3D printing holes is quite common, but it can also be challenging. Check out five simple tips to get more accurate holes from your 3D printer.
3D printed holes are almost everywhere. You need them for pins, bolts, bearings, linear rods, and a host of other mechanical components. Without them, assembling certain 3D prints would be a nightmare comprised of messy glues and rolls of tape.
While designing a hole in CAD software takes only a few clicks, mastering their design for 3D printing can require some experience. For example, how should you design a vertical hole, which is perpendicular to your print bed, differently from a horizontal hole (parallel to your print bed)? What if the hole needs to be tapped?
From orientation to material shrinkage, hole design for 3D printing involves many intricate factors, resulting in noticeably different fits in your final prints.
In this guide, we’ll break down our top tips for 3D printed holes. By the end, you’ll have a host of tools with which to produce them for different uses. Let’s get started!
Nail the Basics: Proper Calibration
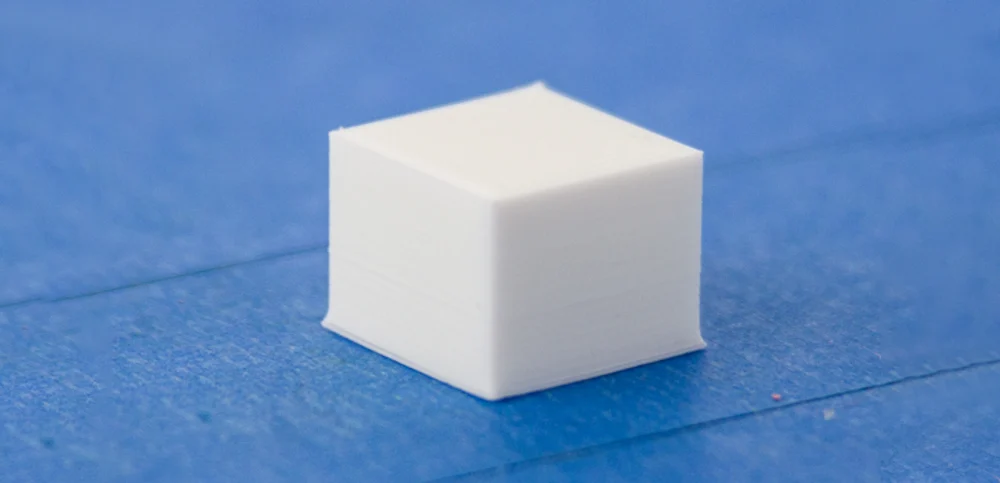
The first key to accurate holes is proper calibration of your 3D printer. Calibration comes in many flavors, so here are the top four that you should pay special attention to:
- Steps per mm: Steps per mm settings tell your 3D printer how much to turn each motor for each millimeter of motion. If these settings are off, your printer will produce holes that are consistently too big or too small. Fortunately, we have a dedicated calibration guide to help you find the right steps per mm settings for your machine.
- Axes orthogonality: Axes orthogonality describes how square your printer’s motion axes are relative to each other. If they aren’t perfectly perpendicular, your printer’s motion will be off, and the holes you produce will be slightly oval. To test for orthogonality, try one of our recommended calibration cubes that feature studs. From there, physically adjust your printer’s axes until they’re reliably square.
- First layer calibration: As you have likely already experienced, the first layers of your 3D prints are critical to successful results. For holes specifically, having your first layer nailed is essential to avoiding elephant’s foot, which is when your print starts a little too close to the bed. This can throw off the size of the hole’s opening, making for a poor fit later down the line.
- Proper clearances: Every machine’s precision is slightly different, so you can’t expect parts to always fit together perfectly. That’s where clearances come into play; these are slight gaps, built into your designs, that ensure sufficient leeway for proper fit. To find the right clearances for your printer, you can follow our dedicated guide.
With these four steps taken care of, you’re ready to start designing! Here are five tips to help you succeed at 3D printing holes.
