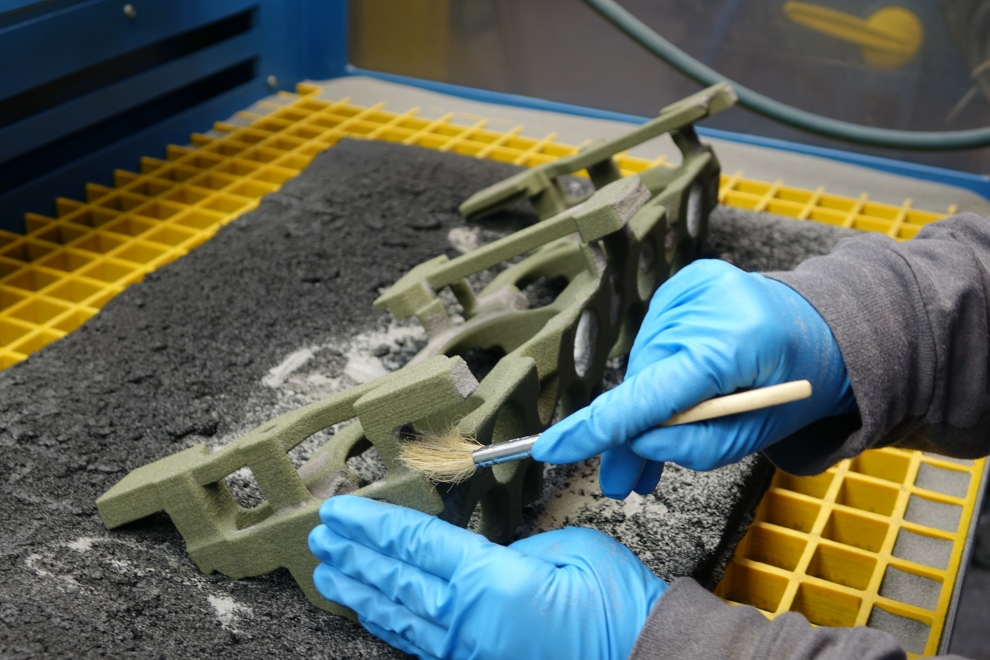
Humans began pouring the first sand castings approximately three millennia ago. And until recently, that technology has remained virtually unchanged (see Figure 1):
• A replica, or “pattern,” of the desired object is placed in an open-ended, steel molding box.
• A special type of sand is poured around the pattern, which is pounded firmly into place and then removed.
• A sprue is cut to allow molten metal to flow into the mold, along with a gate that joins the sprue to the mold cavity.
• A core is used to replicate parts having internal features.
• Molten metal is poured into the mold; when the metal cools, the completed part is removed.
That’s sand casting in a nutshell, although journeyman patternmaker Dave Rittmeyer will tell you there’s far more to it than that. Rittmeyer, the customer care and additive manufacturing manager at Hoosier Pattern Inc., Decatur, Ind., also will tell you the industry has undergone a dramatic shift over the past decade or so, thanks in part to AM.
It’s eliminated much of the tedium of the sand casting process while making the process faster, more flexible, and significantly more cost-competitive than other casting methods.
“Lead times with traditional patternmaking processes are best measured in weeks and months,” Rittmeyer said. “3D printing has drastically shortened that, sometimes to just a day or two. In one example, we tooled up for a crane case in three weeks. That normally would have taken us 14 weeks. We’re also able to print very complex molds and cores that would otherwise have been impractical to manufacture.”
Jetting Success
In 1993, researchers at MIT invented a 3D printing process called binder jet. Three years after that the company now known as ExOne Inc. took the binder jet ball and ran with it, changing the sand casting industry forever.
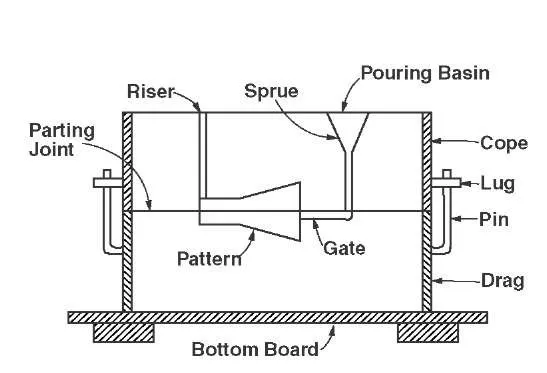
It developed a cold-hardening binder system that deposits sand in layers 0.26 to 0.38 mm thick, then binds selective areas with a liquid polymer that solidifies the sand.
