A living hinge is a marvel of modern engineering found in countless everyday products. This thin, flexible section of plastic allows for the seamless movement between two rigid parts of a single molded component. Its ability to bend and rotate, often beyond 180 degrees, makes it an essential feature in items ranging from bottle caps to storage containers.
At FacFox, we’ve encountered some inquiries from clients curious about the feasibility of 3D printing living hinges. Despite several attempts and explorations into this innovative manufacturing technique, we regret to inform that our trials have not met the desired outcomes. The challenges posed by the layer-by-layer construction of 3D printing have proven significant, often resulting in hinges that lack the necessary toughness and fatigue resistance for practical use. Here we wanna share some knowledge about the plastic living hinge.
Designing for Durability and Functionality
Plastic living hinges offer a cost advantage over traditional metal hinges in two ways:
- Simplified Manufacturing: Living hinges are a single, integrated part. This eliminates the need for separate hinge components and the associated assembly process required for traditional metal hinges. This translates to fewer parts to manufacture and reduced labor costs for assembly.
- Lower Molding Costs: Since most living hinges are a single feature, they only require one mold during the manufacturing process. This is in contrast to traditional hinges, which may require multiple molds for different hinge components. This reduces overall tooling costs.
The design of a living hinge is critical to its functionality and longevity. The hinge must be thin enough to flex yet durable enough to withstand repeated use. The most common types of living hinges include:
- Flat Hinge: A simple and widely used design, consisting of a narrow, flexible section between two larger parts.
- Double Hinge: Features two hinges separated by a landing area, allowing for greater movement and flexibility.
- Butterfly Hinge: Often used in dispensing applications, this hinge flips open or closed past a certain angle, staying in position without an intermediate state.
- Bi-stable Hinge: An advanced version of the butterfly hinge, with additional hinges that provide stability in both open and closed positions.
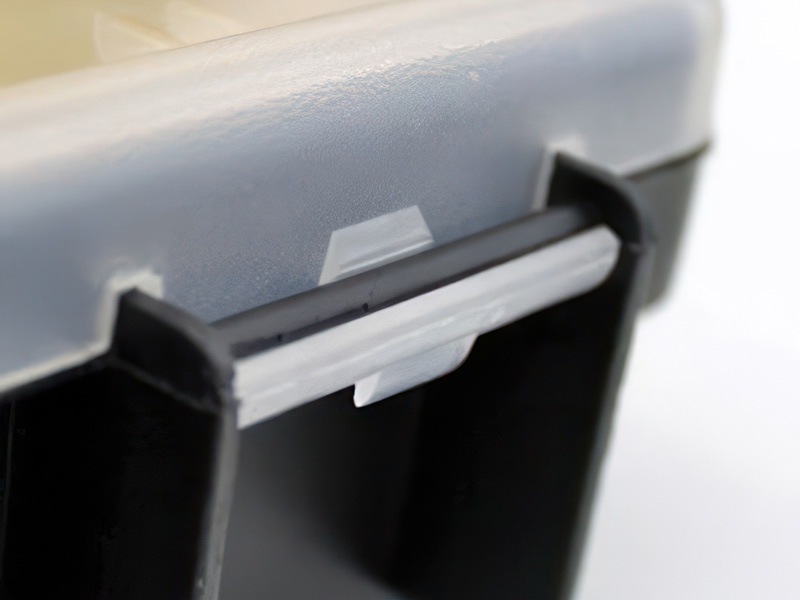
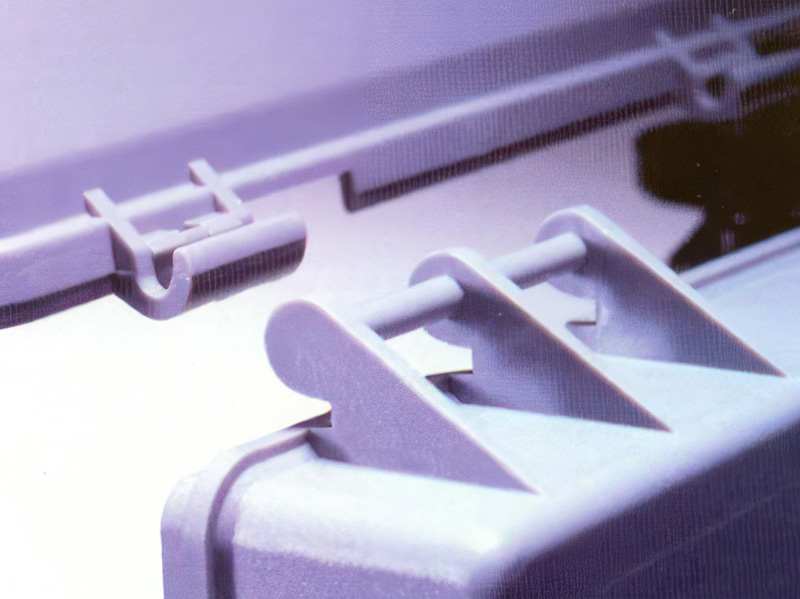
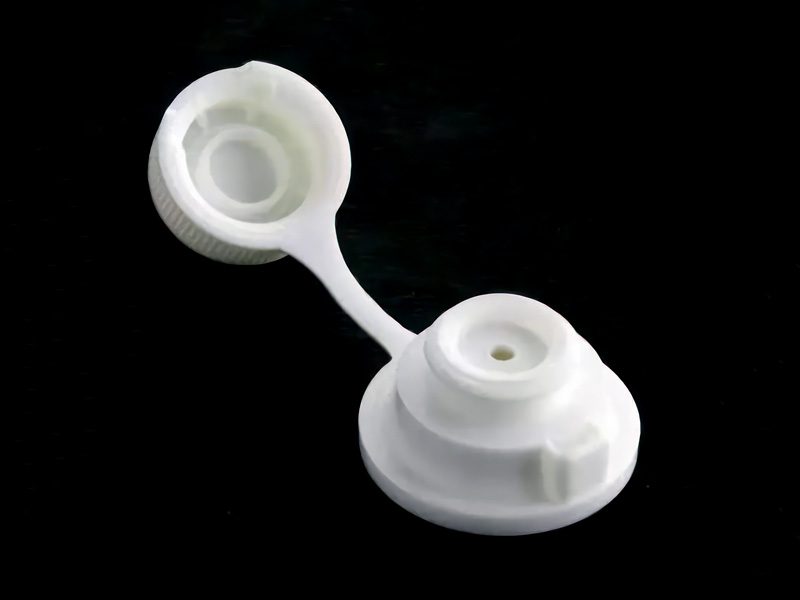
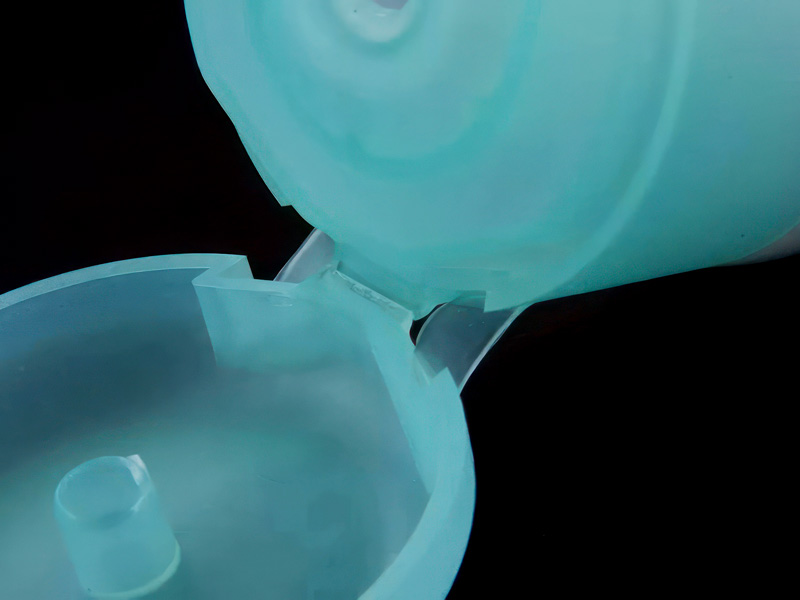
Material Matters: The Backbone of Living Hinges
