The Original Prusa SL1 is Prusa’s long-awaited attempt to stir up the resin world. Check out our review to find out if Prusa pulled it off once again.
One does not have to be a 3D printing enthusiast to have come across the name Prusa. Few brands have the impeccable reputation and fervent fanbase that Czech-based Prusa Research enjoys.
Creators of the Original Prusa i3 MK3S, which currently boasts All3DP’s Best 3D Printer award, Prusa Research achieved its goal of creating a high-quality open-source 3D printer accessible to the masses. For the SL1, the company has set out to do it again — this time tackling desktop Stereolithography (SLA) printing.
To help them with this massive undertaking, Prusa acquired the Czech company Futur3D, which already specialized in SLA 3D printing and had five years of experience in the field.
“The SL1 isn’t trying to compete with the flimsy Photon or with the ultra-pricey Form,” said Prusa himself, “but instead I want it to be the MK3 of the resin world – have the best print quality, convenient design and features, ease of use and other things, while keeping a price accessible for an everyday hobby maker.”
So, did Prusa succeed? Read on as we review this printer and find out if the master of the maker scene, Prusa, came through on his words – once again.
Verdict
PROS
- Complete ecosystem with the CW1
- Minimal setup
- Comprehensive build guide (if you get the kit)
- Slick design
- Compatible with third-party resin
- Replaceable carbon filter
CONS
- Relatively small print bed, for the price
- Washing turbine (CW1) does not function properly
- Slicer estimated time is inaccurate
- Supports sometimes lose adhesion to bed at fringes
- Bed raising not possible mid-print
It’s no secret that Josef Prusa and his team are striving for perfection. And yes, the SL1 is on the right track, but its also not quite there yet in terms of his own ambition.
Compared to the budget resin printers Prusa has clearly stated he is not competing with, the SL1 does offer a bouquet of convenient features that give users the Prusa-feeling of a well designed and harmonized machine. You can expect high-quality prints with little effort even without any prior 3D printing experience, just as Prusa’s goal is.
However, for the price tag, the downsides of the printer can also not be too easily overlooked.
We think of the SL1 as the MK2 on Prusa’s way to creating the MK3S of the resin printing world.
The Tech
The Original Prusa SL1 is an SLA, or more specifically, an MSLA 3D printer.
MSLA stands for Masked Stereolithography Apparatus. Generally, SLA printers use UV light to cure (solidify) photosensitive liquid resins. The SL1 does so via its build-in high-resolution LCD screen that displays a mask — hence the name — in the shape of a single layer.
The UV LED panel shines UV light through the mask into the resin tank’s transparent bottom, curing a single layer of the printed object, which adheres to the printing platform. After a layer is cured, the printing platform moves by a small increment upwards, creating space for another layer.
-
Where the magic happens: The LCD mask
Much like the DLP process, MSLA effectively cures an entire layer at a time as opposed to the point-to-point technique of traditional SLA printing and can, therefore, achieve significantly faster print times. The downside being, with MSLA, the pixel size of the LCD photomask defines the granularity of a print.
Using a 5.5″ 2K LCD screen, the Original Prusa SL1 offers a possible XY-resolution of 47-microns. Paired with a recommended layer height (Z) of 0.025 to 0.1 mm, the SL1 is capable of incredibly detailed prints.
As is typical for an LCD resin printer, the SL1 features a removable resin tank that uses a transparent FEP film as its bottom. Unique to the SL1 though, is how a motor gently tilts the vat after each layer change, thereby separating the print gently from the FEP film instead of lifting the print vertically and thus significantly reducing the tension exerted on the print inside the resin vat. By tilting the tank, the resin is also continuously stirred, improving the surface finish and overall quality of the print.
-
Prusa’s tilt mechanism
Beyond what’s under the hood, right off the bat, the printer’s build quality is noticeable. Especially when assembling the kit, you can see all the parts fitting together neatly; no need for jamming or bending parts into their designated place.
