Not all products can be 3D printed. Nor should they be. Why? Because 3D printing will never rival the economies of scale found in mass-produced commodities.
The benefits of doing this are so big that, according to this 2018 Gartner study, 38% of supply chain managers are already using 3D printing, and 47% plan to use it in the next two years.
If more than 8 out of 10 supply chain professionals will have soon implemented 3D printing in their distribution networks, then your business probably should too – especially considering the speed of change in today’s post-pandemic markets and supply networks.
1. 3D print to avoid the negative effects of outsourcing
For decades, businesses have outsourced to companies using traditional manufacturing practices. It made economic sense to do so. But as international freight costs increase, and as trade tariffs fill more headlines, global logistics is becoming riskier and more expensive.
Add to that the time required to negotiate with multiple suppliers, independent contractors, the challenge of communicating via different time zones, and different languages. More fragmented than ever, outsourced supply chains have begun to lose their luster.
By contrast, 3D printing’s biggest advantage is that it is not an isolated manufacturing operation. It offers an end-to-end process that serves as a fully fledged production method.
Best of all, it doesn’t follow the traditional SCOR supply chain method of plan, source, make, deliver, return. It means you can avoid the risk of forecasting demand. After all, if you guess the wrong answer to ‘how many products will I sell?’, that means reduced profitability.
Instead, 3D printing really shines in the areas of low-demand, slow-moving products. According to this DHL report, spare parts inventory can account for more than 20% of an average company’s unused or excess stock. And no wonder: automotive manufacturers (for example) must stock spare parts for seven to 10 years for every vehicle they make.
2. Huge savings for simplified supply chains
It’s not uncommon for us to mention the ROI of 3D printing compared to outsourcing. What’s not so frequently mentioned are the hidden savings gained from supply chain simplification. Below are five examples of how 3D printing can generate even more returns on your investment:
Transport costs
If your business still runs the logistical gauntlet of producing and shipping spare or slow-moving parts from overseas, then there are some easy savings to be made. This research suggests that by installing a 3D printer in your warehouse for on-demand part manufacture, you could save up to 85% on shipping costs.
Storage and warehousing
By consolidating your slow-moving and excess inventory to free up warehouse space, the same research suggests you can save up to 17% on storage. And that’s not to mention the extra time saved by not having to check and rationalize that inventory cycle stock and safety stock. Plus, you can avoid any stockout costs because parts are printed to match demand.
Low-cost production
For a few dollars each, 3D printed parts can be made on demand with physical qualities that approach those of injection-molding. This is especially true for the Ultimaker S5. With a reinforced feeder mechanism and the print core CC Red 0.6, this large volume printer can extrude advanced, abrasive composites and plastics from the world’s leading materials providers. Ultimaker is also a market leader in making professional 3D printing easy to use. No specialist training is required to operate the machines: onboarding new users typically takes less than three hours. And prints require minimal post-processing.
Less wasted material
3D printing produces parts layer by layer. As opposed to subtractive manufacturing methods, like CNC machining, additive manufacturing places filament only where it is needed. Less wasted material means fewer transportation and waste disposal costs, while also being more environmentally friendly.
Reduced labor
In the past, outsourcing to overseas factories worked because labor rates were cheap. 3D printing reduces dependence on this variable. In fact, one person can operate a small spare parts production facility right inside your warehouse. This is thanks to increased printer uptime and reliability, with network-enabled machines controlled via intuitive printer management software, like Ultimaker Digital Factory.
3. Make your entire value chain more agile
Traditional supply chains are not known for their responsiveness. By reducing the manufacturing duration and cutting out overseas transportation, 3D printing almost negates lead times. Depending on their complexity, most printed parts are produced in hours, not weeks. And production output can be easily scaled with multiple machines to meet demand.
By taking advantage of this infinitely flexible and highly responsive order fulfillment, your company will gain a competitive edge. And as you increasingly transform your supply chain to this modern pipeline, you will be able to take advantage of other efficiencies – like shorter product cycles.