The choice of material is paramount in living hinge design. Polypropylene (PP) and polyethylene (PE) are the go-to materials due to their excellent balance of flexibility and strength. These materials allow the hinge to endure the stress of bending and flexing without breaking, making them ideal for high-cycle applications.
Challenges and Solutions in Manufacturing
At FacFox, we’ve encountered some inquiries from clients curious about the feasibility of 3D printing living hinges. Despite several attempts and explorations into this innovative manufacturing technique, we regret to inform that our trials have not met the desired outcomes. The challenges posed by the layer-by-layer construction of 3D printing have proven significant, often resulting in hinges that lack the necessary toughness and fatigue resistance for practical use.
Limitations of Living Hinges:
- Material Restrictions: Living hinges primarily rely on specific plastics, like PP and PE, that offer good flexibility. While these materials are cost-effective, they have a lower load-bearing capacity compared to engineering plastics like PC and ABS. This limits the weight or stress a living hinge can handle.
- Manufacturing Challenges: While injection molding works well for living hinges, other techniques like SLS 3D printing with PP can be problematic. The layering inherent in SLS printing can negatively impact the hinge’s strength and fatigue resistance. Additionally, CNC machining of PP and PE isn’t ideal for creating living hinges due to limitations in achieving the necessary thin and flexible sections.
Applications in the Modern World
Living hinges have revolutionized the design of many products, offering a combination of reduced manufacturing costs and increased convenience. They are found in various applications, such as:
- Packaging: Easy-to-open clamshells and bottle caps.
- Consumer Electronics: Compact and durable cases for gadgets.
- Household Goods: Storage boxes and kitchenware with integrated hinges.
The Future of Living Hinges
As materials science advances, the potential applications for living hinges continue to grow. Designers and engineers are constantly exploring new ways to incorporate these versatile components into innovative products, pushing the boundaries of what’s possible with plastic parts.
This expanded post delves deeper into the intricacies of living hinge design, materials, and applications, highlighting their significance in modern manufacturing. If you have any more questions or need further details, feel free to reach out via info@facfox.com! Our engineers will respond as soon as possible.