Understanding HIP
Hot Isostatic Pressing (HIP) is a specialized manufacturing process that involves subjecting materials to high temperatures and isostatic pressures. This technique is particularly effective in improving the properties of 3D-printed metal parts.
The Challenge of Porosity in 3D Printed Metal Parts
Additive manufacturing processes like Selective Laser Melting (SLM) and Electron Beam Melting (EBM) produce parts with varying degrees of porosity. This porosity can significantly compromise the mechanical properties, corrosion resistance, and fatigue life of the final product.
How HIP Addresses Porosity
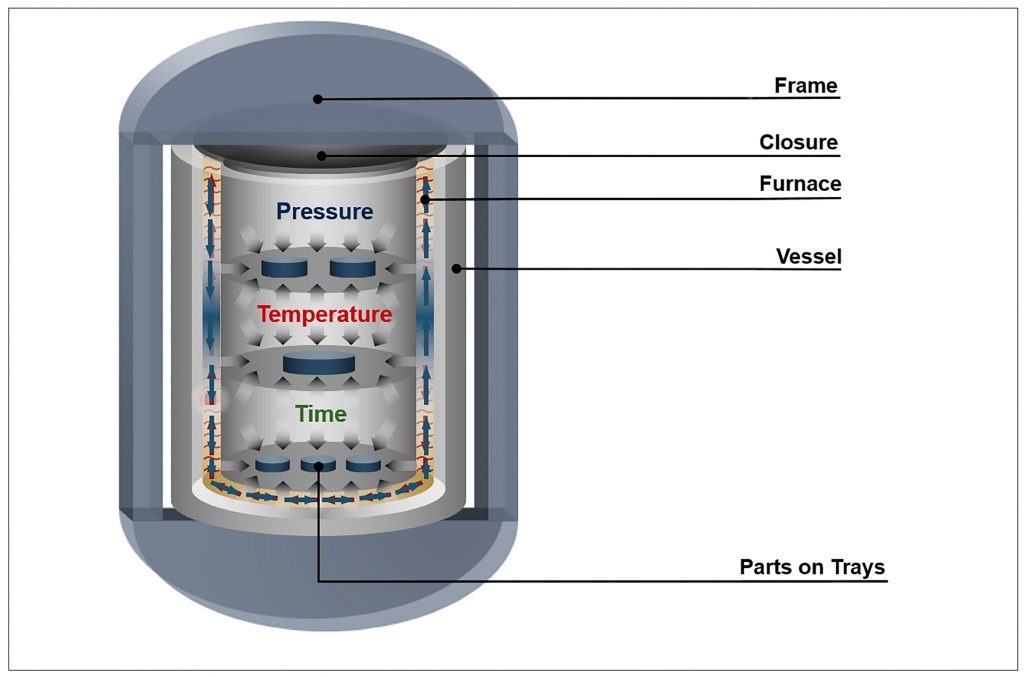
HIP offers a solution to this problem by densifying the 3D-printed parts and eliminating porosity. The process involves the following steps:
- Encapsulation: The 3D-printed part is placed inside a sealed container, often made of metal. Above is a simplified schematic picture of the principle.
- Heating: The container is heated to high temperatures, typically between 1900-2200°F (1040-1200°C). HIP temperatures are often in the range of 70 to 90% of the solidus temperature of the material being processed.
- Pressure Application: Inert gas, usually argon and in the range of 100-200MPa, is pressurized to exert uniform pressure on the material from all directions.
- Hold time: The time depends on the thickness of the components being processed since there is a longer temperature delay in the core of large parts due to its thermal conductivity.
- Densification and Bonding: The combination of high temperature and pressure causes the material to densify, eliminating porosity and creating a fully dense component.
For a specific material, multiple HIP cycles can yield 100% density, each employing different combinations of temperature, pressure, and hold time.
For instance, a cycle with lower temperature, pressure, and longer hold time can produce the same densification as a cycle with higher temperature, pressure, and shorter hold time.
While heating and cooling rates may not directly impact densification, they significantly influence the final microstructure and, consequently, the mechanical properties of the processed material.
Benefits and Limitations of HIP for 3D Printed Metal Parts
A critical requirement for HIPing AM parts without encapsulation is a gas-tight surface. This ensures that the pressure medium doesn’t penetrate the material.
While conventional powder metallurgy parts often necessitate sintering to very high densities to achieve this, AM processes inherently produce parts with relatively high density and gas-tight surfaces.
This characteristic makes AM parts uniquely suitable for capsule-free HIP processing. Let’s see what benefits can be brought be metal prints:
- Improved Mechanical Properties: HIP significantly enhances the strength, toughness, and fatigue resistance of 3D printed parts.
- Enhanced Microstructure: The process refines the microstructure, leading to improved performance.
- Elimination of Porosity: HIP effectively removes porosity, resulting in fully dense components. You can speed up the 3D printing process and leave all to HIP.
- Stress Relief: HIP reduces residual stresses caused by the 3D printing process, improving dimensional stability and reducing distortion.
- Surface Finish Improvement: HIP can lead to a smoother surface finish and reduced roughness.
While HIP offers numerous benefits, it may not be ideal for all metal prints, particularly those with complex structures like sandwich structures and other intricate internal structures. They require demanding conditions for optimal processing.
Applications of HIP in 3D Printing
HIP finds applications in various industries, including:
- Aerospace: Manufacturing high-performance engine components and structural parts.
- Automotive: Producing durable engine components and lightweight structural parts.
- Medical: Creating implants and surgical tools with superior strength and biocompatibility.
- Energy: Manufacturing components for nuclear reactors and other energy systems.
Conclusion
Hot Isostatic Pressing is a powerful technique that complements 3D printing by improving the quality and performance of additively manufactured parts. By understanding the principles and applications of HIP, engineers and manufacturers can unlock the full potential of 3D printing and create innovative products with superior properties.