Hoosier was founded in 1997 by three journeyman patternmakers who operated a couple of CNC machines. They bought their first sand printer—an ExOne S-Max—in 2013.
“Today we have more than 25 machining centers and four S-Max sand printers, and roughly half of our business is 3D-printed sand cores and molds,” said Rittmeyer. “I don’t have an exact figure, but we literally print thousands and thousands of each annually.”
The Indiana company also operates a Stratasys Fortus 450mc FDM machine and a 3ntr A2 for building prototypes, low-volume patterns, and various tooling for around the shop.
3D printing has transformed the company from a regional pattern shop to a global one. Hoosier Pattern now ships 3D-printed sand products “all over the world,” said Rittmeyer.
Higher volumes and relatively simple tooling are still produced using traditional manufacturing methods—milling, turning, and EDM—while everything else is sent to one of the company’s 3D printers. But the balance is steadily shifting to printing.
Said Rittmeyer, “For one piece, or even a hundred pieces, the [printer] usually is the way to go—although we do have one print job that calls for 2,200 parts a year, and just this morning the customer called to see if we can double that.”
Made in Montrose
Craft Pattern and Mold Inc., Montrose, Minn., is enjoying similar additive success. The company had been buying 3D-printed molds from Hoosier Pattern but, about a year ago, decided to invest in its own system.
“There were several reasons for it,” said company President Tony Cremers. “Hoosier was doing a great job for us, but when you’re spending a certain amount each month on outside services, at some point it makes more sense to bring that work in-house.
“The other part is lead time. No matter how good the supplier, having your own printing capabilities determines how quickly you can respond to your customer.”
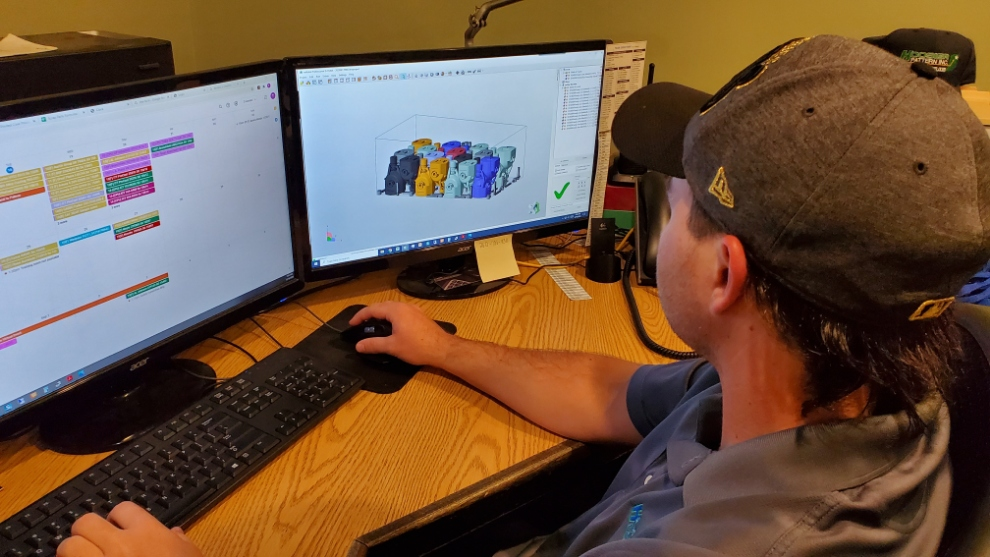
Craft Pattern started 35 years ago as a production pattern shop. It slowly expanded into prototyping and product development work then began pouring small quantities of parts. It has since added 4- and 5-axis machining services, plastic injection molding, and other capabilities.
