cost as much as $150 per pound. Those costs, in addition to other labor and infrastructure costs, translate directly into a prohibitively high part cost.
Metal 3D Printing – Unlimited Design Freedom
MIM has more constraints regarding the part geometry than metal 3D printing. This is due to the need for a mold and forcing binder and powder under high pressures, and then opening the mold and extracting the green parts. The mold is great for a highly automated process, but also comes with drawbacks. On the other hand, when creating parts via 3D on a layer-by-layer basis, new design freedom is possible. Unlike MIM, additional complexity does not also result in additional mold and production costs.
Metal Additive Manufacturing Meets Low Cost
The demand for a low-cost metal additive manufacturing technology is extremely high. Advances in bind & sinter technologies have given new hope for metal additive manufacturing to compete on a cost-per-part basis. Bind & sinter is a category of metal 3D printing that uses a binder in a layer-by-layer process to create a “green part” that is then placed in a sintering furnace to reach full density. It’s expensive to reach over 2,400 °F no matter what process is used, and reaching it every layer is what drives up the cost of powder bed fusion. By printing green parts in high volumes on lower-cost machines and then bulk sintering all the parts at once, the cost is significantly reduced. For the first time, the part cost of metal 3D printing is so low that it can compete directly with MIM.
When to Use Metal AM vs. MIM
Bind & sinter technologies are dramatically driving down the price-per-part for metal additive manufacturing, but how do they compare to MIM? The best bind & sinter technologies today are a great option when volumes are well above prototyping but below the break-even cost of investing in the MIM tool. This decision partially depends on the cost of the mold and is usually when production volumes head north of 20,000 to 30,000 pieces per year. At volumes just below that, it is often more cost-effective to have your parts manufactured with a low-cost bind & sinter technology.
It’s important to remember the freedom offered by metal additive manufacturing with regard to design flexibility. In addition to being able to create geometries not possible with MIM, updating a design is trivial with metal 3D printing as compared to buying a new mold every time a change is needed. Molds also need maintenance after high production volumes and eventually will require repairs or replacement.
Manufacturers working on their new products and researching the most cost-effective way to manufacture small and complex parts need to be investigating bind & sinter technologies. The cost analysis can be done quickly to determine whether MIM is the best option or whether metal additive manufacturing is the most cost-effective path forward.