ABS and PLA are two of the most common 3D printing materials. Learn the differences between PLA vs ABS filament and how to print them both!
The Major Players
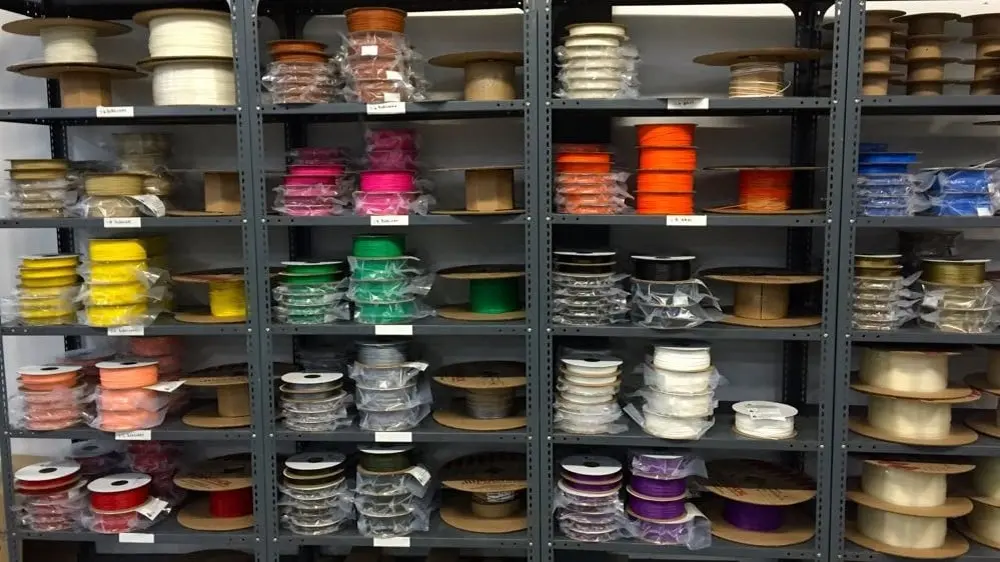
3D printing encompasses many technologies, but the most popular one at the consumer level is fused deposition modeling (FDM). The material used to 3D print parts on FDM printers comes as filament, a sort of string of plastic wrapped around a spool. Filaments can be made of different materials but are usually thermoplastics because these can be easily melted and re-solidified.
Of the many different types of filaments, the most popular is polylactic acid (PLA), known for its ease of use and low price. But there are other common materials out there, like acrylonitrile butadiene styrene (ABS), a widely-used material for injection-molding consumer products like Lego or internal car parts like a dashboard.
Apart from maybe PETG, PLA and ABS are the two most popular filaments used for FDM 3D printing, and while they’re both thermoplastics and look similar, they have many differences. In this article, we’ll compare the two materials on a few different key points, like printing, price, and more.
Printing & Use
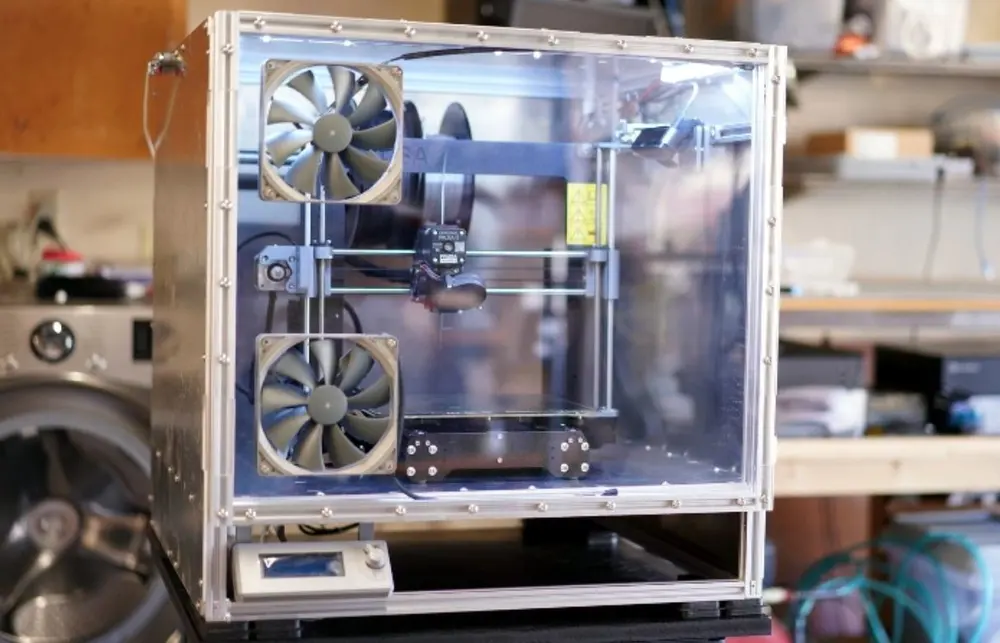
PLA and ABS may seem quite similar at first glance, but they do differ when it comes to printing. In this section, we’ll go over the differences between PLA and ABS in how they’re printed and used.
