Introduction
Generally, accuracy means how close a measurement is to its true value. In 3D scanning, accuracy generally refers to single scan accuracy, but then there’s also volumetric accuracy.
When it comes to resolution, whose general definition is how sharply an image can be displayed, there can also be two values in 3D scanning. 3D scanner OEMs generally refer to mesh resolution– i.e., the distance between points within a point cloud (3D mesh)– when specifying resolution. But, some also specify measurement resolution.
All of these terms can be a bit confusing, and 3D scanning is already a complex enough technology. Let’s go over the basics!
3D scanning accuracy
What is accuracy?
The general definition of accuracy is how close the measurement is to its true or tolerable value. It is often confused with precision, which is how close different measurements (of the same target) are to each other. The simple graphic below illustrates the difference between accuracy and precision:
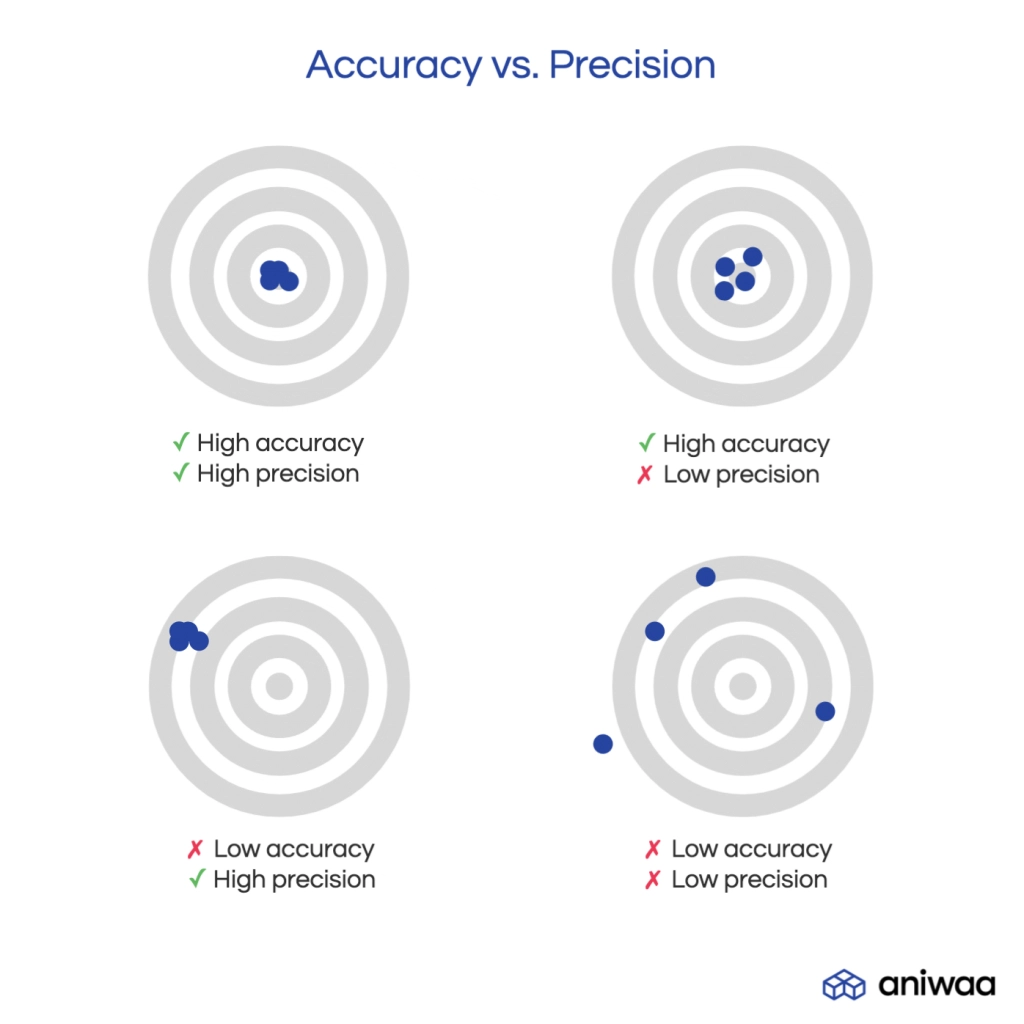
In 3D scanning, accuracy is how close the scanner’s measurements are to the object’s true size. If you measure a cube with an industrial caliper and obtain a width of 200mm, but your scanner captures the cube as 205mm-wide, then it is quite off.
Two types of accuracy specifications exist in 3D capture: single scan accuracy and volumetric accuracy.
Single scan accuracy vs volumetric accuracy
In spec sheets, accuracy often means single scan accuracy. It is the accuracy of one image capture.
