Binder Jetting and Multi Jet Fusion (MJF) are two prominent additive manufacturing (3D printing) technologies, each with its unique strengths and applications. Let’s delve into a comparison of these two methods, focusing on their printing processes and principles:
Binder Jetting
Binder Jetting is a 3D printing process that uses a liquid binding agent to selectively adhere powder particles together. A layer of powder is spread, and a printhead deposits a liquid binder onto the powder, bonding the particles. This process is repeated layer by layer until the 3D object is complete.
Binder Jetting offers several advantages, such as its versatility in materials (metals, ceramics, and polymers), relatively fast production speed, and cost-effectiveness for large-scale production. However, it also has limitations, including the potential for lower part strength and a rough surface finish that may require additional post-processing.
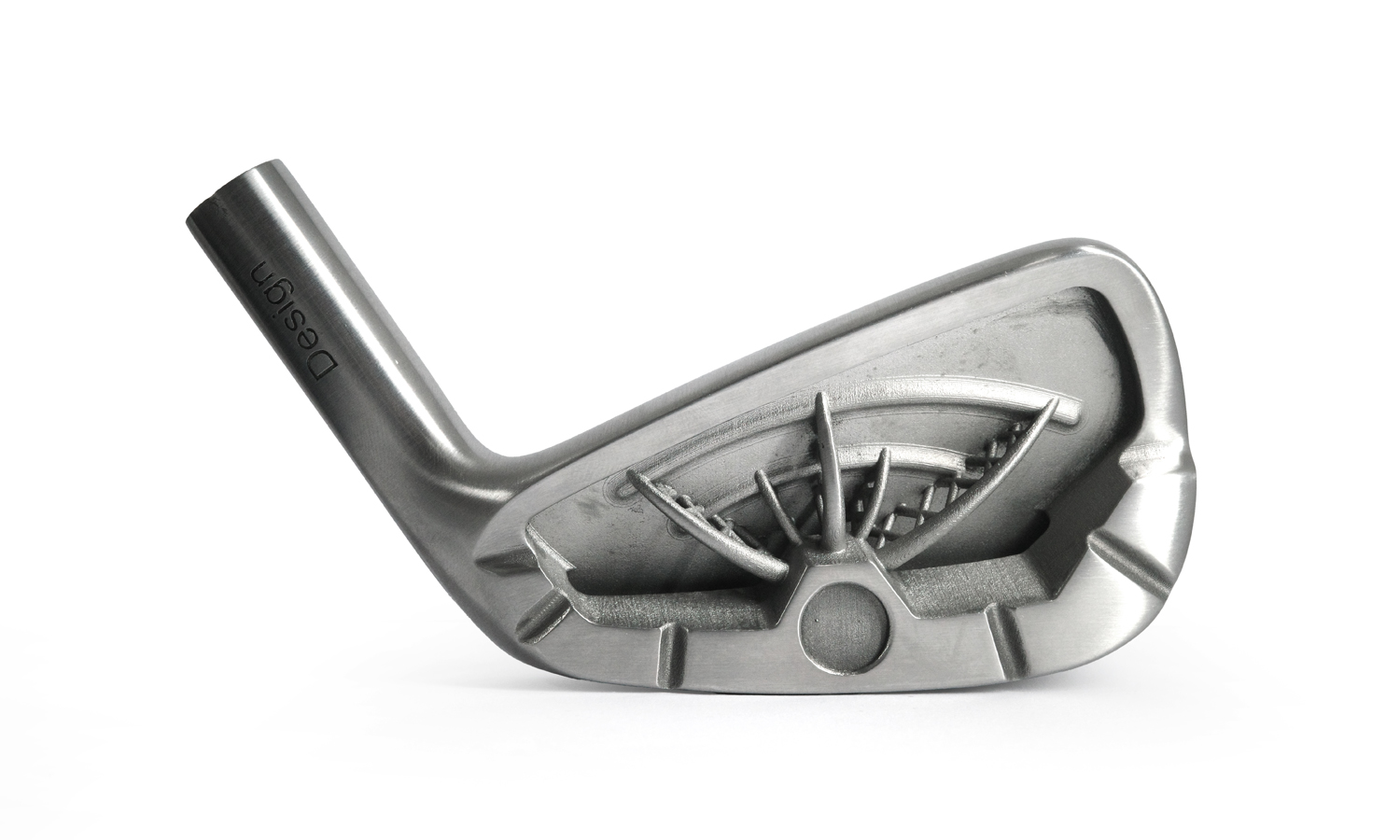
