What is Vinyl Plastisols?
The purpose of this article is to provide an overview of vinyl plastisol and starting points in setting up and running the rotational molding of vinyl plastisol parts. Polyethylene (PE), in general, is the largest polymer consumed in the rotational molding process. Vinyl plastisols differ from polyethylene in that they flow out and coat the inner mold surface until the gel temperature is reached. The gel temperature of a plastisol can be altered to facilitate the molding of certain shapes. Vinyl powders differ in that the mass of material first distributes over the entire inner mold surface. As the mold is heated, it forms a skin and gradually melts to form a uniform layer of plastic.
Advantages
The advantages of rotationally molding with vinyl plastisols are:
- The liquid form allows for ease of handling and the ability to easily meter
- small quantities, thus controlling inventory costs;
- Mold detail and finish replication is excellent;
- Readily pigmented and offers good color stability;
- Paints and topcoat lacquers can be applied ;
(Note: Check with the supplier to be sure that the specific paint or lacquer utilized is compatible with vinyl.) - Offers a wide range of properties (i.e. hardnesses, chemical resistance, etc.);
- Relatively low material cost compared to other materials.
Applications
Commonly produced parts from rotationally molded plastisol include:
- Hobby Horses (one of the first applications for rotationally molded plastisols);
- Playballs and Sport Balls (i.e. volleyballs, tetherballs, basketballs, etc.)
- Industrial Seating Components;
- Automotive Interior Components (i.e. crash pads, visors, armrests, gear shift boots, etc.);
- Toys;
- Medical Devices and Models;
- Boat Bumpers;
- Miscellaneous Sporting Goods.
Manufacturing
When selecting a vinyl plastisol for rotationally molding, in addition to hardness and environmental considerations, one should also consider other potential areas of performance, such as electrical performance, foamability, and the use of inserts (inserts should be primed prior to use) to maximize product acceptance.
Variables in vinyl plastisol rotational molding include:
- Part Shape,
- Ratio of Rotation,
- Speed of Rotation,
- Oven Temperature and Cycle Length,
- Cooling Spray, and
- Mold Temperature,
Part Shape
When first starting to run a plastisol without any processing direction, refer to the attached Rotation Ratio for Typical Shapes table. This table provides basic ratio starting points for many shapes.
Ratio of Rotation
Once the starting point ratio is decided, you are ready to set the controls. Generally, the ratio of rotation is a function of Part Shape.
Most people become confused when calculating the rotation ratio. The major axis is the inner shaft in the arm. The largest wheel located on the arm denotes the major. The minor axis is the outer shaft on the arm. The smaller wheel located nearest the oven denotes the minor. The major axis turns in the vertical plane and the minor axis turns in the horizontal plane.
It is important to remember, the ratio of rotation is a function of the shape being molded. A symmetrical shape, such as a round sphere or cube runs easily at a 4 to I ratio (major to minor axis rpm speed.). To set the ratios, determine the revolution per minute (rpm) of each axis. The rpm speed is easily determined by checking the time required, in seconds, to make one revolution of the major and minor drive shaft wheels (Major: largest wheel, Minor: smaller wheel). See the attached reference chart for converting how long it takes in seconds for one complete revolution to rpm. On most machines, the dials indicating rpm are not accurate and it is best to manually check the rotation speed with a stopwatch.
With the speed (rpm) of each axis determined, the ratio of rotation can be calculated as follows:
Ratio = Major Axis rpm/(Minor Axis rpm – Major Axis rpm)
For example, a Major Axis rpm of 8 and a Minor Axis rpm of 10 equals:
Ratio = 8/(10-8)=8/2=4/1
In a situation where the Major axis is one-half the rpm of the minor axis, the ratio is 1 to 1. For example, the Major Axis rpm equals 5 and the Minor Axis rpm equals 10, the resultant rotation ratio is 1 to 1. The mold mounting shaft on the minor axis (horizontal plane) therefore rotates once for each rotation of the major axis (vertical plane). A rotational ratio of 1 to 1 is not recommended.