Tip #1: Don’t Start in Mid-Air
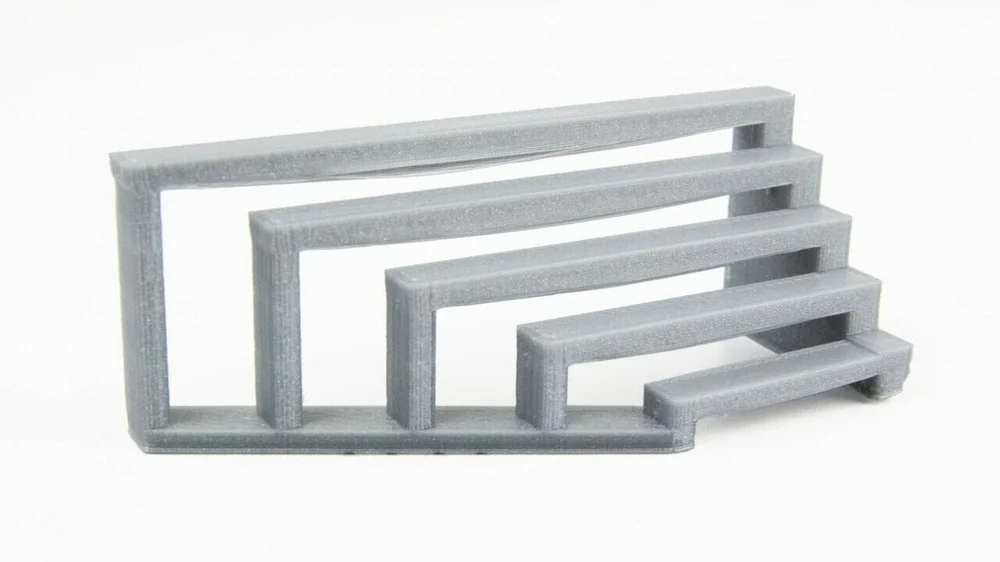
3D printers are quite capable of printing bridges, in the right circumstances. Bridges (shown above) allow plastic to be stretched from one end of a gap to another, leaving less opportunity for material to dangle in between. If you interrupt a bridge with holes, however, you ruin this delicate balance by preventing straight-line paths across the gap; the perimeters of the holes – circles – must be extruded into thin air, with nothing to stick to. This can create a disastrous mess of unsupported print paths, either ruining your print or causing a complete failure.
This issue is typically resolved in one of two ways:
First, some users like to break up mid-air holes such that they rest on a series of straight-line bridges. As you can see above, the perimeter of the hole is able to rest on a series of surrounding layers, preventing the aforementioned print-in-thin-air phenomenon. The result is a much cleaner and support-free product.
Alternatively, some users like to “fill in” their holes with one to two layers of plastic, essentially closing off their bottoms to create a flat bridge. By simply adding this thin layer, the holes are supported from below by nicely bridged struts, which can be cut out later with an X-Acto blade. From a design perspective, this is also much easier to implement than the previous option.
Tip #2: Beware of Shrinkage
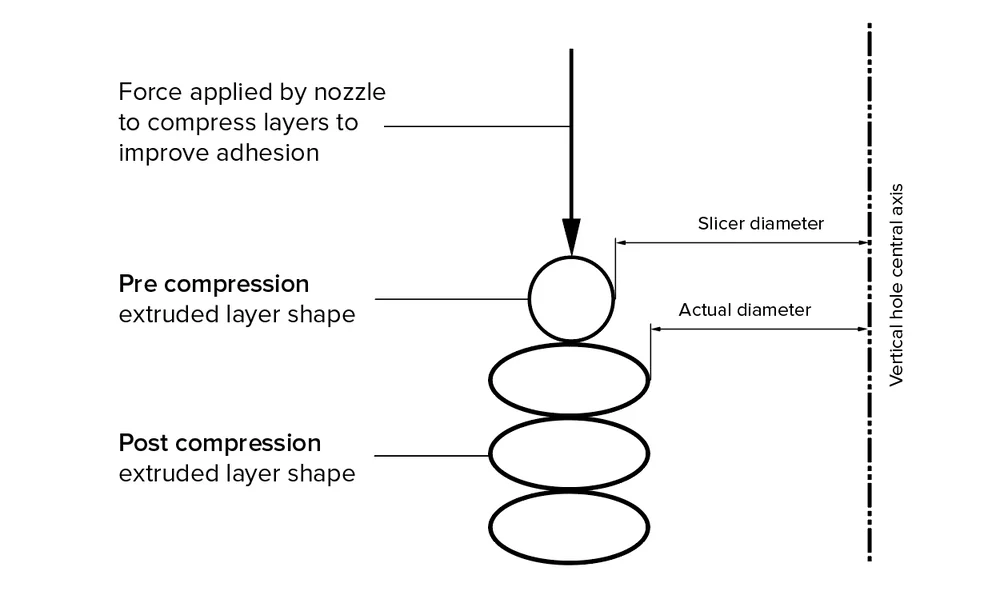
Shrinkage is another critical consideration for 3D printed holes. Despite the many ways that this can occur, the result is always the same: holes that are ever so slightly smaller than what you intended. While the change is subtle, it’s enough to differentiate a bolt that fits too tightly from one that slips right through.