The Original Prusa SL1 boasts a rigid aluminum frame core, with a separate body. The sturdy Trinamic driver — battle-proven from the MK3 — ensures excellent z-axis stability and, with a weight of about 4 kg, the printer is neither too heavy nor too flimsy. When filled with toxic resin, a certain weight is exactly what one wants.
To minimize fumes inherent to the SLA process, the SL1 features a built-in high-quality carbon filter at the back. The fan’s casing can also be removed and mounted with a hose to channel them out the window.
-
Sturdy design – no rocking the bed on this one
When it comes to print area size, the Prusa SL1 offers a maximum of 120 x 68 x 150 mm, which is in the same ballpark as its budget competition and pretty standard on desktop LCD-based resin printers.
What does give the machine a premium feel, however, is the ease of operation. Gone are the days where you had to twist and turn a knob to scroll through the menu of a Prusa printer. For the SL1, Prusa ditches its distinctive click wheel knob and furnished it with a large color touchscreen that lets you tip-tap your way around the file directory in comfort. During prints, the UI provides you with an ample amount of information including the print time, the amount of resin used, and the total layer-height. You can even get a live visualization of each layer as it is printed.
Furthermore, the SL1 displays a level of thoughtfulness not present on many other machines of its stature. Take the manual fill level indicator, which serves as a maximum fill line and lets you top up without overfilling the vat. Similar helpfulness comes in the inbuilt resin sensor, which informs you if a print is likely to run out of resin mid-print.
-
The SL1’s sleek LCD display
When it comes to connectivity, the host of options is now expanded by the possibility of connecting your SL1 to WiFi, allowing you to directly send the sliced files from your computer to the printer. Running back and forth with an SD card or USB stick could be a thing of the past if it wasn’t for the fact that you still had to start the print manually. Besides WiFi, the SL1 also supports USB and LAN.
Assembly
Setting up the Prusa SL1 3D printer is a simple and straightforward process, taking you about 20 to 30 minutes — if you ordered yourself the assembled version.
In case you went for the kit, the assembly will take you up to 10 hours of turning screws, plugging in wires and hooking up circuit boards. But, thanks to the instructions provided online by the Prusa team, this highly complex electronic machine can be set up even by an absolute novice. Just don’t forget about the crucial in-between-steps of enjoying some sweet Haribo gummy bears. It seems like someone in the Prusa team knows a little bit about the psychological factor of conditioning.
-
Some Haribos were definitely earned after assembling the circuit board successfully
All in all, the process of assembling was smooth sailing with only one major incident: connecting the WiFi cable to the circuit board (Chapter 4. /step 19. in the setup guide). Without being dramatic, getting the pinhead-sized connector to stick to the circuit board took us more than half an hour, a stark contrast to the one-click-and-be-done-with-it instruction. It also resulted in some anxiety when first turning on the printer, as circuit boards tend to be somewhat fragile, and any slip of the tools might lead to a premature end to the review.
Thankfully none of these worst-case scenarios happened. As a hint, off-record, to anyone having the kit in mind: Attach the WiFi cable to the circuit board before you screw it in. Then proceed as instructed. It might save you half an hour of frustration.
Apart from this minor hiccup, the setup was a stroll in the park.
Once the machine was assembled, plugged it in, and fired it up, we followed the setup wizard on the printers LCD display for the pre-flight check and calibration.
-
Guiding you through – the setup wizard
Prusa advertises the crucial step of calibrating the printer’s print platform and printing bed as being done automatically when, in truth, it should be called something along the lines of assisted calibration. Nevertheless, it’s an easy setup as — again — all instructions are presented not only in the manual but also on the printer’s LCD screen in the form of photographs and illustrations. The whole process takes less than 5 minutes, and once the machine is calibrated, it will stay calibrated for all consecutive prints.
-
Bed-leveling woes are gone: Once calibrated, the platform stays level
The Prints
The first model we decided to print was the test prints provided by Prusa, using their included Prusa-like orange resin.