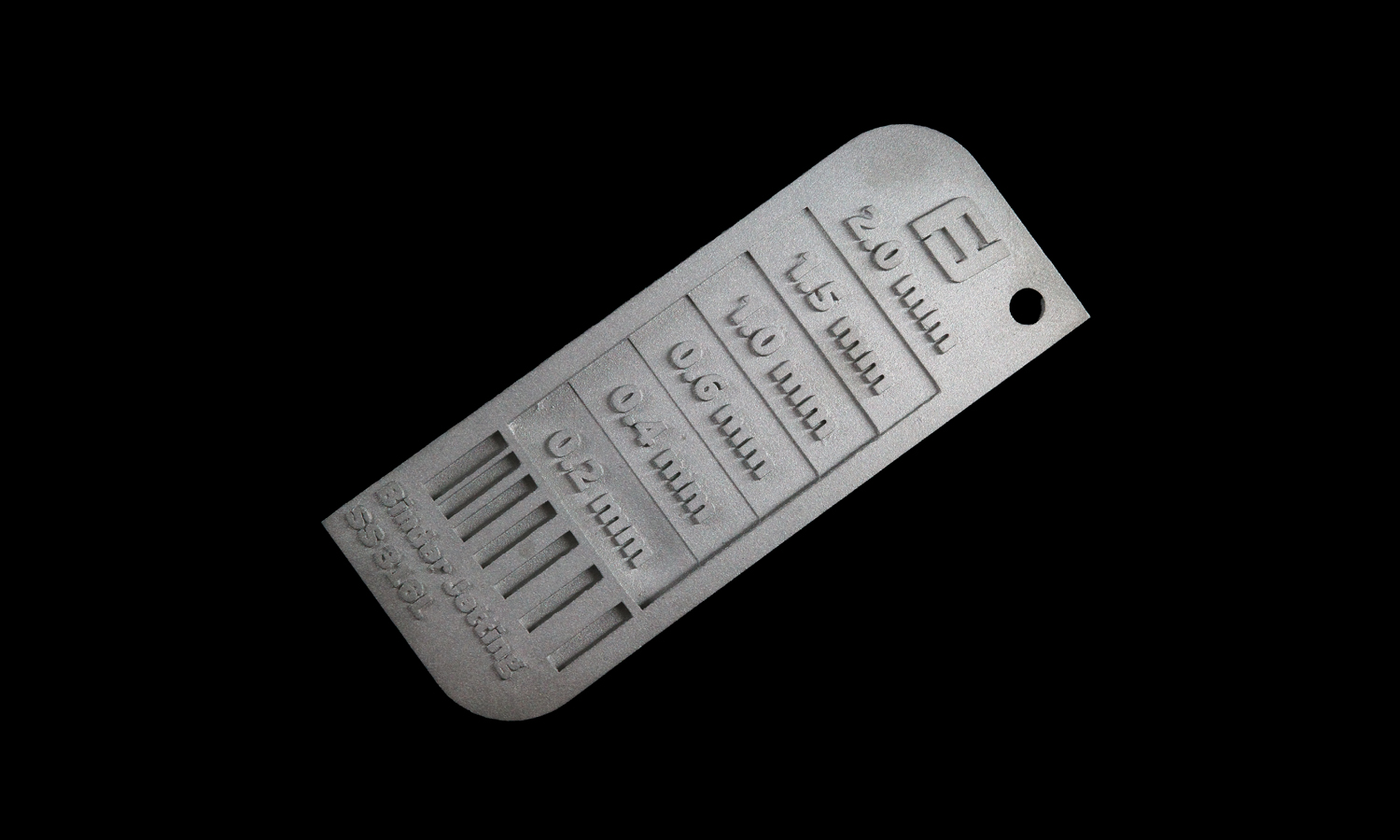
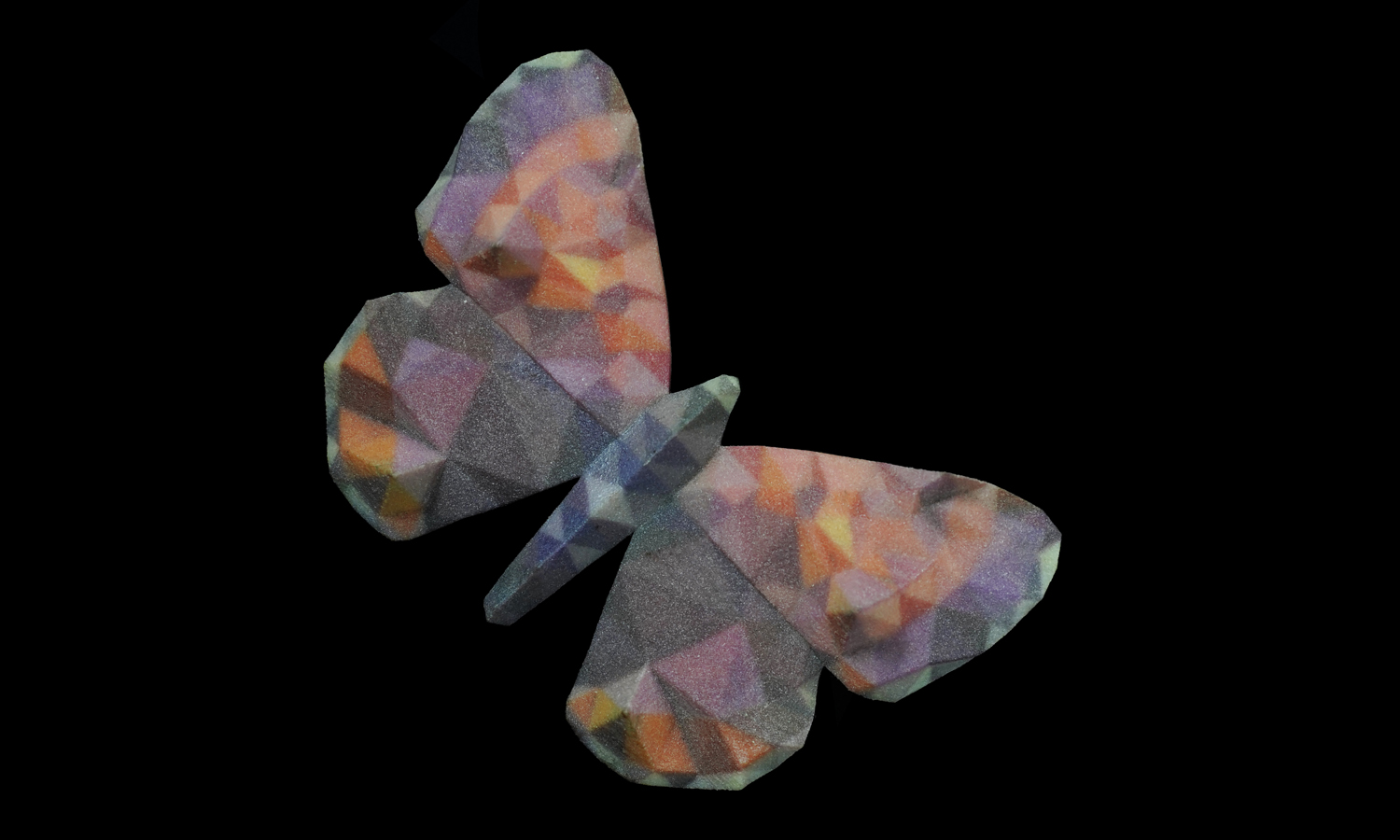
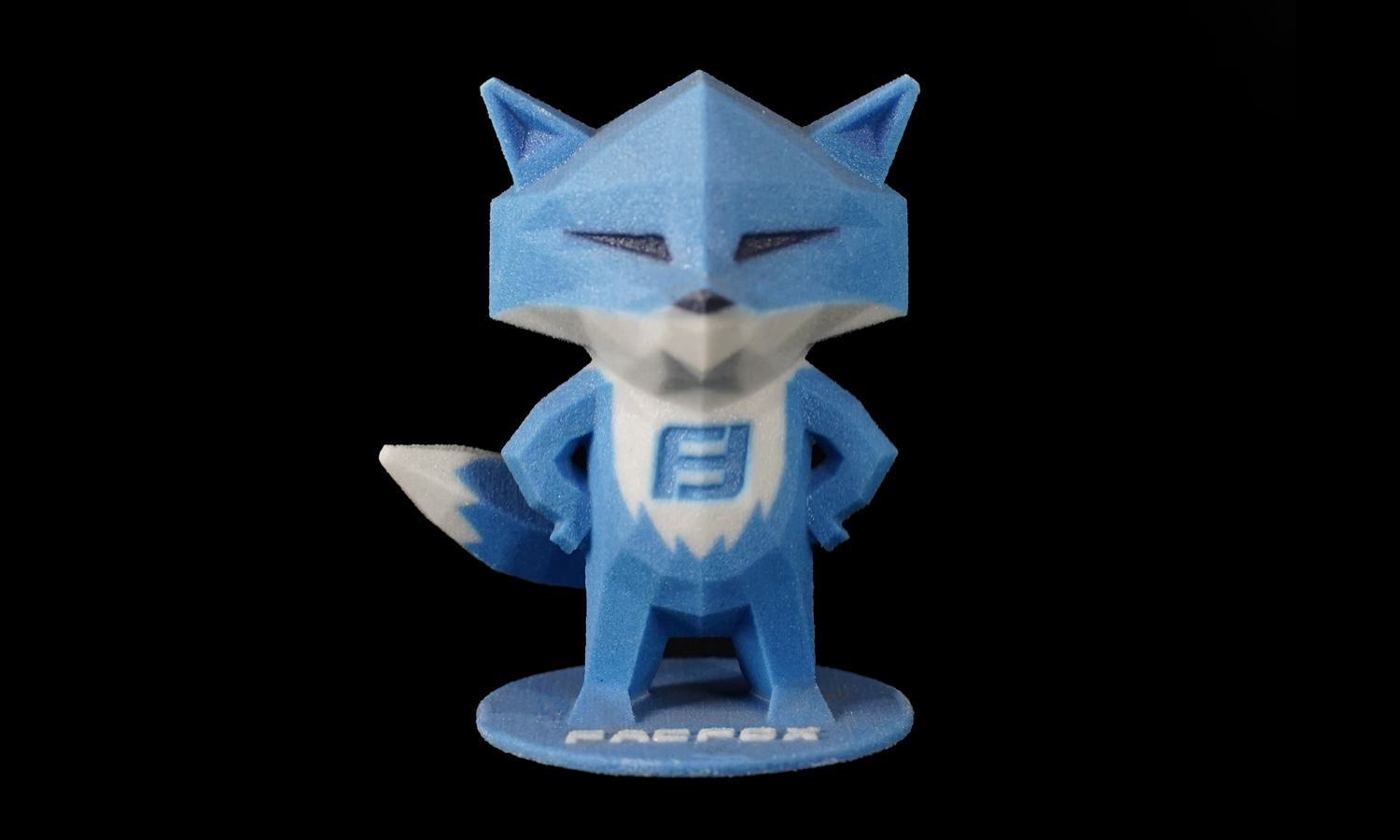
Multi Jet Fusion
Multi Jet Fusion (MJF) is a powder bed fusion technology that uses infrared energy to fuse nylon powder particles together. A layer of powder is spread, and two agents are jetted onto the powder: a fusing agent and a detailing agent. The fusing agent defines the areas to be fused, while the detailing agent improves part resolution and surface finish. Infrared energy is then applied to fuse the powder where the fusing agent was deposited.
MJF offers several advantages, such as high-quality parts with excellent mechanical properties, dimensional accuracy, and surface finish. It is also highly efficient, allowing for rapid prototyping and production. Additionally, unused powder can be reused, reducing material waste. MJF is particularly well-suited for producing functional parts directly, minimizing the need for post-processing.
