3D printing has revolutionized prototyping and manufacturing, allowing for the creation of complex and intricate designs. However, those first-layer prints often lack the desired finesse, showcasing visible layer lines and a rough texture. This is where post-processing techniques like vapor smoothing and vibration finishing step in, transforming your 3D prints into professional-looking masterpieces.
Delving into the Details: Vapor Smoothing
Imagine achieving a smooth, flawless finish like injection-molded parts. Vapor smoothing, also known as chemical vapor smoothing, utilizes this magic. Here’s a closer look:
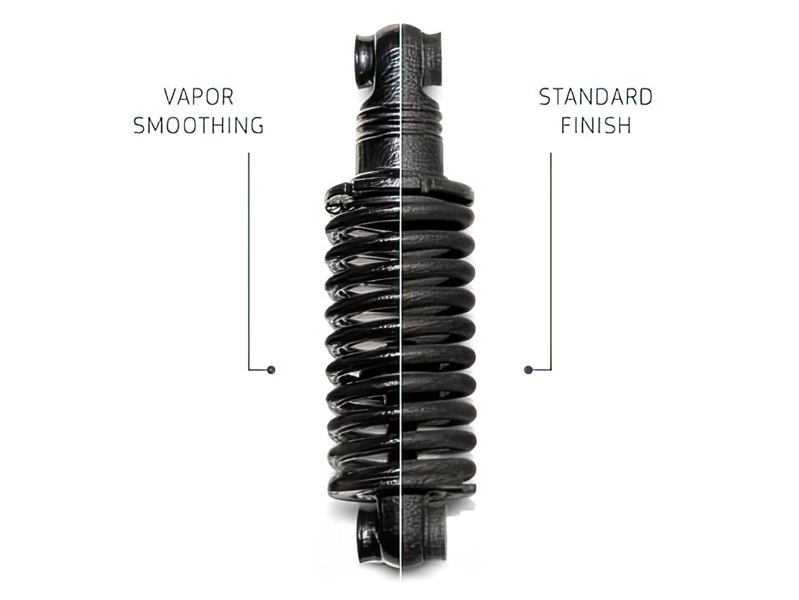
- The Process: Parts are suspended within a sealed chamber. A controlled amount of solvent vapor, commonly a mixture like FA 326, is introduced. This vapor condenses on the part’s surface, gently melting the outermost layer. As the chamber heats up, the remaining solvent evaporates, leaving behind a smooth, unified finish.
- Benefits:
- Superior Finish: Vapor smoothing delivers a high-gloss, water-resistant surface, ideal for applications requiring a polished aesthetic and protection from the elements.
- Enhanced Performance: The process strengthens the part, improving its tensile strength, elongation, and other mechanical properties.
- Preserved Detail: Unlike some methods, vapor smoothing excels at maintaining intricate details even on complex parts.
- Considerations:
- Material Matters: Not all filaments embrace vapor smoothing. While ABS, ASA, Nylon, and some Polycarbonate blends respond well, materials like TPU and certain specialty filaments are not recommended.
- Precision is Key: Overexposure to the solvent vapor can lead to warping and loss of detail. A controlled environment with proper equipment is crucial for achieving optimal results.
- DIY vs. Industrial: While a DIY approach using solvents like acetone is tempting, safety concerns are paramount. Industrial-grade equipment and proper ventilation are vital for safe operation.
The Power of Friction: Unveiling Vibration Finishing
This method employs a different approach, leveraging a tumbling barrel filled with abrasive media. As the barrel vibrates, the media creates friction against the part, gradually smoothing its surface.
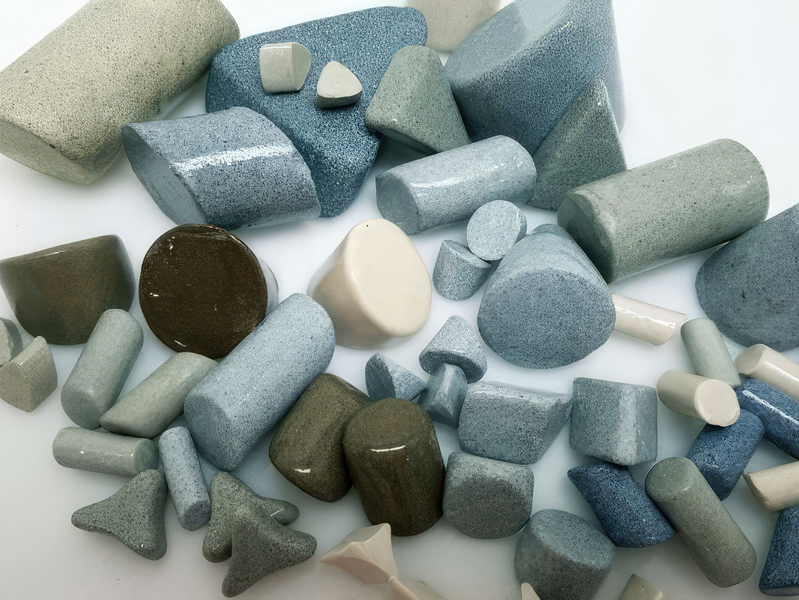
- The Process: 3D-printed parts are placed in the barrel along with selected abrasive media and a lubricating compound. The machine’s vibration creates friction, polishing the part’s surface. Two primary methods exist: vibration and tumbling. The vibration method is faster and ideal for larger, less intricate parts. The tumbling method offers a gentler touch, suitable for delicate and detailed pieces.