As the rpm speed of the Minor axis approaches that of the Major axis the ratio gets larger. For example, if the Major Axis rpm equals 8, and the Minor Axis rpm equals 10, the resultant rotation ratio equals 4 to 1. When the Major Axis rotation rpm equals 8, and the Minor Axis rpm equals 9, the rotation ratio equals 8 to 1. At a ratio approaching infinity, relative rotation stops. To achieve reverse rotation, lower the Minor Axis rpm to a lower speed than the Major Axis rpm. For example, when the Major Axis rpm equals 8 and the Minor Axis rpm equals 6, the resultant rotational ratio is a negative 4 to 1.
In a negative ratio the spin is about the minor axis in the opposite direction. Negative rotation ratios tend to direct the flow more to the horizontal plane and causes poorer fill in complicated molds.
Speed of Rotation
Once the rotation ratio has been determined, the next consideration is the speed of rotation. Speed is simply how fast the major and minor axis wheels revolve in relation to rpm. For example, a Major Axis rpm of 8, and a Minor Axis rpm of 10 is a ratio of 4 to 1, whereas a Major Axis rpm of 12 and a Minor Axis rpm of 15 is also a 4 to 1 rotation ratio.
The speed of rotation is a function of vinyl plastisol viscosity and gel temperature. It is believed that a high gel temperature plastisol runs best at relatively slow rotation speeds. If the viscosity of the plastisol were low or thin, it would require increasing the speed of rotation. When the viscosity is high or thick, slow speeds would be best. The same effect is somewhat the same for lower gel temperature plastisols, viscosity, and running at faster speeds of rotation.
High speeds of rotation can cause problems because of the gyroscopic forces created. With large molds, this instability can result in machine damage.
Setting the speed of rotation and/or rotation ratio is accomplished by changing the pot settings on the machine panels. Increasing the pot setting increases the revolution speed and the rpm and vice-versa. With most machines, there is no correlation between how much a pot setting change will affect the rpm. Trial and error will be needed to determine the effect of any changes.
Seemingly minor pot setting changes may have drastic effects on ratio. To hold the ratio at a given reading requires adjusting both the major (inner shaft) and minor (outer shaft) proportionally.
Oven Temperature and Cycle Length
Generally, for the best vinyl plastisol distribution throughout the mold, lower temperatures and increased cycle times should be utilized. The entire plastisol mass must typically reach 350ºF (177ºC) for complete fusion to occur and optimum physical properties to be achieved. Complete fusion results in the development of ultimate physical properties.
Vinyl plastisols can be formulated to act differently under the same temperature/cycle time relationship. Some materials have a definite or sharp gel temperature and others are slower to react to temperature.
Trial and error will determine the highest temperature and shortest cycle time for an acceptable finished molded product. The balance of high oven temperatures, to achieve a quick cycle time, with the potential burning of the surface of the part, as observed through the development of a yellow or brownish tint on the surface of the part is critical.
Because plastisols gel (solidify) with heat, damper control is recommended on most all plastisol parts. When the damper is open, the heat blast from the oven burner potentially creates hot spots on the mold. By closing the damper for the first several minutes of the cycle, the plastisol will evenly distribute in the mold rather than gel faster on the hotter portion of the mold.
Cooling Spray
Many polymers used in rotational molding are sensitive to cooling cycles. These materials can often shrink uncontrollably when cooled too quickly. Fortunately, vinyl plastisols are not affected in this manner. However, cooling should be done in a manner so as not to damage molds as a result of rapid cooling of metal molds or result in corrosion of the cooling chamber.
A vinyl part will exhibit shrinkage. The shrinkage rate for vinyl will be approximately two percent from the mold dimensions and may vary as the vinyl plastisol formulation is changed.
If the article to be molded is difficult to strip form the mold, removal of the part is more easily accomplished with warm molds. Vinyl plastisol formulations can sometimes be compounded with raw materials to improve mold release performance. Commercially available mold release agents can also be utilized with difficult to remove parts. Testing should be conducted to insure that the mold release agent does not create any issues with the mold or the molded part.