And one thing is clear from the beginning. This printer can handle fine detail exceptionally well.
We scaled down the Perrin Tower by about 50% right away to see just how fine the objects can be printed, and we were not disappointed. Also, the other test model — miniature Prusa holding the honeycomb calibration test object — was imposing, with a flawless surface and high-quality details.
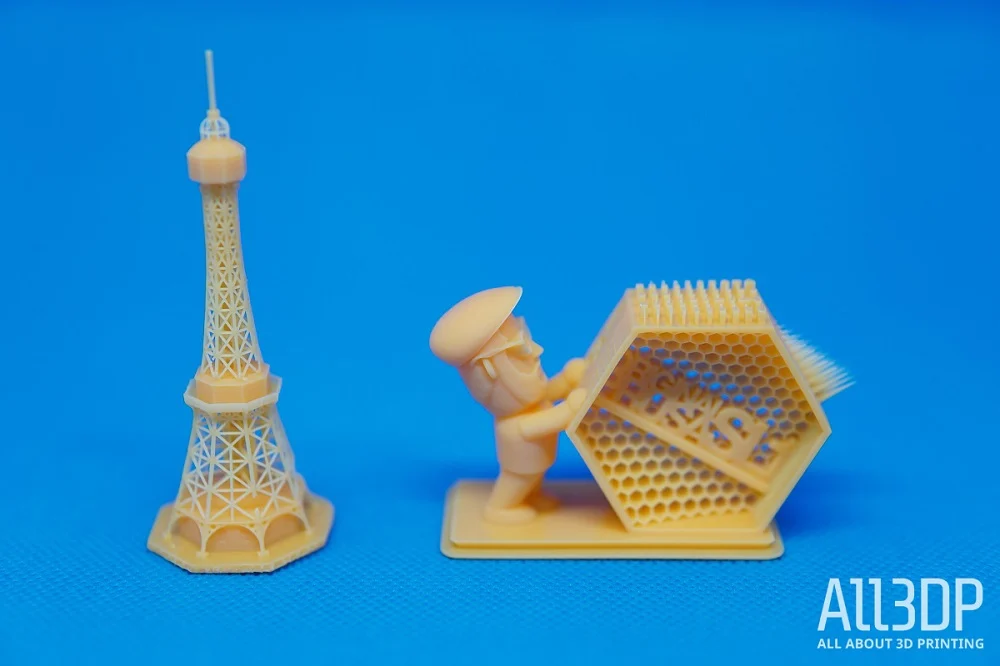
As the Prusa SL1 is an open-source machine, you can use any brand of resin you like, as long as it is compatible with the 405 nm wavelength of UV light (the majority of desktop SLA printers are.) So, we tried out some third-party resins we had lying around from former reviews and, after tweaking with the exposure time, the results were also satisfying. In fact, with some trial and error on our part, SL1 performed admirably with a variety of materials.