Temperature
The first differences concern printing temperatures. In particular, ABS requires higher nozzle and bed temperatures than PLA. The more significant of these is the latter, as ABS tends to warp a lot on the print bed. Indeed, most ABS filaments require a bed temperature of around 80-110 °C. PLA, on the other hand, doesn’t necessarily require a heated bed, but it’s generally preferred to have a bed temperature around 60 °C.
There’s less of a difference when it comes to nozzle temperature. PLA is usually printed with a nozzle temperature of around 180-230 °C compared to the 210-250 °C that ABS needs.
Another temperature-related detail is that, with ABS, it’s usually necessary to have an enclosure around your printer to trap heat and block airflow. This is because ABS is a very temperature-sensitive material, so when there are air drafts or temperature shifts, parts can crack while being printed. PLA is much easier to print in this regard, as you don’t need an enclosure, although it could still improve print quality.
Speed
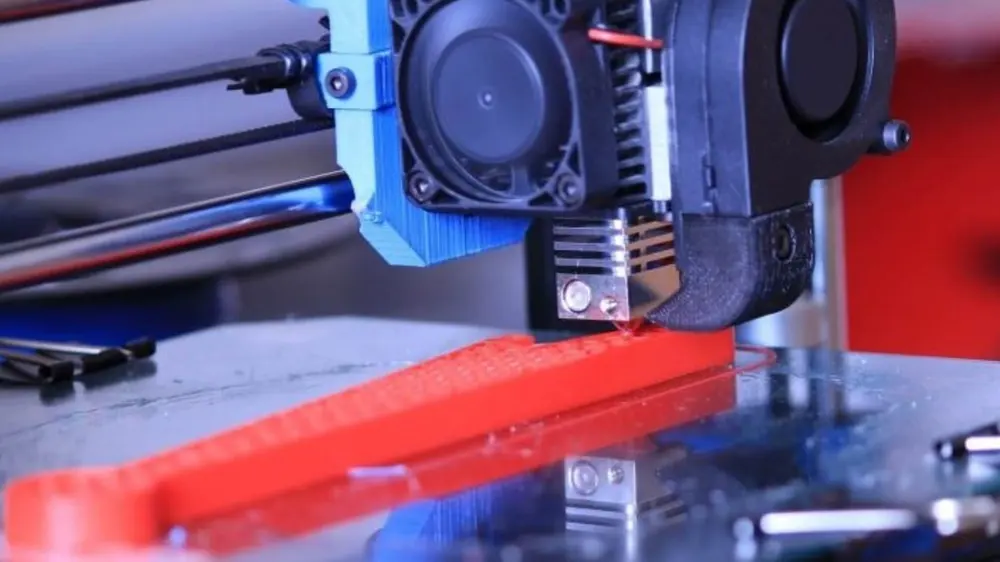
ABS and PLA print at roughly the same speed, which is great because you don’t have to change this setting when switching between slicer profiles for different materials. A speed of 60 mm/s is pretty common for PLA, but it certainly isn’t the limit; some users have achieved print speeds in the range of 150 mm/s or more. ABS can also print at 60 mm/s, but this value is at the higher end, with a more accurate range being 40-60 mm/s.
Speed settings also depend on what other settings you’re using, so choosing between PLA and ABS probably won’t be your most limiting choice.
Fumes

Almost all filaments result in odors when printed, but some are more obvious than others. When a thermoplastic is heated, fumes are released, and these fumes typically aren’t the healthy kind, as they could contain harmful particulates.
