There’s a lot more to create custom sheet metal parts than just cutting and bending a slab of metal. For each part you design, you have to consider the metal’s material qualities and the environment in which the part will be installed. Corrosion could destroy a part in short order if you choose the wrong metal with the wrong protective plating.
A second consideration is what the final product looks like. Some people like the rustic or industrial look of bare metal, but sometimes you want your parts to pop with color. For branding purposes, you might be considering adding your logo or additional text or images must be included on your part.
Typically, sheet metal parts attach to other parts as part of an assembly. Making that happen is the job of specialized hardware. Whether you want to extend the life of your part, make it aesthetically pleasing, or ensure the structural integrity of your assembly, it’s all about the finishing.
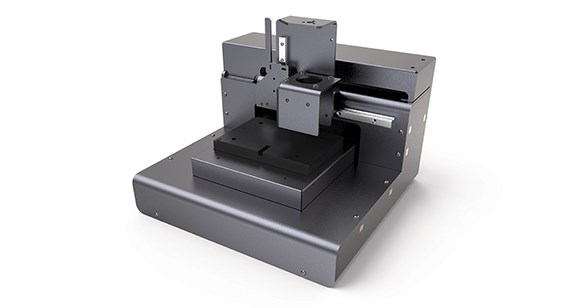
Finishes for Protection: Chemical Conversion Coatings
When iron and water mix to form the dreaded compound iron oxide (FeO2, for you chemists out there), you get rust. Because iron is present in most sheet metal, given the right conditions your part will slowly dissolve into powder. Not good. But treated with the right chemical coatings, sheet metals can be serviceable for years without showing extensive signs of corrosion.
Here are some of the most common types of chemical conversions that can keep your parts intact for years to come.
Zinc
This element is key to the coating that protects galvanized and galvannealed metals. Zinc protects the metal beneath, limiting—and even preventing—rust. In this process, zinc chemically bonds with steel, sacrificing itself when exposed to the elements, especially water, saving the core of the part. Even if the coating is mildly damaged, the presence of zinc will limit corrosive effects on your part. The visual end result of this chemical treatment is that galvanized metals have a spangled quality of silver tones and grays. Galvannealed metals have a smooth, matte-like finish that can be painted later. One thing to be aware of is that these types of metals cannot be welded because they release hazardous toxins. Instead, we can weld cold-rolled steel (CRS) and then have it plated with zinc afterward.
If you need zinc plating applied after a part has been created, that can be done either through an acid or alkaline process. Acid zinc is quickly applied and covers the part well, but it doesn’t always spread uniformly. On the other hand, the alkaline zinc process takes longer because it requires electroplating. An electrical current is run through a zinc bath, causing zinc ions to flow and attach to your core material. The advantage of this process is that metals treated in an alkaline zinc bath have a coating that is more uniform and more accepting of stretching and forming.
Chromate Conversion
Zinc isn’t the only chemical that helps avoid corrosion. Chromate conversion, adds the bonus of electrical conductivity to aluminum, zinc, tin, silver, magnesium, or cadmium parts. The finish ends up clear to yellow in quality. There are different treatments used to coat different metals, but ultimately chromate can act as a protective primer of sorts that allows you to paint a surface. Note that steel and iron-based metals cannot be chromated directly—you would first need to pretreat with zinc.
Anodizing
This method works by placing a sheet of aluminum in an acid bath filled with electrolytes. When you run electricity through the tank, the surface of the aluminum will hook up with oxygen atoms in the electrolyte to form aluminum oxide ( Al2O3). This would happen normally in the real world, but doing it in a controlled environment quickly yields an attractive, smooth, corrosion-resistant surface. You may like the finish just like that, but because the surface is porous, you can also add color and an additional sealant. One thing to remember is that while anodizing works well with aluminum, it does not with CRS.
Passivation
Another way to protect the surface integrity of your part is to passivate the surface. One of the most interesting things about this process is that no one really knows how it works. What is known for certain is that passivation adds an extremely thin layer that protects the surface of stainless steel from corrosion. Doing the process wrong, though, can create more opportunities for corrosion than not doing it at all, so cleaning the metal well before treatment is critical to successful passivation.
Looking Sharp: Sheet Metal Coatings for Aesthetics
Chemical coatings are great at protecting your parts, but maybe you have something more colorful in mind? If so, you should consider one of these two popular metal finishing processes: powder coat or silk screening.
Powder Coating

The name of the process says it all. With powder coating, the objective is to cover as little or as much of an object as you want with a pigmented powder. It seems simple, but there are several steps to make it work properly.
First, your part must be cleaned so the powder can adhere to it. Then, it is attached to an electrically charged wire—typically made of copper. The powdered pigments spray out of the end of a nozzle at your part, powered by a compressor. Because the powder is electrostatic, it loves to stick to charged surfaces. A skilled finisher targets the spray to evenly coat the part. At this point the powder can still come off easily, so your part must be handled carefully.
Once the part has been coated, it goes into a 400°F oven to bake for about 20 minutes. The thermoset polymer in the powder melts and hardens in the oven. In the end, the powder coating leaves your part with a smooth, even surface.
Silk Screening
Let’s say you want to add your logo or some explanatory information to your part. Silk screening is the way to go. You provide the design and text you want transferred. We then use a process that incorporates the design file you provide onto a very thin, fine-mesh screen, upon which we put large blob of ink. When pressure is applied to the layer of ink, it can flow through the screen and onto your part, limited to the areas where you want it to appear. Once transferred, we apply heat to the ink, bonding it to your part. Silk screening works well on raw metal or coated surfaces, and just as with powder coat, we can match your desired Pantone color.
Forming a Final Part
Aesthetics are one of the most critical aspects of custom sheet metal parts. A highly cosmetic part or assembly of parts can be the difference between product success or failure. At FacFox, we strive to offer a range of sheet metal finishing options that can address a variety of needs, both cosmetic and functional.