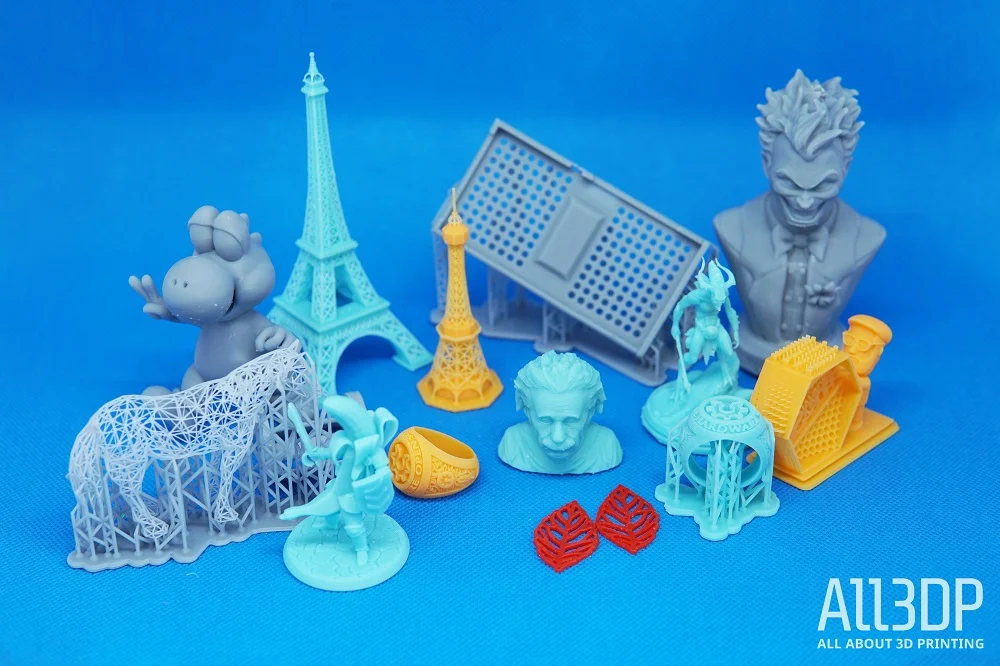
A typical frustration with bottom-up resin printers such as the SL1 though is that you must wait for the print to run long enough for the print plate to clear the edge of the resin vat before you can see if it’s a success or failure. Especially as with resin printers the critical part of a print is the first couple of layers and if they adhere properly (particularly with third-party resin and changed exposure settings).
Woefully with the SL1, there is no way of taking a peek. While other resin printers allow for the print to be paused, automatically raising for you to take a look, this is unfortunately not possible with the SL1. Although you can pause the print, the plate stays put.
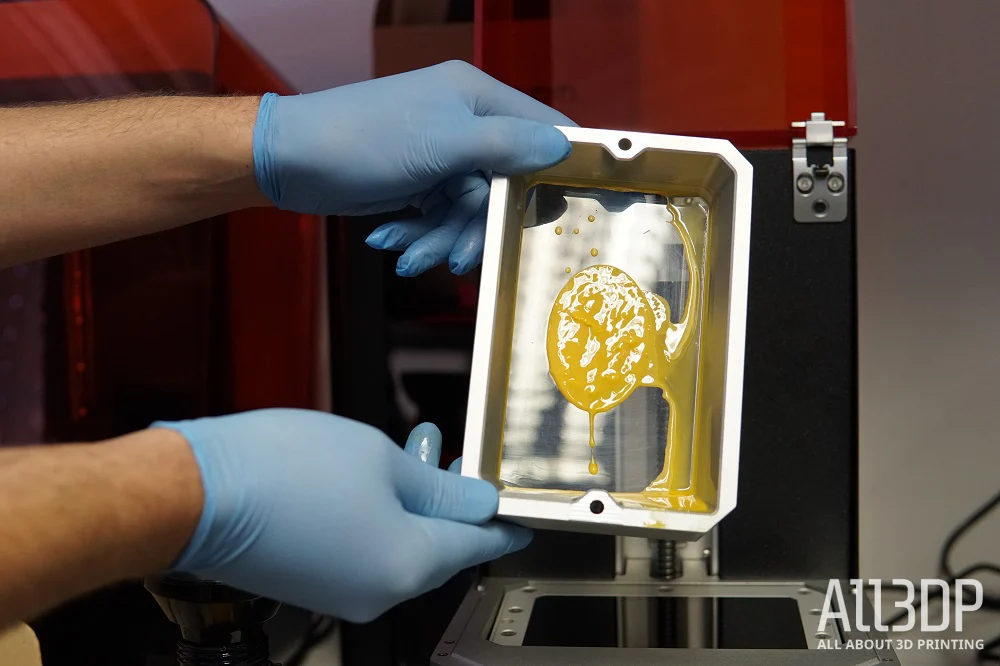
All in all, though, the outcome was satisfying. From the over one dozen prints we solidified during this review, only one print failed, sometime during a night shift, by what we assumed the next morning was a lack of support structures. A somewhat recurring problem we spotted, though, was that the raft beneath the support structures sometimes lost adhesion to the print bed at its fringes. While the prints still turned out flawlessly, and the problem had the handy side-effect of making it even easier to remove the print off the bed afterward, this is surely not the intention of the company.