PLA isn’t really known for giving off a bad smell, and the material is plant-based, so what fumes are there are aren’t too worrisome. On the other hand, ABS is notably more toxic than PLA and yields a terrible odor.
When using an enclosure, lifting the lid of the enclosure will release the fumes all at once, making this smell sometimes unbearable. It’s therefore recommended to be careful handling your enclosure and ensure proper ventilation in whatever room you’re printing. Filters can especially help with this.
Storage
You may not think storing filaments matters that much, but different materials have different hygroscopic levels, meaning some are more sensitive to moisture than others. Hygroscopic materials absorbing moisture leads to a serious decline in print quality; among other things, bubbles can form when the filament is heated and extruded.
PLA and ABS aren’t really known for being on the hygroscopic side of the spectrum (unlike PETG). Still, it’s important to remember to always seal your filament in an air-tight container to prevent any moisture from getting to it. You can also dry or dehydrate your filament before using it with an oven or dehydrator.
Material Properties
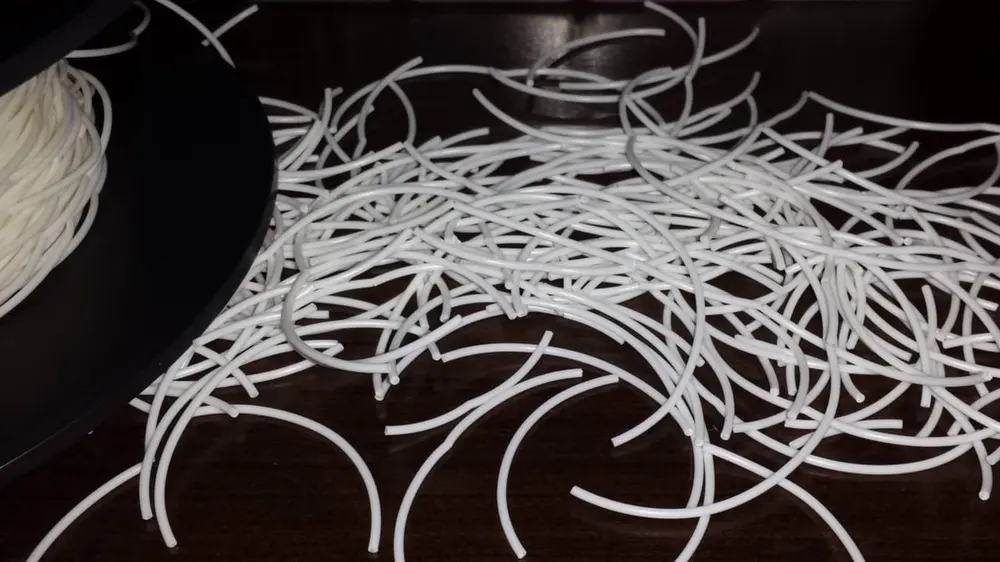
Another important aspect of any filament is its material properties, and PLA and ABS couldn’t be more unalike in this regard. Let’s go over the differences between PLA and ABS when it comes to strength, flexibility, and potential for post-processing.
Strength & Durability
Strength is a vital aspect of any material because weak parts are limited in their applications.
In light of this, MatterHackers performed a test where they printed the same hook in different materials and recorded how much weight each could handle. In their findings, ABS held a minimum of 209 pounds and a maximum of 284 pounds. This is pretty strong and much greater than PLA’s range of between 119 and 184 pounds. Overall, ABS is a good bit stronger than PLA, which somewhat justifies how difficult it is to print.
Another factor to consider is a material’s durability to weathering such as sunlight, extreme temperatures, and other elements. ABS can handle higher temperatures than PLA but tends to crack in the cold, while PLA doesn’t. Additionally, both materials degrade over time when faced with UV rays and moisture, so neither is particularly suited to parts that will be used outside.
Flexibility
PLA and ABS aren’t flexible filaments like TPU, but flexibility is still an important factor because it determines if parts are brittle or more durable. “Flexibility” usually refers to flexural strength, with higher values signifying less brittle materials, but it can also describe the elongation at the breaking point.
AirWolf3D ran a few tests with 3D printed hooks in various materials and found that ABS had a higher elongation at breaking than PLA. In their tests, PLA could only handle 15.3% elongation before breaking compared to the 21.6% that the ABS part could take. In other words, ABS parts tend to be less brittle than PLA ones, which for a functional part could be a significant difference.
