3D printing doesn’t have to be wasteful! Learn about PLA recycling, composting, and how to reduce waste with other materials like PETG.
When plastic is sent to a recycling center, it gets washed, sorted, shredded, and then melted into small pellets, which are then used as raw material for the manufacturing of new products. Each of these steps can be done at a single facility or split across multiple sites.
Whether it’s done at one or many locations, the sorting stage is extremely important to the recycling process. Contaminating one type of recycled plastic with another can seriously reduce the strength and longevity of the final material. As a result, plastic sorting plants use a variety of methods to separate the types of plastic from one another, all the way from simple hand sorting to high-tech density and IR detectors!
What role do PLA and PETG play in this matter? In this article, we’ll go over how recyclable 3D printing filaments are, the possibility of composting, tips for reducing plastic waste, and more!
What Types of Plastic Are Recyclable?
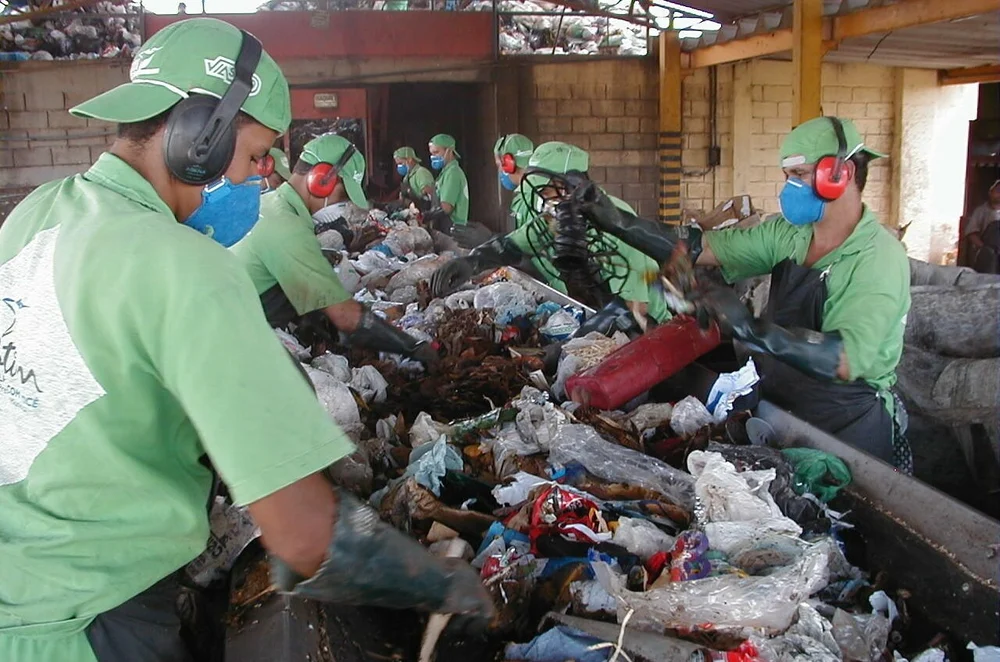
Plastic can be classified into two types: thermosets and thermoplastics.
Thermosets are materials that are molded and then cured into their final forms and include materials like polyurethane or silicone. You will most commonly find thermosets being used as the resin for vat polymerization 3D printing. Typically, these are difficult to recycle, so this article will focus on the other type of plastic.
Thermoplastics don’t have any curing step and become pliable or workable after being heated past their melting temperatures. As a result, pretty much all FDM 3D printers use thermoplastic.
In theory, most types of thermoplastic can be melted down and recycled, with differing amounts of efficiency and material loss for each type. However, the types of plastics that are processed by recycling plants can vary significantly around the world, or even between different municipalities of the same city!
For example, almost every recycling center processes PET and HDPE, which are the materials that plastic bottles and food containers are usually made of. On the other hand, even though PVC is recycled extensively in Europe, it’s much less common in North America.
Is 3D Printer Filament Recyclable?