In general, PrusaSlicer can automatically create an ample amount of support structures where needed, but sometimes it doesn’t hurt to add more manually just in case. This brings us directly to another key feature of the SL1 – the slicer.
PrusaSlicer
Hardware isn’t the only development focus with those hallowed fabrication halls at Prusa. The company’s software team has had its work cut out to prepare the new PrusaSlicer 2.0.0 to accommodate the launch and new workflow of the SL1. For our testing, we used the newer PrusaSlicer 2.1.0 to hand, so all impressions below are accurate as of the time of publishing.
Upon first opening the software, you will find a significant change in the user interface (UI), making it overall more accessible and straightforward to use. While you could probably fill half an article itself on the new PrusaSlicer, we’ll focus on how they implemented the MSLA slicing into it. While SLA and FFF slicers may look alike at first glance, in reality, the two technologies are quite different, except that they work slice by slice.
Slic3r (don’t worry, this atrocity of a name will soon fade out over time) has always been rather generous with supports – and for a good reason. It is one of Josef Prusa’s declared goals to allow even complete beginners to print pretty complex geometry right out of the box, without having to fiddle with the settings much beforehand.
Still, with some models, the algorithm may place them in inaccessible places, resulting in tedious removal of support structures from hard-to-reach spaces, for example, latticed objects with support structure inside them.
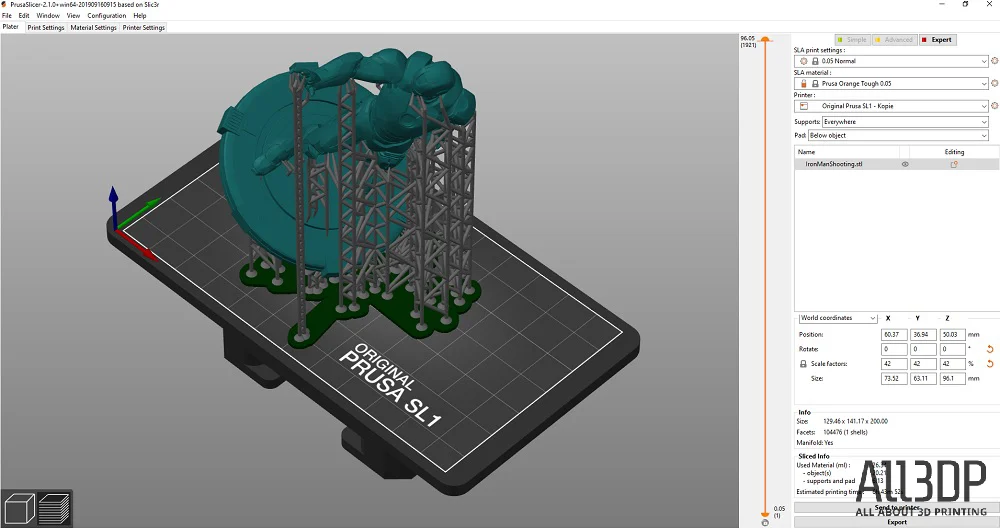
The model context menu (right-click on a model) now lets you generate support blockers and enforcers. Support blockers are useful when you’re generally happy with the automatic supports, and you want to exclude some areas which either don’t need supports or might create hard to remove supports. Support enforcers work the opposite way. Turn automatic supports off and select specific parts of your model that will need supports.