Post-processing
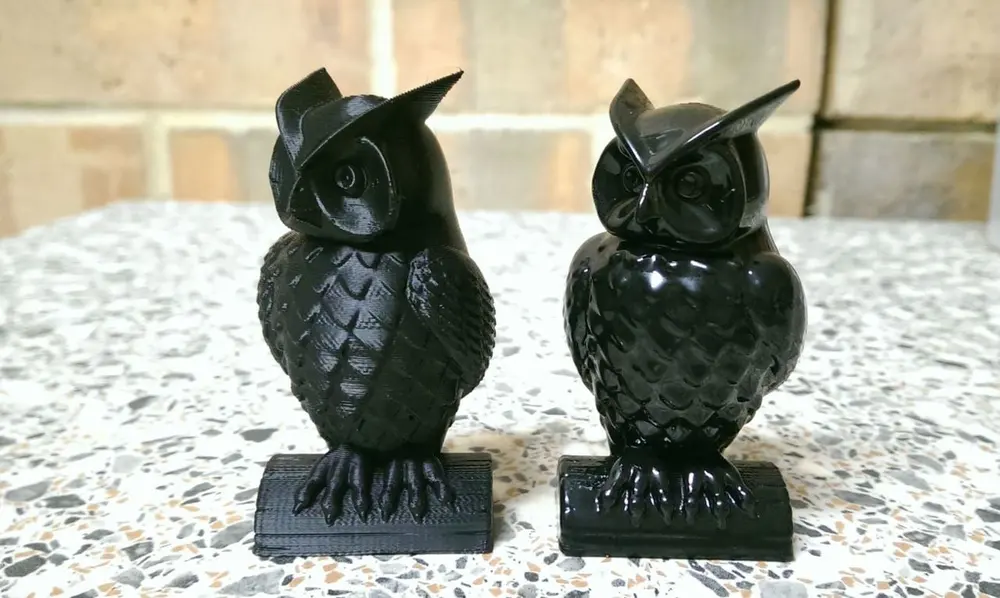
Post-processing refers to techniques that you can use to improve a part after it’s printed. Neither PLA nor ABS have limitations in basic post-processing methods like sanding or painting, although some report that ABS is more easily sanded.
Another popular post-processing technique is smoothing via a solvent. In this, ABS tends to be the favorite choice, as it can fairly easily be smoothed with acetone vapor.
Other Properties
Naturally, there are many other properties of PLA and ABS that might be relevant for a specific use case. For example, PLA is more recyclable and can biodegrade. That said, the above characteristics tend to be the most important, with the rest coming into play in only very niche contexts.
Pricing & Options
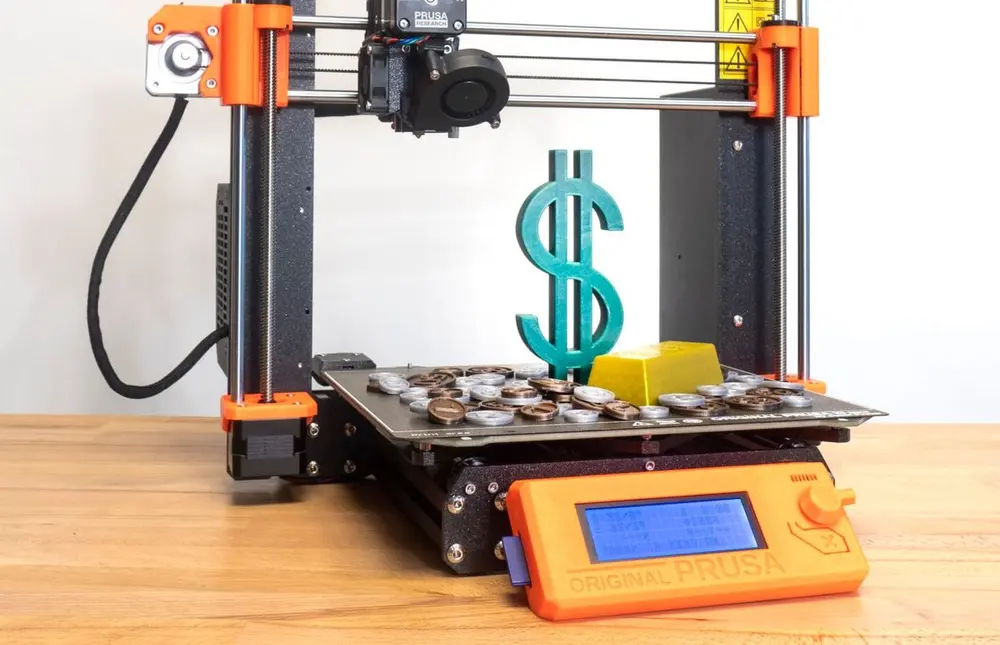
PLA and ABS are similar in price when it comes to the cost per one-kilogram spool of filament. However, if you’re looking solely at the raw material cost, ABS is probably cheaper than PLA. That’s because ABS is so widely used in injection molding for making common, small parts, like interior car components or even Lego.