There are three main causes of shrinkage: material shrinkage, layer compression, and mesh resolution.
Material shrinkage is likely the cause that you’re most familiar with: when a material cools down, it tends to contract. This is the culprit behind many infamous print failures, including warping and layer delamination. For holes, this shrinkage will lead to slightly undersized parts that don’t fit together properly.
Layer compression is another reason for shrunken holes, but it’s actually caused by layers being oversized. When a printer lays down a new layer, it applies a compressive force (as visualized above). While this improves parts’ strength, it also causes the lower layers to squish out slightly, extending beyond the boundaries that they were intended for. The result is a print that’s too “puffed out” in every direction, including within the holes.
Finally, there’s mesh resolution. While not technically a form of “shrinkage”, mesh resolution does cause holes to come out smaller than originally intended. The key here is that, with most 3D printing files, “holes” aren’t actually perfectly round; they’re approximations comprised of polygons (as pictured below). The result is a tiny bit of corner-cutting, causing holes to turn out smaller than initially intended:
To fix these issues, you can start off by designing the holes to be a little too large, preempting the shrinkage. After printing, the holes will come out smaller, closer to the desired dimensions. It may take some trial and error before you hit the sweet spot, but you’ll likely find some margin of inaccuracy that gives you the desired fit.
Alternatively, you can try the material shrinkage settings in your slicer. While different tools will have different names for this, there are typically options to specify your filament’s shrinkage ratio. A similar setting is “horizontal expansion”, which again preempts the shrinkage by automatically expanding or contracting the model before printing.
Finally, you always have the option of leaving the holes as-is (or even slightly undersized). If you intend to tap threads, this gives you some meat for the screws to bite into; otherwise, you can simply drill the holes to the precise dimensions that you require.
Tip #3: Avoid Overhangs
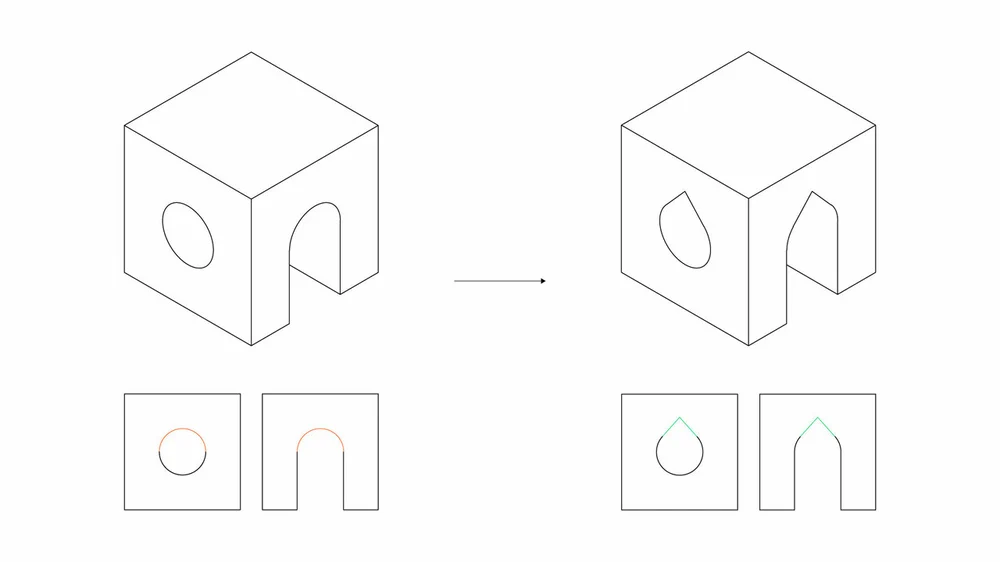
So far, much of what we’ve discussed applies to vertical holes. What if you’re met with a horizontal one? In this case, your biggest enemy is likely going to be overhangs.