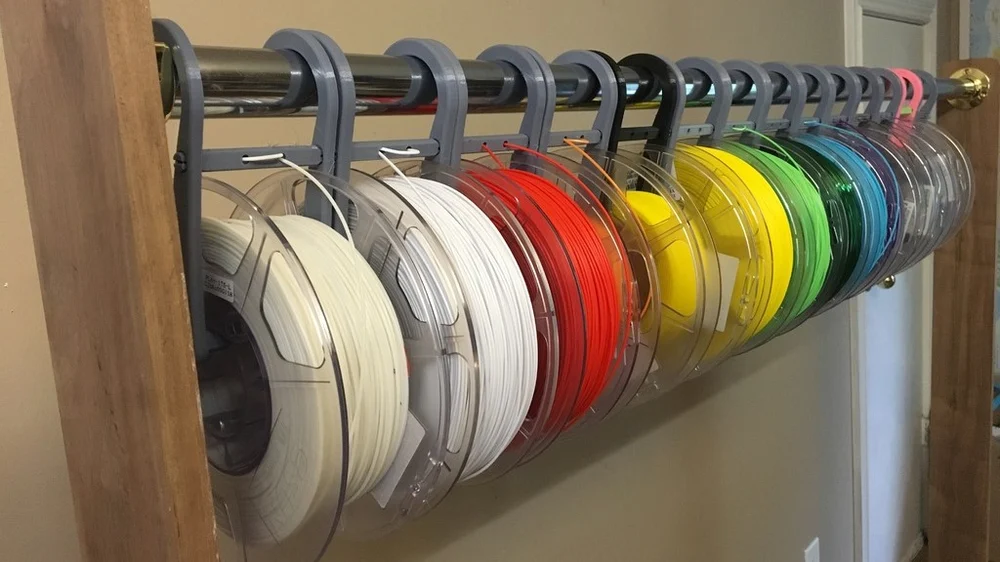
The two classic types of 3D printer filament, ABS and PLA, aren’t recycled by most curbside municipal recycling programs. Under the ASTM International Resin Identifier Codes, both are classified as Type 7, or “Other”, which is not typically processed by municipal programs. So, unfortunately, you can’t just throw your failed prints into the recycling bin.
Even though PETG and PET are chemically very similar, PETG is also excluded from being recycled by most programs. In fact, the chemical similarity of PETG to other types of PET plastic, combined with its low melting point, makes PETG a pesky contaminant during the recycling of PET. That’s because it’s difficult to differentiate from PET and dangerously reduces the temperature stability of the final PET material if it’s mixed in.
Polypropylene (PP) filament isn’t commonly used for 3D printing as its semi-crystalline nature causes it to warp significantly while cooling. For the brave few that do print with PP, it’s recycled in some municipalities. Contact your local recycling center to find out whether they accept it or not.
Almost every other type of printer filament (including nylon and polycarbonate) are also classified as Type 7, like ABS and PLA, so they aren’t usually processed by normal plastic recycling plants either.
Non-Municipal Recycling Centers
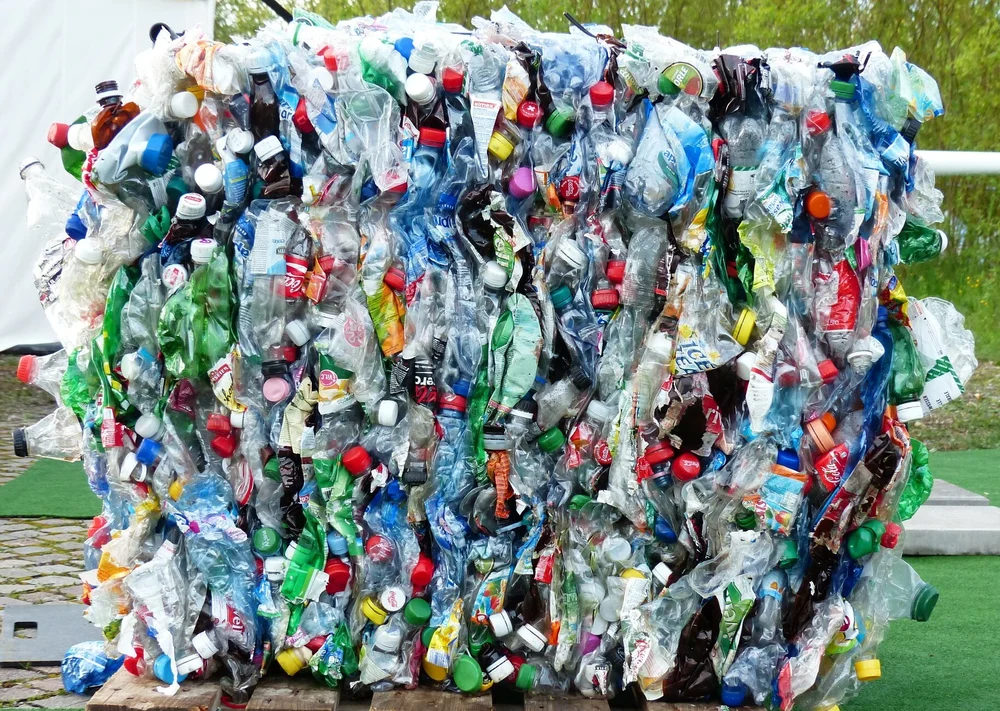
Even though most local recycling programs won’t turn your failed 3D prints into recycled plastic, there are many independent plastic recycling and processing companies that recycle the materials that aren’t processed by the local pickup service.