- Benefits:
- Material Versatility: Unlike vapor smoothing, vibration finishing works wonders on a wider range of materials, including metals, thermoplastics, and even some elastomers.
- Durable Finish: The process creates a smooth, scratch-resistant surface, ideal for parts that experience wear and tear.
- Customizable Touch: By selecting different abrasives (ceramic, plastic, or steel), you can achieve varying finishes, from high-gloss to a more subtle polish for a pleasant touch.
- Considerations:
- Geometry Matters: While effective, vibration finishing can slightly round sharp corners and edges. Careful media selection might be required for parts with intricate features.
- Drying Time: Following the process, an additional drying step is often necessary to remove the lubricating compound.
- Not Water-Resistant: Unlike vapor smoothing, vibration finishing doesn’t create a water-resistant surface.
Choosing Your Champion: A Matter of Project Needs
Selecting the ideal technique depends on your specific project requirements:
- Material Compatibility: Ensure your chosen filament aligns with the process capabilities.
- Desired Finish: For a high-gloss, water-resistant finish, vapor smoothing reigns supreme. If a smooth, scratch-resistant surface suffices, vibration finishing might be your pick.
- Part Complexity: Vapor smoothing excels with intricate details. If sharp corners are crucial, vibration finishing with well-chosen media might be the better option.
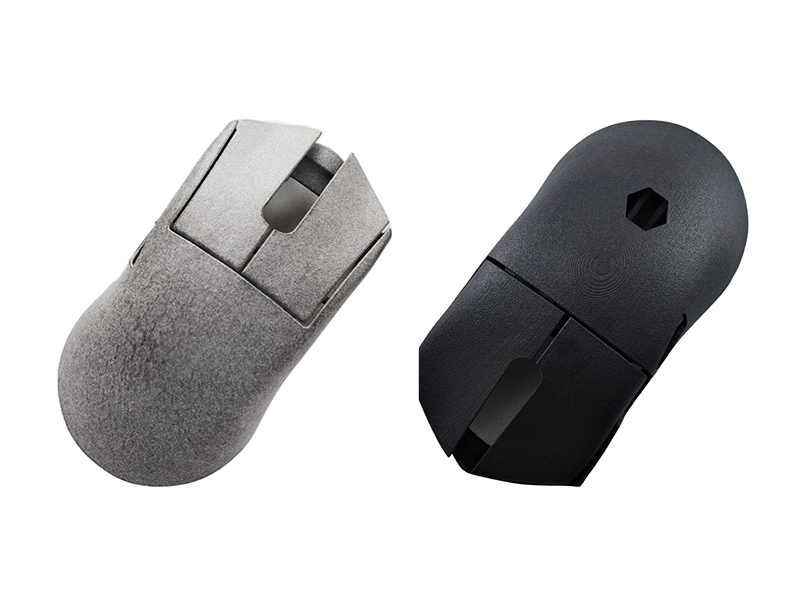
Industries Embracing the Shine
Both vapor smoothing and vibration finishing find applications across various industries:
- Medical: These techniques create smooth, potentially antimicrobial surfaces for medical devices.
- Automotive: They ensure smooth, functional parts for vehicles, enhancing performance and aesthetics.
- Aerospace: They contribute to the creation of lightweight, high-strength parts for aircraft.
- Consumer Goods: They bring a polished touch to jewelry, tableware, and other consumer products.