As you can see above, horizontal holes form overhangs that get steeper as the hole closes. When printing, this means that the tops of the holes will be prone to drooping, resulting in openings that are ever so slightly “squished”. If you’re trying to fit a bolt through, this can be enough to block the opening.
Fortunately, this issue is easily combated by using teardrop-shaped holes instead of perfectly round ones (as shown above). This design avoids the harshest overhangs of the holes, allowing the prints to maintain the radii that you intended. While this technique may slightly increase the complexities of your 3D designs, it’s a small price to pay for accurate final products.
Tip #4: Add Tightening/Compliant Mechanisms
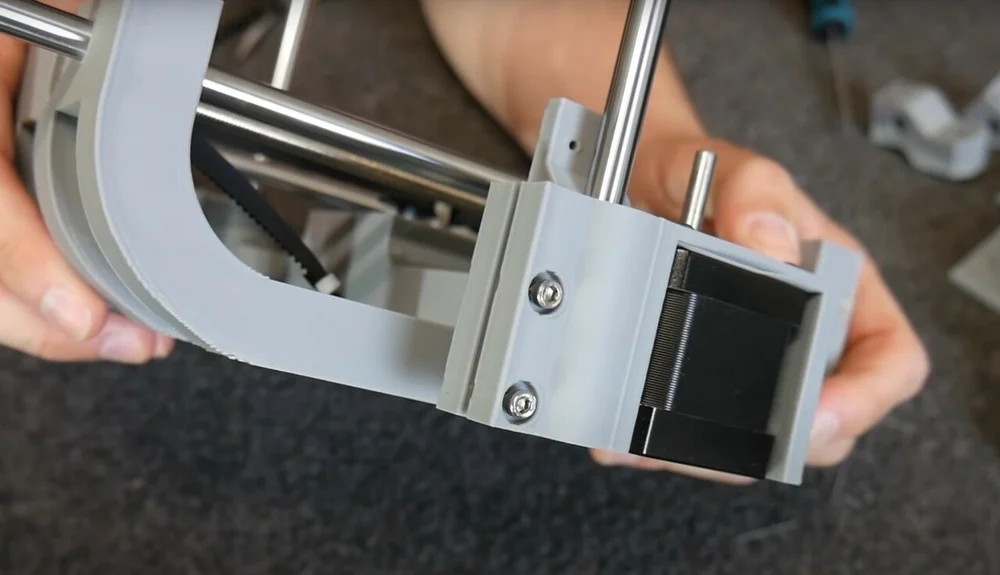
In some cases, you may want a hole that wraps tightly around an object. This is often the case when you’re mounting bearings or rods into 3D printed parts. How do you strike the balance between ease of assembly and a secure fit?
In these cases, your best bet may be to design holes that have a little bit of give. This allows for easier insertion of components, without sacrificing too much “grab” and stability. Such designs typically come in two flavors:
- Tightening mechanisms: These allow the original holes to be large enough for a comfortable fit, to be tightened down later. A common way of designing this is by adding a slot along the length of each hole, as shown above. From there, a bolt can be used to close the gap, clamping down on the object.