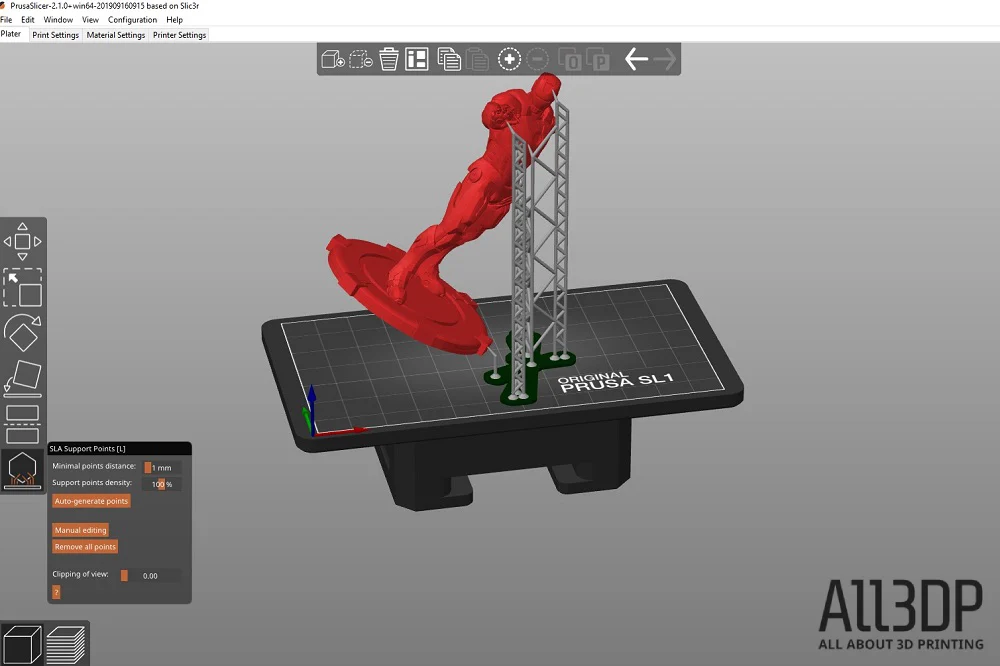
Furthermore, the new PrusaSlicer supports material and printer settings for various resins, as well as a layer preview and object clipping.
As frequent Prusa-printer users ourselves, we always liked the company’s slicer for its ease of use. And with the update introducing the SL1 to the fold, it has streamlined its usability even further, including the necessary tools for successful SLA printing in a simplified UI.
But not quite all the crucial features. By default, all SLA prints are printed as a solid block, meaning there is no infill. Hollowing an object lets you use less resin, first of all, but also allows for stabler prints, as a lighter object also needs less support (so there is less chance of breaking off), and a less dense crosssection has an easier to break bond with the FEP film.
At the time of writing, PrusaSlicer does not feature 3D model hollowing, meaning you have to fall back on programs such as MeshMixer or Windows 3DBuilder. Prusa Research has announced it is looking to implement the feature soon.
Another thing we found to be inaccurate when using the slicer was the print time estimation for the SL1 printer. On average, the print took about half an hour longer than the PrusaSlicer calculated. This is obviously not a deal-breaker but can be irritating sometimes, especially when trying to fit prints into office hours.
Apart from that, the PrusaSlicer is a great tool and fulfills (almost) all the checkboxes needed for SLA printing. As Prusa is big about open source, we are confident that missing features will be incorporated rather quickly.
Post Production
Post-production in previous SLA printer reviews – especially the budget ones – was always quite a mess. Bathing the prints in isopropanol (IPA) is a hazardous but necessary process. Without a post-production machine like the CW1, this meant literally getting our hands dirty and washing the print in a bucket full of 99% IPA solution – the stench is not pleasant.
Curing prints was a similar DIY experience. Either you build yourself a blacklight construction of some sort, or – as we did in some cases – just put the prints out on the balcony and let the good old sun do its job. Yes, it’s ecologically sustainable, but also quite impractical.
Prusa’s CW1 is supposed to eliminate this tedious hustle, but it wasn’t fully up to the task.