Try calling local recycling companies and asking whether they process your plastic of choice. You might need to try multiple places because even if a company processes a plastic type used by 3D printing, many companies might hesitate on accepting plastic waste from a non-verified source.
If, however, they’re willing to accept your waste materials, try accumulating big batches of waste plastic that you can periodically drop off. If you’re part of a Makerspace or FabLab, you can also make a big communal waste box for failed prints and take it over when it’s full. Just make sure to keep the different types of plastic separated, with the plastic types clearly marked!
PLA Composting
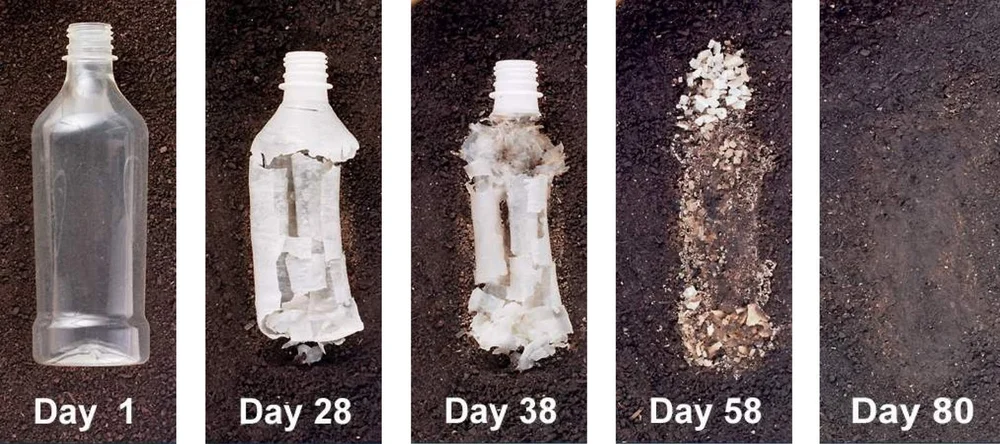
If you can’t turn PLA into recycled plastic through conventional means, there’s another interesting way to deal with it without sending it to a landfill. One of the unique features of PLA is that it’s a biodegradable plastic, which means it can be broken down over time by bacteria and fungi. You can take advantage of this fact by “composting” your PLA waste.
Composting PLA involves breaking it into small pieces and leaving it in a microbe-rich environment like a compost pile. Depending on your local conditions, it can take a very, very long time until the PLA is fully broken down. (Expect up to a year in wet climates, and even longer in dryer climates!)
Note: PLA is not compostable in the formal sense of the word (see this article on bioplastics for more details). So if you live in a place with a municipal composting program, do not mix your PLA waste into your normal food waste. The long degradation time of PLA, as well as its potential to produce trace heavy metal residues after it degrades, makes it incompatible with commercial composting facilities. If you mix PLA into your food waste, it will probably end up getting removed from the compost and sent to a landfill anyway, so just keep it in your personal compost heap!
Re-Extruding Filament
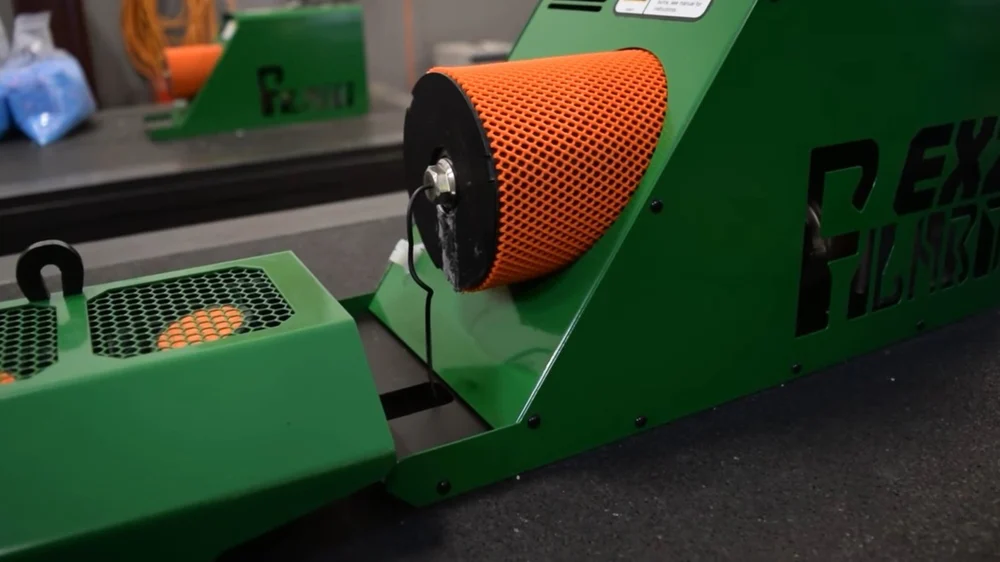
A great feature of the thermoplastics that are used in 3D printing is their ability to be melted down and re-extruded without a significant loss of material. Making and using a filament extruder at home is a little more advanced than using a 3D printer, but it’s definitely within the reach of a dedicated hobbyist, and a great way to practically recycle your waste plastic! It also allows you to make your own filament, which cuts down on filament costs. That is if you don’t consider the cost of making your own extruder.
