Laser annealing does not remove anything from a metal surface. In fact, the marking does not change the surface roughness of the metal surface. It is particularly interesting for applications in which rust buildup or bioburden must be kept to a minimum.
What Is Laser Annealing?
Laser annealing consists of the slow heating of metals with a laser beam. As the metal is heated, oxygen is diffused below the surface. The metal begins to oxidize internally. Once cooled off, you are able to observe a change in the color of the metal.
The thickness of the internal oxide layer is determined by the highest temperature reached by the surface of the metal during its heating; however, in most instances, it will remain below 3000 Ao (300 nm).
The maximum temperature achieved by the surface is controlled by the intensity of the laser pulses, the speed at which the laser beam sweeps the surface and the line spacing between each consecutive passes of the laser beam.
With laser annealing, it is possible to color the surface of very specific metals: steel, titanium and stainless steel.
Laser annealing is very different from other laser marking mechanisms read Laser Etching, Engraving & Annealing: What’s the Difference? for more on the subject.
Basic Principles of Laser Annealing – Thin Film Interference
The colored look of the metal that has been processed through laser annealing can be explained by the thin-film interference phenomenon. Light shone on a metal surface that has been annealed is split into two waves. The splitting of the waves occurs by differential reflections. See the image below.
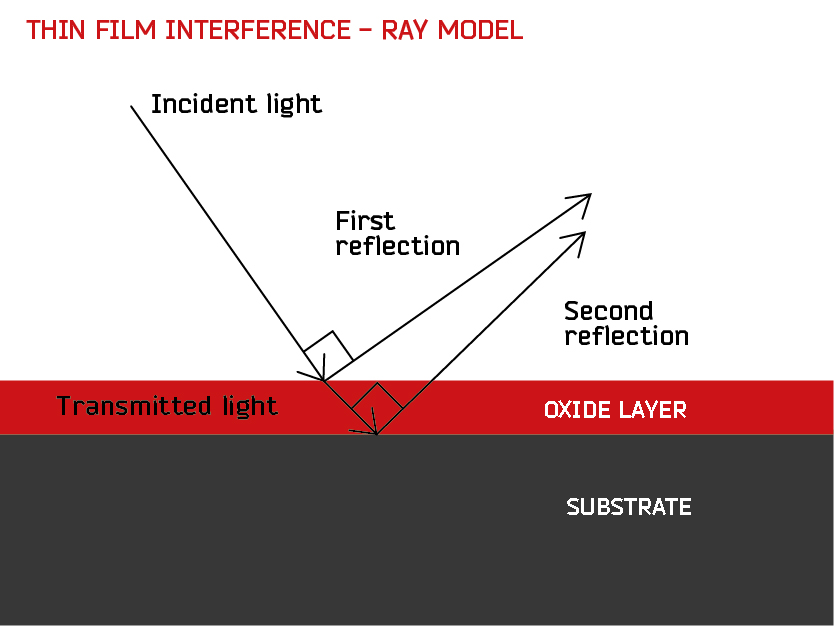
A first reflection occurs when ambient light rays hit the superficial oxide layer. A second reflection occurs when the light transmitted through the oxidized layer hits the unmodified substrate.
Looking at the metal, you can see the light that is coming towards you as a superposition of the light reflected by the superficial oxide layer and the light reflected by the substrate.
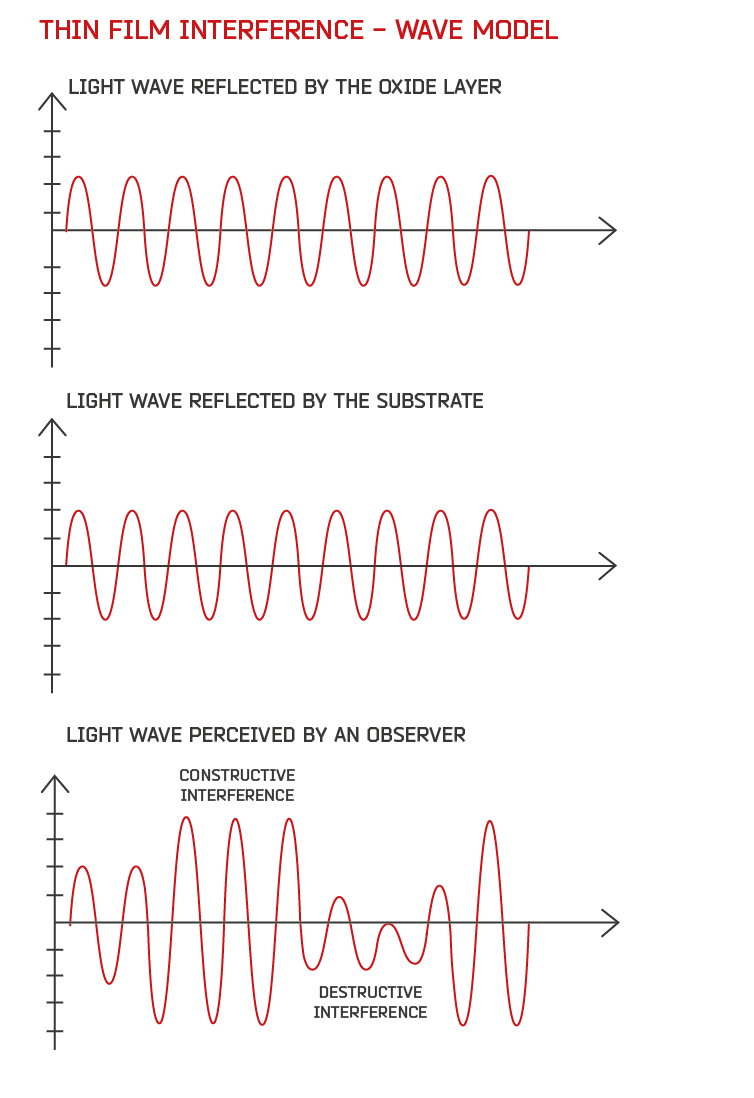
The waveforms of each of these reflections are out of phase and will have different wavelengths. The two waves interfere either constructively or destructively, giving a particular color to the metal.