The Curing and Washing machine (though not in that order, although you can probably guess the reasoning behind the naming) is Prusa’s attempt to combine all three post-production steps: washing, drying, and curing. And yes, it does make post-production easier – and more importantly – less messy.
-
The CW1 with a familiar display menu
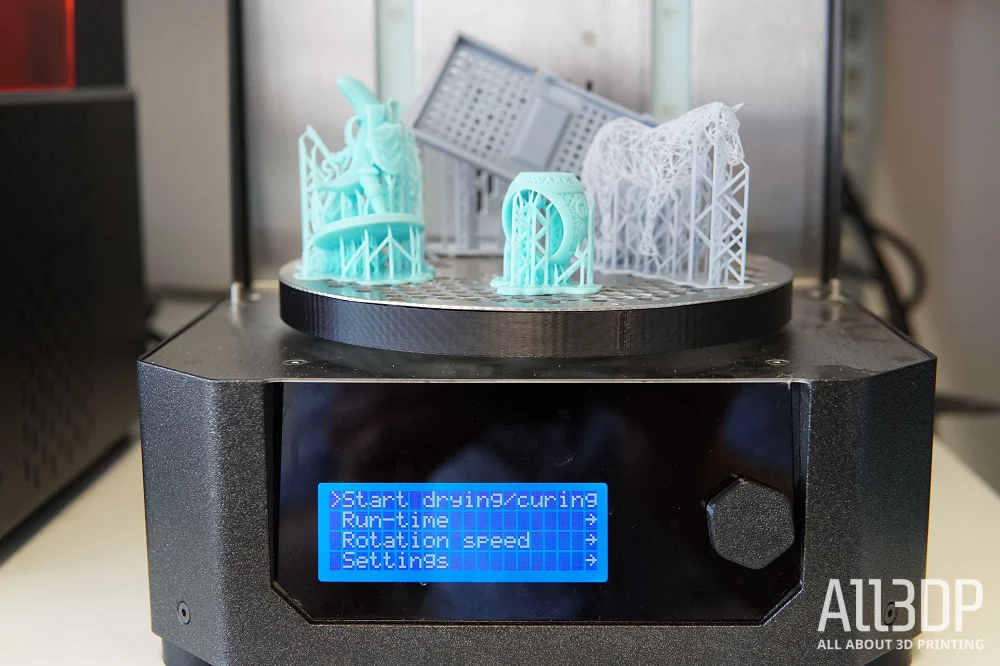
After washing your prints in the IPA bath and removing as much residue from the model as possible, you can take out the container, wash the model off with some water, and then place it on the rotating disk to start the drying and curing stages. The machine has another useful built-in sensor that automatically sets it to washing or curing, depending on if the container is placed inside or not. The standard time setting for each stage is about three minutes.
Two things we came across in our review:
The swirling mechanism, powered by magnets, hardly ever functioned as intended. The turbine you “install” at the bottom of your IPA bucket did not seems to be accelerated by the rotating disk under the basket. We tried to stir it in the right spot with a rod (you don’t want your hands to make contact with that IPA resin mixture) and got it working for a while. The rattling sound it makes when spinning is the indicator.
Since you constantly have to switch between washing and curing, and therefore have to take the basket in and out, the turbine never really stays in place. This might be resolved by simply adding a stronger magnet at the bottom of the turbine to help it take-off; or by adding a frame to the turbine to center it to its intended position.
Secondly – and this is a minor frustration – there is a somewhat unwieldy change between the different modes. If you want to just cure without the drying mode before, you have to click yourself through an unnecessary amount of settings, and vice versa.
Minor irritation at the workflow aside, CW1 still does offer good value for its money. Other, comparable, SLA post-processing machines tend to be in the same ballpark, price-wise, and only consist of a curing station.