4. 3D printing’s unique product performance
3D printing offers small batch manufacture with a significant advantage: geometric freedom. End-use and spare parts made using traditional production methods, like injection molding, must follow restrictive design-for-manufacturing rules. These rules change substantially with 3D printing, allowing more exotic and efficient geometries, which can also leverage generative design. This technique uses AI to improve structural performance, saves material use, and can further shorten the design-to-manufacturing cycle.
Multiple parts can also be consolidated into a single, stronger part. For example, Snow Business uses Ultimaker 3D printers to print the intricate geometries needed for their snow machines’ nozzles.
5. Competitive differentiation through on-demand
In the same way that Uber disrupted the taxi industry, and Airbnb the hospitality industry, consumers have increasing control over supply chains. As digitization fuels the ‘demand economy’, 3D printing synergizes perfectly with connected manufacturing.
This on-demand part production provides the opportunity for greater levels of personalization for finished or almost-finished goods. For example, clothes with personalized printed elements, or a smartphone case with a custom design. Parts can also be individualized, such as manufacturing aids with ergonomics specific to the worker.
Best of all, when it comes to slow-moving parts, 3D printing offers guaranteed product availability through on-demand manufacture. Essentially, 3D printers can replace your ‘just-in-time’ inventory. Already a reality, virtual warehouses can send 3D model files digitally to the nearest 3D printer. And logistics companies like DHL and UPS are already using 3D printing to supplement their ‘end-of-runway’ services when specific parts are needed in the fastest possible time.
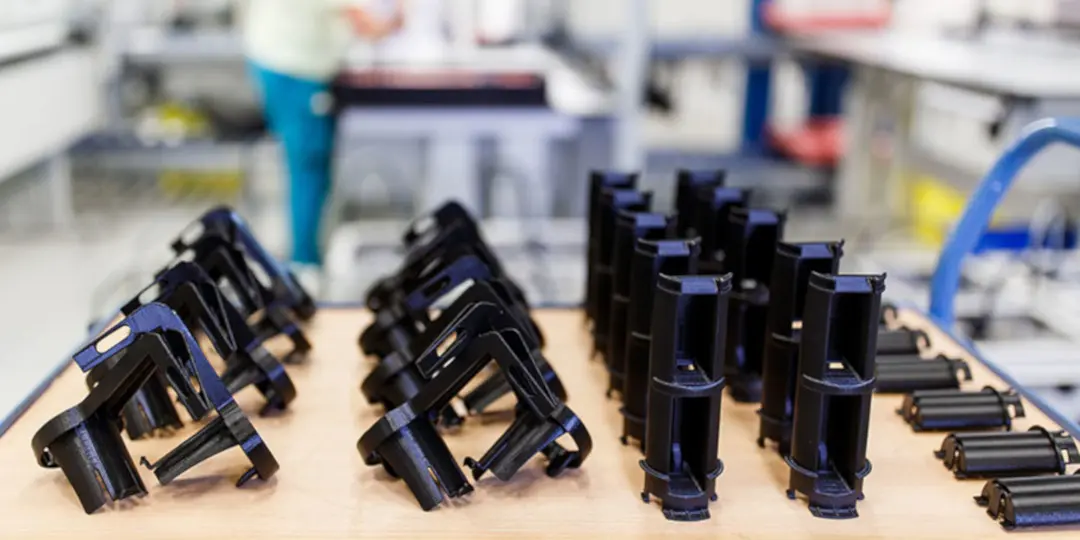
6. Improved customer satisfaction
Embedding 3D printing in your supply chain will even improve customer satisfaction and loyalty. This will be especially true when your company can maintain service levels at 100%.
As a recognizable technology, 3D printing is more consumer-friendly. It offers not only the creation of jobs, but the return of native jobs from anonymous factories.
Conclusion
We’ve already seen developing countries skip landline phones in favor of cell phones. Technology that’s more flexible and requires less infrastructure is always preferable. It is therefore no stretch to imagine those same countries skipping the complex supply chains we rely on today, for methods which embrace Industry 4.0.
Not everything should be 3D printed. But with its multiple benefits – like solving the perennial challenge of a ‘just in case’ stockholding – 3D printing technology offers supply chain opportunities that shouldn’t be overlooked.