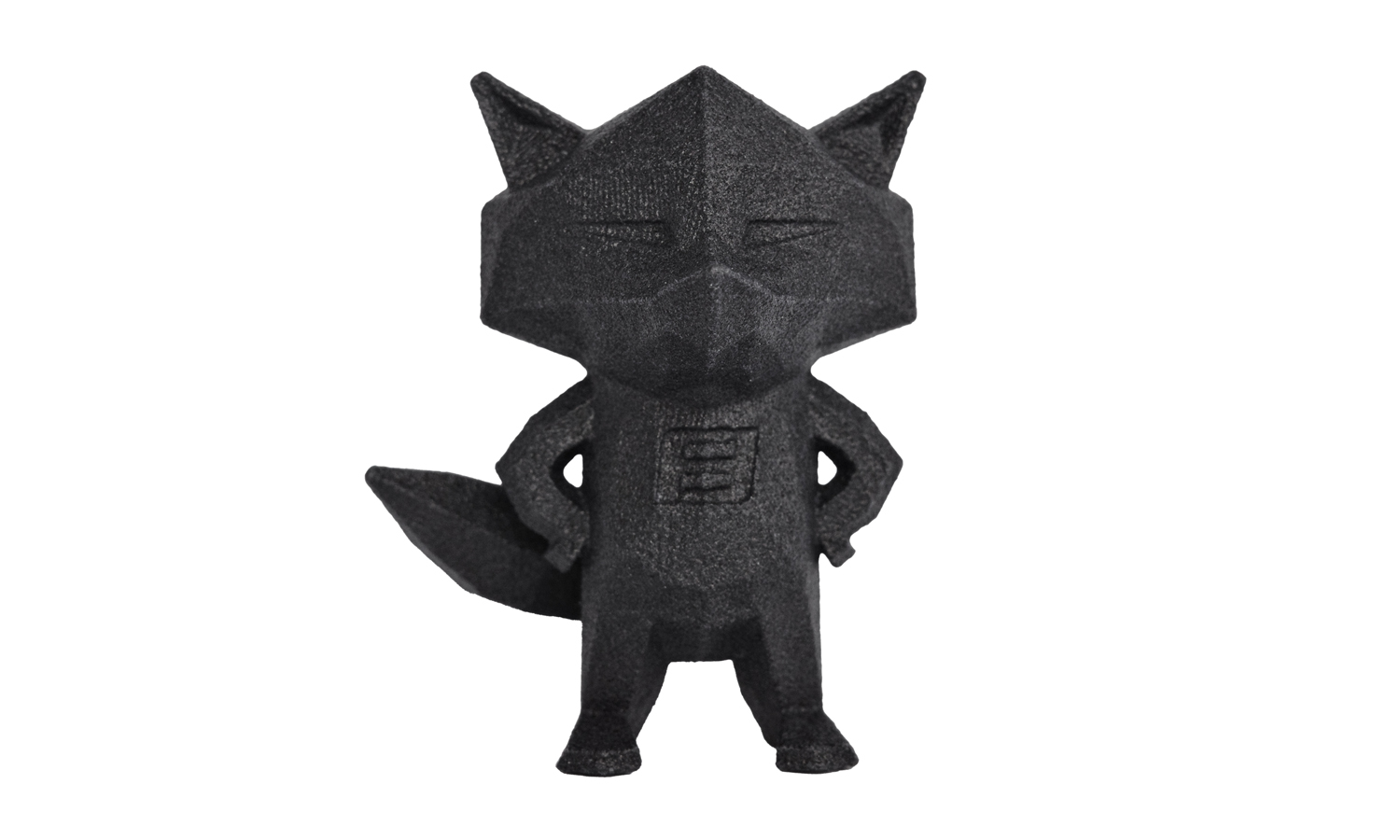
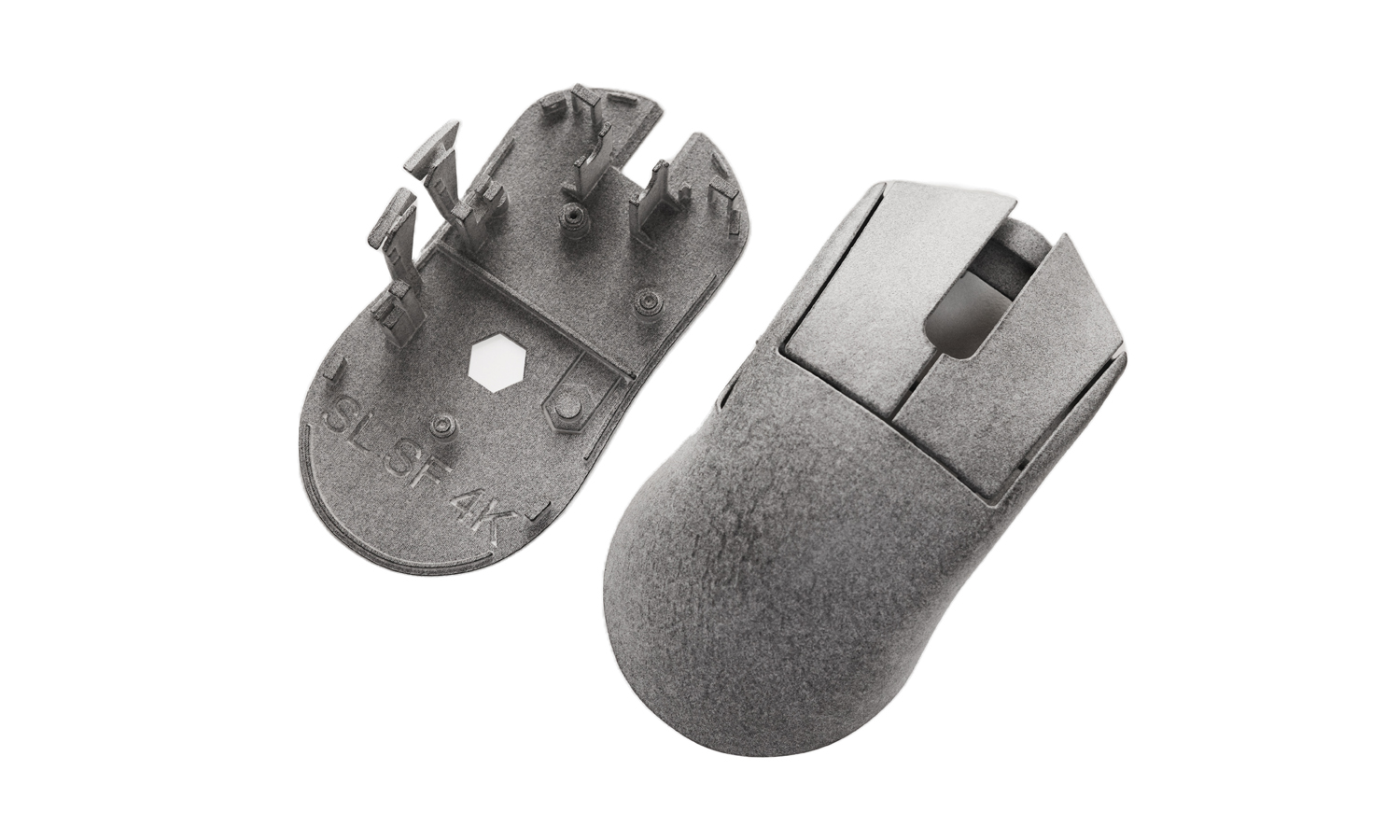
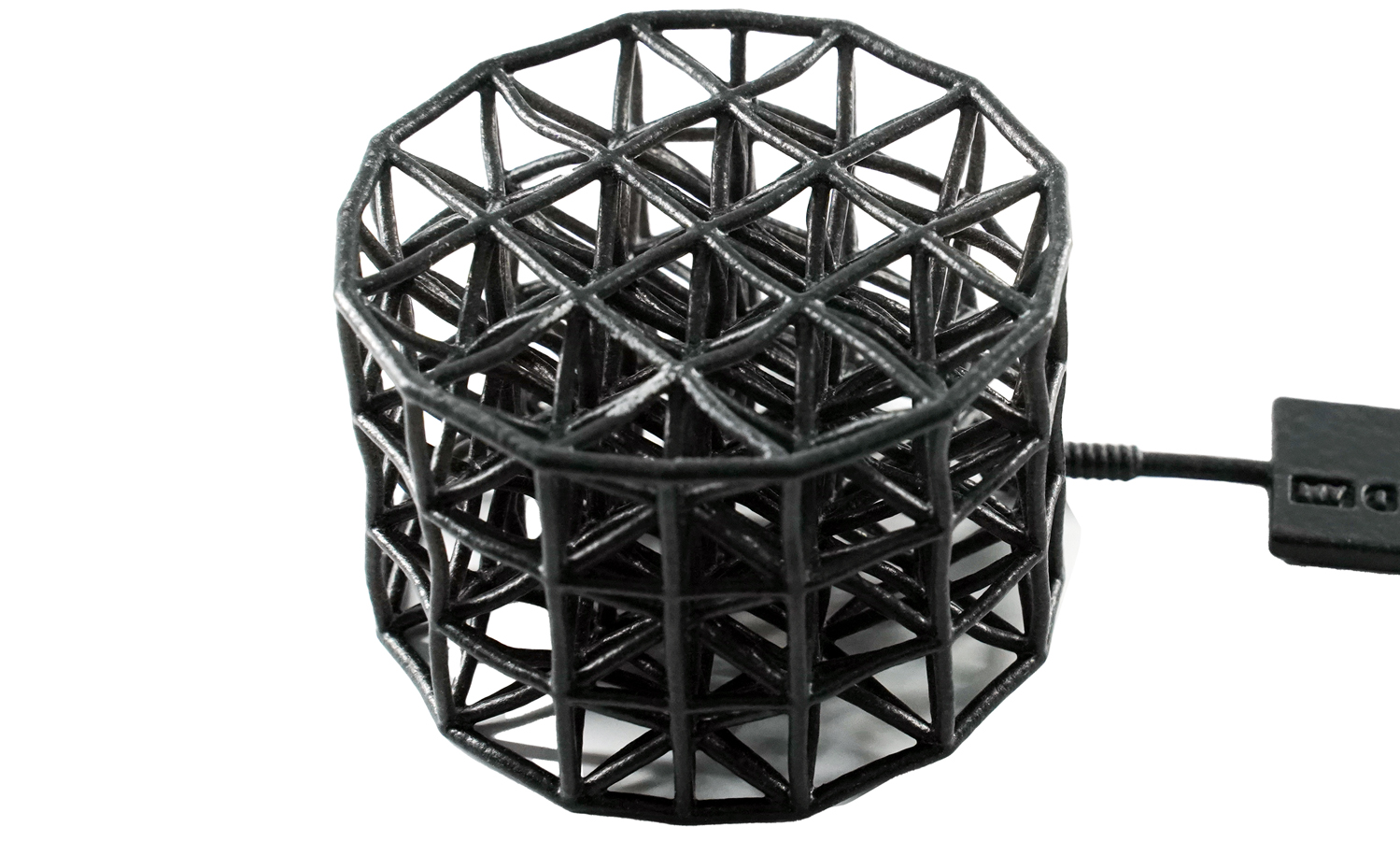
MJF 3D Printed Full-color HP Nylon RPG Minis Custom Statue for Board Game. Photo Source: FacFox
Key Differences
While both Binder Jetting and MJF involve powder-based additive manufacturing, they differ significantly in their processes and the resulting part quality. Binder Jetting uses a liquid binder to bond particles, while MJF uses infrared energy to fuse particles together. This fundamental difference leads to variations in part strength, surface finish, and material compatibility.
Binder Jetting is more versatile in terms of materials, but it may produce parts with lower strength and a rougher surface