Example: 0.05mm accuracy.
Most 3D scanner OEMs also specify volumetric accuracy. It is the accuracy of several captures, and this global accuracy diminishes the bigger the scanned part is.
Example: 0.05mm + 0.15mm/m.
Following our example, if your part measures 2 meters long, the accuracy of your scanner will be 0.05 + (0.15*2) = 0.035mm. That’s quite a difference from the original, single scan accuracy! Volumetric accuracy is thus more important to consider than single scan accuracy, especially if you are going to 3D scan large objects (e.g., cars).
That said, some 3D scanners with integrated photogrammetry modules can build up a sort of 3D skeleton of the object (with adhesive markers) before filling it in with the rest. Markers are precise reference points for 3D scanners, like a connect-the-dots drawing. By using a photogrammetry-sourced “skeleton”, your data is bound to be more accurate.
Note: Photogrammetry is a 3D scanning technology that involves taking multiple photographs of an object from different angles in order to calculate its shape and size.
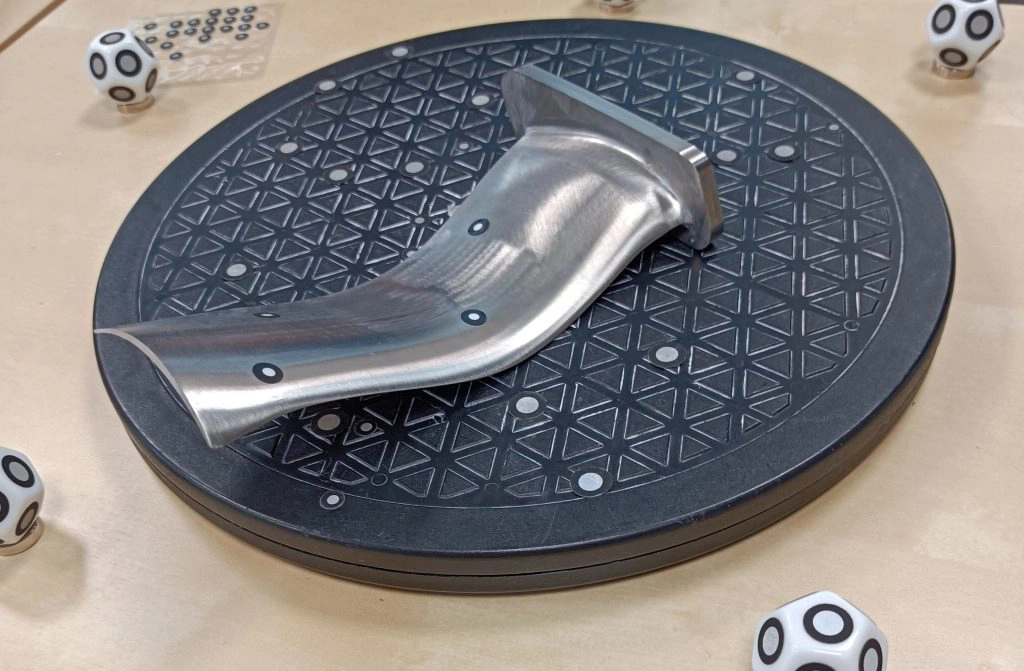
How accurate are these specifications?
Manufacturers indicate specifications which are maximums that were obtained in ideal conditions. If the manufacturer recorded an accuracy of 0.05mm in its lab, it doesn’t mean you will be able to achieve the same accuracy in-house.
A scanner’s accuracy can depend on a number of factors:
- Temperature (a 3D scanner will perform differently at 40°C than it will at 20°C)
- Calibration (how well did you calibrate your 3D scanner? Do you calibrate it regularly?)
- The person performing the scan (though there is less room for error with today’s and tomorrow’s sensors, and more intuitive software)
On another, important note, 3D scanner manufacturers don’t all follow the same standards to measure their scanners’ accuracy. If high accuracy is of utmost importance for your applications, look for brands that have VDI/VDE and/or ISO certifications, for example.
3D scanner resolution
What is resolution?
Resolution can mean many different things depending on what you are talking about (photography, filmography, printing, …), but it has the same fundamental meaning. It is a technical computer science term that characterizes “how well the reality was captured”.
With screens, for example, the resolution is linked to the number of pixels available to recreate an image. The more pixels, the better the resolution and the image quality (the cleaner and crisper your image will seem). We can see this clearly with the circle example below:
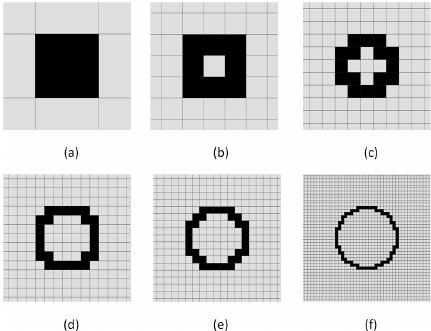
In 3D scanning, there is one main type of resolution: the resolution of your 3D mesh, a.k.a. “mesh resolution”. But some manufacturers also specify “measurement resolution”.