Recycling waste plastic into usable filament requires two steps: shredding the plastic into small pieces, then melting and extruding it with a filament extruder. There are many solutions to the latter step, with hobby-grade plastic extruders like the Filastruder or Filabot available for sale, as well as designs for DIY filament extruders (for one such design, check out our article on how to make your own filament extruder).
Unfortunately, the plastic shredding step remains a bit difficult for the average hobbyist. Grinding up large pieces of plastic puts a lot of strain on the types of motors found in most commercial appliances, and industrial shredders, which can handle the strain, are too expensive for most individuals to purchase themselves. That said, people have found success using a blender or meat grinder to break down small amounts of their plastic waste for filament extrusion.
Tips for Reducing Plastic Waste
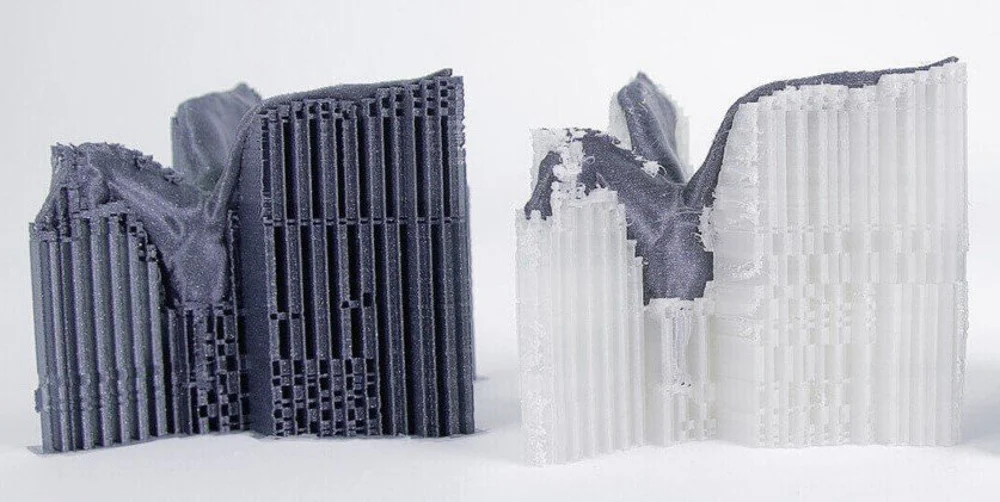
Even though the suggestions above can help you cut down on waste plastic buildup, the easiest way to reduce your waste is to prevent it from happening in the first place! Failed prints and prototypes are an inevitable source of waste for any 3D printing hobbyist, but here are some quick tips for preventing waste buildup:
- Eliminate supports as much as possible. Printing with supports results in a lot of waste plastic and a lot of time removing it from the part. Whenever possible, try to print your models without supports, or design minimalistic supports into the part itself. (If you use slicing software like Simplify3D, you can also trim the number of supports manually.)
- Print with a brim instead of a raft. Rafts are a good way to ensure that the part will stick to the build surface of your printer. However, like supports, they use a lot of material and require extra steps to be removed from the part. If you’re having bed adhesion problems, try adjusting your first layer height, or print with a brim instead of a raft. Brims also help parts adhere to the bed, but use significantly less plastic than a raft.
- Don’t print too many parts at once. The chance of a print failing tends to increase when too many parts are being printed at once. If the printing of one component fails, its aftermath will probably carry over to the other components on the bed, possibly ruining them as well. This is highly dependent on your personal experience and specific printer setup, but unless you have a lot of experience and a printer you can trust, try to separate multi-component projects into multiple prints rather than a single large one. It will take more time, but it might be worth it in the end!
Source: https://all3dp.com/2/3d-printer-recycled-plastic-tips-for-your-waste-plastic/