In the realm of metal additive manufacturing, two prominent technologies stand out: Metal Binder Jet and Powder Bed Fusion (PBF). These methods offer unique advantages and are suited for different applications, but they also have their own sets of challenges. Let’s explore each technology in detail to understand their distinctions and potential uses.
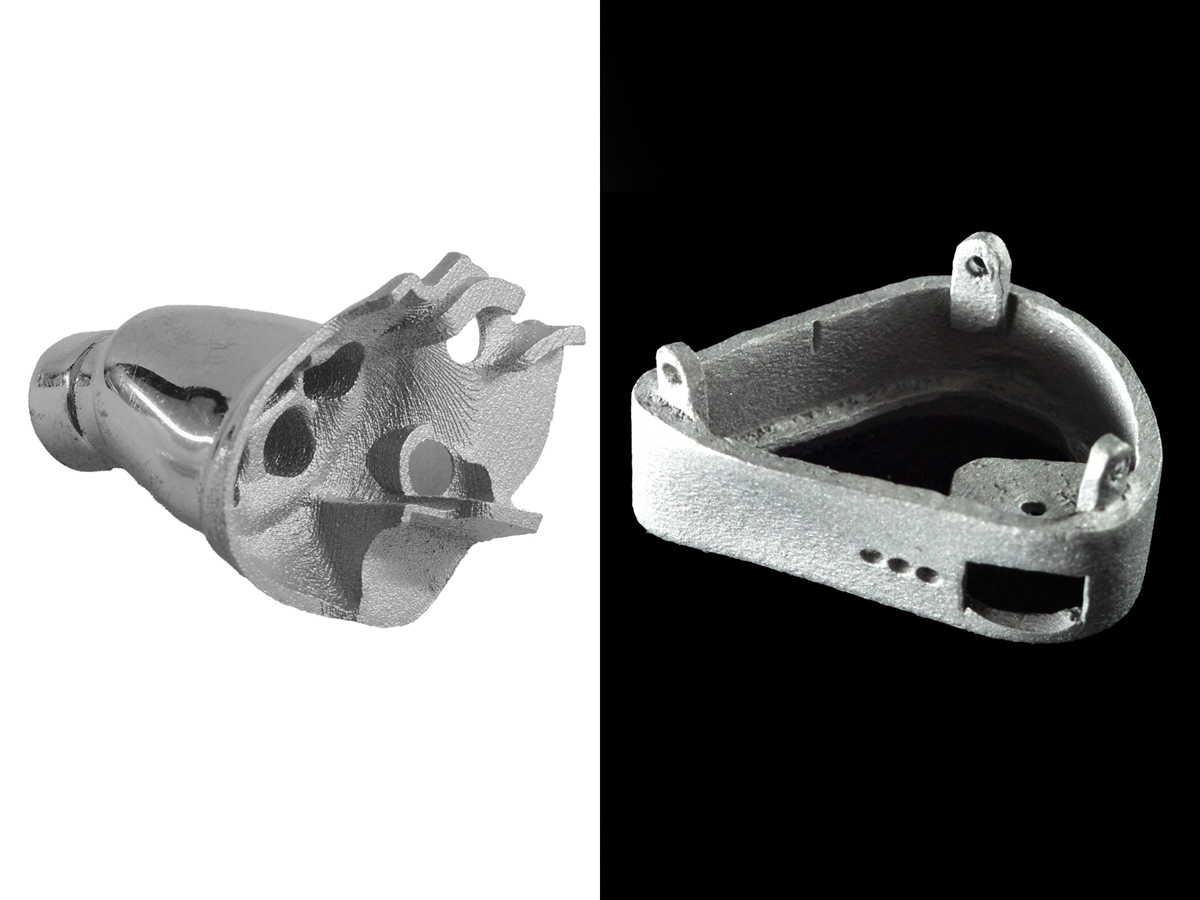
Metal Binder Jet
Metal Binder Jet 3D printing utilizes a print head to selectively deposit a liquid binder onto a bed of metal powder, layer by layer, forming the part’s shape. The “green” parts produced through this process are subsequently sintered in a furnace to remove the binder and densify the metal.
Advantages
- Cold Process: Binder Jet operates at room temperature during the printing phase, avoiding residual stresses and eliminating the need for support structures. This makes the process particularly suitable for high-efficiency batch production.