Mold Temperature
When charging molds with plastisol, the best condition for molds is if they are at a temperature warm to the touch. If the molds are too hot when filled with plastisol, the plastisol can begin to gel on the mold surface resulting in poor plastisol distribution within the mold and an uneven part wall thickness. To eliminate this problem, increasing the length of the cooling spray to lower mold fill temperature is recommended. If a hot mold is required for easier part stripping, a higher gel plastisol may be required to get uniform distribution.
CONCLUSION
Trial and error will determine the best conditions under which to produce consistent rotationally molded vinyl plastisol parts. The rotomolder should use extreme care during the trial and error process as the burning of material in the mold may result in damage to the molds.
- Every shape to be molded has an optimum rotation ratio. Select a ratio that best describes the shape to be molded as a starting point.
- Speed of rotation with plastisols is important. When changing speed, remember to keep the rotation ratio constant. Plastisol gel temperature and viscosity are the major speed of rotation factors.
- Start with an oven temperature of 450ºF (232ºC) and a cycle long enough to achieve fusion. Fusion is best checked by examining a glossy air surface and/or by measuring for the development of ultimate physical properties. Faster production requires higher temperatures and shorter cycle times.
- Set the damper control to close for the first three minutes of the cycle. If the mold shape is not critical to the oven heat blast, leave the damper open and shorten the oven cycle as a result of the hotter oven temperature.
- Set the cooling spray for a period of time so that the molds are warm to the touch when unloading.
Remember: select a ratio and a speed of rotation. Check and adjust the pot settings to the proper rpm. Most importantly, be sure the plastisol is fused properly by using a high enough temperature and long enough cycle time. Trial and Error will determine the best set of using conditions.
Each rotationally molded plastisol item has optimum settings for the best possible part.
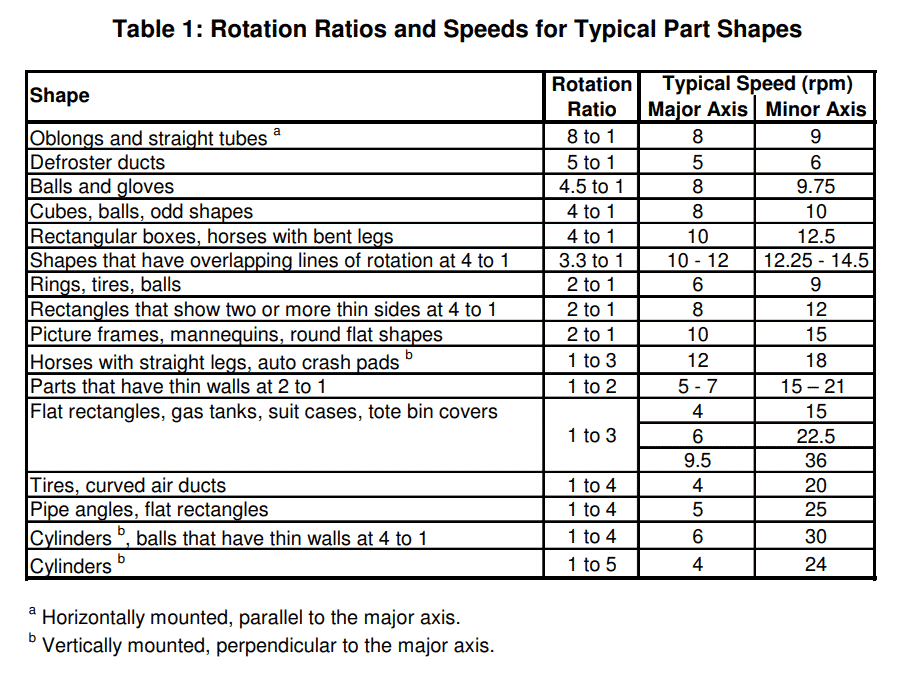