In 3D printing, because PLA is more popular and there is a larger infrastructure built around it than ABS, some PLA spools can be found for cheaper than ABS filament. Yet, this price difference isn’t significant, and the price of a spool of one of these materials is more dependent on other factors. Attributes like the brand, diameter tolerance, color, and shipping are the more influential factors as to why some filaments are more expensive than others.
On that note, because PLA is more popular as a filament than ABS, it also has more brands, colors, and special blends (like composite PLA filaments). ABS filament is also out there with various brands and colors available, but perhaps less so than PLA.
Applications
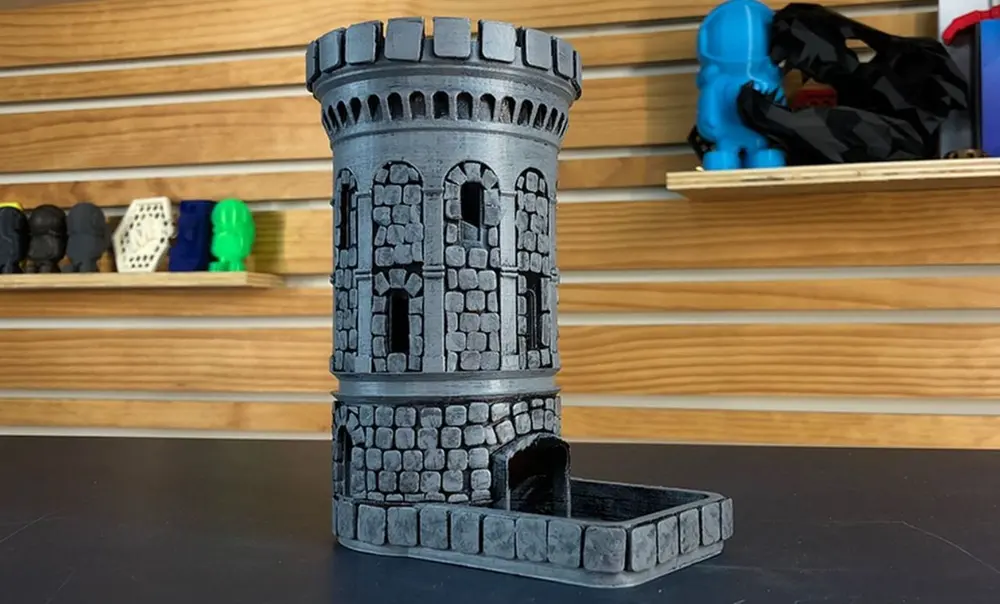
In conclusion, both PLA and ABS are great material but for different reasons. Below, we’ll go over a few applications for each type of filament to help you decide which one is right for you.
PLA is the king of 3D printing materials, having become popular because it’s easy to print and work with. However, it’s pretty weak and brittle, so it’s probably best if you’re new to 3D printing or are looking to print fun models rather than heavy-duty functional parts. Essentially, for anything that won’t be exposed to strong physical stress, hot temperatures, or UV radiation, PLA is your go-to material. A few examples uses include miniatures, display pieces like cosplay helmets, and lightly-functional items like dice towers.
On the other hand, ABS is a more industrial material that’s more challenging to print with but has enhanced qualities over PLA, including its strength, flexibility, and reactivity to solvents. These characteristics make ABS attractive to those looking to make prototypes of real-world parts, components that will undergo physical stress, or snap-to-fit models. Some example applications might include a gear used in a competitive robot, a snap-to-fit chainlink, or anything meant to weather the outdoors.