finish. MJF, on the other hand, is limited to nylon-based polymers but produces high-quality parts with excellent mechanical properties and a smooth surface finish.
Choosing the Right Technology
The choice between Binder Jetting and MJF depends on several factors, including the desired material, part quality, production volume, cost, and part functionality. For applications requiring high-strength, high-precision parts with a smooth surface finish, MJF may be the preferred choice. However, for applications that prioritize versatility, cost-effectiveness, and rapid production, Binder Jetting may be a more suitable option.
By carefully considering these factors, you can select the most appropriate technology for your specific needs.
Feature | Binder Jetting | Multi Jet Fusion (MJF) |
---|---|---|
Material | Wide range (metals, ceramics, polymers, glass) | Nylon-based |
Process | Liquid binder | Infrared energy and chemical agents |
Resolution | Lower | Higher |
Surface Finish | Rougher | Smoother |
Part Quality | Lower mechanical properties | Higher mechanical properties |
Elevate Your Designs with FacFox
Ready to bring your 3D designs to life? FacFox offers a wide range of 3D printing services, including Binder Jetting and Multi Jet Fusion, to meet your specific needs. Our state-of-the-art technology and experienced team ensure high-quality, efficient, and cost-effective production.
Experience the Future of Manufacturing with FacFox. Contact us today to discuss your project.