- Cost-Effective: Binder Jet can produce parts faster and at a lower cost compared to PBF, especially for larger batches. The equipment and materials are generally cheaper, and the process allows for a broader material selection since it does not rely on the material’s laser absorption properties.
- Batch Efficiency: Parts can be stacked in the Z-axis and X-Y orientation, enabling many parts to be printed and sintered simultaneously.
Disadvantages
- Lower Mechanical Properties: While Binder Jet parts can achieve isotropic mechanical properties post-sintering, they generally exhibit lower mechanical properties and dimensional accuracy compared to parts produced by PBF.
- Higher Post-Processing Requirements: The process requires additional steps such as sintering, infiltration, and finishing to achieve the desired properties. These steps can introduce defects and porosity.
- Material Constraints: Although Binder Jet supports a broader range of materials, the sintering process can still introduce some stresses and defects, affecting the final part quality.
Powder Bed Fusion (PBF)
PBF involves using a heat source, such as a laser (Selective Laser Melting, SLM) or an electron beam (Electron Beam Melting, EBM), to selectively melt and fuse metal powder particles together. The heat source scans the cross-section of the part layer by layer, creating a solid metal object.
Advantages
- High Precision and Resolution: PBF can produce high-quality, high-strength, and high-density parts with fine details and complex geometries. The process supports intricate designs and ensures immediate part density post-printing.
- Immediate Density: Parts are dense right after printing, with less post-processing needed compared to Binder Jet.
- Multi-Laser Systems: Recent advancements have introduced printers with multiple lasers, enabling faster build times and larger parts, although this can also introduce additional thermal stresses.
Disadvantages
- High Cost: PBF requires expensive equipment, materials, and maintenance, making it a more costly option compared to Binder Jet.
- High Energy Consumption: The process consumes a significant amount of energy due to the use of lasers or electron beams.
- Support Structures and Thermal Stresses: PBF requires support structures to prevent deformation and warping. The rapid heating and cooling can induce internal stresses, which must be relieved through post-process treatments like de-stressing.
Comparative Analysis
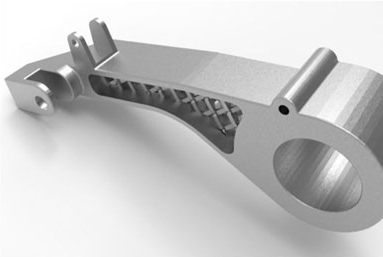
Print Speed and Efficiency
- Binder Jet: Offers faster literal print speeds and high batch efficiency but requires additional post-processing like sintering, which can slow down the overall process. It is particularly advantageous for high-volume production.
- PBF: Generally slower in literal print speed but can achieve a faster overall process with multi-laser systems and less extensive post-processing. SLM tends to be the slowest in total end-to-end process time.
Part Complexity and Quality
- Binder Jet: Best suited for larger, simpler parts with lower resolution. It produces isotropic mechanical properties and good fatigue life but can introduce defects during sintering.
- PBF: Ideal for smaller, intricate parts with higher precision and resolution. The parts are denser and exhibit higher strength and hardness with columnar grain structures.
Material Properties
- Binder Jet: Provides a broader material selection but results in parts with lower mechanical properties and density compared to PBF.
- PBF: Produces parts with higher strength, hardness, and durability, with better metallurgical bonding and higher part density.
Cost and Time
- Binder Jet: More cost-effective with cheaper equipment and materials, but additional post-processing steps like sintering and finishing are required.
- PBF: Higher cost due to expensive equipment and slow scanning speeds, but results in higher quality and consistency in parts. Pre-print setup and post-print processing are more extensive.
Additional Considerations
- Thermal Considerations: Binder Jet avoids heat-induced stresses during printing but might introduce some stresses during post-process sintering. PBF, particularly SLM and EBM, can induce internal stresses due to rapid heating and cooling.
- Support Structures: Binder Jet does not require support structures during printing, while PBF does, with SLM needing both thermal and structural supports and EBM partially sintering the surrounding powder to act as support.
Conclusion
Both Metal Binder Jet and Powder Bed Fusion (PBF) offer unique benefits and are suited for different applications in metal additive manufacturing. BJP is ideal for high-efficiency batch production of larger, simpler parts with diverse material options, while PBF excels in producing high-quality, high-strength, and intricate parts with complex geometries and higher density. The choice between these technologies depends on the specific requirements of the part, including size, complexity, material properties, cost, and production speed.