The main color of the metal is given by the wavelength for which the interference between the two waves is perfectly constructive. In everyday life, this phenomenon can be seen on soap bubbles that look colored.
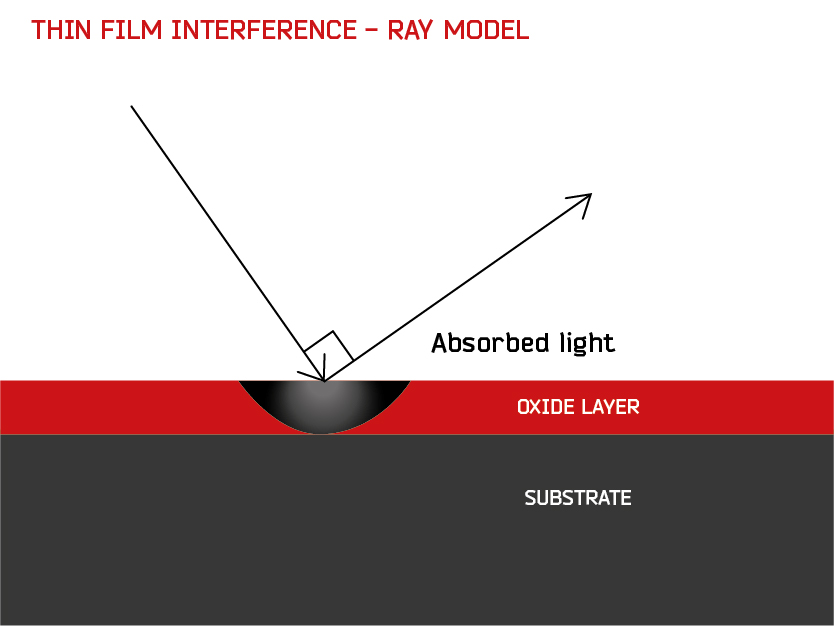
The oxide layer also absorbs a fraction of the light that passes through it. As the layer gets thicker, more light is absorbed (and less is reflected). The surface will look a little darker to you, the thicker the oxide layer gets the darker the surface will be. By tightly controlling the laser parameters, beautiful colors can be achieved, as can be seen in the image below.
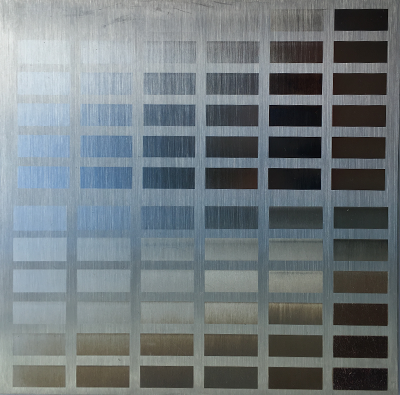
Laser Annealing of Stainless Steel: Typical Applications
Stainless steel is commonly used in the medical, automotive, food, energy and heavy industries, thanks to its resistance to corrosion and low chemical reactivity.
These properties are assured by the presence of a layer of chromium oxide that is created by a spontaneous process called passivation. It is through passivation that stainless steel is protected from rust.
Even if some of the chromium oxides is scratched off, a new layer of chromium oxide will form, maintaining the metal’s corrosion resistance and chemical passivity.
During laser annealing, the chromium oxide layer melts away. But as for a simple scratch, a new passivated layer will be created spontaneously, thereby preserving the stainless steel from further deterioration.
Passivation that occurs after the annealing process tends to deteriorate the marking on the steel. Therefore, the parameters of the writing and passivation need to be optimized in order to create a high-quality marking and ensure that the metal is still protected from corrosion.
Laser Annealing Can Be Used for Industrial Applications
Laser annealing can only be used on titanium, steel and stainless steel. The marking process can generate different colors: blues, browns and yellows. Laser annealing is particularly interesting for the identification of medical equipment as it doesn’t create any nooks or crannies that might enhance bioburden. It’s also been used for the branding of automotive parts that are prone to rust, especially in the exhaust system.