The intention of simplifying the post-processing process and condensing all steps into one machine is exemplary, but – at least from our perspective – could be improved. When the turbine is not working, it’s basically just a bucket of IPA where you soak your print in. Obviously, this still works, but not as intended.
Overall it did shorten and simplify the post-processing tremendously, though.
Is It Worth It?
The Original Prusa SL1 entered the market as the answer to flimsy, budget LCD systems, promising brilliant print quality and rigidity packed into an easy to machine. Compared to the budget alternatives on the market, though, it does not differentiate itself print-quality-wise as the high resolution of LCD prints is just inherent to the technique itself.
The SL1 stands out however when it comes to offering useful features such as greater connectivity, streamlined software, resin detection, and air purification — giving its user the beloved Prusa conveniency — and therefore elevating it from its budget competitors.
Nevertheless, there is room for improvement, and it’s up to the user to decide if the ease-of-use justifies the price difference.
Technical Specifications
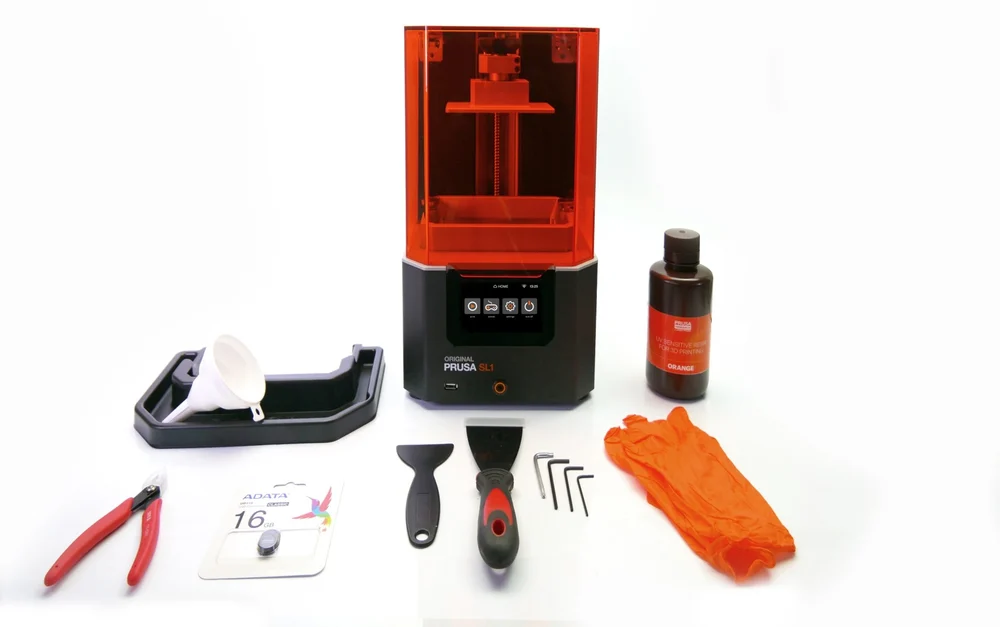
Here are the technical specifications for the Original Prusa SL-1
GENERAL SPECIFICATIONS
- Technology: MSLA
- Type: Resin
- Year: 2019
- Assembly: Fully-assembled/kit
- Manufacturer: Prusa Research
- Country: Czech Republic
3D PRINTING SPECIFICATIONS
- Build Volume: 120 × 68 × 150 mm (4.7 × 2.6 × 5.9 in)
- Layer Height: 10+ microns (0.01 mm)
- Resolution: 2560×1440 pixels
- Printing Speed: 6 seconds per layer
- Bed-Leveling: Automatic
- Display: 5.5″ full-color touchscreen
- Connectivity: USB, Wi-Fi, Ethernet
- Built-in Camera: No
- Third-Party Materials: Yes
- Materials: 405 nm UV resin
- Recommended Slicer: PrusaSlicer
- Dimensions: 400 × 237 × 225 mm
Where to Buy
You can purchase your own Original Prusa SL1 from Prusa Research.