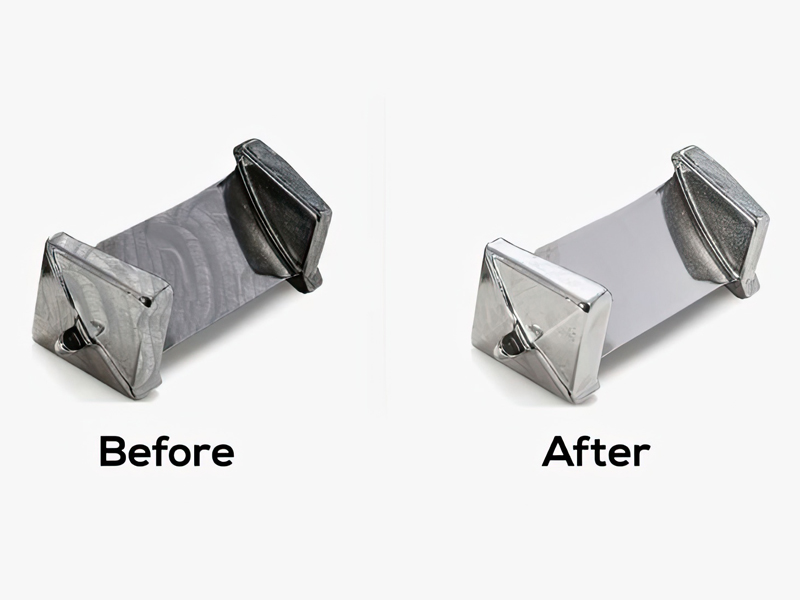
The Final Verdict
By understanding the strengths and limitations of vapor smoothing and vibration finishing, you can elevate your 3D prints to a professional level. Consider the material, desired finish, part complexity, and safety factors to choose the champion for your project. With the right technique, your 3D prints will transform from rough prototypes to polished masterpieces, ready to impress and perform!
Beyond the Basics: Advanced Considerations
- Environmental Impact: Both techniques have environmental considerations. Industrial vapor smoothing can generate hazardous waste, requiring proper disposal procedures. Vibration finishing can create dust and require proper ventilation.
- Cost Factors: Industrial-grade equipment for both methods represents a significant investment. Smaller-scale DIY setups might be an option for hobbyists, but prioritize safety with proper ventilation and equipment.
- Professional Expertise: For complex projects or critical applications, consider partnering with professional finishing services. They possess the expertise and equipment to achieve optimal results.
The Future of Finishing
As 3D printing technology continues to evolve, so too will post-processing techniques. Here’s a glimpse into what the future might hold:
- Sustainable Solutions: The development of eco-friendly solvents and media for both processes can minimize environmental impact.
- Automation Integration: Seamless integration of post-processing steps into the 3D printing workflow will enhance efficiency and streamline production.
- Material Innovation: New 3D printing filaments designed for optimal compatibility with specific finishing techniques will further enhance results.
By staying informed about these advancements, you can leverage the ever-expanding capabilities of 3D printing technology to create truly exceptional finished products.
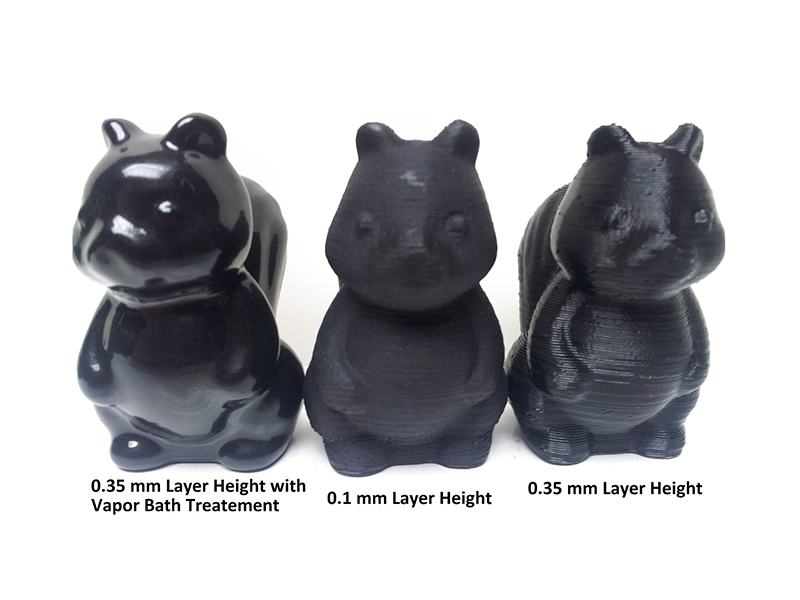
FacFox: Bringing Your 3D Vision to Life
Ready to unlock the full potential of your 3D prints? FacFox offers a comprehensive suite of 3D printing and post-processing services to meet your exact needs. Our team of experts can guide you through material selection, recommend the most suitable finishing technique (vapor smoothing, vibration finishing, and more!), and handle the entire production process with precision and care.
FacFox delivers:
- High-Quality Printing: State-of-the-art 3D printers for exceptional results.
- Expert Finishing: Achieve the perfect surface texture and functionality for your project.
- Fast Turnarounds: Get your finished parts quickly and efficiently.
- Competitive Pricing: Transparent pricing models to fit your budget.
Transform your 3D ideas into reality with FacFox. Visit our website or contact us via info@facfox.com today for a free quote!