Adding sand printing made sense. Adopting the technology, however, required Craft Pattern to learn some things about the technology.
For instance, the surface finish on a 3D-printed mold generally is not as good as one made from a pattern, said the shop’s general manager, Steve Shade. “We’ve also had to adjust our workflow and rethink some of our design practices. 3D printing affords us the ability to ignore some of the basic principles of sand casting, allowing for draft, parting, and coring configurations that simply aren’t feasible using traditional tooling.
“Our designers are no longer bound by the rules they’ve been trained to follow and worked with their entire career, which completely changes how we approach a project.”
Because of this, and other factors such as not having to physically build tooling, the timeline for delivering a cast metal part is drastically reduced.
He noted, though, that the “real elephant in the room is cost.” Whether it’s made of metal, plastic, or sand, anything that’s 3D-printed is generally going to be more expensive. “So you can’t just say, ‘Let’s print everything,’ because it’s not yet competitive from a total-cost-of-acquisition standpoint.”
With traditional tooling, the cost of patterns and core boxes can be amortized, allowing for a relatively rapid reduction in per-part cost as volumes climb. With 3D printing, on the other hand, the cost per part is fairly fixed according to the volume of printed sand, so the economies of scale do not yet apply.
“Still, if you’re looking for a few pieces tomorrow or have parts with very complex geometries, 3D printing is the answer,” said Shade.
Cremers agreed. “It’s definitely made us much more flexible,” he said, adding that the shop can shift directions quickly, even turning parts around the next day. And “it’s made a huge improvement to our core manufacturing. Where before we might have made five or 10 separate cores and then glued them together, we can now print them all as a single piece. Between the labor savings, the part quality, and just the overall process control, it’s a significant advantage.”
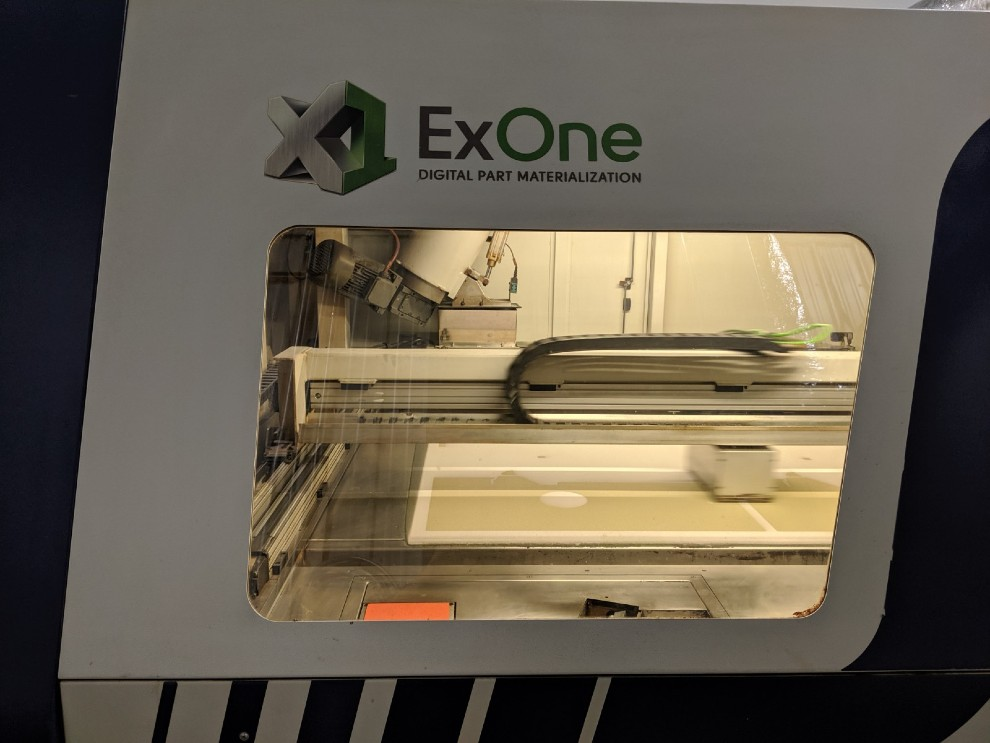