Mesh resolution
Most often, “resolution” or “3D resolution” in spec sheets refers to the resolution of the resulting 3D mesh. It is mainly measured in point-to-point distance– ie., the distance between two 3D points in a dot cloud– as it is the easiest to comprehend. The closer your mesh’s points are together, the better it will look. Point-to-point distance is sometimes called “spacial distance between points” or “point distance”.
Resolution can also be measured in PPS (points per scan). The more points your mesh includes, the smoother, more detailed it will look. This can be compared to 2D print quality, where the more PPI (points per inch) your file contains, the sharper your print.
Keep in mind that a higher mesh resolution means longer loading times and heavier files. If you don’t really need an extremely high definition, then there’s no use in putting strain on your RAM/GPU and weighing down your hard drive.
Note: In any case, you will likely need to invest in a high-end, gaming-quality PC in order to run 3D scanning software and load the enormous amount of captured data. Some of the computers we’ve worked with for high-end scanners cost over $5,000.
Measurement resolution
The measurement resolution translates to how many points the sensor is capable of capturing in a given area. The more points per unit of surface, the better.
But, in the end, what really matters is the mesh resolution that can be obtained and used in the software after computation. In some cases, the software calculates an average of several measurement points to generate a single mesh point (a vertex).
Note that the requirements for mesh resolution are relative and not absolute: on a sharp edge, you need a good resolution; on a flat surface, only a few points are necessary. Some 3D scanning software suites optimize meshes accordingly to avoid stocking heavy, unusable data (and choking your PC) for nothing.
Note: As a metaphor, let’s take the human body and its sensory receptors. We have thousands of receptors at the tip of our fingers, which we use to touch and interact with almost everything. Our backs, however, have very few sensory receptors, as we don’t really use our backs to feel things.
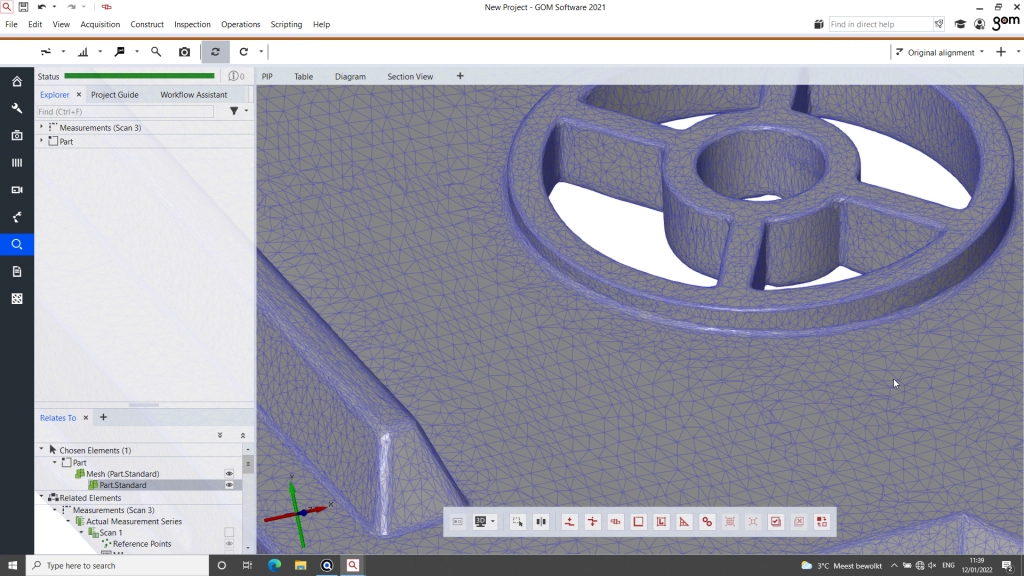
Conclusion
Many different terms are thrown around manufacturer websites and spec sheets. What really matters is volumetric accuracy and mesh resolution, and how well they answer your specific needs.
Furthermore, while accuracy and resolution specs are useful to easily and quickly compare one 3D scanner to another, they shouldn’t be deciding factors on their own. You should also consider a brand’s certifications, history, software, customer service, and more.
Feel free to reach out if you’re having trouble deciding on a 3D scanner or unsure of what you’ll actually need for your use case (and budget!).
Source: https://www.aniwaa.com/insight/3d-scanners/3d-scanner-accuracy-resolution-basics/