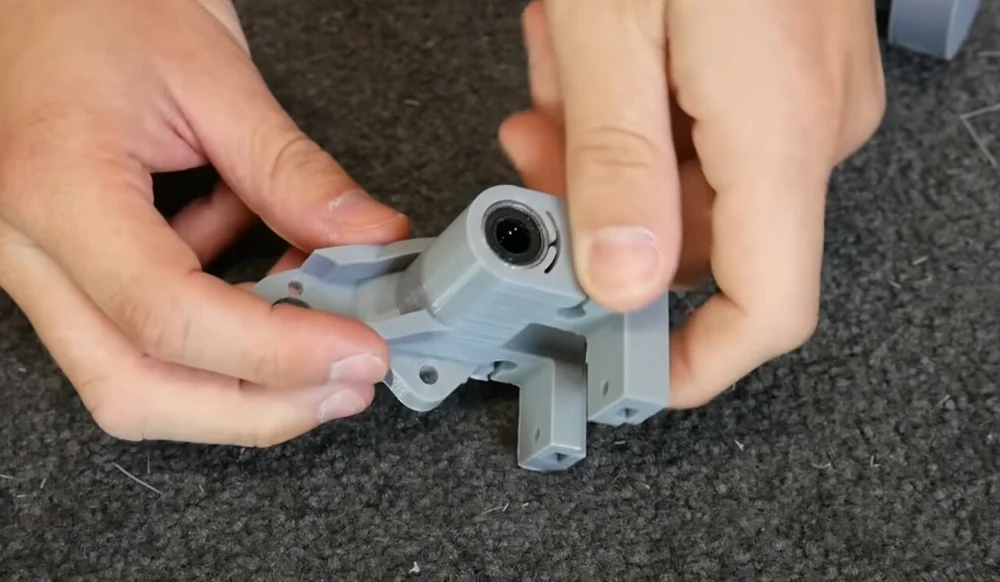
- Compliant mechanisms: If alignment is an issue (as with linear bearings), compliant mechanisms may be more suitable for your application. These rely on the natural springiness of the plastic to offer some play in the sizes of the holes, resulting in tight friction fits. You can see this in action above; the plastic’s flexibility provides just enough leeway to accommodate the bearing. If you’re interested in designing this mechanism for yourself, Maker’s Muse has an excellent tutorial on YouTube.
Tip #5: Tackle Threads
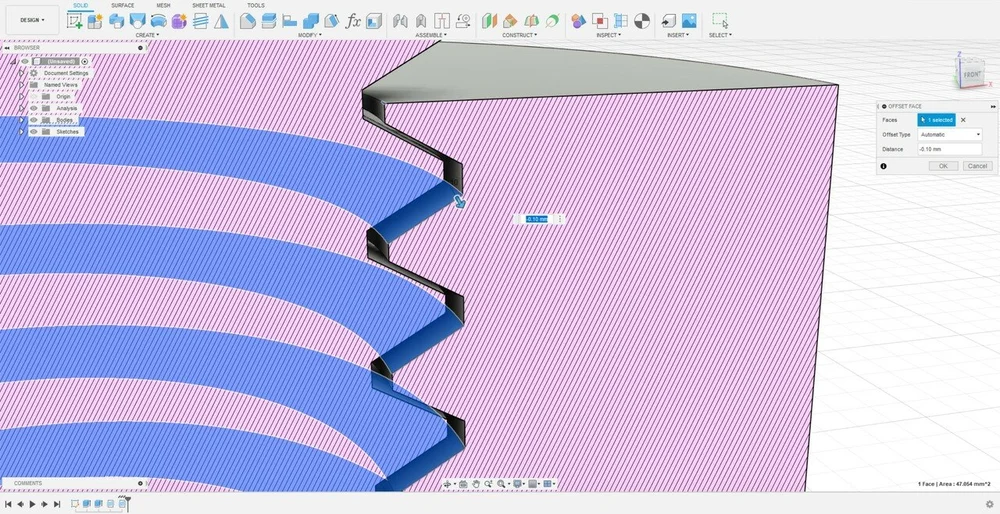
So far, we’ve focused on bare, clean holes, but that doesn’t cover everything. From time to time, you may need threaded holes: these allow bolts to be screwed in directly, without separate tapping or nuts. While this can be quite convenient, it also renders many of the previous tips useless; it’s difficult, for instance, to prevent shrinkage, as bolt threads have standardized dimensions.
To address this issue, we need to get creative with how we adjust the hole designs. One excellent tip is to use a push/pull tool to widen the gap between a bolt and the threaded hole, effectively increasing the clearance. You can use this in conjunction with the aforementioned shrinkage settings to dial in the fit.
While designing, note that bigger threads will come out more cleanly, especially on FDM 3D printers. We recommend printing with a lower layer height to create more precise threads.